Logistics Manager recently paid a visit to DHL’s London Gateway facility to see how the site operates and speak to Saul Resnick, UK&I CEO at DHL Supply Chain.
Having opened in June 2023, the facility achieved BREEAM ‘Outstanding’ certification. It features 3,700 solar panels producing 27% of the site’s power usage, as well as LED lighting. It has been key to DHL customer Mars UK’s supply chain strategy, serving different aspects of its business: Mars Food, Mars Wrigley, and Mars Pet Nutrition.
The construction of the site represented a £350 million investment, part of a strategy to remove 7.7% of current Mars transport from UK roads, equivalent to 1 million miles annually.
In May 2024, the site was visited by the prime minister at the time, Rishi Sunak, who said: “It was a pleasure to visit DHL’s London Gateway distribution centre to speak to staff and tour the impressive site. DHL and Mars’ £350 million investment into this site is a big boost for the area, creating hundreds of jobs.
“Jobs create growth, and financial security which is one of my top priorities, and it was great to see this in action.”
Upon approaching the facility, its height is one of the first things one might notice. Spanning 482,000ft² and standing at 42m, it is one of the tallest distribution centres in Europe. Inside, it houses a tall automated storage and retrieval system (ASRS), with around 99,000 pallet storage locations.
Goods stored at the site range from chocolate products to pet food to chewing gum – which is stored separately to avoid contamination. Products leaving the facility are typically moved to UK stores or retailer distribution centres. The warehouse is constantly monitored from the ‘flow room’, where cameras and displays provide real-time visibility of picks, loads and any technological issues which might impact the operation.
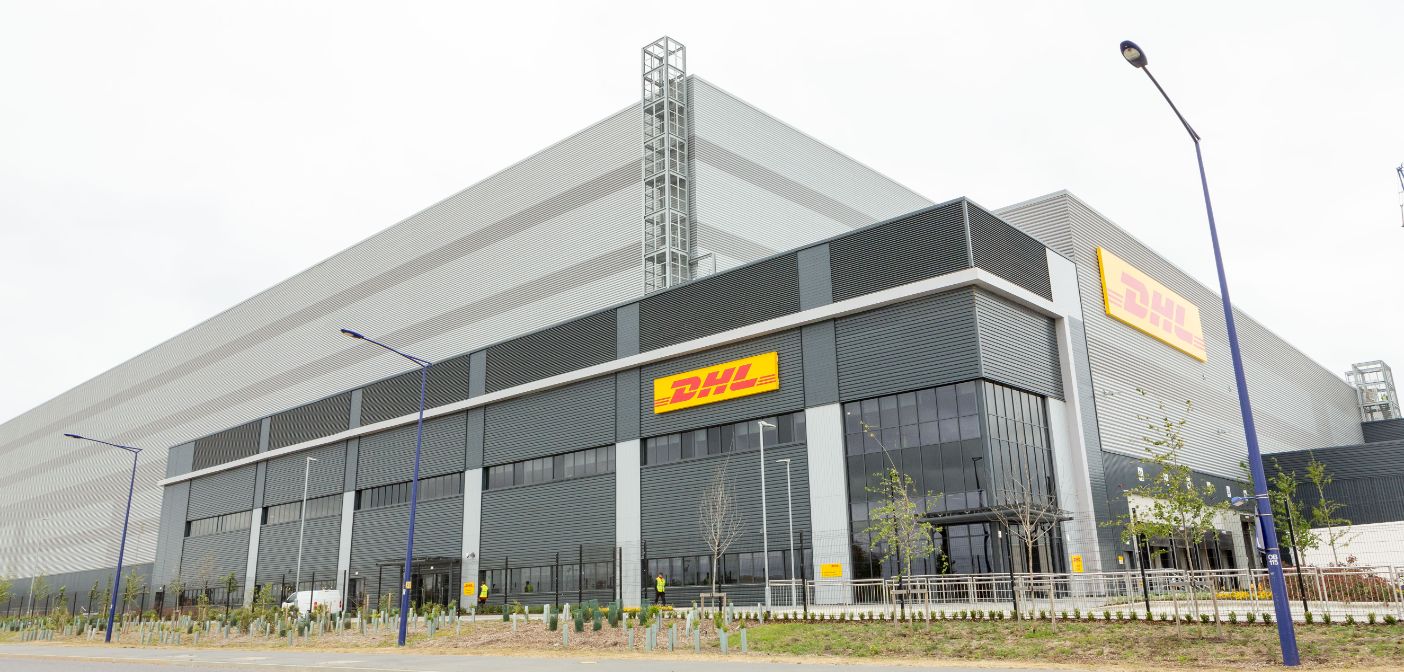
To understand more about DHL’s London Gateway facility and how the logistics company is responding to recent trends and challenges, Logistics Manager sat down with Saul Resnick, DHL Supply Chain’s UK&I CEO. Here’s what he had to say:
First of all, what makes this facility stand out in terms of sustainability?
