Managing large scale transport operations has become more challenging as supply chains have become more extended and more complex. More and more organisations are turning to the control tower concept.
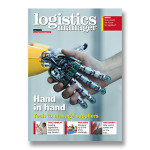
The past few years has seen a significant increase in the demand for control towers to manage transport operations.
It’s the visibility that a control tower can provide that is the most obvious benefit. When allocating business to different transport providers, the control tower allows the operator to see any problems more quickly as well as reducing administration costs.
Companies like Flex have recognised that as supply chains become more complex, the use of control towers becomes ever more important. The control tower can not only offer improved visibility of the operations but it can also provide analytical tools allowing the operator to respond quickly to developments in the market.
Kuehne + Nagel has put control towers at the heart of its strategy for contract logistics. In its 2016 annual report, it said: “The company has specialised in end-to-end supply chain management projects, which are managed via the global network of Logistics Control Towers and performed in cooperation with other Kuehne + Nagel business units. In addition to the continuous strong demand for innovative, integrated services in the traditional markets, growing interest in integrated solutions was also recorded in emerging markets with new projects initiated in 2015.”
Last year, British American Tobacco chose Kuehne + Nagel to operate a control tower for its air and sea movements. K+N developed its Global Marine and Air Logistics Service Centre (GMALSC) integrating all air and sea freight flows into a single control tower. Using an integrated approach provides full visibility of product moves at all stages for BAT. In addition, standardised global processes are combined with local knowledge through K+N’s air and sea network to enhance efficiency.
Unilever implemented its own control tower to manage transport operations across Europe in 2008. Unilever has more than 60 factories and 100 distribution centres across Europe. Establishment of the Ultralogistik facility at Katowice in Poland, marked a moved from locally managed transport to one European transport model.
As well as delivering cost savings it has enabled the measurement and reduction of CO2 emissions in the company’s transport operations, by enabling CO2-friendly transport mode decisions to be made, increasing load-fill and reducing miles travelled.
Since then, it calculates that the use of the control tower concept has enabled it to reduce transport costs by some eight per cent, improve load-fill by about three per cent, reduce vehicle km by 1.7 per cent, and reduce CO2 emissions by nine per cent.
The success of the original scheme spurred Unilever to roll out the concept globally in 2010.
XPO Logistics provides 4PL control tower solutions across Europe under the name ‘KeyPLs.’
Jean-Marc Lami, managing director of XPO’s KeyPL business unit, reckons that control tower not only provide operational control, they also have a strategic role fulfilled by control towers.
“Our KeyPLs offer benefits that go well beyond the operational function, allowing us to bring a fresh perspective to transport operations. We work collaboratively with our customers to optimise flows and determine the right transport plan to meet their needs for continuous efficiency, economic performance, time savings and transparency. We also provide customers with a single point of contact for planning, selecting and managing the most relevant carriers for each route, as well as cost management and performance management. Advanced control towers ensure tight quality control and made-to-measure reporting, allowing a customer to outsource its transport flows to a reliable supplier while focusing on core business activities.”
IT is instrumental in developing an effective control tower solution. “Technology has become essential in managing the complete transport process, from shipment allocation to delivery tracking,” says Lami.
“Our KeyPL software suite can be used as a forecasting tool due to its data archiving capabilities. We use it to achieve continuous improvement of customer operations in areas such as load optimisation, cost control, billing review process and performance monitoring. It is essential that IT solutions meet customer-specific requirements, so that they can provide customers with tailored solutions that are both flexible and scalable to address their evolving needs.”
Setting up a control tower starts with an analysis of the customer’s needs and flows in detail. “Our engineering team will identify all potential synergies and design a tailor-made solution with the most relevant carriers,” says Lami.
“We also work with each customer to understand the activities, constraints, seasonality, regulatory environment and operational framework. Another important factor is the ability to implement the tower quickly and smoothly, with a proven methodology that is respectful of daily operations. However, implementation is not the end of the story. As a customer’s needs evolve, so do our solutions; this combination of disciplined control and fluid change management enables us to form long-term strategic collaborations with customers.
“We encourage goals that are beyond the clear service improvements and efficiency gains that result from implementing the control tower solution. A strong planning process leads to increased efficiency, economic performance, time-savings and transparency, and these can be quantified as KPIs,” says Lami.
Logistics provider Damco recently launched Supply Chain Orchestrator – a control tower solution designed for companies to improve overall supply chain visibility, performance and optimisation. The Orchestrator provides a single coordination point, integrating, validating and distributing data across supply chain partners. The Damco system integrates fourth party logistics provision with predictive and analytical techniques allowing teams to detect and respond to events before they affect performance.
The programme is based on a three-step approach. The idea is that users start by gaining end-to-end visibility, move through enhancing day-to-day supplier performance, to finally optimising the complete supply chain across all providers.
Neil Wheeldon, responsible for Damco’s global product development, says: “We call it Supply Chain Orchestrator because organisations can orchestrate all the separate supply chain actions in real time from one platform, much like a conductor controls the flow and tempo of an orchestra to create perfect harmony.
“Companies can realise significant savings in supply chain and inventory costs, improve service levels and engage suppliers in a more collaborative way. In a recent implementation Damco was able to reduce supply chain costs for a large multinational by approximately 15 per cent while improving overall supply chain reliability.”
The Orchestrator uses a dashboard to provide the transparency needed to manage end-to-end supply chain regardless of provider. Shipment related KPIs and other performance metrics are available, with automated exception alerts highlighting issues that could impact the business.
Expanding the pharma control tower network
Healthcare is one area where the use of control towers has become increasingly common.
Last year, Yusen Logistics opened its pharma gateway at Schiphol. And UPS has been expanding its healthcare-specific capabilities to support clinical trials which make use of a healthcare control tower system.
Yusen’s operation links its Antwerp import/export consolidation centre and European central warehouse with its Schiphol air operations, to form a multi-modal hub. This is managed from a control tower, manned by a UK-based international team linked to Yusen’s offices around the world.
The 1,200 sq m bonded GDP compliant warehouse provides ambient and cold storage, pest control, and separation of pharma and general cargo. The 125 cu m cold store has 45 pallet positions.
Speaking at the opening of the facility, Yusen’s president Hiromitsu Kuramoto said: “This opening represents the next step in the realization of our global healthcare strategy, with this strategic European operation at its very heart.”
UPS is expanding its healthcare control tower network as part of a global expansion of its healthcare-specific capabilities to support clinical trials.
As well as the control tower network, UPS has enhanced its shipping system for clinical investigator sites; package intercept and re-icing capabilities; and upgraded operations to move temperature-sensitive biological specimens in and out of more than 60 countries more efficiently.
“As innovation in the biopharma industry evolves — and with the emergence of personalised therapies and growing direct-to-patient trends — research and development activity will only increase around the world. Our cost-effective portfolio streamlines logistics for clinical trials into one global network across sometimes remote, hard-to-reach locations,” said Habib N’Konou, UPS senior operations director for clinical trials. “With drug research taking years at a cost in the billions, a product loss or damage, including falling out of temperature range, could mean a costly setback. Our recent improvements to our network will reduce product loss or damage.”