Storage is a vital cog in the wheel of retail logistics, and getting it wrong can lead to disaster. Alexandra Leonards looks at its place in multi-channel operations, as well as its relationship with automation.
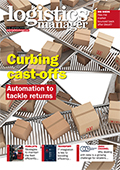
The growing dominion of multi-channel has altered what storage means for retail warehouses. While demand is shifting, storage is being applied to strategy and decision-making more so than ever before.
“Omni-channel retail is imposing a radical shift in logistics practices,” says Edward Hutchison, managing director of BITO Storage Systems. “When you drill down to the core of the challenges created by these changes, storage systems play a key role of an intralogistics strategy required for successful omni-channel fulfilment.”
At BITO, the demand for systems suited to online retail fulfilment is snowballing. But essentially, says Hutchison, customers want the same as those looking for conventional storage: reduced costs through picking equipment that uses less staff and costs.
The growth of omni-channel operations has boosted the general demand for large, industrial packaging.
“Less product is being sold through traditional retail, so less is now stored in shops and more stored in large centralised warehouses,” says Dale Paterson, managing director, Exporta Global. “This has increased demand for industrial packaging and changed the logistics of the supply chain.” To accommodate buyer demand, Exporta, which specialises in plastic pallets, collars and collapsible boxes, has had to adapt its products to fit in with multi-channel processes.
An absolutely vital feature of an omni-channel warehouse is flexibility. And so, retailers and their logistics partners are constantly looking for ways to maximise the fluidity of their operation.
“Flexibility is now a critical element in designing storage systems in respect of; modular design, the ability to re-profile layouts to meet ever-changing demands, a way to deliver short-term response and the ability to react “fast and large”,” says Dagan Hyde, from the Storage Equipment Manufacturers Association’s (SEMA).
Within a multi-channel warehouse, a single stock pool will quite often be delivered to all of the different channels. And this process is usually run by a sophisticated warehouse system.
“The physical storage complexities in combining the differing needs of the different channels in terms of speeds and order quantities can lead to a great deal of specialty around picking operations,” says Hutchison. “A facility will need to accommodate picking pallet and case loads as well as large numbers of single items– some of which may go direct to a customers’ home, others will go to the store for click and collect – along with replenishment stock.”
When designing or implementing storage systems for omni-channel operations, there are myriad factors to consider. For example, online order hit rates at pick slots are slower, and single items are usually ordered – so these types of orders require lots of travel. “There’s also complexity associated with mixed products going to the same consumer, so as the online retailer’s SKU range diversifies then a wider range of locations will be required,” says Hutchison.
For peak periods, which are always a big challenge for retailers and their logistics counterparts, customers want flexible storage systems which can be adapted and scaled up or down to meet the changes in volumes, and SKU ranges.
“Not only for fulfilment of online orders but, in many cases, handling the returns also – which has a counter cyclical peak to fulfilment,” adds Hutchison. “This will require a mix of systems for different pick rates – for example, adjustable shelving for slower moving items and carton flow racks, which offer a greater density of pick locations within a short distance.”
Boltless adjustable shelving is particularly well favoured, for the obvious reason that it can be quickly constructed or deconstructed during peak online periods.
“Modern storage systems have to cater to a much wider range of size, volume and shape of products,” says Hutchison. “There is a move away from individual specialists storing a lot of one type of product using straightforward storage systems, to warehouses storing a massive range of products for direct sale via e-commerce.”
Mike Alibone, of SSI Schaefer, the supplier and manufacturer of warehouse logistics systems, thinks that as well as flexibility, customers are seeking the ability to 100 per cent fulfil online orders.
“There is a dichotomy of practice when it comes to storing product destined for online customers,” says Alibone. “While some organisations will combine all their items into common stock for wholesale, retail and B2C e-com, others will store and manage stock for the latter channel in parallel, and separately to, products from the other channels to ensure that online customers receive orders as a priority over retail replenishment.”
Warehouse upgrade for Holland & Barrett
NBTy Europe, parent company of international chain Holland & Barrett, has seen significant growth in the popularity of the health food store’s online offering over the past few years.
And, up until recently, the company had been running its central distribution centre, located in Burton-on-Trent, entirely manually. The Staffordshire-based site runs an omni-channel operation – serving both its high street and online stores. The company was feeling the pressure of trying to fulfil the growing daily demand for both platforms.
NBTy looked to SSI Schaefer, the logistics and storage systems provider, to install an automated system at it’s existing facility.
SSI Schaefer made sure that Holland & Barrett had its own dedicated stock, held in a separate area within the facility, for its e-commerce customers. To adapt to the retailer’s ever-expanding range of goods, it also installed a two-tier mezzanine floor and mesh-decked pallet racking underneath it. The instalment boosted available storage space, enabling the company to store bulk and replenishment stock on pallets and on large cartons at ground floor level.
SSI Schaefer also installed carton live storage on the facility’s first floor –designed to accommodate the faster moving ‘A’ line goods. The top floor is now largely installed with standard regal 3000 shelving, and accommodates the medium and slow moving ‘b’ and ‘c’ line items.
Pallet gates were also installed on both of the floors. This enables the company to use rapid location replenishment from the bulk stock below, if needed. At the same time, a flexible zone picking system is operating on both of the floors – this allows shipping cartons to move solely to the zones that hold order-required goods on either floor.
