Forklift trucks are not only getting cleverer, the cost of sophisticated technologies is coming down. But buyers still have to think hard about the options available. Malory Davies reports.
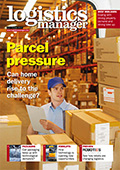
Logistics operators are looking for increasingly sophisticated functionality from their materials handling equipment as technological innovations open up new opportunities.
“Automation is now a key driver in the development of forklift trucks and creating an end-to-end intralogistics solution to increase efficiency throughout the supply chain,” says Steve Richmond, director – logistics systems at Jungheinrich.
“Innovation within laser technology, for example, has seen a huge impact on the increased amount of automated guided vehicles (AGVs) that are now available and in use.
“The Internet of Things (IoT) is also emerging as a key driver within development. Currently almost every piece of equipment in production has the processing capability to communicate with another device. The data collected from this will be invaluable in creating and enhancing solutions that enable organisations to transition to an end-to-end automated supply chain.
“Additionally, battery technology is under constant review to ensure trucks are economical and eco-friendly. With faster, shorter interim charging times and zero maintenance, lithium-ion battery technology has enabled organisations to keep up with an ever-changing landscape where organisations need to allow for more flexible working,” says Richmond.
Simon Barkworth, managing director of Crown, highlights the fact that increasingly, managers of logistics operations need more and more information on which they can base key operational decisions, whether around fleet sizing, reducing costs, streamlining processes, improving safety or maximising productivity.
“This can be achieved through the ‘connected’ experience – the ability of the lift truck to collect and share real-time information and to be able to share that information with both the operator and the warehouse manager. Furthermore, lower component pricing as well as rising labour costs are only now starting to mean that the implementation of some of these technologies are commercially appropriate in our industry. Total cost of ownership and return on investment are among the key elements when we design our equipment – it’s a hard balance to attain, but we believe our products have achieved it,” says Barkworth.
“Affordable automation” is a key theme for Hyster, Industry manager Tracy Brooks says: “ New self-drive lift truck solutions from Hyster Europe will enable businesses in the automotive supply chain, for example, to introduce “affordable automation” for repetitive handling tasks. Intelligent Hyster trucks can help support Industry 4.0, the fourth industrial revolution, through reliable consistency, with the flexibility of manual use to perform additional tasks and support the ‘unexpected’.”
There is considerable concern across the UK logistics industry about the impact of Brexit on the availability of warehouse staff. “Brexit appears to have focused peoples’ minds that the ready supply of good quality warehouse personnel may diminish in the future, and so companies are now looking to see what technologies they can use to reduce the reliance on staff resources,” says Barkworth. “We have anecdotal evidence from both customers and manufacturers of automated trucks that there has been an increase in interest of various types of semi or full automation since last summer.”
Richmond points out that organisations are under pressure to review all areas of their warehouse and business operations as a result, to ensure they drive efficiencies and facilitate a 24/7 approach to logistics and supply chain operations.
“A company that five years ago would have been handling single carton units may now be handling single items, and the technologies associated with that will need to keep pace with the change in customer demand. As a result, businesses are moving away from an isolated view of buying or hiring a single truck, for example, and are instead looking at the processes and solutions that will drive efficiencies across the business as part of a wider strategic approach to integrated intralogistics solutions.
“Organisations will therefore benefit from a consultative approach, working with suppliers for the exact mix of automated, semi-automated and manual solutions to meet their individual needs. In today’s ultra competitive e-commerce climate, businesses that do not consider solutions in the context of their end-to-end operations run the risk of perpetuating inefficiencies that they are running out of time to address,” says Richmond.
Cost is always going to be a critical issue for operators. Steve Richmond of Jungheinrich says: “Supply chains have already undergone a huge transformation as a result of e-commerce, and many organisations now live or die by their management of orders, deliveries, returns and customer service. An efficient supply chain is now arguably as significant for a business as its core product or service offering, and technology innovation is now vital to generating the next level of efficiencies and the reduction in operating costs necessary to meet changing demand while remaining competitive.”
