The increasing importance of space utilisation in UK warehousing is seeing an increase in interest in the narrow aisle vehicle. Lisa Townshend reports.
Recent high street sales figures reveal there is a rise in consumers that choose to shop online. This means that warehouse and logistics operations are now a more fundamental part of UK retailing. However, as this development puts greater demand on storage and distribution, narrow aisle and very narrow aisle warehousing is a real option for generating additional yield.
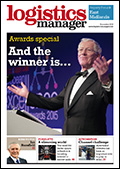
During 2007, immediately prior to the economic crisis, UK orders of very narrow aisle (VNA) trucks reached an annual high of just over 1,100 units: a combination of man-up and man-down lateral stackers and high level order pickers.
After years of recovery, UK market orders of VNA trucks are expected to bounce back and exceed 1,200 units in 2015, with a recent annual growth rate approaching 20 per cent. Some industry analysts are suggesting that the distribution sector – currently responsible for around 40 per cent of GDP – is likely to grow next year by three to four per cent, demand for even greater efficiency in warehouse operations looks set to become more acute.
To meet this increasing demand and ensure that more goods are moved cost-effectively, warehouse operations need to generate more productivity from their assets. A high level of flexibility is required if warehouse operators are to meet business cycle and demand changes, so it is important that materials handling solutions are capable of ironing out the peaks and troughs. What’s more, to operate at peak efficiency, warehouses must make optimal use of the space while also maximising output and productivity.
The challenge when determining current and future fleet performance is to get to grips with economy and function. Warehouse operators need to consider factors such as aisle widths, picking heights and the safest and most efficient method of operating.
Operating in narrow aisles allows the warehouse to increase its storage density while still allowing one hundred per cent stock selectivity. There is therefore a requirement to move higher volumes quickly and safely while avoiding congestion and bottlenecks.
Clearly, narrow aisle trucks should be capable of lifting high enough to cope with the height of the racking. Truck flexibility – the ability of trucks to elevate quickly and smoothly, with sufficient load capacity – is also an important consideration.
Although there has been a large number of improvements made on VNA trucks, product development hasn’t really seen a massive step change. Instead, the investment seems to have been directed towards adding value in picking technology and automated/semi-automated systems that often operate alongside VNA solutions.
Phil Tunney, head of national sales training and product development at Toyota, explains: “There have been developments in areas such as RFID and Personal Protection Systems (PPS). RFID technology allows for operators to position a truck when it links with Toyota Navigation Solutions (TNS) and allows for greater operational efficiency by guiding a machine to its next location on the shortest possible route.”
“PPS is a system that monitors what is around a VNA machine and reacts accordingly when another machine or pedestrian is detected,” Tunney continues. “It improves safety across the operation and reduces the likelihood of a potential collision.
“Their big plus is that VNA machines allow for more racking within the operational space and since more extensive racking means more pick locations, a greater number of SKUs can be stored within the space.”
Changes
John Maguire, sales and marketing director of Narrow Aisle, says: “We are likely to see changes in the type of trucks specified for different applications. For example, the man-up turret truck, which has been a feature of warehouse operations for nearly four decades, will, I believe, start to be seen by many as inefficient and costly technology.
“30 years ago it was felt that the ‘man-up’ truck could provide cost efficient customer order picking but, for many applications, there are now more time and cost effective alternatives than elevating the man to the goods.
“The move away is likely to accelerate and is being driven, in part, by the development of modern CCTV systems are capable of giving the operator a high definition view of his forks and the load at any height – something that people could only have dreamed of as recently as three years ago.”
“Truck ergonomics plays an increasingly important role,” says Paul Smith, VNA and warehouse systems specialist at Yale. “Asking more from a truck invariably means asking more of an operator, so proper consideration must be given to operator safety, comfort and well-being. Raising the operating position is a major advantage, as this allows better visibility of the pallet at all times, while also enabling the driver to perform piece picking when required.
