Despite its many talents, RFID has never really had a seat at the logistics table. But with an increasing desire for transparency, will the qualities of the technology finally be realised? Alex Leonards reports.
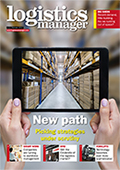
RFID is considered a mature technology by some, including Uwe Henning, chief executive of real-time analytics company Detego. Henning considers the technology to be well-developed and used in closed loop applications like asset tracking and automotive logistics.
But last year Detego, which specialises in providing transparency for the fashion industry, finally saw RFID finding its feet in the fashion retail supply chain. Detego’s growth is chiefly coming from this sector.
“In retail smart shelves, RFID ceiling readers, interactive displays and digital fitting rooms are starting to move beyond the drawing-board as retailers acknowledge the benefits of improved customer service and more revenues from near hundred per cent inventory accuracy,” says Henning.
SML RFID has also seen a steady implementation of RFID within the market over the last year.
“In the retail apparel sector in particular we are seeing significant uptick in adoption of the technology,” says Dean Frew, CTO & SVP RFID Solutions at SML Group. “I believe this is partly because we have seen proven business cases from brands such as Tesco and Herman Kay who are leading the way in RFID adoption.”
Implementation of RFID in the fashion retail supply chain has been prompted by retailers and third party logistics providers having to manage ever-growing global value chains. As well as expanding supply chains, advances in technologies like RFID and rising consumer demand for shorter delivery times is driving the need for heightened visibility.
Almost all retailers and their logistics partners now want real-time knowledge of where their goods are located in their national, international and global supply chains. In turn, Internet of Things (IOT) projects are being used more so than ever before. While it sluggishly rolled along in the past, RFID can now directly address this demand for better visibility and transparency across the supply chains of a number of industries.
“Besides the tracking of assets, like containers, the real-time knowledge of what is going on with each individual item and where that’s happening is on the rise,” adds Henning. “It’s clear that this event tracking and using real-time analytics in SCM only really works with technology that’s fully automated, without the need for a human using a scanner.
“RFID delivers exactly this real-time, automated event reading.”
According to Howard Forryan, product market specialist at Harting, the German manufacturer of RFID transponders, the technology has been persistently evolving over the past couple of years. He says that with recent developments in the passive Ultra High Frequency (UHF) performance area, RFID is now accepted as a technology that can bring both technical and commercially viable improvements to a warehouse’s logistic management operations.
“With the advent of Industry 4.0 and its potential implementation across all areas of manufacturing and the support supply chain, RFID will play a key role in bring these environments together in real time under the umbrella term of “manufacturing logistics,” says Forryan.
He believes that both barcodes and RFID have a place in today’s markets, while RFID is likely to becoming increasingly popular in the future.
“In terms of supply chain and logistics applications, RFID is not mainstream compared to barcode but is often used in situations where line of sight is not viable, or for rapid and secure data capture on large volumes of items contained on pallets or trays,” says Jonathan Bellwood, founder and chief executive of Peoplevox, the e-commerce specific warehouse management software company. “However, RFID as a whole is a valid technology solution in many other areas.
“It is widely used in a variety of applications from manufacturing to hotel room access management systems, for reading ski lift passes, not to mention Oyster Cards.”
Bellwood points out that from a productivity and accuracy perspective, RFID technology allows the collection of more data in one swipe compared to barcodes. “However, the higher cost of RFID systems compared to barcode means the latter is more commonly used in the supply chain,” he says.
Although RFID is able to improve speed for stock takes with tags applied at the source and right the way through the supply chain, not many businesses apply this across the supply chain.
“…few organisations do this from end to end,” says Bellwood. “Overall, the cost/benefit ratio of RFID within the supply chain prohibits its widespread usage.”
Detego’s Henning says that people working in the retail industry have lots of doubts about implementing classic handheld readers, because they still look like bricks.
“People now expect a smartphone type device, but clearly the traditional techniques spearheaded by the AutoID industry still seem to prevail,” he says. “As soon as one of the big tech players like Google enters the marketplace, we’ll see an exciting change here.”
Frew says that like any other disruptive and transformative technology, RFID provides a new and significant opportunity to transform the industry inwards out.
“However, this type of change is often met with various levels of scepticism and resistance,” he says. “We are seeing organisations that are aware of their current inventory accuracy challenges and want to move to fix this.
“Right now RFID is the only answer and the solution requires placing RFID tags on the product at source and then implementing a solution that supports the process in store.”
For now it seems that RFID technology remains a few paces behind where the market would like it to be. But its growing place in the fashion supply chain gives us a glimpse of where it could be in the next couple of years for retail and beyond.
New developments
l Passive UHF technology has become the global standard across vertical markets, according to Detego chief executive Uwe Henning. This means that tag prices have been reduced to a very low level – almost zero in comparison to the products they’re actually tagged to.
l Reading devices are becoming more sophisticated. Zone-reading RFID readers are providing a three-dimensional analytical view of the supply chain which can help improve the management of time, resources and space. “A proliferation of mobile devices, cloud-based solutions and cheaper and smaller sensors to continually stay in touch is certainly making RFID more of a reality,” says Henning.
l According to Peoplevox’s Jonathan Bellwood, there are not many new developments. “Chips, and therefore devices, remain expensive and the relatively low number of device manufacturers means there is little competition,” says Bellwood. “However, one of the most innovative data capture solutions gaining traction is the combination of data and image capture using RFID devices integrated with HD cameras.“
l The biggest trend SML RFID has seen is around how retailers and brands are leveraging the technology in scaled production rollouts in the same vein as Tesco. SML RFID’s chief executive Dean Frew refers to Tesco, who implemented the technology for its clothing brand F&F. “In addition we are seeing numerous retailers and brands adopting RFID solutions within various stages of their supply chains, similar to outwear brand owner, Herman Kay,” says Frew.
l The new generation of RFID transponders hold a lot more memory, according to Howard Forryan, product market specialist at Harting. “Besides the EPC section, used as a serial number, you also have the user section of the transponder,” he says. “Traditionally this is in the region of 512 bits, but we now produce a 3.3 Kbit version.” This kind of size can enable the storage of complex data which can tell a user when an item is due to be serviced. This could be read automatically when a tag passes a reader in a conveyor line.