Crown’s Simon Barkworth argues that by adopting the right type of technologies suitable for their specific application, customers can gain tangible benefits. “It sounds simple, but whether it is downsizing the fleet, increasing productivity, streamlining processes or reducing damage costs – the potential gains are there in terms of making the customer more competitive in their particular market. It starts with full visibility of the operation; InfoLink with the FleetSTATS cost management solution provides this full visibility to equipment utilisation, cost of operation, operation performance, equipment status, energy, and service.”
And Hyster’s Tracy Brooks highlights the fact that repetitive lift truck tasks can be unnecessarily expensive and there is a risk of human error, which may make damage or delays more likely. “Automating these activities can help reduce these costs and offer a good return in the right applications.
“Using a fleet management system such as the Hyster Tracker can also help to increase driver accountability in operations, implement better driving practices and reduce stock and equipment damage.”
How to minimise the pain
Making the transition from manual systems to automated does not have to be painful. In fact, it can be possible to move from manual to automated at the flick of a switch. Crown’s Simon Barkworth says: “Our thought process is to offer ‘dual mode’ trucks that can be switched immediately from automated to manual mode, and vice versa. This approach also creates its own challenges – for example, you need to consider where to place and protect the various automation safety features, such as lasers and RF units, so that they don’t impede an operator when the truck is in manual operation mode. We believe that we have got the balance right in our design approach.” AGV solutions from Hyster are based on Hyster’s trucks with the addition of AGV control systems.
Tracy Brooks says the automation hardware neatly interfaces with the truck’s electronic systems allowing them to be used manually when required. Induction loops, camera systems, lasers, GPS, or a combination of several systems may be used depending on the application. Barkworth points out that semi-automation offers a big opportunity to solve real customer issues. “We see the interest in semi-automated lift trucks growing all the time – for example our Automated Positioning System on our TSP VNA truck, or QuickPick Remote on our picking and tow tractor trucks. Customers see semi-automation as the ability to keep flexibility and make their operators’ workload easier while at the same time increasing throughputs and efficiencies. We concentrate on improving segments of the operation that could benefit the most and which offer the greatest ROI.”
Steve Richmond emphasises the importance of taking a holistic approach to automation: “In the first instance, some may be inclined to consider a complete overhaul of systems, however a company needs to assess and analyse where automation will benefit the business most. If this is done then there is a place for semi-automated solutions to sit alongside fully automated and manual solutions as well. As a greater understanding of the benefits of automation evolves, so to will the demand for a bespoke set up. While a fully automated solution might be ideal for certain operations, others may require a more manual, people led approach,”
Technology
Crown lighter-weight pallet truck
Crown has launched the WP 3010 electric pallet truck, extending the forklift manufacturer’s WP 3000 Series of pallet trucks. Weighing from 279 kg (without battery), the new truck has a load capacity of up to 1.6 tonnes. “Our new model is a compact, agile, lighter-weight addition to the popular WP 3000 Series. It’s a smart solution for all kinds of applications in the food retail, beverage and logistics industries in particular,” said marketing product manager Christian Rotter.
UniCarriers unveils ten trucks
UniCarriers is unveiling ten new TX counterbalance trucks as it revises its family of three and four wheeled forklifts. The trucks have maximum lift capacities of 1.25 to 2 tonnes. Innovations include electric steering with a steer-by-wire-system, and an automatic parking brake. The noise volume when handling loads has fallen by 8.2 dB to 63.3 dB compared to the former model. The revised product family comprises seven models with three wheels (TX3) and three models with four wheels (TX4). The TX4 is now available in two chassis lengths and TX3 in three to fit a wide range of applications. All models are designed for lifting heights of up to 7,000mm and can reach a maximum speed of 16km/h (TX3) respectively 17km/h (TX4).
Linde driver assistance system
Linde Material Handling has launched a digital driver assistance system for pallet stackers. “Ensuring operator safety is an integral concern when we develop new trucks and software,” said David Bowen, warehouse product manager. “As with systems such as Linde Safety Pilot and Speed Assist, the Linde Load Management System is another example of our commitment to improving warehouse safety.”
BYD increases presence in UK
Chinese forklift manufacturer BYD has now expanded its dealer network in the UK and Ireland to 11. The company, which entered the UK market a year ago, says its iron-phosphate battery technology can cut operating costs by up to 40%. BYD’s charging system means there is no gas emission, saving costs by eliminating expensive special charging rooms and battery maintenance. Typically batteries will recharge in around 1 hour from 80% depth of discharge and can be opportunity charged, it says. BYD offers a warranty of eight years or 10,000 operating hours on the iron-phosphate battery.
