New energy saving technologies and innovations could pave the way to more environmentally friendly operations. Alexandra Leonards reports.
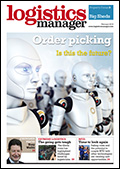
The importance of energy efficiency is being recognised on a universal scale. Last December, UN governments and businesses met in Paris, where they were urged to take notice of climate change, and the dangers that lie ahead. And it is not just governments who are now being forced to take notice. The global materials handling sector is responsible for a huge amount of energy consumption – and plans to reduce this are driving developments and innovations in the forklift sector.
“Emissions – and reducing them – is increasingly a priority for companies across most industries,” says James Clark, secretary general of the British Industrial Truck Association. “That is being supported by forklift manufacturers who are producing a new generation of diesel and electric trucks with minimal, or zero emissions.”
Customers are also striving to improve their own environmental impact – whether that be to save money, time or the planet.
“Customers’ demands drives development,” says Tony Wallis, commercial director, Toyota Material Handling UK. “They are continually looking at ways to be safer, more productive and more energy efficient in their operation, and therefore all developments have to address these key issues.”
Clark says that the performance of electric trucks has improved dramatically – and so, industries that would have traditionally only considered diesel trucks, now look at electric forklifts as a viable option and alternative.
According to BITA, its members predict that the trend of electrical trucks replacing diesel will endure, and a survey found that ten per cent of members asked think a significant substitution will occur.
“The energy that powers the nation’s forklift trucks is itself about to get lifted and shifted as new and emerging technologies challenge convention,” says Matthew Allen, solutions manager, Counterbalance Product at Yale Europe Materials Handling.
“Millions of tonnes of goods are moved around warehouses, stock yards, factories and transport terminals using forklift trucks.
“The industry therefore has a responsibility to find clean energy options that meet economic and environmental needs, as well as those of operators searching for improved operational performance and economy, to help reduce emissions and maximise energy efficiency.”
According to Yale, electric or battery operated trucks have a 60 per cent share of the market. But internal combustion engine-powered forklifts are still preferred for outdoor jobs and larger loads.
The problem with using electricity as a power source is that larger trucks can’t really use it. The energy needed for bigger forklifts is just too great in most cases. And batteries that can cope are often too large and expensive for the average material-handling situation.
Yale say that for larger trucks, the best way to boost energy efficiency is to have either a modern high efficiency LPG or diesel machine with low emissions.
So which solution is the most energy efficient? It is a special type of electric truck that Allen sees as the overall winner when it comes to energy efficiency.
Hydrogen-fuelled forklifts use fuel cell technology. The cell receives both hydrogen and oxygen, which pass through a proton exchange membrane, and electricity is produced to power the forklift.
There are many benefits to hydrogen-fuelled forklifts including: water and heat being the only by-products, a quick refuelling time of three to ten minutes and the ability to operate non-stop for eight or more hours between refuelling.
“Although still in its infancy and with an immature supply infrastructure, hydrogen fuel cells make a compelling case where on-site hydrogen storage can be accommodated or where regular supply can be achieved,” says Allen. “So an increasing share of the FLT population may soon be powered by zero-emission hydrogen fuel cell systems.”
Up until now, there has been limited use of hydrogen fuel celled vehicles, but Allen expects its usage will grow steadily.
One issue with hydrogen cell fuelled vehicles is that they are expensive – Toyota has a car powered by hydrogen on the market for £38,000. It is also difficult to produce the hydrogen without generating emissions – it’s only really environmentally friendly if it’s created from renewable sources rather than fossil fuels like coal.
Hydrogen fuelled trucks that use hydrogen generated from solar power, via an electrolyser, are one of the cleanest options. Honda has already begun to generate commercial volumes of ‘truly green hydrogen’ to power converted Yale trucks at its Swindon plant. These trucks produce zero emissions at the point of use.
Yale predicts that lithium ion-battery technology will emerge as the next generation battery.
