More confidence in the manufacturing sector is being reflected in a boost for sales of counterbalance trucks, says Alex Whiteman.
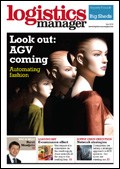
The market for counterbalance trucks rose 6.1 per cent last year, figures from the British Industrial Truck Association reveal. The Forklift Truck Market Outlook prepared for BITA by Oxford Economics highlights the fact that BITA members are optimistic about prospects for the forklift truck market with 83 per cent expecting orders to rise modestly this year – and 17 per cent expecting order to rise significantly.
James Clark, secretary general of BITA, says: “Counterbalance orders and shipments are expected to begin picking up in the second half of 2015 as the improving economy drives new orders and confidence expands in manufacturing, which is key to counterbalance orders.”
The outlook showed that the rise in counterbalance shipments was not only matched but also bettered by warehouse trucks with growth recorded at 11.5 per cent. Clark says this reflects the respective levels of confidence in the different sectors that buy trucks.
“Rising disposable incomes is fuelling consumer spending and the continued growth of e-commerce and the distribution industry in the UK is driving demand for warehouse trucks to satisfy the delivery of these goods,” says Clark.
Matthew Allen, engineering manager at NACCO Materials Handling, parent of Hyster and Yale, recognises the healthy market, noting that sales have been greater than predicted.
“In some markets, there is more demand in warehouse trucks and electric counterbalance trucks,” he says.
These sectorial peaks are partly the result of how warehouses are changing, and Allen, by no means alone in this, notes a growing desire for automation in counterbalance vehicles.
Hyster isn’t likely to be selling automated counterbalance trucks anytime soon, says Allen. But he does believe that there is an increasing desire for electronically controlled machines across the industry.
Egemin Automation recently installed an automated warehouse system at Kim’s Chocolates for the internal transport, automated storage, and order picking of chocolate products. Egemin’s system includes three automated warehouses for the storage of semi-finished products, packaging materials and finished products. Three automated guided vehicles transport goods between warehouses and production.
The three AGVs at Kim’s Chocolates, in addition to the handling of packaging materials, also transport semi-finished pallets between production and the warehouse, where the AGVs temporarily store the pallets up to three levels high.
When looking at automated counterbalance trucks, Michaël Coryn of Egemin says that the biggest advantage of counterbalanced trucks is they can transport any kind of open or closed pallet/carrier and are also able to pick/drop in any rack or position because there are no wheels under the forks.
“For the exchange conveyors this sometimes simplifies the construction because the top of roll can be very low,” he says. “On the other hand, it is not an absolute requirement for the automatic warehouse as narrow or even straddle vehicles are also capable of picking or dropping on most locations.”
While Hyster may not be venturing into these grounds, Allen does note growing requests from customers for specialised systems.
“Counterbalance trucks really are the jack of all trades,” he says. “But we have found that it is imperative that counterbalance vehicles are as ready as they can be for those that want to adapt it.”
To do this, Hyster standardises the control systems of its vehicles, fitting them all with Canbus controls.
Canbus routes all communications over a set (or several sets) of common wires, which connect all devices and controllers on the vehicle. These devices send and receive signals over this common set of wires, announcing what the signal consists of before the data or instruction. If further devices (for example those from automation systems) need to read or send signals to the vehicle and its components and controllers, this is straightforward when designed, integrated and tested properly.
“These additional controllers can link into the Canbus anywhere, and interface with the vehicle much more easily and reliably than with a vehicle wired and controlled with conventional switching and wiring,” says Allen.
With sales growing, manufacturers need to take greater stock of emissions, and look toward meeting European emissions targets. And, as Allen says, customers want their machines to meet standards without losing efficiency and without costing more than the one they’ve just disposed of.
Paul Watson of Doosan describes the latest emissions regulations as one of the most significant developments in the industry for many years – posing a challenge for all manufacturers.
“At Doosan, our R&D capability meant we were uniquely placed to respond to the challenge,” says Watson. “The millions we invested in developing our G2 engine range have resulted in a superior proposition for our customers. The engines comply with Euro-Stage IIIB (over 37kW) and Euro-Stage IV (over 55kW) without compromising on power or needing a diesel particulate filter (DPF). Their improved fuel efficiency means they are not only cleaner, but improve customers’ productivity too.”