TCM launches new forklift
TCM has launched its new TCM 3-wheel counter-balanced forklift saying it offers the lowest energy consumption within its class with 4.2kWh/h energy consumption. The forklift includes a handling and travel system that assists with safety in areas such as: lifting, tilting and travelling. These areas are balanced by load, lift height and tilt angle. As well as this the trucks come with dynamic cornering control.
Fronius Li-ion charging system for Linde
Fronius Perfect Charging has developed a series of battery charging systems for Linde that are specially designed for use with lithium-ion batteries. The systems are available in the 9 kW and 18 kW power categories. Linde offers five different counterbalance trucks with load capacities of between 1.4 and 1.8 tonnes, equipped with lithium-ion batteries from 13.1 to 45.7 kWh. The charging time can be reduced to as little as 50 minutes, depending on the strength of the charger and the size of the battery – for lead-acid batteries, this is normally between seven and eight hours.
Seegrid self-driving pallet truck
Seegrid has launched a self-driving vision guided pallet truck called the GP8 Series 6 which is able to pick up and drop off palletised goods without human interaction. “The GP8 Series 6 closes the automation loop by providing an end-to-end solution, removing the need for human assistance to complete tasks,” said Jeff Christensen, vice president of product with Seegrid.
Acid test for electric dreams
The development of lithium-ion batteries means that operators of electric trucks now have a choice to make when it comes to the power source.
Jungheinrich’s Steve Richmond says: “Lithium-ion (Li-ion) batteries are not only maintenance-free, but they also offer extremely short charging times, which eliminates the need for a second battery in the majority of applications and means that fleets can be in operation continuously, 24/7. What’s more, since neither gasses nor acid are emitted by lithium-ion batteries, charging stations equipped with expensive exhaust systems are no longer required.
“That’s not to say that advancements haven’t also been made within lead acid battery technology; for example the capability to self discharge and the addition of overcharge protection. If looked after correctly and serviced at regular intervals, lead acid batteries can withstand long term use from light through to heavy application,” says Richmond.
Crown’s Barkworth believes that the operation must be suited to the adoption of Li-ion. “The biggest consideration is whether you have the ability to provide the frequency and time to perform several ‘top-up’ charges throughout each of the various shifts. An ideal application would be retail back-of-store or on a loading bay where the truck isn’t in constant use and can regularly be put back on charge. If a customer could modify their operation sufficiently to allow the adoption of lithium-ion, then the potential benefits could be large, from lowering their overall costs to improving health & safety as no battery changing or topping-up would be required. The current cost of converting to lithium-ion technology makes it difficult to achieve ROI in standard logistics operations.”
Anssi Laitinen of EnerSys EMEA highlights the development of a new type of lead-acid battery using a technology known as Thin Plate Pure Lead (TPPL) which offers a practical and affordable alternative to conventional lead-acid and lithium-ion designs. “Lithium-Ion technology requires a very high skill level to develop a well-functioning battery pack (software, hardware, mechanical, thermal, electrochemical, etc). This solid design cannot be adequately achieved in a small design house or groups with limited experience. TPPL technology builds on the proven capabilities of traditional lead-acid batteries with some significant technological advances.”
This means more energy and more power density than conventional units of the same size,” says Laitinen.
Hyster’s Tracy Brooks points out that for some automated operations, Hyster offers the option of LTO (lithium titanate) batteries with high speed charging, as the Warehouse Supervisor software can control which trucks go on charge in which sequence to maximise availability and avoid overload.
Hoppeke offers a range of fibre nickel cadmium traction (FNC-T) batteries which, it says, offer the vast majority of the advantages of lithium ion but only cost around three to four times more than lead acid. “If a lithium ion battery was discharged to 50 per cent and recharged, it could achieve up to 10,000 cycles whereas an FNC battery would offer around 8,000 – this compares with the 1,500 available with a lead acid battery. While lithium ion batteries don’t degrade at all, FNC-T batteries offer between zero and 2 per cent degradation – this compares to around 32 per cent with a lead acid battery. And in terms of efficiencies, the difference between lithium ion and FNC-T is just 0.2 per cent.”