How does it work?
There are four layers to an effective RFID system, says SML RFID’s chief executive Dean Frew. The first involves the collection of raw data, the second a user interface which performs tasks, the third is a back-end enterprise platform, and the final layer is a business intelligence solution. “Each layer is required to ensure RFID is used in an effective way,” says Frew.
Howard Forryan, product market specialist at Harting, says that RFID transponders, otherwise known as tags, can be fitted directly into metal-based multi-item carrier rails. These are used in large clothing retail distribution centres.
“Relevant control data can be instantly written to such tags (96 bit to 3.3kb options dependent on tag type) as the rails pass through a defined incoming goods gate where an appropriate UHF antenna and reader would be located,” says Forryan. “Specifically chosen tags have the capacity to accept more stored data for additional control actions at later process stages.”
Add-ons like extra antennas, scanners and readers can be integrated into a conveyor system at different points, which identify the location of rails and move them to their pre-defined storage position.
“In these situations, typical tag read distances are four to five metres, but up to ten metres can be achieved with certain antenna/reader combinations, dependent on the reader’s power rating,” says Forryan. “Once all garments have been removed from the transport rails, they can be re-introduced into the system by overwriting the data on the RFID tag and appropriate new data applied.”
He says that the key to having an efficient and worthwhile RFID application is flexibility. If its possible to put read points around the whole warehouse, where tags are definitely going to pass, then there is start to finish, total visibility of the warehouse. This limits the need for stock checking, and completely gets rid of the need for manual read processes.
“Properly specified and appropriately mounted RFID tags are also far more robust than barcode labels, meaning that locations are less prone to ‘loss’ caused by unreadable labels,” says Forryan. “Also, because they can hold data as well as simply be ‘associated’ with database records, data can be passed into and out of the management control system as physical items enter or leave the warehouse.”
Detego’s chief executive Uwe Henning says that it is essential to use software to make sense of all the data after its been collected. Its own software provides real-time analysis of what is needed, when and where.
Jonathan Bellwood, chief executive of Peoplevox agrees: “Retailers, warehouses and any supply chain operation can only be as good as the quality and quantity of data they rely upon. This is irrespective of whether the data is being supplied via RFID or barcodes as both are purely a means for capturing data. When using either technology, or a combination of both RFID and barcode technologies in a retail warehouse or distribution centre environment, the data being collected must be quickly, easily and accurately fed into a central warehouse management system.”
Location, location, location
So where is RFID technology best suited? Well, it enables tags to be scanned without being in the line of sight. Several tags can be read at once and you can scan them at heightened speeds – these qualities make the technology fairly flexible.
“The ruggedness and long lasting design of some RFID transponders also makes it more suitable for harsh environments,” says Harting’s Forryan. “Certain hard tag transponders can endure wide temperature variations, high humidity and continue to be readable in dirty environments where the tag may become coated in oils/grease/paint/etc.”
These features could be advantageous in a cold room warehouse storage space. Harting’s own UHF Locfield flexible coaxial waveguide antenna is particularly well suited to large warehouse logistic conveyor control systems. The technology enables boxes to be tracked and traced around curves and in spaces where there appears to be no room for a scanner or antenna.
“Radial read range zones of up to 2.5 metres are achievable over the antennas total length of up to ten metres,” says Forryan.
Peoplevox’s Bellwood says that RFID can be suited to the data capture of very small items and perishable goods. “Where the ability to contain more data than is possible on barcodes comes to the fore,” he says. “For example, with tags embedded on trays containing chilled or frozen foods the addition of latest put away/store by data is a prerequisite.”
But according to SML RFID’s Frew, the single best case for the technology, within the supply chain, is in retail stores.
“This is where we are able to see significant benefits to retailers and brand owners in terms of improved inventory accuracy which enable stores to reduce shrink and provide a better omni-channel experience for their customers,” he says. “For retailers, RFID also removes the need to use third party audits.”
Previously, retail brick and mortar stores would do a manual stock take every month. But of course the stock would fluctuate, and in a matter of days, the data would be out-dated and incorrect.
“Now staff can complete a full stock take on a weekly basis, therefore improving the overall accuracy of their stock and ensuring this accuracy is maintained,” says Frew.
And, following the trends of larger warehouse distribution centres using latest automated storage and sorting systems, RFID is being applied and integrated by enabling critical operational location and control data to be added to warehouse management control systems.
“RFID can help optimise resource planning and help deliver better utilisation of employees time, offering considerable savings over manual barcode reading processes – for example the flexible deployment capabilities of Harting Locfield antennas making this possible in a wider range of physical settings,” says Forryan. “The elimination of manual barcode reading also enables improvements of throughput speeds and reduced handling time.”