Improving the service and maintenance strategy of forklift fleets is a complex task driven by a combination of technology, planning and design. Alexandra Leonards looks at how manufacturers are refining the function and explores the impact Euro Stage V is having on costs.
The burden on logistics operators to adapt to an ever-expanding e-commerce market, alongside the pressure to handle increasing stock levels and deliver goods in shorter windows, takes its toll not only on the industry, but also on the equipment that serves those growing demands.
In a changing consumer landscape, forklift trucks are handling more and more stock, as well as increasingly varied loads. This means that ensuring there is a successful service and maintenance strategy in place is now more crucial than ever before.
The forklift truck industry’s approach to improving service and maintenance has certainly not been one-dimensional. Instead it has implemented a two-sided strategy: to advance access to service and maintenance, while at the same time focussing on improvement of truck design to reduce and minimise the need for maintenance in the first place. By using a combination of associated technologies, planning and design, the market can meet these aims and establish a culture of strong service reliability.
“Having a service and maintenance strategy is really important,” says Paul Hardill, operations manager north, at Doosan Industrial Vehicles. “A user may put a service off if business is busy, but pushing it back can ultimately result in a major breakdown, involving big costs…”
Crucial to minimising downtime and total cost of ownership is adhering to a well-developed service and maintenance strategy. If adjustments and repairs are made immediately, the risk of a breakdown is minimised, and uptime is maximised. This only happens if there is careful management and analysis of the equipment, often through technologies that support manufacturers.
“Any advanced service support operation should have a Fleet Management System which enables customers to access up-to-the-moment information on their equipment fleet, log breakdowns on a 24/7 basis and access maintenance records, account details and other vital information,” says Hardill. “Importantly…live data should be fed through to the engineer’s tablet, making site visits simpler, with all maintenance records updated in real-time.”
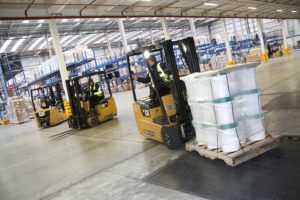
According to Robert Yates, transit warehouse manager for logistics company Europa Warehouse, new technologies and applications are being used by some manufacturers to plan maintenance, pre-order service parts and monitor truck performance. “The goal is to optimise operating time and efficiency; one example of this is the constant measurement of particulate in Hydraulic oil, enabling servicing to be planned when it is needed rather than by a pre-determined time schedule,” he explains.
The important task of monitoring battery performance is also being advanced by new technologies. “Maximising efficiency is vital for intensive logistics operations,” says Stuart Browne, operations director – sales and service, at battery manufacturer Hoppecke UK. “Yet, as raw materials and finished products are moved around a facility, it is all but impossible to tell whether forklifts are being deployed in the most efficient way or how well batteries and chargers are performing.”
If there was no way of measuring this, it would be very difficult to identify the right time to replace a truck battery. A logistics operator might assume that because a battery is having performance issues it must be replaced, when actually the case may be that a refurbishment using original spare parts would be sufficient and more cost effective.
“Happily, the answers lie with the latest technology, which can provide a full analysis of equipment use,” adds Browne. “Armed with data that offers a true picture – not only trucks working hours, but also actual energy used, you are empowered to take action to optimise the working life of batteries and chargers to improve energy efficiency with no unexpected replacement costs.”
It’s not just accompanying technologies that are transforming service and maintenance strategy. The very design of the equipment is changing to minimise the need for maintenance and repairs.
For example, as a standard feature, Doosan counterbalance trucks have an oil-cooled disc brake system. “As they are manufactured as completely sealed units the system is protected against outside elements, such as water, dust, dirt, shrink wrap and metal banding, and this really cuts out the high maintenance requirements of traditional brakes,” says Doosan’s Paul Hardill. “Another significant move is the development of diesel particulate filter (DPF) free diesel engines.”
According to Europa’s Yates, there are a number of design areas that have improved the reliability of lift trucks and lengthened service intervals. “The move towards electric trucks and the ability for them to work in more applications has meant less service and maintenance work due to the lengthened service intervals on these truck by comparison to I/C Engine units, whilst on the I/C units themselves the introduction of improved oils and lubricants and the use of long life filters also leads to longer service intervals,” he explains.
