Choosing the right WMS is a complex task, the system has to be appropriate for the particular operation, and then there are decisions to be made on whether to go down the SaaS route. Lisa Townshend considers the options.
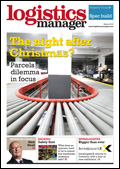
One of the most critical purchases for any warehouse operator is a warehouse management system. Whether it is new, an upgrade to an older system or a bolt on to make a legacy system function better, it seems that the warehousing world is waking up to the need for better data management in many of its operating functions.
But there is now another factor to consider. More and more companies are trusting their data and processes to the cloud – the mystical world which in essence means hosting systems at a data centre, and having someone else look after the server infrastructure, while you get on with running your business.
Craig Sears-Black, managing director at Manhattan Associates, says: “Over the past five years we have seen the migration from on-premise hosting to hosting by a third party provider with Amazon AWS, Microsoft Azure and Google vying with the traditional hosting vendors such as CenturyLink and Rackspace. And moving forward the selection of infrastructure, support and hosting provision will continue to change and evolve. However, the migration to a pure software as a service (SaaS) model is taking longer in the WMS world than in other solution segments due to the complex and varied IT environments encountered within a warehouse.”
Vikram Singla, product innovation and supply chain apps leader at Oracle UK, agrees with the concept of complexity in the warehouse: “Thirty years ago the WMS operated pretty much standalone, running on large, on-premise technology that relied on overnight batch cycles of data to drive the day’s operations, and with hard-coded functionality that gave little flexibility.
“The WMS of today is a different beast. It needs to be able to meet the demands of omni-channel fulfilment, the use of automation, voice recognition and virtualisation, the explosion of data through the arrival of RFID and the internet of things, and the need for real-time connectivity. It has to be deployable – and removable – on demand, to be able to meet the seasonal demands of a flexible supply chain.
“In addition the WMS still has to maintain its laser-focus on the customer – fulfilling orders accurately and consistently to ensure customers get the ultimate experience. Orders that are on time, complete, damage-free and with right documentation and ancillaries. Oh, and at a price that is economic.”
From a supplier perspective, WMS is going through change. Consolidation, use, function and features… vendors are having to look at their offering to keep up with customer needs. Gavin Clark, commercial director at Snapfulfil SaaS WMS provider Synergy Logistics says: “One thing we have seen is that a lot of the specialist vendors are being gobbled up by finance houses or finance vendors; so there is a huge amount of consolidation. This is reducing the options for buyers because people who want to go out and buy a best of breed WMS are finding it harder. This is also limiting the innovation side of things; we are spending a lot on research and development ourselves but from an external point of view we are seeing less best of breed vendors and more all-encompassing supply chain suite.
“Legacy platforms are also becoming obsolete. Some of these systems were written in the nineties and early noughties and the platforms they were built on are now no longer supported so companies are being left with an unsupported system.”
For Eric Carter, solutions architect at Indigo Software, it’s integration, not consolidation, that is a key trend. “We are seeing significant demand from customers to integrate their existing WMS with other tools to improve process efficiency. For example, customers are asking us to help them integrate weighing scales, conveyors, parcel carriers etc, with the objective of joining together the picking, packing and dispatch processes into a single, seamless transaction. The end goal is to minimise the necessity to build quality checks into the process at each stage, thereby saving time and resource costs. Instead, with an integrated and automated process, a single individual can be responsible – and accountable – for picking, packing and dispatching, driven by the WMS,” he says.
But legacy systems require changes to remain functional, warns Tom Kozenski, vice-president solution strategy at JDA. “Many warehouses are still running on older, legacy WMS that have been developed and deployed nearly a decade ago. This is because the functional requirements for WMS have not changed much until now and that upgrades have historically been expensive. However, the current approach to warehousing will require dramatic changes to support the fulfilment of smaller orders, compliance with government and industry regulations, and the need for more intimate integration between critical business applications. Fortunately, cloud technology is making this transition from old to new easier by allowing warehouses to better use technology and computing capacity to meet these challenges, he says.
For Clark it is this ease of use in transition that is helping the cloud to gain traction. “The recent Gartner Magic Quadrant report suggested that cloud options should now form the part of all major purchasing decisions. Not only is it more accepted in the WMS market but also everybody seems to be talking about cloud of some description. When we launched in 2007 most of the WMS vendors were busy pooh-poohing it and saying it couldn’t be done – it wouldn’t be fast enough or reliable enough. Yet those same vendors are now releasing and promoting cloud systems. So there is definitely a high level of acceptance.”
Singla is seeing a real future for cloud solutions in supply chain. “One of the major contributors to the emergence of flexible business operations is the cloud. Talked about for several years, the cloud is already dominant in other business areas such as human capital management, customer experience and financials.
“While supply chain may have come relatively late to the party, with the possible exception of transport management and procurement, a recent IDC survey found that 80 per cent of organisations are already using or considering supply chain solutions in the cloud. The supply chain cloud market is expected to grow at 19 per cent CAGR and reach $4.4bn by 2020, so get ready, because the cloud is coming,” he says.
Carter sees cloud options as well suited to a certain size of company. “Web based systems have their place and are popular among start ups and SMEs that do not want to invest in an IT infrastructure and are seeking a low cost entry point for a small number of users.
“When your warehouse operations and sales order processes are in the infancy stage, a cloud based system is very appealing, there is no outright purchase cost and no need for internal IT expertise. But as the company matures, cloud systems can be restrictive if the user wants to make changes and that performance is often outside of their control and dictated by the hosting infrastructure available.”
