E-commerce is having an impact right across the retail supply chain – and especially at the loading bay. Alex Whiteman reports.
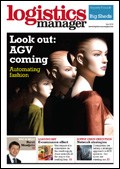
No longer just a box, warehouses are a stock pot constantly refilling a retailer’s various sales points – whether physical stores or via the online offering. As Thomas Langley, projects director at Hörmann, says: “the biggest change has been the rise of home shopping,” and more recently, click and collect.
With this sea change, retailers have been developing their loading bays and warehouses to suit changing paradigms. For Leon Butler of Transdek, a loading bay utopia would be one in which multiple vehicle types could be serviced from any bay, allowing a high level of flexibility in the planning and marshalling of loads and traffic.
And this utopia is slowly coming into being. Loading bays are more and more finding themselves host to a variety of different vehicles, from traditional to double-deck trailers, and then vans suited for high-street replenishment.
John Meale, managing director of Thorworld Industries, reckons that the biggest trend affecting the loading bay is the continued growth of double-deck trailers, providing greater efficiencies in cost and deliveries for distribution.
“Accordingly, loading bays are being adapted to cater for new trailer sizes; the challenge is to optimise warehouse design to enable them to service traditional vehicle types as well,” says Meale.
“With more bays devoted to double-decks, it may become necessary to have temporary or semi-permanent additions for the loading and unloading of single-deck trailers or vans.”
Over the past few years, in particular, Meale notes a growth in the creation of bespoke solutions incorporating platforms and ramps – and also in the purchase and hire of mobile yard ramps – as companies seek to protect themselves against bottlenecks.
“Innovations in trailer design will inevitably force changes to the optimisation of loading bays – yet the danger of too much specificity is that valuable loading bay space is required for each vehicle type,” says Meale.
“In such circumstances, there might be an argument in favour of a simple all-purpose loading solution – such as a platform and ramp combination – that is easily adaptable to all vehicle types.”
Butler says that for double deck trailers, instead of the conventional rear ‘barn’ door often used, which have to be opened prior to docking, Transdek has developed an new door type.
“Featuring twin slide doors, operating on the same principle as a sash window, only one door can be opened at a time, and the doors are only unlocked and opened once the vehicle is docked,” he says. “This eliminates the safety hazard to drivers having to walk in busy yards, minimises the risk of shrinkage from the unsealed back door and improves temperature retention for chilled or frozen deliveries.”
However, for this system to work, Transdek has added an additional transverse docking bar to the rear frame of its new double deck trailers, and in turn uses an automatic braking system to ensure trailers stop within the correct distance from lifts, which will reduce potential damage to vehicle and lift.
CHANNEL HOPPING: Speed and flexibility is critical
Speed and flexibility of product flows are critical for retail supply chains to service the complex multi-channel and omni-channel marketplace, says Leon Butler of Transdek.
“As a transition area between warehouse and goods vehicles, it is vitally important to keep equipment in the loading bay running efficiently and minimise downtime,” he says.
Thorworld’s John Meale, notes the substantial investment in integrated systems with the warehouse – aka intralogistics – to manage processes.
“However, that investment places considerable strain on the loading bay,” says Meale. “It is absolutely vital that the loading operation is up to date, otherwise there is the risk that goods will be ready for dispatch but without the mechanism to get them out of the building.”
As product flow in the loading bay increases, minimising downtime to ensure delivery deadlines are met is key to satisfying customer demands. For this to be achieved, it is critical that companies implement routine servicing schedules, says Butler.
“From the OEM’s perspective, the onus lies not only on ensuring highest standards of engineering quality and conformance with all relevant design and safety standards, but also providing operators with regular on-going training, as well as ensuring exceptional levels of after sales support,” he continues.
To guarantee that correct servicing procedures are carried out on its loading bay equipment, Butler says that Transdek insists upon all service engineers conduct comprehensive systems checks with detailed reports.
“It also means speeding up the loading and unloading process to optimise vehicle turnaround times. Most bays are pre-designed to allow optimal loading speeds for ‘standard’ single deck vehicles, ISO containers and rigid trucks. But adding the increasingly diverse range of double deck trailers into the mix complicates this neat pattern.”
CASE STUDY: Bespoke platform for Conquest Hospital
Focus of safety within the loading bay, led Booker & Best, which operates the rapid response contract for Conquest Hospital in Saint Leonards-on-sea, near Hastings, to implement a new bespoke loading bay platform supplied by Thorworld Industries.
“The Conquest Hospital is a busy, modern district general hospital, with a high incoming delivery rate,” says Andy Kershaw, Booker & Best’s contract supervisor. “The organisation is always looking for ways to progress safety standards and procedures, so was keen to improve its loading bay provision for efficiency and operative safety.”
Thorworld provided not only the loading platform itself, but also a dock plate, dock bumpers and alignment kerbs.
Meale says: “The selection of a bespoke Thorworld solution underlines our capability to create truly appropriate systems that not only look great on the design board, but really can perform in the loading bay, ticking all the boxes when it comes to both safety and function.
Meale also highlights the significance of eco-design and energy efficiency. He notes not only the commercial but also the environmental benefit to reducing energy costs, especially those involved in generating a consistent temperature for cold store applications.
The implications for improving efficient energy usage are a need for a more effective seal during the loading and unloading of vehicles – especially so in temperature controlled environments – a more effective seal reduces heat ingress.
“A variety of solutions are available; yet perhaps most interesting is the next generation of four-sided seals currently being developed by a number of manufacturers,” say Meale. “If anybody gets that right, it’ll be a real winner. It is a major topic of late among members of the Elevating Equipment Product Group.”
