An ever-changing face of retail has uprooted the look of the warehouse. But during this period of warehouse change, the need for counter-balance trucks has seen little movement. Levels, overall, have remained flat. Technical services manager at Briggs Equipment says that although levels of warehouse equipment have seen a marked increase in recent months, there has been little shift in counterbalance truck numbers.
There have been the occasional large orders. Palletised freight network Palletforce recently reached an agreement with Toyota for up to 100 new forklifts to be used at its hubs in Burton-upon-Trent. The pan-European distribution network said that it will take delivery of a fleet of f Toyota Tonero 8FGF25 gas-powered counter balance forklifts.
The Tonero 8FGF25 has a load capacity of 2,500kg, a four-metre duplex mast and enhanced safety and durability features. Each of the forklift trucks is fitted with TWIS (Toyota Wireless Information System), which records real-time information from the truck. The information can then be accessed through the web and features a simple dashboard to enable Palletforce to see the fleet performance.
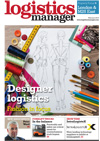
Dave Rylance, Toyota’s product manager for counter balance, says that the firm has also received an increased number of enquiries around electric solutions, but importantly he has witnessed a desire to remove truck traffic from the warehouse floor.
“About 12 months ago, we saw a rise in the number of people seeking a towing solution,” he says. “This desire has gained momentum, as safety has risen up the list.”
And increasing safety is a primary concern across the business world. The warehouse presents one of the more volatile environments for workers and there is a constant need to improve safety, particularly when it comes to large, moving equipment such as counterbalance trucks.
Manufacturers have, and indeed are trying various ways of improving safety within the warehouse. One system that has gained particular traction is RFID for monitoring individuals on the warehouse floor.
Rylance says that Toyota has been looking to develop its Spot Me warning system, and as such the firm has been spending time with third parties as it seeks to develop this RFID warning system for individuals on the ground. However, such systems present their own difficulties to be overcome. Notably, the way to handle ad-hoc visitors, and the potential expense, especially if areas of counter balance operation are open to members of the public, an aspect picked up on by Clifton.
“If such systems require those on the floor to be wearing bracelets, or similar garments, then they are useless – or at minimum costly – to warehouses with public access,” he says. “But the basic premise has something to offer, but there needs to be further development.”
This aspect of triggering systems is something recognised by Rylance, who says that this along with customer management of the system once put in place presents a big hurdle to be overcome if RFID systems are to be implemented.
Clifton says that Briggs has been focusing, working and experimenting on systems that, like RFID, detect obstacles and alert the driver – though this of course does not eliminate the potential for human error.
Linde has introduced a similar system, its auto-reverse speed reduction system. Alison Tucker, Linde’s counter balance product manager, says that the system produces audible and visual warnings for operators and pedestrians when a person or object is detected by the reverse sensors. At an agreed point, the speed reduction through the transmission is activated which then slows the truck down from 5kph to 1kph.
“This dramatically reduces the risk of collisions and serious injury to pedestrians when reversing,” says Tucker.
Visual warnings have become a popular safety system in counter balance trucks, according to Rylance, who notes a particular popularity among manufacturers for blue light warning systems.
Alongside its auto-reverse speed reduction system, Linde has implemented a number of new safety features across its forklift range. Others include the Linde Safety Pilot; Driver Assistant/Curve Assist; Linde Hydrostatic Drive; and its Auto-reverse speed reduction system.
According to Tucker, the Linde Safety Pilot will indicate when the truck approaches its maximum parameters with information on the load centre of gravity; the load weight currently placed on the fork arms, the current lift height, the tilt angle of the fork arms and the maximum lift height up to which the load may be raised. To help operators quickly identify all of these values, the display features a clear graphical design keeping numbers to a minimum.
Innovations in safety
The Linde Driver Assistant is an electronic system reducing traction speed automatically depending on steering angle resulting in perfectly safe cornering manoeuvres every time. Uniquely this can be fitted as standard to both engine and electric counterbalance trucks as well as reach, pallet trucks and order pickers in the Linde range. Truck speed can also be controlled electronically to match customer site speed limits. While the hydrostatic drive provides customers a transmission fitted with not only safer and more effective braking but also forward and reverse manoeuvring and pinpoint accuracy. This means that a Linde truck is parked on a gradient with the engine running the roll back will be limited to creep speed as opposed to the truck “running away” with gravity as conventional trucks will. While if the truck is parked on a gradient and the engine is switched off, the truck will move approximately one metre before the oil immersed multi disc brakes in the transmission are applied and the truck becomes stationary.
Marketing manager at Jungheinrich, Craig Johnson, says that Jungheinrich has been looking into various devices that can alter the speed of vehicles, as well as flashing-beacon warning systems, which come into effect once the trucks reach a certain speed designated by the user.
“There is also our corner braking curve control system,” says Johnson. “In addition to this we have improved the vision window on our trucks by 85 per cent, something that comes as standard on our counter balance trucks.”