These batteries have lots of advantages, including rapid charging, and long battery life cycles – with some lasting five to 15 times longer than other batteries. But it also has environmental pros. It is 15 – 20 per cent more efficient than lead-acid batteries.
As it stands these batteries are expensive. Existing set up costs are considerably high:
“The payback today limits use to specialist applications such as the food industry, where the cleanliness of a sealed solid-state battery brings unique benefits,” says Allen.
But there are signs that costs are being driven down as volumes grow and infrastructure advances.
“There is also the potential for this technology to replace diesel engines and avoid an ever tightening legislative determination to bear down on NOx and particulate emissions, plus the potential price and supply volatility of hydrocarbon fuels,” says Allen.
Iron-phosphate batteries is another technology that incorporates energy saving solutions.
“In the highly competitive manufacturing and logistics market in Europe, the benefits of lowering operating costs represent a clear advantage in terms of reduced sales prices or in terms of increased profitability,” says Javier Contijoch, forklift director BYD Europe. “Switching to electric forklifts using BYD Iron Phosphate technology is a major development that meets this demand.”
According to BYD, its Iron-Phosphate batteries consume about 40 per cent less electricity during charging and discharging in comparison to a standard lead-acid one. It also says that the “highly efficient charging” results in limited loss of energy
– and therefore lower energy bills. The company describes the batteries as “100 per cent environmentally friendly” because they do not contain heavy metals or acids.
But it’s not just electric or hydrogen powered trucks that are making moves in efficiency. IC and battery engines are also constantly being updated to ensure that they are as efficient and environmentally friendly as possible.
According to Yale’s Matthew Allen, these engines will “continue to provide a tough workhorse for the materials handling industry.” New generation engines guarantee low fuel consumption and vibration levels, as well as reduced exhaust and noise pollution, he says.
“Although fleet managers are sufficiently satisfied with today’s FLT engines and the range of energy options available – as they provide the choice, versatility and capability that current forklift operations demand – it is clear that, as the value and economic payback of new technologies becomes more advantageous, new generation technologies will continue to emerge and will start to acquire greater market penetration,” says Allen. “This can only be good news for the industry, and the environment.”
It’s easy to identify the problem, and the preferred outcome, but there are lots of elements to consider when tackling high energy consumption or emissions – and the solutions are multifaceted.
When producing an energy efficient machine, forklift suppliers must take into consideration the fact that expensive solutions will not be popular, and neither will those that are difficult to operate.
“Companies look at a number of features when acquiring trucks, not only so they look at the product features and the impact they will have on the safety, productivity and efficiency of their operation, but they will also look the different finance options: purchase or rental and the service support they will receive,” says Toyota’s Tony Wallis. “Buyers look at the total cost of ownership and they choose partners who help them to understand and manage these costs.“
Yale’s Matthew Allen describes the ideal forklift as one with low, stable fuel prices with maximum fuel efficiency – identifying renewables as the “likely answer”.
“Interestingly, there are a number of off-grid solar and other renewable charging sources being used, but the initial investment required can often show disappointing pay-back periods,” said Allen. “Even so, most people believe that a mix of energies is a good thing.”
The issue is not that there are not pioneering technologies and solutions being created – but that the balance between all the elements is difficult to achieve.
“Even when fuel costs and efficiency issues have been addressed there is a still more to consider,” says Allen. “No operator is going to accept unreasonable inconvenience or inefficiencies created by power units that fail to deliver the level of duty, performance and refuelling times that conform to operational productivity patterns.”
Whether battery, diesel or hydrogen is used, really depends on the company and project at hand. Space constraints, fuel availability, duty cycle and operating hours all impact on the decision.
Rental: No longer a stop gap
Short-term rental is becoming increasingly popular in the industry.
It is traditional for companies to use additional rented forklifts to pick up work during peak times. But rented forklifts are becoming a permanent fixture for many. This is because what many materials handling companies want is flexibility.