Watson believes that DPF technology is both out-dated and doesn’t work very well on forklifts, noting that those trucks fitted with a DPF build up soot over time resulting in a need for replacement.
“The alarming regularity of this leads to increased downtime when the truck cannot be used, impacting productivity and is unacceptable in many modern operating environments,” he says.
According to Watson, Doosan’s DPF-free trucks not only nullify this, they also have better fuel consumption.
Mitsubishi fits its GRENDiA ES LP gas trucks with a three-way catalytic converter – as standard – which cuts carbon monoxide, hydrocarbons and, crucially, 95 per cent of harmful NOx gases.
Alongside this, Mitsubishi has been developing its EDiA trucks, a new breed of all-weather electrics. Stewart Gosling of RDD, UK importers for Mitsubishi Forklift Trucks says that as well as eliminating emissions, dust, heat and noise issues, and reducing operator fatigue, it also reduces your carbon footprint and real-life costs, too.
STRATEGY: TCM plans expansion in the UK
TCM, the dealer-driven forklift brand within the UniCarrier group, has set out ambitious plans to expand in the UK. The UK is currently seeing a uplift in demand for forklifts, and Graham Jones, TCM dealer development director said: “We have a strong dealer network, which we continue to support and build upon to extend coverage across the UK. We’ll be working to give them more opportunities with the backing of a global organisation and access to greater value, such as the aftermarket, technical support, warranty, parts, factory training and marketing.
“We have a proven formula for growth, based on flexibility – the dealers will have all the tools they need to provide excellent service and first class products.”
TCM sales and support will be channelled entirely through the dealer network. It will offer a full range of products from diesel, electric and LPG counter-balanced trucks to reach trucks, stackers and VNAs.
TCM (Toyo Carrier Manufacturing) was established in 1949 and produced Japan’s first forklift in the same year. The UniCarriers Group was formed in 2011 from the mergers of Nissan Forklift, TCM and Atlet, with integration of TCM completed in 2013.
Nobuo Yoh, CEO and president of UniCarriers Europe, said: “Because of its high recognition and the great confidence of customers in TCM equipment, we have now decided to revive the name in Europe as a dealer brand.”
TCM offers a full range of forklifts. To differentiate them from the white-grey UniCarriers models, the equipment will be sold in a yellow finish and via indirect sales channel.
According to UniCarriers, the firm principally wants to use TCM to reach customers who need durable forklifts for industrial applications.
TECHNOLOGY: Flexi celebrates 25th anniversary
Flexi Narrow Aisle is celebrating the 25th anniversary of the development of its original Flexi articulated truck concept.
150 visitors attended an open day, which provided a live demonstration of the latest articulated vehicles including the Flexi VNA and the new Flexi CuBEMAX.
Peter Wooldridge, founder and managing director of Narrow Aisle, said: “Until the Flexi Front Wheel Drive articulated forklift truck was developed by Narrow Aisle, companies had little alternative but to operate a two truck system with a counterbalanced forklift working outside and feeding a reach truck inside the store or warehouse.”
Flexi says that more than 5,000 units have been sold worldwide.
SAFETY: Safety is a by-word
Reducing emissions can help improve the health of forklift operators. However, this is not the only aspect in safety terms that manufacturers are targeting. Egemin’s Michaël Coryn says his firm is continuously investigating the market to evaluate new and improved technology.
“We want to make our vehicles smarter and safer in a ‘non-contact’ way,” he says. “This means the vehicles stop before even touching somebody.”
Paul Watson of Doosan, says that safety is the key driver in Doosan’s forklift design and its Operator Sensing System (OSS) makes a “major contribution to safety”.
“If the operator is not in the seat, the truck will not move,” he says. “Lift and lower functions are disabled and the tilt function is locked. Additionally a warning light illuminates if the seat belt isn’t fastened, and an alarm will sound if the operator leaves the seat without applying the parking brake.”
The forthcoming Doosan 7-series electric counter balance range, features an automatic electronic parking brake system is installed as standard, meaning as soon as the truck is stationary, the electro-magnetic brakes are applied automatically – this also gives an unlimited ramp hold function.
