The efficiency and safety of the forklift truck fleet is dependent on a good service and maintenance regime. But a range of options is available and picking the right one is critical.
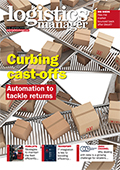
It is possible to make savings by delaying or cutting back on maintenance and servicing – but that saving can come at a very high cost. Peter Harvey, chief executive of the Fork Lift Truck Association, says: “Scrimping on this vital aspect of truck ownership will reduce the lifetime, efficiency and productivity of your truck, while increasing the risk of expensive, unscheduled downtime and repairs. But, most importantly, it puts people’s lives and health in serious danger.
“For smaller firms that operate a single, older counterbalance truck, this advice is even more relevant: counterbalance trucks account for 87 per cent of all fork lift truck accidents.”
Terry Kendrew, managing director of Impact Handling which distributes Cat lift trucks, believes an effective maintenance regime is vital to ensuring that trucks deliver the uptime expected.
He says it is all too easy to forget that trucks will need to be taken out of operation periodically for service and maintenance, and points out that it is not economical to have to call an engineer out because a truck has broken down.
Kendrew also highlights the need for engineers to have somewhere to work on trucks. Space is increasingly at a premium in warehouses, but it is important for the service engineer to have a safe place to work with the required services.
Mark Sullivan, aftersales director at Linde Material Handling, agrees: “Prevention is better than cure and ensures the truck is working to its maximum performance. Correct maintenance with regular checks ensures operator safety, keeps the truck in a stable and usable condition and can increase the life-span as a result.
“Operators should also avoid the temptation to get small jobs done quickly by lifting lighter loads with one fork alone – this is a more common practice in warehouses and can lead to problems further down the line, with uneven load bearings due to one fork receiving more wear and tear.
“Additionally, the Health and Safety Executive states that a ten per cent reduction in the original fork thickness means it is time for a replacement, as this equates to at least a 20 per cent reduction in load-bearing capacity.
“There are other golden rules which should be followed too, such as not allowing the forklift to ‘tilt’ when it’s lifting and making sure tyres are in good shape. Industrial forklift tyres should have a ‘60J’ line, indicating when they are down to their final 100 hours of usage and in need of imminent replacement,” says Sullivan.
Paul Jones, service director at UniCarriers, says: “On many occasions operators make the comparison between road-going vehicles and their MHE fleet and it’s easy to understand why, but should they? The priorities are similar – ensuring the fleet is serviced properly and at the correct interval. We promote regular PM service completion as one of our highest priorities. Automated advanced notice to the customers’ fleet manager, visible notification to the operator and PM completion compliance reporting to all our customers. We can’t always see the similarities when it comes to fuelling the MHE fleet. Road-going fleets enjoy being refuelled at forecourts that offer consistent quality of fuel, the same can’t always be said with fuel for IC-engined machines held at some customers’ sites or the correct procedures for using and charging battery powered machines. This is where we see downtime and avoidable costs being incurred and want to help customers take corrective measures.”
Most forklifts in the UK are on hire agreements, which will generally include a full maintenance package which can include tyres as well.
Impact’s Terry Kendrew says that users who choose to buy can choose a number of options including full maintenance or planned service packages. “We are quite flexible and can provide what the customer wants,” says Kendrew.
He points out that for many users, maintaining the forklift fleet is simply a burden and they are more than happy to have that taken care of by someone else.
Not only that, he says, sometimes those who choose to manage the maintenance of their vehicles can struggle to give it the attention it requires.
“My recommendation is to give it to us – we can maintain the truck in line with what you want.”
UniCarriers’s Paul Jones says: “All machines cost money to maintain, you can choose to include as much or as little as you want within your maintenance contract – the fact remains that maintenance is still needed and it still costs money. No matter how much usage a machine has or how gentle the site application, the contracted rate for maintaining a machine should be more attractive to a customer rather than on a pay-as-you-go basis. If a customer chooses to wrap up as much as they can into a maintenance contract, they can budget efficiently and focus on the avoidable costs that they may be incurring.”
Sally Baker, marketing manager at Briggs Equipment, advocates a proactive approach to maintenance as this will help to eliminate potential safety risks, minimise equipment downtime and reduce maintenance costs.
“Unplanned maintenance not only impacts on the total cost of ownership, but also has a detrimental effect on productivity and staff morale. Since well-trained drivers respect their equipment and use it properly, the influential role of the truck operator should not be underestimated when fleet managers assess costs and determine their maintenance strategy.
Baker argues that drivers have a pivotal role to play in helping businesses to keep maintenance costs down. Knowing how to operate a forklift to carry out a particular task is not the issue here. The input from well-trained drivers, who carry out daily pre-shift checks and report any problems promptly, along with their efforts to make safety a priority and so minimise the likelihood of damage to equipment, are critical in reducing equipment downtime, keeping repair bills low and achieving KPIs.
“Sometimes, fleet managers are under the misapprehension that their rental contract covers damage caused by careless forklift operators, but it doesn’t. It’s therefore vital that drivers respect their machines and appreciate that getting the job done as quickly as possible isn’t the be all and end all. Training is essential to ensure that operators conduct daily safety checks, work to proper procedures and use forklifts to in a suitable environment to carry out the tasks they are designed to do,” says Baker.
The importance of understanding what is, and what is not, included in a contract hire agreement is highlighted by John Maguire, director of Narrow Aisle.
