In all sectors of industry and commerce, the need to ship orders quickly and accurately has seen a rise in companies looking at ways to improve their order picking processes for efficiency and speed. Lisa Townshend reports.
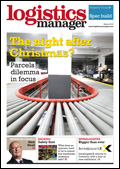
The growth of e-commerce has been a double-edged sword as consumer choice and flexibility increases, but with it comes the challenge for distribution centres to keep pace with expectations for faster and more accurate delivery.
According to a survey produced by YouGov on behalf of Honeywell, nine in ten distribution centre operators expect to adopt new mobile devices and voice-direction technology in the next five years to help them to meet the challenges brought on by the move to e-commerce.
The survey canvassed IT decision-makers across the US, UK, France and Germany, and showed that mobile solutions are expected to increase in adoption over the next five years, driven by the need for increased order fulfilment accuracy and improved customer service.
One major issue for distribution centres is mispicks. The survey found that the average global cost of one picking error is $59, equating to an average of more than $400,000 annually on mispicks to a distribution centre. Costs vary by country, with the cost of a mispick in the US ranking highest ($67), followed by France ($60), Germany ($52), and the UK ($50).
The issues of e-commerce and high-quality consistent and efficient order fulfilment go beyond the usual sectors – retail, tech, fashion and so on. Sectors such as automotive, health & pharmaceutical and energy share the same concerns, but with the added issue that any loss of quality could either impact on the safety of a finished product or threaten the health of patients around the world.
The recent Logistics Manager State of the Market survey found that 79.5 per cent of companies in the automotive, energy, utilities & transport and health & pharmaceuticals sectors were looking to invest in infrastructure such as scanners, mobile technology and voice picking in the next six months. This shows a real need identified in these sectors for reliable and efficient systems.
Andrew Southgate, general manager at Lucas Systems, highlights the necessity for traceability. He says: “One key trend affecting many industries is product traceability, especially in areas where consumer health and safety is concerned. For example, in food, beverage and pharma it is increasingly important for distributors to know which customers are receiving a specific lot and/or batch of a given product in the event of a product recall. In automotive and other industries, manufacturers and distributors are required to track item-level serial numbers for warranty and recall information.
“As regulatory demands to capture and track this information have increased, distributors have had to adapt their processes and add new data capture steps, often resulting in the creation of manual workarounds that add cost and time. Using mobile work execution solutions in picking can help address these product traceability issues while simultaneously improving the efficiency and accuracy of picking far beyond what is typically possible with traditional WMS-driven RF or voice workflows.”
Citing an example, Southgate spoke about a distributor of medical devices, who had been using RF for picking, but their existing picking system did not support capture of serial numbers at the point of pick. As a result, they had a separate post-pick process for entering the serial numbers for all products that required serial tracking. When they implemented the Lucas mobile work execution solution, Lucas also provided voice-directed applications that allowed users to scan serial numbers as they picked the items, eliminating the post–pick process. This resulted in manpower savings above and beyond the productivity gains they realised using this solution.
Michiel Veenman, Swisslog’s industry segment leader for pharmaceutical, believes that automation is ideal for the future of an ever-more stringent industry. Veenman says: “Automated processes, such as goods-to-person picking, automatically ensures that the correct product or batch is presented to the operator. A well-designed workstation ensures that the operator can only access the right product, allowing for pharma-specific regulations such as line-clearance to be implemented.
“In the near future, it’s also likely that this will be taken one step further, replacing human involvement with robots, eliminating the possibility for human error. Some have already used this for simple processes, the expected push in the development of even smarter robotic applications for logistics makes this an area for growth.”
Eric Carter, solutions architect at Indigo Software, feels that there is less influence by profit margins in the pharmaceutical sector. “In the pharmaceutical sector profit margins are a lot higher, and manufacturers have the scope to invest in the latest technology to meet their legislative requirements for full traceability. They are investing in advanced picking and labelling technology to enable full lot control and accurate picking using barcode scanning, voice and RFID. In addition to improving picking accuracy, it makes the collection of product data that supports the quality systems in these businesses almost seamless and guarantees audit trail reliability.