It’s achieved its BREEAM ‘Outstanding’ accreditation, placing it in the top 1% of non-domestic buildings in the UK environmentally. It’s helped Mars realise its ambition of creating a world-class logistics environment that is sustainable, smart and agile using the latest technology and storage facilities like ASRS technology and high-frequency charging of equipment. [The site has] up to 30% less energy usage, using rainwater harvesting and LED lighting throughout.
Why was London Gateway specifically chosen as the best location for this facility?
That’s really about access to the port, access through our links and the ability to take product off the road as much as possible. [The facility has allowed] about a million miles to come off the road, which reduces Mars’ logistics footprint by about 7.7%. So the access is great. It’s also a good source of employment, in terms of people in this area, and very good access into the London market as well from a population point of view.
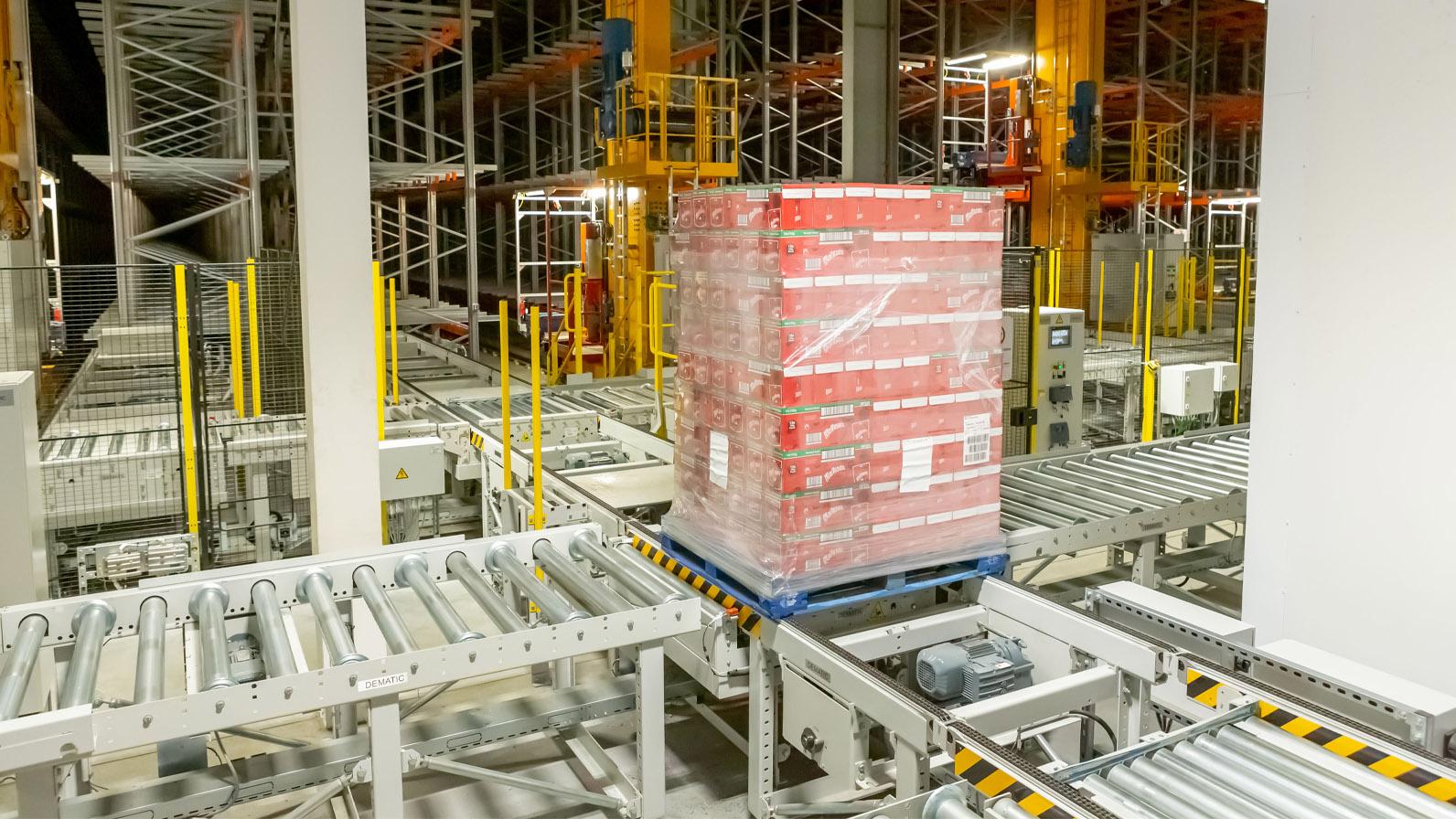
Walking around today, we can see that there’s a lot of technology in use, whether it be the conveyors or the ASRS. Could you tell me a little bit more about the technology in use at this facility to assist with processes like picking, packing and materials handling?
