It’s worth putting some thought into the floor of your warehouse – not only is it critical to safe operation, but it can also have a decisive impact on the efficiency of operations.
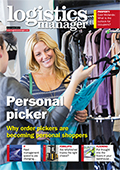
It’s easy to overlook the floor of the warehouse, but the technical challenges can be significant. It has to be strong enough to take the weight of racking, goods and materials handling equipment, and it has to be flat enough to allow safe and accurate movement.
And those challenges become even more significant when automated equipment is deployed.
Kevin Potter, managing director of Flowcrete UK, says: “The floor must maintain a flat, level and functional surface despite the movement of heavy loads, trafficking from hard rubber and steel-wheeled forklift vehicles and potential exposure to deteriorating factors such as chemical spillages, intense cleaning routines and dropped objects. Getting the floor flatness right is a critical requirement, as surface unevenness can lead to excessive vibration on a lift truck. Exact floor flatness is crucial to ensure that lift trucks can operate at maximum speed.
“The slip resistance of the floor is key to minimising on-site accidents. Aggregates can be broadcast into resin floor coatings to enhance the floor’s anti-slip profile. The aggregate can be customised to match specific requirements, for example entrances may need a higher degree of slip resistance because rain water might be walked in from outside,” says Potter.
“Clever use of walkways and signage can help warehouse facilities comply with regulations and make the most use of the available space. Bright and obvious signage on the floor is ideal for creating clearly identifiable walkways and boundaries. Clever use of floor signage can also help to maximise the available floor space by marking out the best positions for entry, exit or storage,” says Potter.
“Many of these flooring properties were exemplified recently at a Heathrow Airport warehouse, which was refurbished so that it would be suitable for large-scale pharmaceutical storage and distribution activity. Over 11,000 sq m of specialist resin flooring solutions was used to optimise the floor, with different parts of the facility requiring tailored solutions to meet particular challenges,” says Potter.
“Prior to applying the finish in the main area of the facility, the substrate had to be carefully prepared. Approximately 10,000 sq m was shot blasted and protruding steel fibres were ground down. Two coats of the epoxy-based primer Peran STC was used to prepare the substrate for a final 2mm coating of the self-smoothing epoxy resin system Flowshield SL. The chemical resistant epoxy Flowcoat SF41 was used to create a forklift path as well as pedestrian logos, numbers and multiple line markings.
“Achieving a smooth finish was essential to ensure that the forklift trucks could move quickly and efficiently around the site,” says Potter.
CoGri recently highlighted some of the challenges of modern logistics operations when it hosted a seminar in Jakarta, Indonesia discussing
“Concrete Floors – Failure by Design”. It focused on e-commerce and the drive for higher density and automated warehouses; the impact a high quality floor can have on the cost of pallet movements in a warehouse; and the impact a bad floor with cracking, damaged joints, delamination or a dusty surface can have on reducing profitability by causing disruption and driving up maintenance costs.
Face Consultants, part of the CoGri Group, has just completed a project at facility operated by Iron Mountain, the data storage specialist, at Silivri in Turkey.
Chris Linley, design manager at Face, says: “The results of the inspections and surveying confirmed that the topping slab had curled and debonded, leaving the finished surface of 6,130 sq m not fit for purpose.”
Face proposed a fully restrained, mechanically bonded topping slab. With a minimum depth of 100mm, the topping slab was reinforced with 1No A193 mesh placed at mid-depth. The bond was provided by way of 12mm Ø bars, resin anchored into the existing base slab at typically 1000mm centres. Further restraint was provided by ensuring that the anchor bars overlapped the mesh reinforcement.
One of the main considerations with the floor design on this project was carefully managing the expectations of the client. A bonded topping slab can only be considered as fully restrained and restraint against shrinkage is a leading cause of cracking in slabs.
“It was vitally important that as the end-user, Iron Mountain were made fully aware and accepted the risk of cracking being observed in the slab. We gave reassurances that any cracking that might occur would be minor and aesthetic only, with the width of any cracks being controlled by the reinforcement placed at mid-depth of the slab”, says Linley.
Uretek, specialises in foundation and infrastructure soil problems and used a geo-polymer technology to provide floor and foundation re-levelling, ground stabilisation and strengthening as well as void filling and water sealing.
It recently completed work to stabilise the floor at a major warehouse in Enfield. The work was required to stabilise the ground and lift the existing floor back up to a safe operating level. This needed to be done so that the site could safely house racking and associated distribution systems.
Quick route to more space
One of the quickest and most cost-effective ways to increase warehouse space is to install a mezzanine floor.
