The rapid changes in the demands being placed on logistics operation mean that optimising the network is an increasingly difficult challenge, and harnessing the right technology is critical.
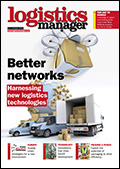
One of the key challenges in logistics is optimising inventory, distribution and transport. And it is a task that never goes away. The most appropriate solution for one set of circumstances can quickly become sub-optimal as business conditions change.
So, recognising change in the business and understanding how it will impact on a logistics operation is critical.
“Every logistics operation manager probably spends some part of everyday thinking about optimising their network,” says John Sewell, principal at Crimson & Co.
“This might include how to use a warehouse, how best to ship this order to the customer, or even how best to pick different types of orders: these are all network questions. You then change the network to solve particular problems or exploit opportunities but the challenge which often exists with this process comes from the same problems continuing to persist and the alternative solutions failing to have the desired effect.
“Most organisations will review their network every three years with the key drivers being integration between company and networks, growth outperforming capacity, outsourcing the supply chain to easy burdens or simply to address internal complaints and gripes,” says John Sewell.
Niklas Hedin, chief executive officer of delivery management company Centiro, points out that multi-channel retailing has added another layer of complexity to logistics networks, which in turn has heightened the economic impact.
“In the past, retailers were able to optimise their networks based on product volume and had fewer delivery destinations. They now have to contend with shipping a wider variety of goods to a huge number of different locations. For example, in addition to handling pallets at the distribution centre, they also need to deal with the stream of smaller orders with some sent to homes, others to collection points and the rest to stores. Many retailers are still coming to terms with how to do this in an efficient manner, and this is before they even consider the economic impact of their reverse logistics operations,” he says.
“In time, as retailers gain greater visibility across their supply chains, they should be able to use this information to optimise resources and create greater efficiencies. For example, by having greater insight into where inventory resides they should be able to make better delivery decisions. So in some cases it may end up being much more efficient to deliver a particular item from a nearby store as opposed to a centralised distribution centre. Against this backdrop, we are likely to see retailers use a combination of ‘mini hubs’ and larger distribution centres as a one-size fits all approach won’t meet today’s customer demands.”
Fab Brasca, vice president, solution strategy, intelligent fulfilment at JDA, highlights the fact that in today’s increasingly omni-channel environment, demand is king, and meeting it quickly and cost-effectively is critical to business success.
Alienating customers
“To meet the demands of today’s market place, organisations need to ensure that every element of the supply chain acts in sync: the distribution and fulfilment plans created should act as the glue to connect the various execution components such as inventory management and transport,” says Brasca. “This, however isn’t as easy as it seems and if businesses fail to adapt to increasing volatility, they risk alienating customers from poor service and face increased costs from across the supply chain.
“The future winners will be businesses that have designed an ultra-responsive and highly flexible supply chain network, which is able to adapt to new challenges efficiently, to survive and grow.”
Brasca believes that the starting point in any network optimisation process is the understanding and segmentation of demand in all its forms.
“Segmentation can take multiple forms including aspects such as key customer definitions, direct consumer versus store, fast versus slow mover, etc. Understanding those segmentations and their associated service level requirements forms the driving force behind creating a supply chain blueprint.”
Understanding the bigger picture is critical for Niklas Hedin. “We must stop and think about the bigger picture when it comes to logistics networks. In short, logistics managers need to rip up the rule book and start again as networks need to be more dynamic than ever before to meet the demands of today’s customer. A one-size-fits-all approach is never going to work, because you need to develop different supply chains for different needs.”
But identifying the elements of a typical logistics operation that have the greatest potential for improvement is a challenge in itself.
“One of the most important areas of improvement is defining the possible flows of product based upon the segmentation of demand,” says Fab Brasca. “This has the cumulative effect of understanding where to stock and service to meet segmentation requirements as well as applying the appropriate flows necessary for defined service levels.”
But he warns: “One of the biggest pitfalls in network optimisation is thinking that it is a static exercise rather than an on-going process.”
Any design solution needs to be future-proof and thought must be given to how that will be achieved. Transforming the supply chain into a source of competitive advantage is challenging amid increasingly complex trade-offs stemming from globalisation and consolidation, economic uncertainty and rising costs. Brasca says: “To future-proof its network design, retailers and suppliers must consider better, more innovative ways of reducing operational costs and working capital investments while also driving continuously improved customer service, revenue and growth. Future-proofing the network’s design requires more than today’s status-quo daily planning and execution; it requires a dynamic optimisation approach based upon holistic data-driven analysis.”
Sewell highlights a number of factors: “Firstly, separate opinion from the facts and then centre the review on the facts. All reviews have to have both fact and opinion, but too many studies start with a very narrow range of options driven by exactly the sorts of narrow view which culminated in the need for a review to take place in the first place. In most cases, breakthrough solutions don’t come from network analysis. They come from understanding the facts.
“It’s important to distinguish between improvement benefits and network change benefits. This sounds simple but is a perennial problem. Network reviews have the potential for huge savings but most of them can arise from doing the current job better rather than from changing the network. Look for a base case approach that builds a detailed bottom up model of current operations. From this you can identify opportunities for improvements and then identify where savings can be made across the network. Of course, sometimes the current network can become just too ‘stuck’ to improve (for instance industrial relations, poor contracts, poor site) but that is a separate discussion,” says Sewell.
