Service and maintenance is crucial to those that rely on forklifts in their operations. Alexandra Leonards explores the challenges happening market, and examines the best ways to maximise the life expectancy of equipment.
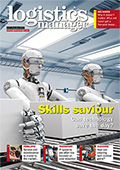
Maintaining the quality of a forklift is tough for both the manufacturer and the customer. For the manufacturer, ensuring the customer’s requirements are met is a big task, while for customers, choosing the right package and supplier can be a real challenge.
Crown’s Simon Barkworth points out that, from a customer perspective, the key challenges include deciding which lift truck manufacturer and/or provider is going to provide the lowest total cost of ownership (TCO).
“This can be particularly challenging, as the market is so competitive and customers may be tempted to opt for the lowest acquisition price only then to be stung by much higher maintenance repair bills over the duration of the contract, for example for damage repairs,” says Barkworth. “From a supplier’s perspective, the challenge is to convey to the customer that you have the right package in terms of product and service that will ultimately give them the TCO they are seeking.”
At Jungheinrich, the business has noticed that with tighter deadlines and increased volumes, consumer demand and the rise of e-commerce has placed more pressure on warehouses and distribution centres to become more efficient.
“The supply chain must now reflect a 24/7 consumer culture,” says Steve Shakespeare, director, customer service at Jungheinrich UK. “With changes to shift patterns, a flexible working culture is expected and, as such, more flexible intralogistics solutions are being sought.
“When it comes to e-commerce and multichannel operations there is a certain level of uncertainty whereby peak periods could see increased usage and volumes. As such, organisations are looking at ways to optimise the performance of their equipment by investing in the right service and maintenance programme.”
Linde has noticed the same trends. “With a huge upsurge in online shopping, many warehouses – particularly in the retail sector – are working towards a 24/7 operation,” says Steve Redman, service operations manager at Linde Material Handling. “While staff will work in shift patterns to avoid fatigue, the trucks are often in operation constantly with precious time spared for refuelling, charging and checking for faults.
“Wear and tear of trucks in constant use will only become more and more common with this upward trend in online retailing. This trend is also true for industries who experience significant seasonal peaks such as around the Christmas period, or crop harvesting seasons.”
Francesco Pampuri at Baoli EMEA thinks that, regardless of positioning in the market, the challenge which all manufacturers face is that of providing a premium quality after-sales service, to reduce to a minimum the machine stoppage times.
“To respond to this challenge Baoli has set up a solid organisation in Europe with an enormous warehouse in Italy, which will act both as a centralised distribution hub and a spare parts area,” says Pampuri. “The aim is that of being the first manufacturer of forklift trucks from the Far East which can count on a sound and well-organised structure which is able to ensure the complete and immediate availability of spare parts.
“On the other hand, the technical support is provided by a network of carefully selected and trained dealers so as to guarantee extremely high levels of after-sales support.”
From Pyroban’s perspective, an explosion proof conversion of a forklift ensures it is safe in a potentially explosive atmosphere at first use. “However, to counteract the risks posed by inevitable wear and tear, a system of preventative maintenance should be put in place to ensure equipment continues to be safe, and is regularly serviced by an engineer trained to work on the specific explosion proof system,” says Darren Boiling, Pyroban. “Companies are often working under time pressures and in the event of a problem with a truck, might be tempted to try a quick fix with any available engineer.
“However, even small changes by an untrained engineer can compromise the whole safety system, and in turn the safety of the whole site.”
What are the best ways to maximise the life of a forklift?
“It would without doubt be to carry out the machine inspections specified by the manufacturer,” says Baoli’s Francesco Pampuri. “These requirements are too often ignored, thereby running the risk that a small problem such as the wear of seals or a lack of oil generates more serious problems which could have easily been avoided.”
This is a strategy that Crown also sees as one of the best ways to extend forklift life. “Always ensure the lift trucks are serviced to the manufacturers’ recommended frequency and standards,” says Crown’s Simon Barkworth. “Gone are the days of servicing a truck based on the calendar – i.e. religiously servicing it every six months or every quarter regardless of how much usage it has performed since the last service.