Dan Soulsby, Egger’s category manager for building products, says: “As businesses grow they will often look to relocate premises to expand their operations. This can be very costly and time consuming, not to mention the upheaval involved in moving a business to a new location. Often a more economical and efficient answer can be to consider installing a mezzanine floor in the existing premises. This can allow businesses to make the most out of their current premises with the potential of doubling the area for a one off cost as oppose to either moving entirely or increasing rental costs”.
And Laura Eskrett of Hi-Level Mezzanine Floors points out that an obvious advantage of a mezzanine floor is that it gives the flexibility for warehouse managers to expand their current space without the need to move to new premises, no matter what industry.
“Each of our floors are unique and custom built depending on their purpose. They provide an ideal solution for businesses needing to expand their storage and stock space, they can even be used customer facing as a showroom floor within retail outlets. Alternatively, in the automation and manufacturing industries, our structural steel mezzanine are capable of withstanding extremely heavy loads, making them ideal for holding conveyor systems and machinery,” says Eskrett.
And she points out that mezzanine floors are helping retailers adapt to the demand of the growing e-commerce sector.
“With many physical retailers transitioning to selling their products online and the growing popularity of retailers that exclusively sell goods online, warehouses need to be able to respond quickly to demand. Mezzanine floors make the best use of vertical space within a warehouse that would otherwise go unused, the floor space can then be used for a variety of different functions such as picking, packing and delivery,” says Eskrett.
Egger specialises in the design and manufacture of structural flooring boards for use in both residential and commercial build projects throughout the UK and Northern Ireland. Soulsby says: “We’re always pushing the boundaries with our products to offer customers innovation and excellent quality solutions for their projects.
“Egger OSB HDX is ideal for this application as it provides the strength and stiffness required for a mezzanine floor, plus a whole host of additional benefits to the installer.”
Epoxy coatings in focus
Epoxy resin floor coatings have become a popular choice for warehouses thanks to the ability of these solutions to provide a robust, level platform that can withstand the on-site challenges for an extended period of time while providing additional operational benefits.
Kevin Potter, managing director of Flowcrete UK, says: “Epoxies are available in a wide range of colours and can be tailored to ensure surface flatness as well as resist heavy loads, hard rubber and steel-wheeled forklift traffic. The seamless nature of epoxy floor coatings makes it easy clean and the warehouse operator can further enhance the warehouse’s cleanability by incorporating stainless steel drainage into the finish,” says Potter.
“Facilities that need to protect the floor against very challenging conditions, such as thermal shock, hot oils, highly corrosive chemicals and heavy physical impacts should consider polyurethane flooring materials. Polyurethane floors are generally thicker and more robust, however as they typically have to be trowelled down so it can be difficult to achieve the smoothness of a poured in-situ epoxy finish,” says Potter.
“Polyurethane floors can include an antibacterial additive to help safeguard food & beverage produce. This property was required at LF Logistics in
Malaysia, which provides distribution centre management services to nearly 400 brands worldwide. The ultra-hygienic polyurethane coating Flowfresh HF, which includes the bactericidal agent Polygiene, was chosen to refurbish its warehouse floor, as it would meet the strict cleanability criteria required,” says Potter.
“Resin systems that have been made using methyl methacrylate (MMA) technology can rapidly speed up the floor’s curing time to only a few hours. These systems are ideal for sites that can’t afford a long shut-down period… but need a seamless, hard wearing and colourful surface,” says Potter.
Yorkshire tea gets a lift
Bettys & Taylors, which produces Yorkshire Tea, acquired an additional building adjacent to its main Plumpton Park site to act as a flexible multi function facility, to enable it to expand further.
To maximise utilisation of the upper level storage space within the 10,000 sq ft building, Bettys & Taylors chose a mezzanine lift from Transdek.
Transdek’s mezzanine floor lifts are designed to carry up to one tonne uniformly distributed load, which makes them ideally suited to the lifting of medium to light weight, or bulky, products. An ultra slim lift deck enables the lift platform to lower flush with the floor at ground level, allowing easy access for pallets and trolleys for quick loading.
The lift for Bettys & Taylors includes new design features including a new ram box design, software updates and improved operator controls as standard on every machine.
“The new Transdek mezzanine lift was quickly fitted, is very robust and really easy to operate. It is perfect for our requirements,” said Homi Tehrani, project technician – site development at Bettys & Taylors. “From the sales department to the installation team everyone has provided an excellent professional service. It was also great to deal with another innovative Yorkshire company that has the same high values.”