According to John Maguire, managing director of Narrow Aisle, the development of lithium-ion batteries is also helping to reduce the amount of service and maintenance trucks require.
“…the fully integrated lithium-ion system used to power Narrow Aisle’s new Flexi LiTHiON range of articulated reach trucks requires zero maintenance – the truck monitors the battery function constantly and reports the battery status in real time,” he explains. “Other developments such as digital electric motor technology are also helping to reduce truck maintenance requirements.”
Narrow Aisle has also introduced digital electric motors across its Flexi range of battery powered VNA warehouse reach trucks. With all drive, hydraulic and power-steering functions controlled digitally, the trucks offer significantly reduced maintenance costs.
“Operator diagnostics to aid security and fewer and simpler preventative maintenance visits per year will increase uptime and reduce maintenance costs across the range,” adds Maguire. “And simple, easy to use diagnostics and a low-cost handheld service module allow engineers to rapidly identify any potential fault before it becomes a real problem.”
The impact of Euro Stage V regulations on service and maintenance costs
The changing design of forklift trucks across Europe is not only driven by aims to reduce maintenance. Diesel and LPG forklift trucks must now comply with new EU Euro Stage V emissions regulations, established at the beginning of the year.
The rules enforce more stringent Particulate Matter (PM) and Particulate Number (PN) emission limits for engines between 19 kW and 560 kW, according to the International Council on Clean Transportation.
These diesel and LPG powered vehicles must now reduce their PM emissions to 0.015 grams per kilowatt-hour, a 40 per cent reduction on the previous Stage IV regulations. This means that the design of trucks must change significantly.
Euro Stage V regulations are having a varied impact on the market. Many manufacturers and their customers are reaping the benefits of cleaner equipment, while some are still waiting to feel the impact on their service and maintenance costs and others are struggling with such drastic changes.
Europa Warehouse is yet see the consequences of such regulations. “The effect of the change to Euro Stage V engines has not been felt yet, as we are waiting for details of servicing requirements and oil specs etc from the engine manufacturers,” explains Robert Yates. “The maintenance procedures and diagnostics are more computer based for these engines and so it is difficult to forecast the effect on maintenance until we have more details.”
JCB has certainly not been hard hit by the new changes and has instead embraced the new emissions rules.
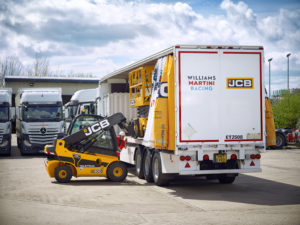
“In addition to meeting the latest emissions standards, Stage V compliant models in the JCB Logistics Teletruk range are 25 per cent more fuel efficient and, typically, can undertake a full eight-hour shift on a single bottle of gas,” says Paul Murray, general manager, JCB Teletruk. “This significant reduction in fuel consumption not only optimises truck up-time but also means total cost of truck ownership is minimised.”
But the changeover to Euro Stage V is not necessarily straightforward. For example, LPG trucks need to be kitted up with three-way catalytic convertors in order to reduce or eradicate particulate matter. Though, as commercial director of Doosan Paul Watson points out, this equipment is fairly inexpensive and requires minimal maintenance.
The real question mark hangs above the diesel forklift truck market. Diesel vehicles must go through what Watson describes as “lengthy regeneration processes” associated with diesel particulate filters or “DPFs.” He says that most diesel trucks on the market prior to the new regulation required DPFs anyway, in order to meet previous Stage IV rules. But, with trucks needing to reduce their emissions even further, diesel trucks now need even more advanced DPF cleaning systems and operating regimes. According to Watson, this may mean longer periods of downtime and more expense for less sophisticated diesel engines.
However, there are ways to avoid the downsides typically associated with DPFs. For its Euro Stage V engines, JCB has developed a low-particulate combustion system which works to reduce in-cylinder emissions before they enter the exhaust. They are and are fitted with a compact, highly efficient, combined selective catalytic reduction system and exhaust filter for engines above 56kW and a single canister, oxidation catalyst and exhaust filter for 55kW models.
Other manufacturers are also finding ways to sidestep the disadvantages of DPFs. A number of years ago Doosan launched DPF-free G2 engines, which offer lower fuel consumption, longer maintenance intervals and maintenance-free after-treatment systems. These trucks exceed the previous Euro Stage lllB and Stage lV legislation, with no need to carry out a regeneration cycle on the DPF.