“We are delighted to be working in partnership with SSI Schaefer – the new automated system provides a faster, more efficient and accurate operation in meeting our online requirements,” says Mark Kendrick, group distribution director, NBTy. “The system also offers us a scalable solution to our e-com enterprise, enabling us to choose the level of automation to compliment the current level of demand.
“The automated system operates at five to six times the current output of the manual operation, thereby removing the risk of meeting demand fulfilment,” says Kendrick.
Five key storage trends
Inclined shelving and carton live storage.
There appears to be a move away from conventional small parts storage, like longspan racking and shelving, towards inclined shelving and carton live storage.
According to BITO’s Edward Hutchison, this is mainly due to “inherent virtues of the carton live system” – for example faster picking, reduced manpower, improved space saving and organisation.
Drive-in racking
The availability of dense storage is growing, with more and more specialised options making their way into the market.
In particular, drive-in racking appears to be increasingly popular. This type of racking is chiefly suited to operations that don’t need to collect products in sequence. Many warehouse operators are using drive-in racking to store large stock volumes.
“This is particularly relevant for large volumes of the same line item, pressure-sensitive goods and unstable pallet loads,” says Hutchison.
Plastic
Exporta has noticed a strong movement towards plastic containers, pallets and storage solutions. The company’s managing director, Dale Paterson, says that many customers are choosing these options because plastic offers durability and is more hygienic than other traditional materials, like wood.
This trend is influenced by stricter regulations on hygiene, as well as businesses evaluating product life cycle to minimise costs, while at the same time increasing competitiveness.
Total solutions
Customers are constantly demanding more efficiency and lower costs from the storage systems market. And, according to SEMA’s Dagan Hyde, it is finding these solutions via the utilisation of materials; build programmes, automation and provision of a total solutions approach.
Driving faster access
The demand for faster access times is influencing the design of modern day storage systems.
“From the outset, many new storage installations are now ‘up spec’ed’ from what may at one time have been simple shelving or racking, to more pick efficient solutions involving a degree of simple mechanisation,” says Mike Alibone of SSI Schaefer.
These methods, used to speed up the process, have been influenced by changes to the market, like the growth of e-commerce, and other issues, like limitations to installation based on the constructional features of a building.
An increasingly visible relationship
A growing relationship between storage and automation is becoming increasingly visible in the warehouse. Exporta’s Dale Paterson would even go as far as to say that it is now necessary to design storage with automation in mind.
“The relationship is becoming more and more important as companies are exploring ways to become increasingly efficient,” says Dale Paterson, Exporta Global. “Design of modern storage systems need to include capability for automation, and traditional storage containers, need to be designed to be compliant with automated systems for maximum application options and efficiency.”
SEMA’s Dagan Hyde highlights move towards automation. “At the recent IMHX it was apparent that automation is a key feature of the storage industry’s future,” he says. “Buildings, storage, MHE will all need to evolve to meet the demands of a fully integrated, flexible automated storage system.
“The future holds some exciting opportunities for those companies who embrace these new developments.”
SSI Schaefer’s Mike Alibone says that the ease at which a storage system can be adapted to an automation system really depends upon the level of automation that is actually being applied to a warehouse operation.
“Choosing a storage solution which is based on a fully Automated Storage and Retrieval System (ASRS) may appear as a costly investment initially but the long-term savings in, say, moving from a large, manual labour-intensive system to a dark store for pallets, totes or cartons, can be realised as a substantial return on investment through considerably reduced labour and energy costs,” says Alibone. “If, however, the physical nature of the stored product changes appreciably, it is more difficult to adapt such a storage system to accommodate the change.”
Traditionally, ASRSs are integrated into total internal logistics materials flow systems. “So projects will often involve multiple products such as pallet racking, dynamic storage, pallets, bins, containers, etc.,” says Edward Hutchison, BITO Storage Systems. “Seeking a supplier that can offer (and, ideally, manufacture itself) all of these elements will make it easier when it comes to designing a complete solution that fits together precisely and meets the requirements of the application.”
Warehouses that operate with low-level automation, or mechanisation, including pick to belt or roller conveyors, pick by light, and voice-picking, can all be easily and readily adapted to accommodate automation.
Bin storage is one example of a system that works well with automation. These systems are used where SKUs are stored in individual bins or trays, and are a common way of handling goods-to-person picking for small items that only need a low quantity. This storage format can deliver better use of warehouse volume in comparison to manual picking, as well as reduce access time.
“A supplier that can offer a comprehensive choice of uprights and beams for racking will be better able to adapt a storage system design to meet precisely both a customer’s initial and anticipated load requirements,” says Hutchison. “To facilitate a wide range of location configurations for an order picking operation, pallet racking systems should offer a variety of different upright heights to accommodate a range of pallet loads as well as beams constructed for a range of bay widths.”
If, for example, this racking installation needs to be upgraded into an automated storage system, or integrated into a total logistics system, a number of punched profiles can be incorporated into the racking design to pre-empt the future installation of conveyors and roller tracks.
“Racking, however, is just one element of an automated storage system,” says Hutchison. “Pallets or bins and containers are also involved.”
He says one of the big challenges when designing containers is finding a way for them to be customised at no extra cost to suit a greater variety of SKUs. To be used across different environments, containers have to be versatile.
Believe it or not, one of the newest trends for containers is low noise design for travel on automated conveyors.
“An increasingly important point for containers used in automated picking systems is the amount of noise they generate,” says Hutchison.
“Using a container, which maintains a flat base thanks its thicker plastic, will significantly reduce the amount of noise in an automated warehouse,” adds Hutchison.