The narrow aisle truck market is developing day-by-day, conjuring up new technologies to maximise performance. Alexandra Leonards explores some of the new technologies in the market.
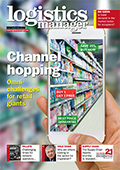
The narrow aisle truck market is seeing long-established systems combine with new and innovative technologies to amplify performance.
“Narrow Aisle trucks perform in some of the most intense warehouse operations and, as such, productivity is key,” says Simon Barkworth, managing director at Crown Lift Trucks UK. “Much talk of future technologies is about the Internet of Things, whereby mechanical objects are networked and their performance monitored and optimised.”
Crown has a wireless operator and fleet management tool called “InfoLink” which addresses demand for systems that can harness accurate and on-demand business metrics. “By connecting forklift trucks, operators and facilities and collecting accurate, InfoLink provides real-time information for better decision-making,” says Barkworth.
Driverless technology might also see itself fitting into the narrow aisle trucks market in the near future. “Driverless transport systems have until now primarily been used for tasks of a highly repetitive nature, such as transport of small parts,” says Jurgen Emmenegger, VNA and warehouse system specialist for Hyster Europe. “However, in future we anticipate that narrow aisle trucks, reach trucks and low level order pickers will increasingly be used in automated transport and in the putting away and extraction of palletised goods.”
He says that, depending on the application; a variety of technical solutions may be adopted. “This may involve partial or full automation of the truck using induction loops, camera systems, lasers, GPS or a combination of several systems,” he says.
Barkworth says that Crown uses lots of its resources on ensuring that uptime is maximised. “Strong steel covers protect expensive internal components; long-term reliability is improved by the separation of electronics from heat sources; and integrated technologies, such as Crown’s exclusive Access 1 2 3 Comprehensive System Control optimise performance, energy consumption and uptime,” he says.
At Hyster, they are offering warehouse simulation software to its customers. “Warehouse simulation software from Hyster can also be used to help customers design their warehouse for optimal flow, efficiency and product mix,” says Hyster’s Emmenegger.
“This takes challenges such as space limitations or congestion issues into account to help identify solutions with a low cost of operation, while achieving the peak flow rates required. With consumers wanting more choice and quicker deliveries, better warehouse design has never been more important.”
Crown has advanced its TSP Series by incorporating RFID. “The optional RFID-based Auto Positioning System (APS) enable it to take the most effective route to the next rack location with just one control handle movement,” says Barkworth.
“Upon receiving a task destination, the truck travels and elevates to the exact pallet location in the most time-efficient motion, increasing productivity by up to a quarter and ensuring correct slot locating, regardless of operator experience or skill level.”
The series also includes another optional feature, “Auto Fence”, which improves safety by automatically slowing travel speed, stopping, or limiting lift height within the VNA based on the location of the truck. The system catalogues special areas in an aisle, like intersections and overhead obstructions, and the truck continuously monitors its exact location to identify and follow any programmed restrictions or controls. “Also contributing to overall performance, the Regen Lower System creates and adds energy to the battery during the lowering cycle, while larger batteries provide access to more power, fewer battery changes and longer shift life,” adds Barkworth.
But what about handling specific types of products, that have unconventional shapes and sizes or larger loads?
“We have a model that is exclusively configured for handling rolls with the fork carriage replaced by arms that cradle the roll shaft,” says Hyster’s Emmenegger. “Another customer handles heavy doors of up to 2 metres long in their warehouse, so the VNA has been delivered with a longer turret head to accommodate these large, unwieldy loads.”
The company has also made trucks that are designed specifically for the spirits industry. These trucks include a tilt option, which enables easy turning of casks during the conditioning phase of storage.
“A high degree of attachment stability is needed on these trucks as the casks are rolled over the very tip of the forks,” says Emmenegger. “Another example is a customer which needs to store mattresses, washing machines, sofas and other large and heavy goods at a height of 10m in their warehouse cube.
“To support this application, the sturdy Hyster C1.5L VNA Truck has been modified with a walk-on platform and lattice gates on both sides. The lattice gates can be opened a full 2.7 metres giving a two-man team walk-on access to the racking for large items, such as super king size mattresses.”
According to him, the mast can handle a three metre long metal cage and a load of 800kg in any location on the platform.
“ Even at 10m, the cage moves only minimally, giving the team a stable environment in which to pick and put away stock efficiently,” adds Emmenegger.
Challenges
Barkworth thinks that the growth of e-commerce and the associated multi-channel distribution challenges currently appear to be the areas attracting most thought and investment.
“Speed of delivery and accuracy of order fulfilment are being driven by the ever-increasing demands of the consumer, and the industry is striving not only to keep up with the rapid pace of change, but to also anticipate future trends,” he says.
He says that the challenge this pushes down through the supply chain is considerable.
“Manufacturers and suppliers of materials handling equipment such as ourselves have to ensure the promises their customers make are met, which means ensuring equipment is fit-for-purpose, well maintained, optimised for a particular task – and they are expected to deliver all of this and more at a competitive total cost of ownership,” says Barkworth.
Hyster’s Jurgen Emmenegger thinks that the biggest challenge for any narrow aisle application is always finding ways to lift the load capacity and dimensions to the height required in the available aisle width.
“Truck width plays a major part in this, as does mast and chassis construction,” he says. “ The patented Quad-Form and Tri-Form mast designs of the Hyster VNA truck require no tie-backs but still provide deflection resistance.
“This promotes greater residual capacities at height for any given truck width and means applications can achieve handling for the given capacity requirement in a narrower aisle.”
He says that VNA trucks can also help overcome space limitations in order-picking applications where aisles are often designed wider to allow two trucks to pass one another.