Mitsubishi launches Euro Stage V LPG truck
Mitsubishi has launched what it describes as the first LPG forklift to meet Euro Stage V low-emission targets.A customer-led trial found that the Mitsubishi GRENDiA ED FG15-35N range, which includes both LPG and diesel models, consumed 40 per cent less fuel than rival machines. According to Red Diamond Distribution, the exclusive importer of Mitsubishi Trucks in the UK, over a five-year rental term this would equate to savings of more than £10,000.
“The need to reduce our environmental impact is more urgent than ever,” says Stewart Gosling, sales director at Red Diamond Distribution. “It’s not simply good practice but also about being on the right side of the law.
“In the past that drive to achieve conformity and meet demanding new environmental standards has almost always resulted in an uncomfortable compromise, usually a deterioration in performance or an increase in fuel consumption.
“In short, the GRENDiA ES series sets the highest standards for IC engine counterbalance forklift trucks in terms of carbon footprint whilst enabling the operator to achieve maximum productivity…”
According to Red Diamond Distribution, the LPG-powered trucks include closed-loop three-stage catalytic converters which reduce carbon monoxide and hydrocarbon emissions, alongside 95 percent of dangerous NOx gases.
Both the LPG and diesel models in the GRENDiA 1500-3500kg capacity range are fitted with a sealed chassis and belly guard, designed to stop the “cyclone effect” whereby the engine sucks dirt from the floor and throws it into the air.
“The Mitsubishi design team is genuinely focused on real-world requirements,” says Gosling. “They appreciate that customers face multiple, often competing, challenges; balancing the need to work at peak efficiency, drive down running costs all while meeting ever-changing legislation.
In developing the GRENDiA range they’ve achieved the near impossible by doing that and more: reducing the owner’s carbon footprint and maintaining Mitsubishi’s legendary reputation for reliability.”
Service reliability is key for Chiltern Cold Storage
Chiltern Cold Storage, which specialises in temperature-controlled logistics solutions, has a long-standing relationship with its forklift truck supplier UniCarriers.
The Peterborough-based company operates multi-temperature warehouses, including ambient, chilled and frozen. It stores more than 2,500 different products, from raw materials and ready meals, to poultry and ice-cream. Working in extremely low temperatures is a challenge for the business and has an impact on its industrial trucks, which must be reliable and available for a daily handling of about 1,200 pallets.
“In our three warehouses, we need a truck fleet with this throughput that can withstand the harsh environmental conditions day after day,” says John Davidson, managing director at Chiltern Cold Storage. “The temperature in the warehouse is between -22 and -24 degrees Celsius – the key thing for us is service reliability, and this is what UniCarriers offers us”.
The fleet of UniCarriers vehicles are used for disparate purposes: pallet picking and exchange as well as storage and retrieval are handled by Chiltern Cold Storage with reach trucks. While the logistics business utilises PMR pallet trucks to load and unload trucks and transfer pallets to other storage areas. Counterbalance trucks are used for container transfer and various yard work. Chiltern Cold Storage also uses high-level order pickers from UniCarriers, primarily for inventory control.
UniCarriers has provided the company with 22 vehicles, but the scope of the relationship reaches far beyond just acquisitions. In fact, the manufacturer gives advice for new orders and the implementation of major projects.
“What convinced us above all was the high level of reliability,” says Davidson. “With the UniCarriers vehicles, we have minimal maintenance requirements and a great uptime.
“They are an irreplaceable piece of equipment in our warehouses.”
UniCarriers has regular meetings at Chiltern Cold Storage, where key performance indicators such as the total cost of ownership of the fleet are discussed. During site visits, partners discuss current challenges and evaluate procedures and processes.
“UniCarriers gives us recommendations for optimising our workflows, but we also pass on our experience as input,” explains Davidson. “This regular exchange benefits both sides and is an integral part of our collaboration.”
During monthly meetings subjects such as battery-performance of trucks and the impact temperature-controlled logistics has on the vehicles are discussed.
This feature originally appeared in the November 2019 edition of Logistics Manager: click here to subscribe to the print edition