“It is often more important to consider the things that have been left out of the deal as much as the items that have been included.
“Ask your supplier about limits to the number of hours of truck usage allowed before penalty charges apply. Consider if it would be cost effective for replacement tyres to be included in the package. Provision of diesel or LPG fuel is almost always excluded, with electric trucks becoming more popular, he says.
“What happens if the battery fails? Is the warranty the responsibility of the truck provider or the battery manufacturer? Does the battery warranty cover the whole length of the lease agreement? Will your supplier provide a replacement truck in the event that yours breaks down? If the contract doesn’t specifically mention a replacement the chances are that you won’t get one. Most MHE “Contract Hire” FMC agreements do cover for breakdowns and wear and tear repairs on the whole truck. Often MHE “Contract Hire” agreements do not cover replacement tyres, worn underside of forks, operator abuse and accident damage repairs. Does ‘maintenance’ mean all repairs caused by wear and tear?”
And, says Maguire, “it’s worth checking the supplier’s policy on truck return conditions at the end of the contract. If there is no mention of “fair wear and tear” then you may be obliged to undertake some refurbishment of paintwork, operator’s cabin and other components at your cost.”
The critical test of work-worthiness
Not all users realise it’s a legal requirement to pass a Thorough Examination of forklift machinery every year, much in the same way cars have to complete their MOT, says Linde’s Mark Sullivan.
“The examination ensures that the mechanical parts of the fork truck are regularly inspected to keep the fork truck safe to use when operated to manufacturers recommendations.”
Peter Harvey, chief executive of the Fork Lift Truck Association, says: “It is important to remember that Thorough Examination is not normally part of routine maintenance, so its requirements must be satisfied separately.
“Essentially, whether you own or rent a truck, you are responsible for ensuring this is carried out at the legally required intervals (at least once every 12 months) and obtain a Report of Thorough Examination. In addition, you will need to clearly display the next examination date on the truck.
“To maintain a fork lift truck properly, regular servicing must be carried out by someone with the necessary training and experience. It’s much more complex than servicing a car. Your truck’s manufacturer will recommend intervals for inspections and services and these vary depending on the nature and intensity of your application. Your service provider can advise on what is needed and when. If trucks are on hire, you must allow your hire company access for maintenance as necessary.”
And Laura Nelson, managing director of RTITB, warns: “Forklift operators may not realise that by not carrying out a pre-use inspection they may be breaking the law by failing in their duty of care to themselves and to others. Even if the correct inspections are taking place, companies also need to remember to properly record the checks that take place. Without this, they may not be covered in the event of an incident.”
Explosion proof trucks
Explosion protected forklifts are highly specialised pieces of safety equipment that should be maintained and audited in a very different way to standard forklifts.
Darren Boiling, group after sales manager at Pyroban, says that although equipment leaving the Pyroban factory is safe for operation in an explosive atmosphere, daily use in demanding applications can result in significant wear and driver damage, so it is imperative that equipment is maintained correctly throughout its life to prevent an explosion.
“There are three simple steps to maintain compliance and safety throughout the life of an explosion proof forklift. Firstly, use engineers who are trained on the Pyroban system, then, follow the recommended service schedules and finally, carry out Ex-ASAs.”
“Companies are often working under time pressures and in the event of a problem with an explosion protected forklift truck, might be tempted to try a quick fix with any available engineer. However, companies that do not use qualified engineers to conduct safety checks are risking their reputation and could face serious legal implications in the event of an incident.”
“ATEX 1999/92/EC requires the end user to ‘demonstrate that work equipment is designed and maintained with due regard for safety.’ Pyroban recommends its equipment is maintained to EN60079-17 which states that an inspection routine should be introduced to ensure the continued safe operation of equipment and that the employer is not failing in his legal duty of care.”
“The Ex-ASA annual safety audit is a thorough inspection of the safety critical components on an explosion proof forklift by a qualified engineer. It ensures that the integrity and safety of the materials handling equipment is not compromised during its working lifetime.”
One critical step
What is the single most important thing an operator can do to extend the working life of their fork lift trucks? Industry leaders are pretty much united on the answer: a proper daily check of the vehicle before the shift starts.
Terry Kendrew, managing director of Impact Handling, points out that this can provide an early warning of problems as identifying a problem while the machine is still fit for work can ensure than it does not break down. “A well looked after machine costs less to maintain.”
Ian Coulman, Rushlift’s UK sales director, points out that the first responsibility of an operator is completion of a pre-shift check (paper or management system) covering such things as oil levels, brakes, tyres, chains, forks, visible damage; reporting of any faults or damage immediately; and documenting and record keeping of pre-shift checks.
FLTA chief Peter Harvey focuses on the need to ensure that the procedure is a formal one that is recorded every time and performed in accordance to instructions from the truck manufacturer. If faults affecting safety are discovered, the truck should not be used until any resulting queries or concerns have been reported to a manager or supervisor; advice has been obtained on warning lights showing; and any fault affecting safe operations being rectified.
Linde can provide advice to operators on how to carry out daily checks, says Mark Sullivan. He also highlights the importance of scheduling regular services.
Thomas Toenders, telematics solutions specialist for Hyster, says: “Many businesses are lacking suitable monitoring for their forklift fleet. Quite often, they may not realise that they can be much more productive and save money by using data provided by an accurate fleet management system such as Hyster Tracker.”