David Bugden, marketing manager at Proteus Software, believes flexibility is the key. “The benefit of the hosted solution is the ability to expand – forget all the other infrastructure capability, security and backup. It makes it easier if companies need to add additional capacity or even temporary warehouses – the ability to make those available is more flexible and a shorter timescale from conception to implementation.
For Clark, the IT requirements present the most obvious benefit. “A lot of companies will have either low IT resource or they will have a high IT resource but a lot of things to do with it. In our experience WMS comes at the bottom of the to do list when it comes to IT. Therefore we design systems that don’t need a huge amount of IT. This makes it fast to implement, easy to deploy and simple to support.
“In addition there is disaster recovery built in – if something goes wrong and you have an on-premise system you are into data recovery and all sorts of things. With a web-based system you plug a new warehouse into the same system put the same numbers on the racking and you are up and running. We have actually had examples where a serious fire or flood problems have been averted through the use of a web based system,” he says.
For all of the benefits, it has taken a long time for cloud based WMS to become a viable option for warehouses, and it is not all about the cost. Issues such as bandwidth, trust in the security, and a willingness to have faith in another company to keep your data, have all been factors in the barriers to implementation.
Bugden thinks the market is coming full circle with regards to a third party model. “It’s interesting how the market has gone. In the early days customers never bought fax machines and copiers – they were rented. Mainframe computers were predominantly provided on a service/bureau basis. So we are going full circle. But in between, many businesses have become proprietary about the box in the corner that holds their data – they feel protective of it and rightly so. Nowadays I think there is a more confident trend not only to have processes such as payroll but often your HR data hosted somewhere provided on a subscription model.”
On a more operational level, Clark looks at the issue of bandwidth. “Our primary concern when we go out and visit people is if they are in remote areas. If there is nothing but fields and farmland and somebody has popped a warehouse in the middle of this my first question will be ‘what is your internet connection like?’. We have written our systems to be very data minimised, but if somebody has 30-40 people operating in a 100,000 sq ft warehouse and they’ve not got a good or reliable internet connection then that can be a problem, says Clark.
One thing that comes with a flexible system is the ease with which you can collaborate and integrate with partners. Singla shares the view that the ability to share data easily with partners in the supply chain is vital for successful business. “Standards-based integration, especially through web services, is fundamental to enable this upgrade process in cloud environments. The fulfilment network relies on a multitude of partners – multiple order channels, 3PLs, suppliers, distributors, stores and shared warehouses; therefore a cloud-based system becomes an advantage.
“As companies grow through new markets or products, or change partners to provide simplicity in the customer experience, cloud-based systems provide collaboration advantages as mobility is built-in from the start.”
One of the criticisms levelled at WMS is that its complexity does not allow for companies to make full use of the systems. Clark says: “I read a report recently that 20 per cent of people who take a WMS haven’t got one already but the rest have looked at it because they have had problems with obsolescence with the legacy system not delivering the functionality they need.
“What we’ve found is if you deployed a WMS say in 2002; you made decisions about your business in 2002, your industry in 2002, how your customers were buying from you in 2002. They haven’t revisited those decisions that were relevant back then but now are out-dated. To address this they bring the vendor in whose first question is ‘are you on our latest version?’. Not many people take upgrades because of the cost. So you have ‘version lock’ as our American colleagues call it. We get a lot of enquiries from people who have a system they don’t want to upgrade or is cost prohibitive to do an upgrade to revisit those decisions.”
Alex Mills, sales and marketing director at Chess Logistics Technology, calls for companies to use the cloud to their advantage: “There may be many benefits of migrating existing applications to the cloud but we have seen that the costs to the end user organisation remain broadly in-line with the conventional systems that they already use. To be truly transformational and disruptive, cloud systems also have to be accessible to smaller and growing businesses who until now have not been able to find or justify the investment needed for the type of system used by established companies. We see potential in the market for a scalable solution that offers excellent functionality but without the upfront and on-going maintenance costs of existing solutions,” he says.
Bugden believes it is in the partnership between vendor and customer that warehouses get the most from their WMS. “Systems like ours are not cheap – there is a significant investment for the client and therefore it’s unlikely that they would embrace a system like ours without feeling that there was a probability of getting a cost return within an 18-month to two-year period.”
Case study: Sleeping easier at Comfy Quilts
In 2015, Comfy Quilts opened a 110,000 sq ft facility to allow its principal stockholdings of finished goods and raw materials to be consolidated into two sites in Middleton, Manchester. The sites operate on a 24/5 basis and employ 86 people across three shifts.
To support a more efficient and stable warehousing operation, the company chose Snapfulfil to implement a WMS. Snapfulfil now manages both of Comfy Quilts’ main DCs, each in excess of 100,000 sq ft, as a single operation with two locations, providing a single view of inventory of both raw materials and finished goods.
Comfy Quilts took possession of the new warehouse on 21st October 2015 and went live with Snapfulfil across both warehouses simultaneously on 28th October. With on-site support, the switch was completed in three days, with the final orders being shipped from the old system on Thursday evening and the first orders shipped out of Snapfulfil on Monday morning.
From contract signature to going live, the system implementation was completed in 15 weeks.
Warehouse manager Mark Farrell says: “Over the past two years, we have been manually emulating everything a WMS does –we were the WMS. As well as being time consuming and labour intensive, we have been at the mercy of human error and, as the business has grown, so has the margin for error.
“Implementing Snapfulfil has radically improved both accuracy and operational efficiency which allows us to offer an excellent service to all of our customers – internal and external – as standard.”