Buying a forklift is half the task – the next step is ensuring that the right service and maintenance regime is in place.
I’ts big and strong – and at first sight it seems that a forklift truck doesn’t need too much looking after. But given the critical nature of what a truck does, the correct service and maintenance regime is essential. Not only that, proper maintenance is a legal requirement.
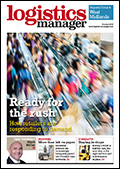
The Fork Lift Truck Association points out that pre-shift checks are a legal requirement. “A sound system of daily or pre-shift checks is the cornerstone of good maintenance. This ensures that essential fluids are kept topped up and potential defects are identified before they become a problem.”
It produces the FLTA Daily Checks booklet, which, as the name suggests, provides advice on regular maintenance.
All forklift trucks have a recommended service interval. The interval will be affected by environment in which a truck is used – cold stores, harsh chemicals, or simply a wet environment.
It’s important for operators to work with their service provider to create a schedule that is appropriate for the truck and the operation.
Trucks must also undergo Thorough Examination – the equivalent of an MoT – at least once a year. The Thorough Examination, which is managed by Consolidated Fork Truck Services, covers two sets of Health and Safety Regulations: the Lifting Operations and Lifting Equipment Regulations 1998 (LOLER 98), and the Provision and Use of Work Equipment Regulations 1998 (PUWER 98). The CFTS is a joint venture between the Fork Lift Truck Association and the British Industrial Truck Association.
Generally, the owner of the truck is responsible for ensuring the truck is safe – the same is true if the truck is on long term rental. But if the truck is on a short term rental, then it is the responsibility of the rental company.
The importance of preventative maintenance is highlighted by Ian Capes, managing director of Maxim, UK distributor of Baoli equipment. “In today’s world no business can afford to hold a back up truck, so when a truck is out of action the business can be affected. To ensure up time of the truck is at a maximum the key service issues are the preventative maintenance frequency, the response time and first time fix.
Some companies prefer to maintain their vehicles themselves, while others choose to outsource service and maintenance.
Capes argues that outsourcing is the way to go. “There is a false belief by some users that having their own engineer on site gives them a quicker response and repair time. This is actually very far from reality. When you are responsible to keep trucks running, you do need to know what you are doing. Having a trained and experienced guy stood around when no repairs or maintenance are required can be very costly.
“By contracting a service agent who does this repair daily, gives the assurance of the correct fix. Users should look for dealers who are fully trained and qualified to carry out all necessary repairs and hold the latest diagnostic repair fault finding equipment.”
It is all too easy to get it wrong when it comes to maintenance. “It is a very generic mistake to always select the cheapest price, this being the price on paper,“ says Capes. “However, the users should look at the level of service on offer, the qualification and expertise level of the physical engineers, and the type of parts and general back up on offer. This way they can be sure that in the end they will get low running costs.”
Cost is always a critical issue and Sally Baker, marketing manager at Briggs Equipment, argues that buying on price alone is a short-sighted approach to materials handling management and one that is likely to backfire in light of growing customer demand for longer rental/lease contracts.
“When it comes to fleet expansion or equipment upgrade, an evaluation of lifetime costs enables fleet managers to arrive at a meaningful figure and facilitates comparison. That said, what is the lifetime of a forklift truck? It was typically calculated over three years, but nowadays a lease/rental contract is more likely to be for five or even seven years and some businesses want to spread the cost over ten years.
“Servicing and maintenance is essential, irrespective of whether the business owns the equipment outright or acquires it on a rental or lease basis. Key performance indicators cannot be achieved if forklift trucks break down regularly. Businesses have to weigh up the costs of employing their own engineers or outsourcing. Carrying out servicing/maintenance in house gives you complete control, but it’s a question of having the requisite expertise to keep equipment downtime to a minimum and taking into account increased overheads in terms of the associated costs of employment.
“Outsourcing from industry specialists ensures the engineers working on your machines are up to date with industry developments and are fully trained on the equipment they support. With the ability to turn the level of service up or down and on or off, outsourcing is highly flexible and enables the company to focus on its core competences to achieve/maintain a competitive advantage.”