We’ve got the latest ASRS, you’re quite right in saying that. Blue Yonder is the WMS that we use. We’ve got DAI Matflo yard management and slot booking tools. So you saw an example of the flow room where we utilise those tools. We have robotic wrap machines, we have automatic vehicle offloading conveyors, so there’s no human intervention in that. We have materials handling equipment using lithium-ion batteries to reduce electricity usage. And then we also have people using smart-powered business intelligence tools and what have you, which operate the activities and look for continuous improvement.
You saw examples of performance dialogues on touchscreen boards, where people are engaging on a continuous basis with live information, and we can monitor progress accordingly and monitor performance accordingly as well. There’s an array of different technologies.
Another emerging technology that seems to have taken on a larger and larger role within the logistics industry is AI. What role is AI playing in DHL’s operations?
AI is clearly an evolving capability and platform that most organisations are now playing with, but [we’re] not necessarily at the maturity of it, and will be some time before it [reaches a stage of maturity]. But we certainly make use of AI globally and within the UK, where it may be able to help us with resource planning, identifying where we may need talent or people in particular areas of geography up front.
And also from a technology and automation point of view, where we might need equipment ahead of the curve based on what demands and patterns are predicted.
From a productivity point of view, we’ll use AI to make sure that we’re using the best pick path, the best operational performance that we could do to make the slotting of the product a lot more efficient. And wherever we can see nuances where we historically would be using spreadsheets or manual intervention, that technology and that robotic learning is now allowing us to make sure that we use our historical data and our current data, of which we have an enormous amount, to our benefit to make sure that we’re more efficient and more effective in our operations.
The festive period is fast approaching, which is obviously a busy time for Mars – one of the biggest customers at DHL’s London Gateway site. What is DHL doing to prepare for the peak season approaching at the end of the year?
Peak season is consistent with any logistics organisation. You’re always going to have peaks and troughs. Most industries go through that. So for us, it’s all about planning and preparation where we anticipate that we’re going to need more staff.
It’s getting those staff on board early, that we bring them in and train them up quickly into our business. But it’s also about understanding the data, staying close to our customers, talking to the customers, understanding what trends, if any, they’re seeing in their marketplace, and what their expectations are.
Black Friday and Cyber Monday – those are relatively new constructs that didn’t exist some 10-15 years ago, whatever it might be now. Whereas it always used to be about peak, now you’ve got different peaks and different troughs that occur in the market.
So we have to make sure we’re prepared for them and plan for them, which is what we do on pretty much a routine basis. When I say routine, we’re always planning for what’s coming ahead but if we know that there’s big peaks ahead, then we have to obviously plan from a recruitment and staffing and space availability point of view as well.
And staying on that topic, how has increased e-commerce demand impacted the logistics sector on the whole and at facilities like this one?
What’s clearly changed, and I can talk from my own personal experience having been in the industry for a long time, is that customer expectations, our customer’s expectations and their customer’s expectations, are different to what they used to be, specifically around speed. I’ve got children and if they order something at 9:00 this morning, they wonder by lunchtime why it hasn’t arrived.
So we have to be aligned to that expectation, consumer expectation, as well – and we are. So we’ve also changed our service offering somewhat in some cases. [For] small to medium-sized businesses specifically, who aren’t necessarily the size of large multinational organisations, we want to give them access to our systems and technology and people and processes as quickly as possible.
