As automation technology gets more sophisticated it is also getting more diverse, with more applications and new ways to boost efficiency. Johanna Parsons reports…
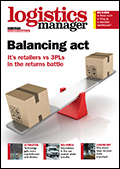
Warehouse automation has developed to amazing levels. The influence of e-commerce and the evolution of ever more sophisticated technologies means that previously unimaginable skills and speeds can be achieved with the latest systems. But high-end kit comes with a cost and it is imperative that aspiring automators thoroughly investigate what technology represents best value and, in particular, which areas of the warehouse would benefit most from an investment in automation.
One legacy of the e-commerce boom is that even tiny manufacturers and independent retailers are now having to deal with online order fulfilment. Retail peaks and the requirement to deal with multiple retail channels mean manual processes are often insufficient – and that means big problems on the warehouse floor. So the days when automation was exclusively for the big players are long gone. Regardless of size, any business considering taking on automated equipment will of course see return on investment as key so it is important to determine the multiple demands of the individual operation. To address these variables there is now a huge scale and variety of automation equipment on the market.
Eric Carter, solutions architect at Indigo software says that the firm has seen two distinct trends. Larger businesses with more ready finance are showing real appetite for robotics and AI, while he says “among smaller companies we have seen much greater use of automated conveyors and storage and retrieval systems, which are integrated with their WMS and picking systems. This provides them with a level of partial automation and improves efficiency levels for smaller companies who tend to have less access to the resources needed for full automation,” says Carter.
John Boulter, managing director of DHL Supply Chain Retail UK&I, agrees that there is no shortage of options for those wishing to take a more tentative approach. “There’s a vast range of well-proven technologies available to businesses wishing to automate,” he says. “We’re seeing businesses – in particular in the retail sector – investing in automated storage and retrieval systems to hold and automatically move pallets according to requirement. Meanwhile, semi-automated cranes, robotic shuttles, automated mini-load and sortation systems and auto-packing are just some of the ‘traditional’ modular solutions which DHL provides its customers to allow them to benefit from automation without the need for significant capital investment.”
Furthermore, Boulter says that it’s not always the cheapest systems that work out as best value. The less downtime the better the business case for automation in any specific area of the warehouse, and that can include high-end robotics. “It can take six to seven years for businesses to see a return on investment from full scale integrated automation projects, and they often involve significant changes to internal processes for full integration. Meanwhile, more tactical and stand-alone automated solutions, such as collaborative robots, can pay back in as little as 18 months,” says Boulter.
Finding the right solution to the right piece of the intralogistics puzzle is the aim, and the retail market in particular is evolving at such a rate that anticipating requirements is a real challenge. But the manufacturers are responding – not just with higher-tech equipment, but by developing existing technologies and pushing them into new areas of the warehouse.
“Which system is right for which element is constantly shifting, due to the ever-advancing technological development of each solution,” says Craig Rollason managing director of KNAPP UK. “For example, shuttle storage systems have become suitable for an ever-wider range of applications as they have become faster, taller, longer and deeper,” he says.
KNAPP’s Pick-it-Easy Robot was originally developed for the healthcare industry, picking individual boxes of medicines from a hospital pharmacy, for example. But the e-commerce demand for single item picks means its appeal is now much wider. “As this kind of technology becomes established and enhanced – and investment costs come down further – robots will become familiar features of warehouses across the UK.”
Rollason says that even if the business case for a robotic solution isn’t yet there, the demand for smaller pick orders fuelled by e-commerce has made picking accuracy paramount, and there are plenty of options. “Manual or semi-automated picking solutions can benefit from a variety of technologies aimed at improving accuracy such as RF terminals, pick-by-voice systems, pick-to-light technology or image-recognition solutions that verify the items picked.”
He says that many traditional reservations about robotics are now misplaced as robots now have the image-recognition abilities and fine motor skills required for order picking applications. In fact he reckons that robotic order picking will become commonplace in the next few years. But he points out that robots are nothing new in the warehouse. “The cost of robotic labour compared to human labour has fallen dramatically over the past 30 years. This has meant that a number of physically demanding and repetitive tasks – such as unloading goods from pallets or stacking them onto pallets – have been given to robots. Now technological developments have equipped robots with the image-recognition abilities and fine motor skills required for order picking applications,” says Rollason.