“The short-term hire of lift trucks – once a largely unplanned and ‘stop gap’ measure for organisations with a need to cover seasonal peaks – is now a vital part of many leading companies’ business models,” says John Maguire, commercial director of Narrow Aisle. “The flexibility and cost efficient pricing structures offered by short-term rental has seen strong growth in demand for uncontracted rental trucks as part of many users’ core fleet throughout the year – not just at traditionally busy times such as during the run up to Christmas and Easter.”
Many companies want the ability to trim down a fleet to sustain optimum fixed costs, all of the time, says Maguire. “They are therefore looking for new contracts with short-term rental input,” he adds.
Toyota’s Tony Wallis agrees: “Short-term rental is important as it supports companies at peak times but also if they need more flexibility. Many customers are operating with short-term contracts from their clients so it is important we can find solutions to help them to be flexible and competitive.”
Maguire says that uncontracted rental appeals to companies for a number of reasons, but operational and budgetary flexibility are potentially the biggest drivers. “Finance directors often find short-term contracts useful as the trucks do not always need to appear in the user company’s balance sheet,” he says.
Case study: The energy efficient electric forklift
Yale reckons it is now producing Europe’s most energy efficient electric forklift series – a status that has been backed by energy consumption figures based on the standard VDI 2198 60-cycle test.
Replacing the hydraulic service brake system with E-breaking on its three-wheel ERP15 20VT trucks has secured the series’ position as market leader in energy efficiency.
The new system is self-calibrating and doesn’t need any maintenance. The brake pedal position is monitored by a sensor whose voltage output will determine how much braking torque is provided by the motors. The parking brake system is independent of the E-braking and still includes the original Yale Stop – which automatically puts the parking brake on when a forklift is stationary and traction has not been requested.
Another feature is the E-steering function. Its four-wheel ERP16 20VF has been updated with E-braking – bringing the 1.6 tonne, medium wheelbase model to an energy consumption figure of 4.4 kWh/h.
“With their energy efficiency and best-in-class manoeuvrability, these trucks have always helped customers increase throughput and reduce cost per pallet moved,” says Karen Calver, Yale product manager for electric counterbalance. “Now economy is even better and, with the three-wheel truck, officially unbeatable.”
Costs: Minimising the total cost of ownership
The total cost of ownership is potentially one of the most significant considerations for a business when purchasing a forklift. And so, forklift suppliers must aim to meet the customer’s need – on a number of levels.
“An important factor driving developments is the total cost of ownership of the trucks,” says Rory Harvey-Kelly, general manager of Baoli Material Handling Europe. “This means that buyers are also considering the cost of maintenance and service. Accessibility of the components becomes more and more important, because time is money. When developing Baoli forklifts, easy accessibility of components is a key factor.”
BYD’s Javier Conijoch says that buyers are simply looking for lower cost of operation.
“That is,” he says, “to minimise the sum of the acquisition cost of the truck plus the operating costs – electricity consumption and with lead acid batteries costs related to distilled water, battery amortisation and labour time required to maintain and swap batteries.”
Toyota’s Tony Wallis identifies the operators as the biggest cost. “If you look at the total cost of ownership the highest costs are the operators so the maximum efficiency, productivity and safety of the trucks is critical,” he says. “The training and operator efficiency is often overlooked and operator training is not just about complying with the legislation, it is also one of the best ways to help operators work productively, safely and reduce the amount of damage they cause.”
He says that operators shouldn’t just know how to operate a truck, but that they should also be familiar with specific truck features, and the environment they operate in.
Competition: Innovation spurs market growth
Innovation and technology are motivated by competition, as well as the drive for energy efficiency.
“There is mounting evidence that competition-induced innovation may become an important driver of market growth,” says BITA’s James Clark. “Our members are re-examining existing products to provide new offerings to customers.”
He says that a broader counterbalance product range, with lower prices will likely encourage orders because customers will then “find it easier to justify purchases”. He adds: “Competition-inspired innovation should spur market growth and efficiency improvements which will provide incentives for firms to upgrade their fleets. The warehouse market may also witness innovation from competition in counterbalance as engineers realise the advantages of new designs.”