“Having a reliable audit trail is imperative when dealing with FDA type regulations. Picking systems can be set up to capture an operative’s digital signature when stock is moved around to different locations and store the movements associated with each user on a database.”
Carter believes the reverse is true when looking at automotive. “Manufacturers of automotive components face some unique challenges, which potentially limit their ability to use the latest fully automated picking technologies. From experience, although these suppliers are providing stock directly to the car maker’s assembly lines, which requires the highest levels of accuracy and speed, they are often working from paper based systems.
“Car assembly is pre-planned with military precision and the right components need to be provided at the right time. This places a huge responsibility onto the supplier to ensure they pick exactly the right items and that shipments are double and triple checked for accuracy.
“Yet although the cost of getting it wrong is unthinkable and means production line disruption, automotive component manufacturers are often not using automated picking technologies. This is because the margins on many of the products are low, and they believe the ROI achievable is not strong enough. They think it’s cheaper to check quality into a process with two or three levels of quality control rather than build it in using advanced technology. But where they have made the investment into order picking automation, the benefits are there.”
James Sharples, managing director at Swisslog, points to the impact of stopping a production line; ensuring picking is highly accurate. “In the automotive sector, the focus is on getting the right part to the line at the right time and in the right sequence. This means that thousands of parts have to be picked and delivered to a production line; an environment which demands as high levels of accuracy as anything you’ll find – no-one wants to stop an automotive line because the part is delivered late.”
Sharples sees the industry’s use of AGVs as an example of how automation can enhance accuracy. “Generally huge 3PL operations are used to manage these supply chains, and have often relied on a lot of manual handling. Automation increases productivity and maintains accuracy while the impact on inbound logistics, storage and picking can be seen in many car plants, as is the increasing use of AGVs for delivery to line.”
Case study: First Gebhardt-ECS Storebiter shuttle system for UK
Gebhardt-ECS was appointed to implement a dynamic multi-level storage and picking system at the Lear Corporation factory in Coventry.
Due to the range of designs and optional items required for seats for premium car brands currently, the conventional mezzanine-equipped storage and picking system at the factory had become inefficient and expensive to operate. In addition, more space was needed to store the required number of items.
The solution includes the use of 14 Storebiter MLS multi-level shuttles to handle 18,000 storage trays. Each shuttle can access four levels of trays, which increases the quantity of trays that can be stored compared to conventional single-level shuttles.
The project, which includes mezzanines, tote conveyors and a Gebhardt Storeware warehouse control system, was due to be operational by the end of 2015.
Case study: Just what the e-com ordered
Resulting from strong growth in online sales, Holland & Barrett needed a separate operation to process internet orders. The company contracted Pcdata to implement a fast and scalable order pick system based on Pick to Light and PickCarts.
The decision was made to set up a separate Internet operation, resulting in a 30,000 sq ft expansion of the Beverwijk distribution centre in the Netherlands, with a mezzanine area of 17,000 sq ft.
Pick-to-light is used in the process flow fast mover area. Pre-labelled shipping boxes are placed on the conveyor. The box barcode is scanned, linking the box to the associated Internet order. The conveyor transports the boxes to the correct zones, where it is pushed out for picking. Each zone display will show the number of products the picker needs to pick for that particular zone. In addition, pick-to-light displays will light up, and show how many pieces need to be picked at that location. Each pick is confirmed and the pick-to-light display turns off. When all displays in a zone have been pushed, the operator moves the box back onto the main conveyor and it is moved to the next zone.
The slow mover process uses five Pcdata Pick Carts which each have the capacity to hold 20 boxes. Scanning the barcode links that box to one of the locations on the cart. Each location on the cart is equipped with a put to light display. Once the cart is loaded, the touchscreen tablet mounted on the cart informs the operator which location to go to. The location is confirmed with a scan, lighting up the displays on the car, which indicate the number of items from that product location that need to be placed in each box. As picking is completed, the operator puts the boxes on the conveyor that transports them to the packing tables on the ground floor.
Logistics manager Vincent Schippers of Holland & Barrett says: “The whole project went according to plan, thanks to thorough and realistic time management.”