Indeed shifts in the supply and demand for workers is an important factor for many businesses looking to potentially invest in automation and robotics. DHL Supply Chain’s Boulter says “Automation technology can help tackle a number of issues across sectors, for example helping staff meet increased demand as well as the ever-growing need for efficiency and accuracy. It also helps to reduce the impact of some of the labour issues we’re facing as an industry, such as an ageing workforce and uncertainty around employment of non-UK nationals.”
Simon Cooper of Dematic agrees that labour issues are an important factor. “In large e-commerce fulfilment centres many hundreds of people are already employed as pickers and packers and, in key areas, finding staff is becoming increasingly difficult, but many more will be needed if the trend to online continues as predicted.
“Perennial fears over the loss of some manual warehouse tasks to robots could possibly stand in the way of a sensible solution to the problems of scale of demand and cost. A draft report to the European parliament, prepared by MEP Mady Delvaux in 2016, even raised the idea of a tax on robots. However, robots can increase the productivity of the existing labour force and would be invaluable in the boost to activity leading up to Christmas, when finding extra staff can be difficult,” says Cooper.
Cooper reckons the most influential fact is that robotics and automation radically improve productivity which helps businesses grow and develop, requiring more people to maintain systems and run the newly developed channels of growth. “Thus, the overall prospect for jobs remains positive going forward, although some roles may change,” says Cooper.
He re-iterates Boulter’s concern that finding labour for picking processes may become more difficult in the UK following the decision to leave the EU. He believes this will make investment in robotic picking an even more compelling option. “It seems likely that many retailers will choose to amortise the cost of automation over a longer time period, and so ensure operational efficiency and customer service, rather than be exposed to the possibility of being dependent upon a dwindling pool of labour, with the linked prospect of rising labour costs,” says Cooper.
It’s a complex issue, but the continued growth of e-commerce certainly emphasises the importance of throughput times and efficiency. “High labour content of manual singles pick operations supports investment in transport systems and end of line automation,” says Roger Platt, principal at LCP Consulting. “Flexibility is important and growth is difficult to predict. However, it’s difficult to see how a company with a manual, high volume, high labour cost labour model will remain competitive as automation becomes more widely adopted.”
Brian Whale, senior logistics consultant at Swisslog agrees that labour cost savings tend to be among the first that spring to most logisticians’ minds when weighing up the advantages of automation. But he says “Of course, there are other benefits related to picking accuracy, operating data and the ability to maximise floor space as well as the integration with other parts of the supply chain.”
And it’s not just single item picks for e-commerce that can benefit from the efficiencies of robotics. Dematic has developed shuttle based systems to deliver full cases of product in sequence to robots that pick and place product in mixed-cases onto pallets or roll cages ready to be unpacked on the shop floor. Swisslog also recently unveiled ACPaQ, a robot-based system for creating customised mixed pallets for individual stores from single-SKU pallets. It can set down up to 1,000 cartons per hour in the exact location predefined by the palletising software, and Swisslog says it has the potential to triple the speed of the palletising process.
Trailer loading
Dematic’s Weston says that automation is now stretching even further from the pick face, into the delivery vehicle. “Trailer loading and unloading is a further area of development and is something we are working on in the US.
“In essence we have mounted a robot on the end of a boom conveyor that can telescope into the rear of a trailer. Vision systems are used to recognise the build pattern within the rear of the vehicle – but it’s not just easy single SKU loads, it could be mixed loads. Under the command of intelligent software the robot identifies and picks unit loads and places them onto the boom conveyor,” explains Weston.
The consensus is that the growth of e-commerce and omni-channel retail is providing a huge appetite for large scale automation projects and the most advanced robotics. But even relatively small businesses will be interested in the efficiencies that could be made by addressing certain, specific aspects of their operation. And from the simplest conveyors to the fanciest robots, automation equipment is being developed for more parts of the warehouse than ever before.
