Will augmented reality revolutionise the future of order picking? Alexandra Leonards takes a look at smart glasses and their place in the market.
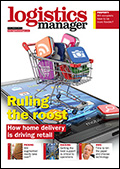
Technology is crucial to the development and transformation of a warehouse. It can dictate the entire flow of an operation; it can mark the success or failure of a project. Getting it right is paramount – especially while new pressures on the logistics industry mount and edge to the fore.
It is not the time for feeble choices when it comes to technology, but for bold innovations that are designed to disturb the natural current of the logistics space.
“You could compare it to a headset display in a car – kind of like an assistant,” says Johanna Bellenberg, Picavi. Once a pick-by-light company, Picavi was established when the business decided there must be an easier way to pick items in the warehouse. For over two years it developed the software behind smart glasses for order picking.
Picavi smart glasses project virtual items into reality by using a transparent overlay, acting as an assistant to reality which is able to guide workers throughout a warehouse operation.
Although smart glasses have certainly revolutionised the Picavi business and purpose, some still think the technology isn’t ready for the market. “The smart glasses market integrated into the order picking market, at its current stage of development, is too far removed from reality and working norms to become a viable technological solution for this activity,” says Chris Tozer, UK territory manager at Ivanti (formerly Wavelink).
Tozer believes that the technology demands an entirely new perspective, and that this significantly impacts on how an individual operates.
“Not to mention some of the health and safety and logistical issues that may be caused from integrating technologies across an organisation, for example handling machinery, or warehouse safety,” he says. “The technology and methodology behind smart glasses certainly holds strong potential, especially when integrated into this market – however we are not there yet.”
But the glasses aren’t a pilot for Picavi; they’re being used in real operations. “We have a lot of different kinds of customers, including globally active companies,” says Bellenberg. Arvato SCM Solutions’ order-picking project for German audio company Sennheiser is one example.
Swisslog, the automation business, sees the benefits of augmented reality – and believes its presence in its own logistics space is inevitable. “It would appear that the writers of Star Trek were clearly on to something,” says Brian Whale, senior logistics consultant at Swisslog. “Most of us now carry a communicator, some even have a wrist-mounted screen.
“Soon we will have “virtual all round vision” to support daily activities in the form of smart glasses.”
Whale says that virtual reality headsets are becoming commonplace in the gaming world, and that they will soon become part of Swisslog’s intralogistics world. “I am an old man but these innovations even have me hooked,” he says.
From a safety perspective, Bellenberg stresses the stark difference between virtual and augmented reality. The virtual form completely shuts off reality, and the picking glasses have a loose connection to this. But augmented reality is different because it combines reality and the virtual world.
One Picavi customer was concerned that the technology might not work effectively in a warehouse with ten-metre racking. The customer thought that the angle of the storage space would impact the vision of the operator. But, according to Bellenberg, because the virtual display is above the eye line, it doesn’t disrupt natural vision. As well as this, because the glasses simply display the information you would normally see on a manual list, there isn’t an overload of information.
“A very important feature is that you can work hands free, so the system maximises productivity,” she says. “With high times savings between 12 and 40 per cent.”
Smart glasses deliver adaptable layouts; bespoke to the project at hand, as well as significant error reduction. If a mistake is made, or something is scanned incorrectly, the glasses won’t continue until the correct barcode or item is scanned.
Evolar, which too supplies augmented reality for the warehouse, has its smart glasses on the market, and is piloting with a number of postal companies. But Dirk Matheussen, founder of the company, says that because the technology isn’t mature enough, the industry won’t really see it take off until 2019/2020.
David Myers, chief executive of Touchpath International, agrees: “It is a technology that could be used in the warehouse, but is subject to more trialling. The market is waiting for it to be proven. But thinking outside the box, this or similar technologies might be more useful where the data is changing dynamically.”
Myers uses the example of container loading, suggesting that as the container is being loaded, using the real time information that it sees, the augmented reality system can calculate where everything has to be positioned to maximise the efficiency of the fit.
Evolar’s Matheussen says that with mixed order picking becoming more prevalent due to the rise of e-commerce, the warehouse is getting even more complicated. Alongside this, demand capability is getting higher and higher. According to him, the simplicity of augmented reality technology presents an opportunity to deal with some of these new challenges. Warehouse workers are totally guided through the warehouse, hands free, and they don’t need a lot of pre knowledge to use the glasses.
In some areas of picking, says Matheussen, the activities are highly automated, for example pallet picking with reach trucks and AGVs. So on one side of things, there is increasing automation for one-size products. But, with high density picking jobs, and lots of variability in the e-commerce market, there is a need for more flexibility – especially now that consumers can order something in the morning and receive it in the afternoon.
“It’s the same for sorting product packages with big differences in sizes,” he says. “It’s difficult to automate – so there’s lots of opportunities where we can make a difference.”
Myers says that one scenario where he can see smart glasses doing well is picking optimisation.
“Each picker views a digital pick list on a heads-up display wearing (say) Google glasses; then, when they select an item the display calculates the most efficient path through the warehouse to guide the user to the package, before auto-scanning it as picked,” he says. “In reality you can also do this on a handheld terminal, or by voice, or on a mobile.
“The glasses simply provide a different way of delivering the same information.”
But Matheussen says that many customers with voice picking systems now want to get rid.
“It takes a while for people to get used to it – there’s a high learning curve,” he says.