DOORS: Handling multiple vehicle types
Double-deck trailers may be gaining in popularity, but they are not the only vehicles entering the loading bay. The shift in vehicle type accessing the warehouse is leading operators to make choices: do they upgrade their existing sites, or relocate?
Projects director at Hörmann, Thomas Langley says that he is seeing warehouses change their door layout to not only suit the rise in double-deck trailer usage, but also to accommodate the number of vans entering the loading bay.
“Double-deck trailers are not the only vehicles that are spending more and more time at the loading bay,” he says. “So too are vans, and we are seeing loading bays, which for instance, will feature two standard doors and 20 van bays.”
However, how operators accommodate these vehicles and whether to shape up or ship out, Thorworld’s John Meale says this is size dependent. Companies can only expand if there is space to do so.
Leon Butler of Transdek says that in the face of intensifying market competition, there is definitely an appetite for organisations to make the most of existing resources, including warehouses and loading bays. If there is the opportunity to convert a loading bay with a warehouse extension, which offers extra loading capacity and eases pressure in another part of the supply chain, or provides enough breathing space to postpone a move to a new site, this can be a cost effective option in the short term.
“However, it is often only a stop-gap solution. As organisations grow and the nature of the market continues to evolve it is usually only a matter of time before more major changes are required,” he says. “What additional storage and loading bays can offer the supply chain is the flexibility of an intermediate step.”
Butler points out, though, that as soon as taller vehicles are included in the mix, then there has to be a certain amount of redesign in the loading bay.
“How much really depends on what types of vehicles are being used, and how many double deck trailers are being adopted at a particular site,” he says. “For some of our customers, who have moved specific parts of their operations to double decking, there is a justification for designing the warehouse around double deck loading requirements to maximise the overall benefits. But the vast majority of new warehouses are still designed to cater for single deckers.”
Meale says that even if there is additional capacity to expand at an existing site, the big question is whether to go permanent or temporary.
“For instance, some operations may experience seasonal peaks (notably Christmas), in which case it makes greater sense to augment regular loading capability with short-term solutions such as rented yard ramps.”
Langley notes that those who are opting to relocate, and those developing new sites, are future-proofing their new warehouses by putting in blanks instead of doors. This minimises initial costs, but leaves the option open for additional doors to be put in easily.
Butler also recognises this increasing desire to incorporate future proofing into their networks from the outset, such as factoring in extra capacity at a new warehouse to cover growth forecasts.
“For others, it means juggling loading bays around as the supply chain is restructured,” says Butler. For example when Boots, the UK’s leading pharmacy-led health and beauty retailer, converted to its current centralised NDC distribution model, it involved Transdek relocating large numbers of lifts from outlying DCs, as these were transformed to smaller CDCs.”
Further complication is added to the operation if European trailers need to be loaded/unloaded, as these are built at a lower height and have a bottom deck 270mm above ground level, says Butler.
“Companies need to factor in servicing of these vehicles where relevant,” he concludes.
CASE STUDY: TJ Morris expands to service growing store network
Discount chain TJ Morris (Home Bargains) has more than 370 stores nationwide and plans to expand that to more than 700 over the next few years.
The retailer therefore enlisted construction specialist Bowmer & Kirkland and industrial door and loading bay manufacturer Hörmann to develop its new £12m regional distribution centre in Liverpool last year.
The 200,000 sq ft unit is opposite TJ Morris’s existing high bay warehouse facility. The design features 21 loading bays, complete with dock levellers, shelters, bumpers, traffic lights and wheel guides.
With the potential to service up to 700 stores in the next few years, the new Liverpool warehouse and distribution centre’s loading bays needed to be able to withstand frequent, day-to-day use from a variety of vehicles, lift trucks and other materials handling equipment.
As TJ Morris’s fleet encompasses lorries with different loading heights, a solution with hydraulic dock levellers was the best choice, as lorry tail lifts can be moved underneath the dock levellers, which is also useful for the loading of heavy goods.
Hörmann’s HTL 2 telescopic lip dock leveller allows the retailer’s pallets to be situated at the end of the vehicle’s loading surface, thus providing a better use of loading space. The telescopic lip can be extended and retracted in a targeted manner via separate control buttons, and can be easily controlled on the loading surface.
Another way TJ Morris manages multiple vehicles is by using Hörmann’s longer dock shelters with inflatable heads. These adjust to a lorry’s size and create a seal around the trailer, irrespective of size, so they can be customised to most situations.
Top and side flaps are mounted on a galvanized, compressible steel frame, which results in a stable, flexible and robust construction. The scissor arm design ensures a higher degree of pre-tensioning, as the springs are pressed in parallel, which helps to increase the pressure of the cladding after the loading process. As well as providing increased insulation, these types of dock shelters minimise rainwater run-off in adverse weather conditions, helping to reduce any slip hazards.
TJ Morris has also opted for three specific dock shelters that use Hörmann’s DOBO system. The solution allows trucks to dock on a loading bay before opening the rear doors, meaning the goods remain fully protected inside the vehicle to lower energy costs, prevent theft and help maintain the correct temperature.
As loading takes place around the clock, Hörmann’s DT dock seals were incorporated, comprising a material that consists of 2mm thick polyester with a special woven inlay that is coated with UVPC on both sides.
The site also uses two Hörmann HS 7030 PU spiral doors, as they are characterised by their high thermal insulation, fast opening speed and safety light grilles.
McLaren Construction and Hörmann have also been working together on TJ Morris’s new 700,000 sq ft distribution centre in Amesbury, Wiltshire, to assist with the retailer’s expansion plans in the south. The £70m site in Solstice Park is a replica of the same sized facility that opened a decade ago at its original headquarters on the edge of Liverpool, and has 76 loading bays and 92 sectional doors.