At Hyster, there has been an emphasis on seatbelt use. Matthew Allen, engineering manager at NACCO Materials Handling Group, and his team have been working with the firm’s customers to develop existing seatbelts.
“It’s a simple but real addition, that we have come up with,” he says. Its “intelligent seatbelt” stops the truck if not worn, or worn incorrectly – whether the driver is sat on it or if he has buckled it behind his back.
Stewart Gosling of RDD agrees that safety is about more than protecting drivers. It’s about looking after those on foot, as well as preventing costly damage to vehicles, stock and racking – delivering a direct benefit to your bottom line.
“Safety is a by-word for Mitsubishi,” says Gosling. So much so that it counts itself as innovator of the world’s first driver protection system IPS2 “before it was ever compulsory” he adds.
“Trucks are fitted with an enhanced IPS2 system – as standard – which locks driving and hydraulics down when the driver isn’t seated,” he says. “You can even password-protect your trucks – preventing unauthorised use.”
With visibility is a key factor many accidents involving forklifts, both Mitsubishi and Doosan claim to offer improved visibility. The Mitsubishi GRENDiA promises 38 per cent more visibility than some trucks, with fork tips and loads in full views. Doosan’s Zeus cabin is designed to provide greater rigidity, according to Watson, as well as “outstanding” visibility and a clear easy-to-read dashboard.
Hyster also provides a tracking system that allows supervisors to monitor speed and impacts. This not only monitors the safety of the vehicles but also provides a means through which some aspects productivity can be monitored.
TECHNOLOGY: Two new series from Crown
Crown has launched two new series of trucks: the C5 series of LPG powered lift trucks, and the SC 6000 series of three and four wheel electric trucks.
The C5 series is available with lifting capacities of up to three tonnes, and can work in rough terrain and all weather. A gear-driven valve train eliminates the need for frequent belt replacements or chain adjustments, a the power brake enclosure prevents the build-up of dirt and debris. It has a four-piston braking system with hill hold function fitted as standard.
The truck has Crown-built 2.4 litre engine and a rugged powertrain with a lifespan of up to 20,000 operating hours. A fully enclosed cab is available for all-weather working.
Crown’s on-demand cooling system is available as a option. This combines precise ventilation with radiator clearing for reliable cooling. “This means that with each engine start, the fan automatically reverses to clear debris from the radiator,” says Crown’s Martin Hainge.
The SC 6000 Series of electric trucks includes three-wheel and four-wheel models, with capacities ranging from 1.3 to 2.0 tonnes and lift heights of up to 7.5 metres. The truck has been designed to give operators unobstructed views in all directions – even when fitted with one of the available cab options.
The steer axles feature massive steel/cast-iron construction and heavy-duty tapered roller bearings which enable the truck to withstand jolts as it travels over rough surfaces and dock boards. Nested I-beam masts minimise longitudinal, lateral and torsional flexibility. And there is an intelligent on-board control system to ensure that the SC 6000 maintains constant speed on ramps and automatically adjusts operation of control functions in correspondence to different load weights, lift heights, steering angles and travel speeds.
MOTIVE POWER: The Li-ion, the H and the lift truck
Emissions legislation means that forklift truck manufacturers are looking at alternative sources of power such as fuel cells.
Egemin is using fuel cells at one of its US facilities. However, says Egemin’s Michaël Coryn, the basic installation to provide refilling of these fuel cells is also not so easy to install it in a safe way.
Hyster has been in the process of developing machines with fuel cells, and Matthew Allen expects these to be offered to customers within the next year.
“20-30 trucks powered by fuel cells would be a good option for warehouse operators,” says Matthew Allen.
Doosan’s Paul Watson says that lithium ion is allowing Doosan’s customers to negate the need for additional batteries and battery changing equipment and also allows the firm to increase and maximise the life of the battery and piece of equipment it is fitted in. “Lithium Ion batteries also helps our customers where their battery maintenance regime has given serious cause for concern,” he says. “Maintenance free, no topping-up needed means no corrosion from over-topping or running dry from neglect, both of which are seen all too often in numerous warehouses, he says.
“They offer many additional benefits to customers, but are not needed or suited to all applications and customers need to take a longer term view of increased safety, increased productivity and reduced maintenance to be able to weigh up whether the return on investment can be justified.”