Order-picking systems must be flexible and capable of switching in new people and labour, especially during peaks like the Christmas period. And according to him, voice picking requires lots of training.
“The training of the workers is very, very short,” says Picavi’s Johanna Bellenberg. “With an MPA hand scanner it takes two days.” Picavi’s customers have said that with their system, workers are ready 20 minutes after first using the technology.
“It’s already cheap,” says Matheussen. “Normally the return on investment is six months.
“It’s more about the acceptance.”
Matheussen says that regardless of the flexibility of augmented reality, it’s still a big change for businesses. “They have to wear something, so there’s some resistance there,” he says. “There’s still the need to convince people.”
However, he stresses that the industry is very much interested in the technology. According to him, people using visual technology generally experience less stress than those working with a paper based system. This is because users don’t have to worry about making mistakes – the system helps when something goes wrong a long the way.
“Out on the field if they have an issue, they call an operator, or they do Skype, or send pictures back to the operator,” he says. “And then there’s lots of calling and discussion about the picture.
“We have developed a remote support – the camera opens a live stream and you can start streaming data to the operator, with snapshots and annotations so they can see what you have to put attention on.”
In other words, the operator can have live interaction with the person in the warehouse and intervene directly. Which solves the problem while saving time and money. “A combination of voice and visual will happen – I think that will be the future for a lot companies,” says Matheussen.
Technological inroads into labour intensive market
According to robotics company Eiratech, most of the new technologies that are on the short-term horizon are variations of platforms and models that already exist in the market. “Advances in voice and light guided systems coupled with smart glasses and some new ‘cobots’ will all make further inroads into a sector that is slowly taking itself out of the traditional, more labour-intensive approach to order picking,” says Alexey Tabolkin, chief executive of Eiratech. “As the growth of the e-commerce share of the retail markets continues to grow, there should be more enthusiasm to embrace these technologies in the challenge to tackle the changing dynamics of small order fulfilment.”
Chris Tozer of Ivanti, says that contrary to some thinking, the increasing fragmentation of retail orders and the variety of locations needed to distribute to, means that human interaction in the order picking process will continue to rise. “Within full pallet operations however, I certainly see the future hosting a rise of robotics in the manual picking and handling element of these operations,” he says. “In more systematic order processes, where flexibility and tailoring of orders is not needed, the rise of robotics and machine learning, will improve the speed and consistency of order picking on a large scale.”
Touchpath International’s chief executive David Myers says that today warehouse management systems have to support both zone and wave picking. “Where the order is split across different zones different pickers are picking the order at the same time; then it all comes together,” he says. “In wave picking the pickers are picking bulk – picking the same item for several orders at the same time.” Picked goods are then split into individual orders, then packed and shipped. “The trend now is towards warehouse slotting solutions – ensuring the fast moving items are at the front of the warehouse, to speed fulfilment,” he says. “The picker then does not have to move more than a few feet to reach a fast moving item, and may be doing so twenty times a day; whereas the slow, once-a-month item is stored further back.
“Big Data analytics now supports huge warehouse slotting algorithms. These enable the system to tell you where each item ought to be stocked – which location will maximise efficiency.”
Swisslog has noticed an increase in demand for automated item picking robotics, automated case pick systems and automated mixed case palletising. Brian Whale predicts a push towards more automation in the picking market over the next two to five years. “Our robots are already able to interact with human operators to work as a team; robots can pick up to 30-60 per cent of the customer’s product range and a (human) operator finishes the order,” he says. “We predict this will continue to be a popular option in the near future, providing a big stride into the Industry 4.0 warehouse of the future.”
Myers says that companies are beginning to trial picking robots. “The robot retrieves a tote from the racking in the warehouse, brings it to a bench where a person picks out what is required, after which the robot returns the tote to the relevant racking location,” he says. He also says that autonomous vehicles are coming to the fore. “The warehouse operative completes the pick before putting it on (usually) a wire-guided vehicle, which then takes it to the packing or shipping area,” he adds.
Smart glasses save time
In November last year Arvato SCM Solutions started an order-picking project for Sennheiser using smart glasses. The company says the technology saves time and ensures a smooth flow of materials.
“We’re very pleased to have a service provider like Arvato at our side, one that not only shares our point of view with regard to innovation and development but also invests in the actual implementation,” says Günther Maaß, global logistics manager at Sennheiser.
A display integrated into the glasses gives warehouse employees all the necessary context-related information and navigates them through the work process.
For purposes of the project, a separate pick process was identified in advance together with Sennheiser so that processes can be carried out in a controlled environment and evaluated with precise time measurements.
Arvato says initial feedback from employees on the operational side of the business is positive: the new pick technology is easy to learn and intuitive to use.
“With our pick-by-vision solution, the pickers have both hands free and their eyes on the current process steps at all times – in contrast to the work with hand-held devices,” says Dirk Franke, chief executive of Picavi. “Instead of relying on the tiring voice commands of pick-by-voice systems, our system inserts data directly into the field of view of the worker in real time.”
Over a number of weeks, the collected data was compared and evaluated. During this time, the Arvato employees continued to wear the mobile WLAN smart glasses to get used to them and be as prepared as possible for the coming peak season of growing order volumes.
“Innovations are not ends in themselves; they are absolutely necessary to realise competitive advantages and further growth,” says Patrick Manders, VP global solution design in the business unit hightech & entertainment at Arvato SCM Solutions. “Targeted innovation management helps companies increase their competitiveness, efficiency and sustainability.”