Automation allows consolidated DC for Co-op Denmark
Co-op is Denmark’s largest retailer, a co-operative with an annual turnover of DKK 50 billion, 38,000 employees and 1,200 stores. When the global recession gripped the region, Co-op Denmark decided to consolidate slow moving dry food goods from a number of warehouses into a 45,000 square metre facility in Odense. A goods-to-man automated picking system was required to break-bulk for slow moving products and then assemble store orders in totes for despatch.
“As these four local warehouses were 100,000 square metres in total we had to find a way to squeeze it all in to one facility and that could only be achieved through automation,” says Christian Flindt, Co-op Denmark’s technical manager at the Odense DC.
“The Dematic system only occupies 6,500 sq m of the warehouse, but it takes 70 per cent of the volume of the goods. So we didn’t need a lot of forklift trucks.”
Flindt stipulated a fast, reliable and scalable system, and the goods-to-man picking technology has increased productivity from 140 to 450 items picked per hour. It has also improved on-shelf availability in the retail stores by preparing ‘store ready’ orders in totes, for each category and packed in sequence. This allows faster shelf replenishment at the retail outlet – saving shop staff half an hour per pallet of totes.
MultiShuttle technology is linked to RapidPick IT. The system was designed for small-sized slow to medium movers that were inefficient to pick in a conventional way but that fit easily into a tote. In total there are some 45,000 storage locations in the MultiShuttle, offering the capability to hold around 9,000 SKUs, giving Co-op Denmark the capacity to fulfil 62,000 order lines per day for between 300-400 shops.
Automated aviation parts
Zenith Aviation turned to an automated inventory storage and retrieval system to run more efficiently and to enable growth of its complex business. The firm provides spare parts to regional airlines and aviation business in the USA as well as consignment parts services from its base in Fredericksburg, Virginia.
Using 23 horizontal carousels and six Shuttle Vertical Lift Modules from Kardex Remstar, Zenith Aviation says it has increased productivity and throughput, maximised floor space and improved pick accuracy to 99.9 per cent.
Zenith’s traditional racking and a mezzanine shelving system had been at near-capacity, before it invested in 11 horizontal carousels and two Shuttle VLMs to manage its spare parts inventory. Relocating these parts from 12,000 sq ft of shelving to just 4,688 sq ft released over 60 per cent of the firm’s floor space.
“These machines fit perfectly into our smart growth business model,” says president Robert Stanford. Soon after the first automation implementation Zenith added 12 more horizontal carousels and four more Shuttle VLMs to their facility. The warehouse now covers 50,000 sq ft with a parts storage capacity of over 750,000 line items.
When an order is processed by the accounts department, Power Pick Global prints a pick ticket which directs the worker to the relevant zone. The worker scans the bar code of the pick ticket and the machines retrieve the parts. A pick to light bar indicates the exact location of the part and quantity to pick. The next pick is indicated via the pick to light system, and when complete the worker returns to the shipping area to pack and ship the order.
Stanford says “We invested in and built this system for anticipated future growth and doing so has opened doors to new opportunities for manufacturer distributors and client consignment deals which have accelerated our growth.”
Zenith’s core business model has been to purchase parts from aircraft operators that are either upsizing, downsizing, or going out of business. “It is important that our system is able to handle a large influx of new parts,” said Stanford. Since the implementation, on-site inventory has grown from 20,000 line items and 3 million individual pieces to over 41,000 SKUs – more than 5 million individual pieces.
The added capacity has allowed the firm to grow its consignment business whereby it stores, advertises, sells, invoices, packs, ships, and collects payment for parts on behalf of other aviation operators. Managing consigned parts owned by multiple operators within one warehouse is a challenge but using Power Pick Global inventory management software parts are logged separately on the books, even when they are mixed within the storage unit to improve storage density. Real time reporting allows
Zenith to view and monitor each operator’s inventory individually.
Without a brick and mortar expansion, Zenith is able to deliver more parts in a shorter amount of time, meeting customer demand quicker. “With the added capacity available in the system, now there is no deal that’s ‘too big’ for us,” says Stanford.