Baker also points out that fleet managers need to understand their contractual obligations. “Most rental and lease contracts, which cover around 80 per cent of equipment acquisitions, include a service level agreement for preventative maintenance. However, the customer still has an obligation to look after the equipment because accidental damage is not covered by the rental/lease agreement.
“To monitor performance, spot trends, pinpoint issues such as truck overuse and the associated extra cost this would incur, technology plays an increasingly important role. Fleet managers can’t get the best out of their forklifts if they can’t measure how they are performing. Briggs Equipment developed its interactive, web-based reporting system BE Portal to satisfy the customer need for more comprehensive, dynamic query-based reporting and reliable information on which informed decisions about improving productivity can be based.
Lifecycle
“Performance/maintenance issues tend to occur as a forklift near the end of its lifecycle. If it has not been well maintained, the older the equipment is as the contract nears its end, the more likely the customer is to experience breakdowns. Unplanned maintenance impacts on the total cost of ownership while also having a detrimental impact on productivity and driver morale.
“Drivers have a key role to play in helping to minimise unplanned repairs. Knowing how to operate the forklift truck to carry out a particular task is all well and good, but well-trained drivers respect their equipment and use it properly. Their input, in terms of carrying out daily checks and reporting any problems promptly, and their efforts to reduce risks in the workplace and so minimise the likelihood of damage to equipment, are critical in reducing equipment downtime, keeping repair bills low and achieving KPIs,” she says.
Capes says: “Downtime is an expensive issue and the effect on the total cost can be horrendous. To keep the uptime as high as possible, it is important that the preventative maintenance service frequency is calculated correctly on an annual basis. For the service plan the application and its effects on the truck needs to be taken into consideration. This includes understanding, for example, dusty environments, heat exposure, etc.
“Parts fitted come into play for the total cost as well. Some providers try to convince the users that by fitting cheap aftermarket parts they will save money. However, experience and evidence show that this is actually not the case. In reality they often can last a much shorter life span of a genuine part.”
Baker highlights the pivotal role of the driver in getting optimum performance from a truck as well as controlling maintenance costs.
“Some fleet managers are under the misapprehension that their rental contract covers damage caused by careless forklift operators, but it doesn’t. It’s therefore vital that drivers understand they must respect their equipment. This means only using a forklift to carry out the tasks it is designed to do, conducting daily safety checks, working to proper procedures and ensuring that the equipment is deployed in a suitable environment.
“Drivers have to appreciate that getting the job done as quickly as possible is not the answer. Taking the time to check the forklift truck over and look for potential faults, in accordance with the relevant equipment checklist, must be part of their daily routine. Whatever time pressures they may be under, shortcuts are unacceptable. Overloading, driving with an elevated load, forgoing PPE and complacency when parking all involve risks to driver safety which, in turn, can compromise the business operation.”
Accidents
Baker points out that it is widely accepted that most accidents are due to untrained drivers and unsafe working practices, yet a good proportion come about during interaction with third parties.
“It is especially important that forklift drivers are vigilant when working with lorry drivers during loading/unloading on site.
“Two of the most common causes of damage occur at the loading dock, when the forklift truck is inside, and when lorries pull away as a truck is about to drive inside. The truck sustains damage as it either falls out of the lorry or off the end of the loading dock and the forklift operator is also likely to be injured. The onus is on the forklift truck driver to signal that it is OK for the lorry driver to move off.
“Even the most experienced drivers can slip into bad habits and if parts wear prematurely as a result of bad practice, this results in unexpected repair bills which impact on total cost of ownership. Technology enables fleet managers to calculate machine damage, but if fleet managers factor in damaged stock, broken racking and other site damage, the real cost to the business starts to become clear.
“Expert training designed to raise awareness of the issues and change behaviour combined with policies and incentives that value forklift operators will reduce the potential for damage and major, unplanned maintenance bills. Importantly, by getting the best out of its drivers, a business will reap numerous benefits, including increased productivity from a contented workforce,” she says.