So we’ve come up with platforms like DHL Fulfillment Network, which gives a standardised-type approach to e-commerce from a technology integration and contractual service perspective. It’s almost like a plug-and-play, where they can bring their products in very quickly, have an operation set up not massively dissimilar to what you saw today, but on a much smaller scale, perhaps. And then they can start trading and transacting with their customers in a much quicker way than what historically would have been the case. So we’ve evolved accordingly, and we have a couple examples of that platform that I’ve just described that enable a lot more customer centricity, from our perspective at least.
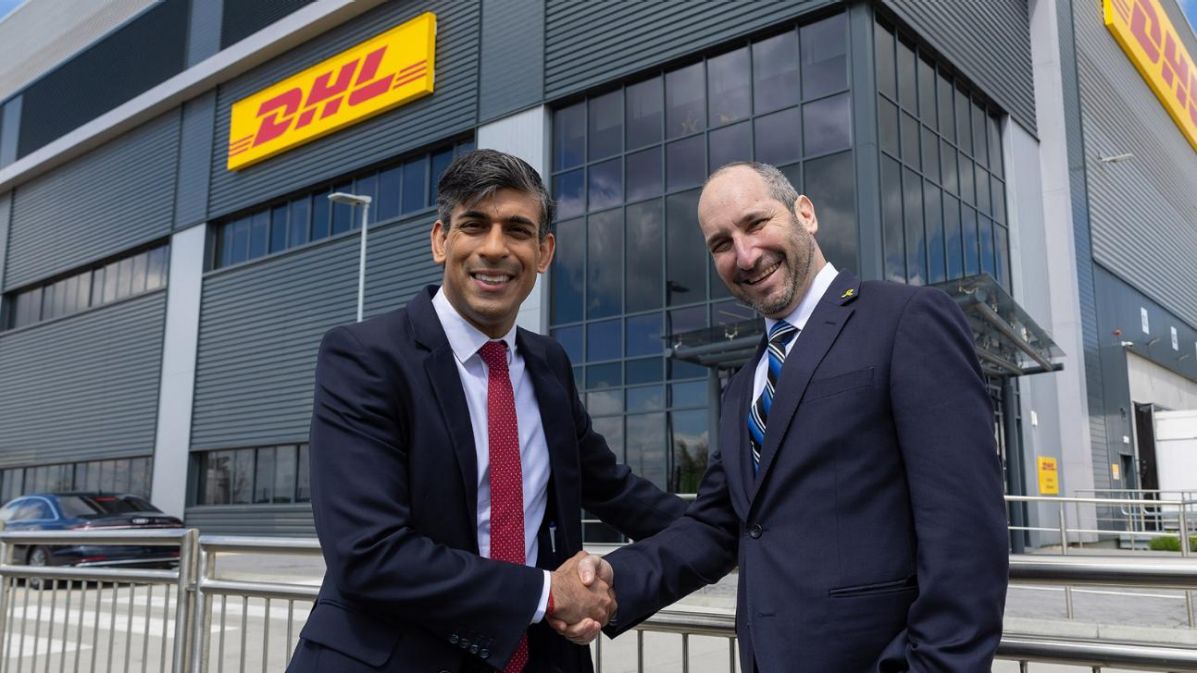
Lastly, this site was visited by former prime minister Rishi Sunak in May. The UK obviously now has a new prime minister, Sir Keir Starmer. What do you expect from him and his government in terms of support for the logistics industry, and what would you ask of the new government?
If you go back pre-Covid, most people would not have understood what supply chain is, I think it’s fair to say. Clearly Covid demonstrated that if the supply chain fails, everything fails. And so there’s a lot more public awareness about what the supply chain is. We appreciated the visit from the previous prime minister, and hopefully we’ll be able to entertain the new prime minister sometime soon as well.
We appreciate the work that they are doing with us, but clearly we’ll continue to argue the case that logistics and supply chain needs to have a distinct focus and that the government and public bodies understand the importance and the criticality of getting supply chain right.
And that can be a number of things. It’s about road access. It’s about power access. It’s about access to charging stations. It’s about access to electricity for battery electric vehicles. All of those things are critical to our future as an industry in supply chain and logistics, but also to the government’s ambitions to grow business, which I know they have.
I recently had the privilege of being at 10 Downing Street with the business minister, the chancellor and the prime minister [to hear them] talk about their ambitions as a new government. So for us, [it’s about] continually educating them on how we can help them achieve their objectives as a government and as a country by making sure that we’re at the forefront of innovation and that we’re well-equipped to manage whatever demands or challenges may come ahead.
READ MORE: DHL launches new Coventry DC, announces contract with Sephora