How available warehouse space is used determines warehouse efficiency, and failing to ensure this can have a significant impact on profit margins. Maria Highland examines the challenges…
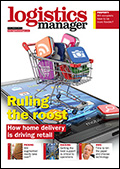
The warehouse was once considered to be the back end of business and now it has now shifted position. An efficient warehouse is now at the forefront of any successful logistics operation. It is no longer simply a place of storage and instead takes its place as an indispensable core component. A successful warehouse operation is governed by product availability and visibility.
Racking and shelving is responsible for warehouse storage density, visibility and the speed of retrieval processes. It can either increase or decrease the efficiency of your logistics operations. Managing director of BITO Storage Systems, Edward Hutchison, says that “racking and shelving plays a key role in maintaining the flow for highly accurate order picking and can generate cost savings by eliminating the need for outside storage, handling and transport which will reduce costs and improve productivity.” Correspondingly, behind every successful warehouse operation, stands an efficient racking and shelving system.
“Customers want racking that is adaptable,” says Hutchison. “This starts with the racking’s basic components: the uprights and beams. Bolted frame components will allow a fast exchange of damaged components. Uprights need to be available in a range of widths and different material thicknesses to allow an ideal upright geometry for frame heights of over 20 metres and bay loads as heavy as 40 tonnes. Flexibility comes with drop on components such as steel, mesh decks, steel or chipboard panels used either with or without support bars, in this way a shelf level can be created to store goods of any size and shape.”
Mike Alibone, business development & marketing manager at SSI Schaefer, says that companies should aim for racking and shelving that offers stability, adjustability and capacity. The loading (in terms of weight) must also be taken into consideration, as it will inevitably determine the design choice. How the racking and shelving affects the equipment specification and the floor on which the structure will be built is also important.
“There is a science behind choosing and installing both pallet racking and shelving which is fit for purpose and that ‘purpose’ may have a multitude of parameters associated with it,” says Alibone.
Before it can begin to address operational needs, successful racking and shelving must be fit for use. If racking and shelving is physically unsuitable for its proposed use, whether it cannot bear the weight, the loading, or withstand warehouse conditions, it can impair warehouse efficiency.
Hutchison says: “A customer should satisfy itself that the racking and shelving company offers the required quality and capabilities, that it can manage the type of project in hand and bring it in on time and on budget”. He suggests that customers “pay attention to the quality of the materials used in the racking and shelving and how they stand up to the rigours of everyday warehouse operations. For example, galvanising and epoxy coating ensures high corrosion resistance and guarantees a long service life for all components.”
Environment
Good quality racking and shelving systems can also improve warehouse safety- a common issue in the warehouse. Alibone says: “When operating in a racking/shelving-based environment safety is of paramount importance. All storage systems should be maintained to the highest standard in accordance with the manufacturer’s recommendations and legislative requirements. Such issues of safety can be overcome by ensuring the involvement of health and safety management throughout the whole design process- from conception through to realisation.
“This involvement in the early stages with the design team is crucial to ensure risks are designed out and that the solutions provided can be operated and maintained safely.” Racking and shelving that poses minimal risks and increases safety will also help to avoid any work place accidents, which can have costly repercussions both financially and in human terms. Floor anchoring, pallet support bars and column guards can improve the safety of the racking and shelving structure.
Investing in good quality racking shelving may tick all the boxes when it comes to safety, flexibility and suitability, but how can racking and shelving improve warehouse efficiency?
Hutchison says that most manufacturers and retailers look for “racking and shelving that will help them to ensure that when items leave their warehouses and distribution centres, they are in the best condition, they have been accurately picked, they are well packed and the customer gets exactly what he wants on the day he wants it. They want a storage system that meets their requirements precisely and is designed to gain maximum productivity.”
For example, SEC Storage has designed and implemented a tailor-made storage system for the International Logistics Group’s new warehouse, which accommodates five clients from the beauty and fashion sector. SEC storage needed to come up with a solution that would allow the replenishment of a variety of products ranges, such as lingerie, clothing and cosmetic products, alongside seamless picking and despatch. The “primary solution for the facility is a single tier rack supported picking structure that maximises cubic capacity in over fifty per cent of the warehouse. The system is designed around specific client package types, which could include anything from a BDCM1 box to a flat, lingerie box or footwear. By standardising the bay aperture between all the varying sizes, capacity is maximised within the system,” says Dean Kahl of SEC Storage.
Optimised
Productivity has been optimised in the warehouse as “the system has been designed by considering pick rates and travel distances. The compact installation means that the travel distance of each warehouse operative has been significantly reduced when compared to the same storage capacity being achieved over a single level, ” says Kahl. SEC Storage’s racking solution saves warehouse space as “the nature of the rack supported structure also means that packing stations have been incorporated into the system on the ground floor”, therefore the remaining “space can be converted to picking levels at a later date to boost capacity according to demand. Further packing stations have been installed on the first floor, allowing for simultaneous packing during peak periods,” says Kahl.
Storage density can also increase warehouse productivity. This is an important customer requirement when choosing suitable racking, as optimising space is key in any logistics operations and can ensure that your warehouse is working to its maximum capacity. “For manufacturers it’s about consolidating their raw materials or components on site as close to the assembly line as possible. This safeguards production – reducing stoppages due to product not being in the right place. It will also eliminate the duplication of stock, thus reducing stockholding. Saving on floor space is also critical in Omni-channel retail facilities. They require a large number of pick spaces for a broad range of SKUs and will be handling a mixture of slower and faster goods – often all in a single system,” says Hutchison.
Having racking and shelving with a higher storage density not only increases productivity and efficiency, but also saves energy running costs. SSI Schaefer provides high-density storage solutions such as Mobile Racking, which can minimise the building footprint by up to 45 per cent. “A significant reduction in energy loss (and utility bills) also ensues, due to the correspondingly-smaller roof structure reducing air escape. The other cost savings of a smaller, more efficient Mobile Racking warehouse include a 35 per cent lower overall investment in construction costs and a reduction of up to 49 per cent in utility costs,” says Alibone.
Alibone also recommends multi-tier shelving, which features low leg loads and “can be constructed more rapidly, needs less head room and typically results in a saving of 30 per cent over a mezzanine-based system offering the same storage capacity.” Alibone also says that the “flexibility in the multi-tier shelving design also enables it be tailored to meet floor slab capacities in existing buildings, while the lightweight shelves make it easy to rapidly adapt the storage location to changes in stock profile.”
Sometimes, increasing your warehouse efficiency requires adding a personal touch and going that extra mile. “Businesses expand and distribution operations grow, the problem of how to store more product in an extendable system, which also allows rapid access and the flexibility to accommodate an ever-changing stock profile, becomes more acute,” says Alibone. The future of racking and shelving thus turn to tailored solutions.
“The latest developments tend to evolve from customers requesting bespoke solutions”, says Hutchison. BITO have already begun to tailor their products to suit the needs of their client. “BITO was approached by a major online retailer that wanted a shelving product of a set width and a set depth that didn’t exist,” says Hutchison.
“The retailer also wanted dividers to be spaced so that they would suit a robotic picking system. We had to manufacture a bespoke design to suit its specific requirements. So everything on the shelving system is completely bespoke. The client was able to bring their own staff to test it and adjust it.”