“Cushioned floor space to absorb vibration and operator presence foot pedals should also be considered. Pedals activated by the driver’s feet provide a comfortable operating position and are easily fitted and affordable. Depending on the application, the added flexibility that comes from the operator’s ability to sit or stand can be achieved with trucks that have a three-way adjustable forward-mounted controls arrangement or seat-side located joystick controls positioned vertically or horizontally.”
Warehouse operators need to work smarter
Les Knight, Yale sales director at Briggs, states: “To meet rising demand, warehouse operators need to work smarter and that means finding cost-effective ways to improve their materials handling performance to increase overall productivity.
“It’s not just a question of increasing the number of trucks to cope with demand, either. This is far too simplistic an approach and is likely to result in congestion and bottlenecks in aisles that are already occupied. More and more supply chain businesses are therefore coming to appreciate the benefits of VNA machines, which now routinely feature in the equipment list when warehouse operators decide to upgrade or expand their materials handling fleets.”
It seems the warehouse world is getting slimmer. Long live the narrow aisle.
Case study: Reconfiguring the DDH warehouse
EK Automation was commissioned for a complete warehouse system for global packaging specialist Deufol België NV/DDH Logistics at Heist-op-den-Berg, Belgium.
Primarily DDH Logistics wanted to replace only its old narrow aisle trucks. But, after a planning phase it was decided to go for full modernisation, and DDH ordered the complete automation of the warehouse in Heist-op-den-Berg. The product was mainly Duracell batteries for packaging and shipping directly from site. The new system is geared towards the Christmas peak season, where output peaks with a throughput capacity of more than 150 pallets/load cycles per hour. In total more than 30,000 pallets in 36 storage aisles with a length of 65m and a mix of racking heights to 10.5m.
The hybrid navigation combines the inductive navigation in the storage aisles, with the flexible laser navigation in the outer storage area, which can also be optionally switched into manual operation if required. The “Fly on the spot” exact positioning compensates for any intolerance in the floor, on vehicles and the racks, and to prevent damage or collisions. Empty transports and rack changes are minimised by the intelligent control station EK OS 800, which is issuing transfer orders to the vehicle via WLAN, and is connected to the DDH-warehouse management system. The EK software engineers also created an individual customer’s interface for DDH Logistics.
Case study: Boosting capacity at Bluemay Weston
Component manufacturer Bluemay Weston decided earlier this year to reconfigure the pallet racking within the existing facility around a narrow aisle layout and replace the counterbalanced truck with a Flexi AC NANO articulated truck.
The company produces a range of non-metallic components used by manufacturing companies operating in industry sectors as diverse as aerospace and cosmetics.
The 25,000 sq ft warehouse alongside the factory was purpose-built in 2008 but, with the company’s output growing all the time, the warehouse’s original layout was not able to cope with the resultant increase in throughput of raw materials and components leaving the production line.
By condensing the warehouse aisles, Bluemay Weston was able to accommodate extra pallet racking locations within the store. The height of the racking was also increased to 5m at the top beam. These steps resulted in an increase in pallet capacity at the unit of more than 50 per cent.
The Flexi AC NANO articulated truck is more space efficient than the truck that Bluemay Weston had previously relied on within the store. The Nano was introduced to provide a lower cost, entry-level articulated forklift that can lift loads weighing up to 1.6 tonnes to heights of up to 5m. The truck’s front end and load can articulate through 220 degrees.
The change has more than doubled Bluemay Weston’s storage capacity, enabling the company to buy in raw materials in greater quantities than was previously possible – something which has not only resulted in a drop in the purchase price paid but has also alleviated a potentially sticky production issue.
Sales manager, Kevin Bendle, says: “Such has been the increase in demand for our products since the warehouse was originally built we only had the space to store some six weeks’ worth of expanded polyethylene – one of our key raw materials.
“Our expanded polyethylene supplier is based in Belgium and was quoting a lead time between ordering and delivery of eight weeks. With only enough storage capacity to hold six weeks’ stock we faced a potentially devastating supply chain shortfall.
“However, thanks to the extra pallet capacity the re-configuration and the Flexi NANO has brought, this is no longer an issue.”