Innovation has never been more important in the trailer market with pressure to maximise capacity, reduce fuel consumption and meet environmental requirements. Malory Davies reports.
Trailer design is evolving rapidly to accommodate the demands for more capacity and lower costs – as well as the pressure to reduce carbon footprints.
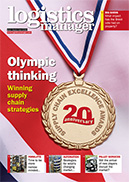
A government-backed experiment with 15.65m trailers is now well underway. Earlier this year Jack Richards added two more of the longer units to its fleet saying that the additional capacity in three 15.65m units meant it could take one equivalent trailer off the road.
There has also been growing interest in double deck trailers, and this year has seen trials starting with kinetic energy recovery systems.
Lionel Curtis, technical director of Cartwright, highlights strong demand for double deck trailers. “We have been very busy with double deck trailers of all types, fixed deck, moving deck, curtainsiders, refrigerated units and so on. Demand for them is much stronger than last year – of course, that is linked to the carbon footprint.”
Burning a litre of diesel fuel produces 2.68 kg of carbon dioxide. Curtis points out that a single deck trailer carrying 26 pallets can be expected to give a fuel consumption figure of ten miles per gallon. By comparison, a double deck trailer carrying 52 pallets will give a figure of nine miles per gallon, so the carbon footprint per pallet is almost half. “It really is as simple as that,” he says.
Derek Skinner, technical director of Schmitz Cargobull, agrees that the advantage of using all of the internal space by supporting one load above another cannot be in question. “It’s just how that is done.”
He points out that running a high step-frame double deck trailer requires careful route and logistics planning, with warehouse investment to load/unload to see the benefits. “This can only serve the long haul business which is not the growth area for transport. Smaller urban deliveries are the future, and for this a vehicle that can navigate low bridges and fit the urban road network is what’s required. A double deck trailer where the height can be adjusted to suit the load and be more universal is the smart solution.”
Of course, there is an additional purchase cost to a double decker. Curtis says a moving deck trailer will be almost twice the price of a single decker, but a fixed deck unit will be significantly less than double the price.
The issue of carbon footprints will become even more significant next year with European Union plans to make bodywork display a “green” rating.
The exact form of this legislation is still under discussion. Cartwright has been working to ensure that it is based on grams of CO2 per pallet kilometre. The alternative, basing it on a rating for a trailer with no reference to the volume of goods, would be very bad for double deck units – and could actually put an end to them. “It would be complete madness,” says Curtis. He points out that Cartwright has developed a refrigerated three temperature double decker with a sloping front that can carry 44 pallets.
Transdek has been developing the wedge concept on a fixed double deck trailer, which managing director Mark Adams can offer six-to-seven tonnes more carrying capacity than a powered deck trailer. The step-frame design of a conventional double decker limits the load space at the front of the trailer. Not only that, it means that it is difficult, if not impossible, to get the maximum weight over the fifth wheel. This in turn can lead to axle overloads when the trailer is running at maximum weight, and it might even be necessary to put ballast over the fifth wheel.
The Transdek Wedge design uses a low profile chassis design, and works with a tractor unit that has a fifth wheel height of 1070mm – lower than the standard UK height of 1250mm.
Adams points out that an organisation operating 100 conventional step-frame trailers could replace them with just 80 Wedges, a big saving not only in trailers, but also tractor units and drivers.
The core of Transdek’s business is double deck lifts, and it signed a deal with Cartwright earlier this year for the manufacture of its trailer designs. It has also appointed Graham Usher to the new role of sales director for trailers to drive forward expansion of its fixed double deck trailer operations. He was previously sales and marketing director of Buffaload Logistics.
Schmitz Cargobull has made load security a priority and has introduced a curtainsider that meets the EN 12642 XL standard for load control and goods protection. Skinner also highlights the development of TrailerConnect – a telematics package which provides location information, operating information for improved efficiency and lower total cost of ownership.
When it comes to trailers for urban deliveries, noise is a key issue along with emissions. Road congestion is an ever growing problem for deliveries, and one way of easing the situation would be to make deliveries at night. If there is to be any chance of that being achieved, then ensuring that vehicles operate quietly will be critical.
Derek Skinner says: “Reducing noise and weight is important too – which is why Schmitz Cargobull now produces the MF6 Multifunction Floor. It’s lighter and tougher than conventional flooring, and also meets the PIEK requirements for noise levels.”
He points out that generally across the industry there is better signalling, with FORS-compliant lighting and side-indicator repeater lights.
Curtis argues that delivery vehicles should be able to use bus lanes in the small hours of the morning – after all there are not a lot of buses around then. “But they would have to do it quietly,” he says.
Going with the flow
Cartwright’s Lionel Curtis points out that reducing fuel consumption and carbon footprints, has increased the focus on aerodynamics. A double deck trailer with a sloping front will give a ten per cent fuel advantage over the conventional brick shape, he says.
Curtis also sees trailer weight climbing the agenda as an issue, pointing out that new materials are becoming available that will enable manufacturers to the reduce the overall weight of trailers. He highlights panels and floors as key areas. The challenge is to find materials that have the right properties in terms of strength, durability and stiffness – and of course the cost of materials is always an issue.
Derek Skinner, technical director of Schmitz Cargobull, says: “Operators should look beyond aerodynamics as this is just one part of answering the much larger question, which is ‘What is the most effective way of improving the cost of ownership of trailers?’
Therefore, operators need to question both the initial cost and residual value of their trailers, and take into account any repair and maintenance costs, quality and up-time estimates, and the impact that their trailer’s weight and efficiency in use will have on fuel consumption -a combination of weight, overall height, aerodynamics and rolling resistance. Operators should take a holistic view to develop and evaluate a complete solution, which may not be as obvious as first thought.”
Formula One technology comes to freight transport
SDC showed a new trailer KERS system at the CV Show in April. Fuel savings of up to 25 per cent are promised from KERS (kinetic energy recovery system), which was pioneered in Formula One motor sport. It uses regenerative braking to charge a bank of “ultra-capacitors” that can then power an electrically driven axle.
The SDC system has been fitted to a 13.6m trailer for Eddie Stobart, and uses two controls – one on the tractor unit and one on the trailer. This effectively turns the whole tractor trailer unit into a hybrid electric vehicle. As well as the reduction in fuel consumption and associated emissions, SDC says the KERS trailer can cut NOx and reduce brake wear.
Fowler Welch has introduced a trailer using kinetic energy from the axles to power the fridge unit. It charges in-built batteries at as little as 5-7 mph allowing up to 90 minutes of stationary power before the hybrid motor kicks in.
Paul Allera, head of fleet, says: “The new trailer enables us to manage deliveries in areas with noise restrictions by negating the use of the unit’s diesel engine to power the trailer and decreases the volume of fuel needed, helping us to reduce CO2 emissions and operating costs.”
Derek Skinner, pictured, says: “KERS have shown great advantages in specific fields such as and urban bus environments. Clearly any operation needs to have significant periods of acceleration and braking to use and generate power. Otherwise the extra weight of such a system reduces payload and if it doesn’t contribute to power (through lack of “charging” potential), it increases fuel usage. There are other ‘quick wins’ currently available – such as simply specifying a lighter trailer – as for general logistics, systems such as KERS need further justification.”
Lionel Curtis also sees a role for KERS, particularly to power a fridge unit. “That is a really neat way of using the energy,” he says. There is also the possibility of powering a lifting deck and other electrical gear.