Clifton says that visibility is also an area that Briggs is considering when it comes to counter balance. Alongside this, he notes that a lot of work has been carried out on sound levels and the amount of effort required to drive a truck.
“A forklift driver working in a distribution centre is driving, daily, the equivalent of Birmingham to Glasgow,” he says.
General manager of JCB International, Nicola Bagworth, says that the JCB Teletruk offers huge safety advantages.
“These advantages come from the truck’s forwards reach, which means that single side loading is possible,” she says. “Fork rotation also means that forks can be tipped back to secure difficult loads and without a mast we have 100 per cent forwards visibility.”
JCB has also implemented its Adaptive Load Control (ALC), which Bagworth describes as an operator aid that automatically limits the capacity of the machine in lifting or reaching applications.
Case study
More power
Power sources present their own volatility, and research into electric ranges have to take into consideration the safety of the battery used. Experimentation on lithium batteries began over 100 years ago in 1912, but it wasn’t until the 1970s that the first non-rechargeable lithium battery was developed.
Attempts to produce a rechargeable lithium battery were halted, due to the instability of lithium, especially during the recharging stage. Then, in the early 1990s, Sony introduced a lithium-ion rechargeable battery.
Opinions differ on whether lithium-ion offers the most complete way forward for electric forklifts. And JCB is yet to offer an electric range.
Jungheinrich believes so much in the technology that it has its own production facility for lithium-ion batteries in Hamburg (Germany), in addition, Johnson says it is the only major manufacturer to have an entire series of lithium-ion battery powered truck.
“Lithium-ion’s speed of charge is a key benefit, twinned with the overall life expectancy of the batteries, which is twice that of an acid battery,” says Johnson. “There are of course developments in fuel cell technology, but at present these still present a very real safety problem.”
However, there are side effects of that swift charge, and lifetime. Notably the energy drain recharging the batteries causes. Clifton says that those using lithium-ion batteries really need three batteries per truck: “One for use, one on charge, and one cooling”.
Rylance says that at Toyota the view is that lithium-ion batteries are a wonderful concept, but flawed for counter balance trucks: “The power draw for multiple charges would be so high that it could shut a plant down,” he says. As such, lithium-ion is not a priority for the firm, which is instead focusing its battery development on fuel cell technology.
“We’ve been involved with fuel cell research and development for between 10 and 15 years,” says Rylance. “And this is the route we are going down and will continue to pursue.”
Clifton believes that lithium-ion batteries are hindered by charge time, and that getting this down to one hour will prevent the power drainage recharging has on a company’s overall power supply.
“Charging these batteries is fine for a smaller operation,” he says. “But amps per hour used in the recharging process is huge, and if you run a large operation with multiple trucks running on lithium-ion batteries and you need to charge them all, the power drain will be substantial.”
“Hydrogen fuel cells, however, don’t suffer from this,” he continues. “The recharge time is just a matter of minutes.”
Briggs, in conjunction with Honda, has a project underway to develop “the first, true, long term hydrogen fuel cell”, according to Clifton.
Tucker believes that lithium-ion certainly presents the greatest potential in the short term, particularly for smaller warehouse trucks. For counterbalance trucks though, Linde has begun trials with alternative fuels.
“In 2013 Linde Material Handling, BMW and the Institute for Materials Handling, Material Flow and Logistics at the Technical University of Munich received funding from the German Federal Ministry of Transport and Digital Infrastructure in support of the field testing of fuel cell industrial trucks at BMW plant Leipzig,” she says. “The grant was used to develop a fleet of hydrogen-powered forklift trucks and tow tractors for logistics trains testing the eco-friendly and efficient hydrogen drive system in industrial trucks under realistic production conditions.”
The Linde E25 HL and Linde E35 HL trucks used in Leipzig—with load capacities of 2.5 and 3.5 tonnes respectively—feature a newly developed 80-volt fuel-cell system.
Mark Hanke, head of the industrial truck design department at Linde Materials Handling says that since the beginning of the project, Linde has made gradual truck optimisations with regard to the forklift trucks.
“This has included, for example, updates to the internal software of the fuel cells. Information on the daily use of the trucks by BMW in Leipzig is extremely valuable to us, and supplements our own test runs at our test site,” says Hanke.
Robert Micheli, scientific associate of Professor Willibald A. Günthner at the Institute for Materials Handling, Material Flow and Logistics at the Technical University of Munich. Explains: “We continually analysed a variety of aspects, including individual event messages and service reports. In doing so—and in conjunction with maintenance costs—we were able to determine the technical availability of the truck. Together with the evaluation of the handling steps over time during hydrogen refuelling, the ‘operational availability’ of the industrial truck emerged.”
“With the experience gained from the project, we at the Institute for Materials Handling, Material Flow and Logistics—together with our project partners—have also developed guidelines for use of the hydrogen-powered industrial trucks to help future users when it comes to acquisition and operation, including the required infrastructure and licences,” says Micheli.