“Seriously consider whether you want to build a continuing model. Everybody wants one in principle, but doing this properly is a huge investment and will require substantial maintenance both in software costs and maintaining a team to use the model. Cost can range from at least $400k (USD) to build and $200k to operate per year. The benefits are to be able to use your network model in day-to-day business decision making where it may provide a core competitive opportunity: find a way of taking on a new contract to supply; find the optimum way to supply this customer; deal with the risk of a core port being blocked for a month; identify the right place to put the seasonal inventory build this year,” says John Sewell.
“Actually the precise logistics modelling output is normally unimportant. The traditional focuses of network reviews – centres of gravity – is, unless you have very low value and high bulk product, not a very precise guide to decisions. Very often the centre of gravity and the associated optimum location of multiple warehouses become obsessive in these studies. They need to be done and the results are important, but exact location even if it were important is unlikely to be a place with you want the facility to be, so you will find you are not based there anyway. The important question is the search area and knowing what the penalty of sub-optimisation will cost.
“Bottom up activity modelling has the potential to provide greater bang-for-your-buck. Ultimately, any network review that does not contain bottom up activity modelling is likely to be an exercise in obscurity. If you don’t have a tight grip on the cost now, the future cost of doing activities (and clarity on why the cost has changed) then the strategy that results from a review will always be a black box,” says Sewell.
Using technology in network design and optimisation
Technology development is changing approaches to network design and optimisation fast, says Crimson’s John Sewell. “Essentially, network reviews can now be completed as what they are – big data problems – where a true end-to-end view can be taken in complex supply chains.
“Too many reviews in the past were based on often breath-taking assumptions, with outputs that were ‘black boxed’ and obtuse.
“Even simple tools like Excel can now process vastly more data and exploit real time map information embedded in applications like Google maps. This means that analysis can be done with a focus on real data and real options using better visualisation tools, greatly improving the transparency of the explanation,” says Sewell.
“The big network modelling software tools are also moving on fast. They remain expensive and complex to implement and maintain. They continue to promise slightly ahead of what they can easily delivery but it is now possible to build network models that:
l Contain all aspects of a network review – network locations and costs, inventory deployment and delivery routing – to generate a full cost of the end-to-end supply in one managed database structure
l Allow detailed bottom up cost modelling of almost any conceivable network element – factories, warehouses, cross docks in as much detail as is needed
l Allow testing of a proposed network solution with a wide range of input values to see how robust the solution will be in the face of real world events
l Allow temporary scenarios to be tested, so for example, the impact of closing this warehouse in off peak can be remodelled to see the impact of flows through the network,” says John Sewell.
JDA’s Fab Brasca believes that organisations must look to technologies which provide strategic, end-to-end capabilities to evaluate, design and optimise the entire supply chain.
“Businesses can use new technologies such as RFID tags which can help them to keep a real-time pulse on the actual demand at point of consumption. The use of technology can help to lower the costs of reading and evaluating patterns, while allowing organisations to pro-actively channel products to customers giving the highest margin or profitability.
“Technology will also allow the company to provide the customer with differentiated service offerings. This is particularly important as the multi-channel market continues to develop and becomes increasingly competitive,” says Brasca.
Putting the focus on the agility of the network
Agility is one of the top priorities for many organisations: competition is more global and more intense, customers – both businesses and consumers – have higher service and customisation expectations than ever, new demand trends can emerge and spread within days thanks to social media. And the pace of business has significantly accelerated.
Robert F Byrne, vice president and general manager of forecasting solutions at E2open, points out that agility is not just about being very fast in the execution – reacting faster than the competition as new market opportunities emerge or disruptions in the supply chain happen. Rather it is about both better preparation and faster execution.
“At the strategic level, where the time horizon is one year or more, agile companies design their supply chain with the required flexibility in mind. Zara’s well documented success as a fast fashion brand would not have been possible without the conscious decision to use local suppliers, allowing for the short replenishment lead-times required by such a business model. Zara gave up on the cheaper sourcing from Asia because putting firm orders with suppliers months in advance and waiting for the containers to arrive by sea from China was not going to work for them. In this context, it is interesting to note adidas’ recent announcement that they were once again going to make shoes at home by building a new “Speedfactory” in Germany, with intelligent robots to assemble shoes at faster speed.
“The design decisions that agile companies make at the strategic level are not only related to the physical design of the supply chain. They also look at how to handle the product proliferation and customisation in the most efficient way. Nokia, when it was still a supply chain powerhouse, had a clear postponement strategy that defined how late – and therefore where in the supply chain – a generic mobile phone became market and customer specific. This gave Nokia the flexibility to better respond to demand, whatever the forecast was. Today, companies go even further and use inventory optimisation algorithms to place the optimal inventory of generic or semi-configured products along with key components to enable the last minute flexibility to build whatever configuration is required at the lowest possible cost for the supply chain organisation.
“At the operational level, companies have to deal with the fact that reality is always going to be different from the plan. Having a well-designed supply chain is no guarantee that a company will always have the right product in the right quantity at the right location when the actual demand comes in. What distinguishes leaders from other companies is that they are better at sensing demand and supply changes and responding quickly and accurately. In that sense, supply chain design is only a prerequisite for running a responsive supply chain.”
Byrne highlights a number of key characteristics of agile companies:
l Get a quicker and more accurate read on the actual demand and forecast. Leading consumer goods companies, who are particularly exposed to the uncertainties of the retail/consumer markets, have over the years invested in newer demand sensing technologies that provide them with a much more accurate picture of future demand.
l Connect electronically not only to retailers but also to all the other actors of their supply chain – suppliers, co-packers and other contract manufacturers, warehouses, logistics providers, etc. This is the foundation that gives companies a complete, end-to-end picture of the current status of the supply chain.
l Use state-of-the-art planning applications that give them rapid decision support with what-if scenario capabilities.