“This can lead to trucks not being serviced as regularly as they should be. With modern fleet management systems such as InfoLink, the usage hours of the trucks are constantly being recorded and will flag up when a service is due.”
Linde also suggests truck operators carrying out daily checks on the trucks to make sure everything is in good working order and to ensure safety.
“Fleet managers should also schedule regular services every 1,000 hours to ensure that their trucks are not only in a safe and usable condition for the operator, but are also working to their maximum efficiency,” says Linde’s Steve Redman. “For example, our ‘connect:’ system on the truck tells Linde that it is approaching its 1000hr service schedule ensuring that the customer has minimum downtime and the product is serviced in line with the manufacturers guide.”
According to Jungheinrich’s Steve Shakespeare, because forklift trucks are heavy-duty pieces of equipment and are built to be durable, often operators can be less mindful when it comes to operating them in a manner that will contribute to extending their working lives.
“Prevention is often much better than cure, so maintenance of the external working environment and consistent routine inspections of the truck are necessary to help avoid costly and unnecessary damage,” says Shakespeare. “Overall wear and tear to the forklift truck will be more significant if the working environment is untidy or unkempt; running over debris such as wooden pallets and plastic wrap can cause avoidable damage to forklifts.
“Adhering to safe working practices and ensuring that regular inspections are carried out can also help significantly.”
Kate Pointeau, brand manager at Hyster Europe, says that access to key components is crucial to helping minimise service and maintenance downtime for busy operations.
“For example, cowl-to-counterweight service access, a one-piece removable floor plate and simplified layout of the wiring and hydraulics all feature on the Hyster Fortens 2-3.5 tonne IC trucks,” she says.
How to extend the life of your battery
Jungheinrich’s Steve Shakespeare says that battery technology is evolving and energy management is becoming increasingly important.
“Understanding the maintenance of these changing energy sources is crucial when it comes to ensuring batteries perform to the best of their capability,” says Shakespeare. “Outside of committing to a specific battery service plan there are several things that operators can do themselves to prolong the life of a truck’s battery.
“Specifically, when it comes to lead-acid batteries, it is best for operators to avoid quick charges during work breaks, as this could result in reduced performance and efficiency.”
As well as this, checking water levels can also be very important when it comes to the life expectancy of batteries.
“ A regular regime of cleaning and topping up the battery with distilled water can greatly extend its working life and performance,” adds Shakespeare. “Lithium-ion battery technology is far less demanding when it comes to maintenance and, unlike a lead acid battery, is capable of working efficiently when charged in shorter bursts.
“However, continuous partial discharges can decrease the accuracy of the devices power gauge, so it is important for operators to, on occasion, let the battery fully discharge to its cut-off point and then recharge.”
Linde’s Steve Redman says that it’s easy to prolong the life of batteries: charge a battery at the end of each eight-hour shift or if it is discharged more than 30 per cent, always charge a battery in a well-ventilated area, do not over discharge, maintain both truck and battery according to the manufacturer/suppliers instructions, always ensure the battery gets a full charge.
“However, thanks to Lithium –Ion technology there are alternatives to traditional lead-acid batteries,” he says. “The batteries offer unique features such as a CE label, user-friendly charging and – most importantly – considerable savings.”
According to him, these batteries: eliminate the need for battery rooms and increase your storage space, mean that spare batteries are not needed and the batteries do not have to be transported for re-charging. He says that lithium-ion batteries from Linde do not require servicing and can be charged during operator breaks (coffee break, lunch hour) without damaging them and these batteries can operate normally in ambient temperatures of between -35ºC and +45ºC.
Crown’s Simon Barkworth says that changing or charging batteries is of course is a priority, but equally important is proper maintenance of the batteries, including topping-up when necessary.
“ On the former, the Crown InfoLink system records and reports on the Depth of Discharge of the battery when it is put on charge,” says Barkworth. “For example, most battery manufacturers have warrant ies that cover a certain number of cycles of the battery.
“Charging or changing batteries too early will lead to an increase in the frequency of cycles and so will shorten that warranty period.”
“Among the many measures which can be taken to extend the life of the batteries, the most important are without doubt charging them correctly and checking the fluid level every week,” says Baoli’s Francesco Pampuri.