The past few years have seen significant changes in loading bay technology, making it ever more important to get the choices right if the full benefits are to be reaped.
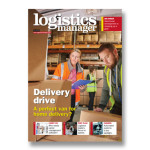
It only takes one look at a modern warehouse to see that it is very different from one built 20 years ago – and a big part of that difference is the number of doors.
Goods are no longer stored for extended periods, throughput is high and to accommodate that takes lots of doors.
Tom Langley, projects director at Hörmann, says: “We’ve recently seen considerable expansion in the big shed market, which in turn has led to a surge in demand for loading bay technology across the industry as a whole.” However, Langley also notes that there has been a significant change with the shift towards smaller, regional warehouses alongside large central hubs.
“There’s also an increase in demand for adaptability within warehouse design. Many companies now use a variety of vehicles for their operations, all with different requirements in terms of loading bays. Manufacturers need to be able to provide a flexible approach for customers, ensuring that the best possible products and control systems are selected to fit in with their specific processes and procedures.”
He points out that the shift in demand towards smaller loading bay sites is primarily down to the growth of e-commerce, which is forcing retailers to develop new ways to satisfy consumer needs. Companies are now opting for multiple smaller, more localised warehouses that are capable of faster turnarounds for delivery to thousands of homes, as opposed to the traditional larger hubs.
“This new style of hub has been designed to provide a fast turnaround on goods and use a range of vehicles, including multiple smaller vans. For this reason we’re seeing an increase in demand for smaller doors and loading bays as well as our MLS and HTLV dock levellers suitable for vans. These sites also tend to have a far more doors, for instance we recently supplied 101 doors for a new TNT depot and sortation hub in Swindon,” says Langley.
Consumer expectations are also much higher now than they were only a few years ago, with people demanding faster deliveries and convenience at a lower cost. Retailers require loading bay equipment and technology that will allow for large quantities of goods to flow very quickly both into and out of their warehouses.
Reducing the carbon footprint of a warehouse operation is increasingly important for companies. Not only is there the environmental aspect, there is also money to be saved.
“At Hörmann we invest a lot in research and development to ensure our products benefit from the latest technological advancements, whether that brings faster or more thermally efficient products,” says Langley. “The loading bay is one area in particular where energy loss can easily be minimised. Telescopic lips allow the dock leveller to sit behind an insulated door, while the use of inflatable curtains provides a seal around the sides of the vehicle, a solution commonly used in frozen or chilled food environments and low carbon warehouses.”
Safety on the loading dock is a perennial concern and it’s important to ensure that the products supplied are suitable for the site and vehicles in use there.
“Visual cues are essential for both drivers and loading bay staff. Traffic lights, particularly those with arrows to aid continental drivers, mounted both externally and internally of the loading bay door, can be used to signal when it is safe to load, unload and move the vehicle,” says Langley. “By ensuring processes happen in the correct order, not only are accidents less likely, unloading times can also be reduced, thereby increasing the efficiency of operations.
“Most of the latest developments in loading bay safety are a combination of technology and process. At Hörmann we’ve seen an increase in demand for our key chute system, which involves the keys being hooked onto the raised door, preventing the driver from pulling away early. We are also about to release our newly developed vehicle restraint system. Systems such as these complement and reinforce the practices in place at many warehouses, where operations take place in a specific order to reduce the risk of accidents,” says Langley.
Boyes goes double deck
Value retailer Boyes has installed 6.5 tonne double deck lift and three dock levellers at one of its North Yorkshire distribution centres.
As part of the project at the Havers Hill site in Eastfield, an extension has been built that links two warehouses together – creating a central marshalling and loading area, which also provides additional storage space. It chose Transdek to install three dock leveller pods to the front of the new building to increase loading capabilities.
Alongside the fully clad levellers, one of Transdek’s surface mounted 6.5t double deck lifts has also been installed to facilitate increased delivery efficiency from Boyes’ growing fleet of double deck trailers, which can reduce transport costs by up to 40 per cent. The lift can accommodate up to 12 roll cages, each with a 550kg capacity and provides fast loading speeds to maximise trailer use.
One of the challenges faced by Transdek’s team during installation was a significant right to left yard slope. The company designed and manufactured bespoke wheel ramps to correct the gradient and allow level loading for all types of vehicle trailers.
“Over the last four years, Transdek’s V2G lifts have significantly enhanced our warehouse productivity and increased logistics efficiency,” said Kevin Marson, maintenance manager at Boyes.
“With the new dock levellers and integrated double deck lift we are now in a position to handle our expanding fleet of double deck trailers, as well as all types of distribution vehicles, much more effectively.”
Phase two of the project, planned for June, will involve Transdek constructing a mezzanine floor extension at the site, which will operate as a holding area to provide increased storage facilities.
Upside down solution
Sara LBS solved a Sussex vegetable grower’s problems by creating a roller door that works upside down.
The door was one of two supplied by sara LBS for the packing house. The requirement was for a door with cut-outs to accommodate a track conveyor that transports plants into and out of a large growing room. This was an overhead conveyor which served a mezzanine many metres above floor level. Because it was so near the roof the door’s drum had to be installed below the conveyor and the door had to work upside down.
The door needed to be 4,900mm wide by and have insulated sectional profiles. The application required the door to be operated two or three times a day, opening to let wide loads pass, and to provide a working life of seven to ten years.
For the Chichester project sara LBS’s heavy duty security roller shutter doors, which are based on hollow galvanised steel curtains, were filled with polyurethane insulation to reduce energy losses.
Sara’s Nick Cox says: “We worked through all the details like opening and closing speed, colour and weather seals with the client to come up with the ideal bespoke solution.
“Because the door is at a high level where no personnel ever go during normal production operations, we were able to dispense with the usual safety edge. We had to fit in with the building’s tight construction schedule.
“In fact, the doors were not ordered until late in the project, so we had to work to a very tight schedule and complete all our work in only six weeks.”
New dock leveller for Heinz
Heinz has chosen to improve the loading bay safety systems at its UK based manufacturing facility in Kitt Green, near Wigan, using a new dock leveller and platform from Thorworld Industries.
The factory produces more than one billion cans of product a year.
Graham Hollinghurst, project manager at the Kraft Heinz Company says: “We always put safety first at the Kitt Green facility, so to ensure our equipment was completely up-to-date, we started to research a new loading bay solution that would provide an even safer way for powered pallet trucks and their operators to access the rear of vehicles delivering dry and chilled ingredients.
“We also needed a better access solution for operators to load empty stillages, so were very keen to see any options out there that were capable of meeting all of our facility’s needs.”
Thorworld’s engineers created a bespoke modular scheme to give access to shipping containers. A maximum incline of six degrees was specified to suit the powered pallet trucks in use on site. The limited space available required an L-Shaped ramp / platform combination with a suitable turning area at the top of the ramp. Operator access to the dock leveller was provided via a set of access steps and a collapsible framed dock shelter included to prevent weather ingress.
The new dock leveller and platform fits within a wider set of improvements Heinz has implemented at its Kitt Green site. Additions such as a separate mechanism to prevent HGVs from moving during loading, and the installation of a ‘portal frame building’ to house the new leveller and ramp have also been added – protecting both operatives and product lines.
Heinz has also replaced a 10,000kg dock leveller with new Thorworld apparatus.
John Meale, managing director at Thorworld, said: “It’s terrific to hear that a company as reputable and internationally renowned as Heinz has chosen to invest in our loading bay apparatus, in not one, but two areas of its UK operation.”