“With two lean Hyster VNA machines, aisle dimensions can still be reduced even though multiple trucks are operating in a single aisle,” he adds. The Hyster C1.0 – 1.5L VNA truck series can lift a maximum load of 1.5 tonnes to nearly 17 metres, depending on the model.
“This truck suits many different applications, but is particularly well suited for those handling difficult loads,” says Emmenegger. “In a VNA environment, the operator is up with the load being stored or retrieved, so optimum visibility is provided. This significantly reduces product damage and can improve operational efficiency over ‘man-down’ solutions.”
KP Snacks opts for a narrow approach
UK snack producer KP Snacks, due to a high demand for its products, upgraded its intralogistics processes at its Ashby-de-la-Zouch warehouse. In turn, the store’s pallet volume was significantly boosted.
The warehouse, located on the same site as the company’s major KP production facility, no longer offered the capacity needed to manage the increasing flow of stock that left the adjacent factory.
The company explored a number of options, including moving to a bigger space, before it settled on a solution that was designed and implemented by Flexi Warehouse Systems, the systems division of Narrow Aisle.
Originally, the layout of the store included standard pallet racking, which was worked by a combination of traditional counterbalanced forklifts and reach trucks.
However, with the new growth, the model was no longer space efficient. This meant it didn’t enable KP to achieve the throughput speeds it was looking for.
As a solution, Flexi recommended narrowing the aisles of the warehouse’s storage cube and replacing the pallet racking with an integrated two-deep storage system served by a fleet of Flexi StorMAX truck units. This is controlled by a specially developed WMS to optimise the first in last out and maximise pallet storage efficiency.
The technology, and two-deep system supplied at the site, enables KP Snacks to handle two pallets from the same side of each very narrow aisle, which doubles the capacity of each run of racking in the store.
At the site, a fleet of just five Flexi StorMAX trucks is all that is required to maintain the operation.
“The Flexi StorMAX system has allowed KP Snacks to maximise the capacity and efficiency of its existing adjacent to production storage facility,” said John Maguire, commercial director, Narrow Aisle. “Flexi Warehouse Systems was able to work with KP Snacks to re-design and re-configure its existing intralogistics infrastructure and, by using new technology and handling techniques, we have created a more cost effective operation with a very attractive pay-back period, and without the huge additional double handling and transport costs involved in an off-site distribution centre.”
“Flexi Warehouse Systems’ ability to offer a complete service from design through to supply and installation of all storage equipment allows food manufacturers with warehouse operations, such as KP Snacks, to modernise their existing facilities and make real operation costs saving in double quick time.”
Keeping pace
AGS Packaging Solutions Provider took delivery of a third Aisle-Master VNA articulated forklift for its European headquarters in Cork.
The new forklift has been taken on to keep pace with a rise in the volume of materials being handled at its manufacturing facility and distribution centre.
“We looked at a number of different brands and the warehouse staff were heavily involved in the decision making process,” says Noel Finnegan, operations manager. “We saw the Aisle-Master as comparable to a combination of a VNA and counterbalance truck, and a demo provided by our partners in Lift Truck Sales (Toyota) proved that it could do just what the manufacturers stated. It’s a great improvement on the previous system: the ability to pick from racking and load directly to HGVs in the yard is particularly beneficial as this eliminates double handling and really speeds up operations across the twelve hour shifts that the trucks put in.”
The new truck’s manoeuvrability enables them to move easily around the manufacturing areas to take semi-finished or finished products to and from the storage bays.
Most of the pallets at the site are not particularly heavy, but the 1.5t AM15 SHE electric powered models ensure that 1t loads can be easily lifted to a top bay height of 7m.
The vehicles are able to move freely and easily within the 1900mm aisle-widths that were configured for the old machines. “There is very limited turning space at the end of the aisles and I was initially worried about potential damage to the racking,” says warehouse manager Tomas Bernotas. “But this has not been the case at all – testament to the ease of operation of the trucks and the visibility they offer the drivers.”
Articulated strategy for Howard Tenens
Logistics company Howard Tenens invested in articulated forklifts from Narrow Aisle. Nine Flexi HiMAX trucks were ordered to be used at Howard Tenens’ facilities in Ashby de la Zouch and Sharpness.
The investment is part of a wider programme in which Howard Tenens has committed £42 million to the development of its property portfolio, logistics contracts and systems solutions as well as employee training, in the last three years.
“We have been working with Narrow Aisle for over a decade,” says Mike Jones, general manager, Howard Tenens Sharpness. “They were able to demonstrate flexibility within the 3-year contract that allows us to tender competitively for new business and, in turn, a significant saving was made by trading in older trucks.”
John Maguire, Narrow Aisle, said: “Howard Tenens has long realised the space and throughput efficiency benefits that Flexi articulated truck technology brings and we are delighted to be entering the second decade of our relationship with them.
“The latest additions to Howard Tenens fleet – the Flexi AC HiMAX – offer the perfect solution for high bay warehouses where fast throughput capability and narrow aisle storage density are required.”
The HiMAX trucks allow pallet loads to be stacked more than 12 metres high, and its HiVIS lift mast and specially developed integrated tilting and side shifting fork carriage eliminates mast deflection at the highest lift heights.
The trucks have triplex free lift masts which offer forward visibility. When handling pallet loads at the highest level, a high definition LCD CCTV system ensures Howard Tenens’ operators have a clear view.
The trucks also provide multi-shift availability because they have simple cassette battery changing and 6.5 hour charging technology that ensures the trucks are available around the clock if required.
The forklifts were provided on an inclusive contract rental package that means all planned maintenance, safety inspections and repairs are included in one fixed monthly rental charge.