The order picking function has come under greater pressure than ever before with change being driven by the growth of online retail. Alex Whiteman examines some of the challenges.
Retail has shifted dramatically in past decade. The impact of this sea change has been felt along the entire supply chain. Omni-channel and online retail has required retailers to make efficiency gains. And these gains have put pressure on picking systems.
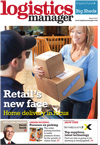
Voiteq director Anton du Preez highlights three key changes in retail that impact picking: omni-channel, the growth of convenience stores and on-going “lean” initiatives in stores and supply chains.
“Omni-channel requires piece picking, ideally pick-and-pack, of a large number of small orders to very specific deadlines, such as next day delivery,” he says. “Warehouses that are setup for large store order fulfilment need some fundamental layout changes, resources and processes. Accuracy, speed and scalability for peak periods are critical for good omni-channel service.”
The growth of convenience stores combined with “lean” initiatives aimed at reducing inventory in the supply chain, has impacted the retail and manufacturing supply chain, says du Preez.
“For large stores, retailers want to convert some of their back-of-store storage into shop-front floor space, and convenience stores tend to have limited storage from the start,” he adds. “Since this means there is less buffer stock in the network, retailers and manufacturers are having to make smaller, more frequent deliveries.
“This in turn requires retailers to have more put-to-store (pick-by-line) picking with smaller quantities and manufacturers to deliver more store-friendly, mixed pallets that can easily be broken down and used to directly fill store orders. This is driving a significant growth in case picking by manufacturers and each retailer has slightly different requirements for their pallet configuration.”
Noel Blake, account director at TGW agrees that it is hard not to notice the ever-increasing pace in retail.
“The idea of pick today, ship in two seems long gone,” he says. “Even the largest retailers are demanding more frequent and thereby, smaller replenishment volumes. What were once pallet quantities, are now case and what were once case quantities, are now piece picks.”
Vocollect regional director Darrel Williams highlights the fact that accuracy together with efficiency is paramount in meeting these demands, especially with retailers having to send many smaller orders going to multiple destinations, including directly to the consumer.
Automation is being applied to certain online retail product profiles, says Bito Storage Systems’ managing director Edward Hutchinson – particularly when volumes have reached a level where only automation can ensure the consistent accuracy required to achieve the100 per cent service levels demanded by online shoppers. However, the characteristics of picking singles means that many online retail fulfilment operations remain largely manual processes.
“Many multichannel retailers are now picking store orders and online from the same stock rather than having siloed pick faces or facilities for each channel,” he says. “They are using more sophisticated demand planning and warehouse management systems to manage the centralised pool of stock for the different channels. Once the stock is retrieved it can then be sorted and packed to according to the channel.”
Regardless of the product handled, or the picking method and equipment used, Stefano Sangalli, publishing divisional director at Ceva in Italy, says locating product according to the frequency of picks should be a fundamental feature of the design of an order picking system.
“The fastest-moving product should be stocked as close to the pick point as possible, and at those levels that are easiest to pick from,” he says. “Slotting in fixed picking locations needs regular review to maintain high levels of productivity. The frequency of review will depend upon product life cycles and seasonality.”
Technological evolution
On-going technological evolution has improved efficiency for workers, but there is still plenty of room for discussion over the most appropriate system for a particular application.
“To be successful in order picking you first have to understand the process, ascertain what is and what isn’t necessary, and then eliminate any ‘dead time’ while still meeting the business need,” says Vocollect’s Darrel Williams.
“In today’s environment this is made all the more difficult by the ever-changing demand from our customers. New product, new sizes, promotions, pick more, pick less – it’s a brave manager who can accurately predict what is needed and when.
For Williams, picking efficiency is all about enabling the user to do the job with no distraction, without any unnecessary and time-consuming activity, and making every action a value added step.
“This is where voice technology comes into its own – faster and more accurate than paper picking and scanning,” he says. “The worker receives just-in-time instruction while on the move, and can confirm instructions while actually doing the job they are employed to do, removing the need to stop to read, tick, point, scan or even place a scanner to one side while picking a heavy item with both hands. “
Keith Philips, CEO of Voxware, reckons that the growth of cloud-based technologies has been critical in furthering its voice-based picking systems.
“Cloud technology makes implementation a far simpler process,” says Philips. “Alongside this there is a reduction in costs, which is felt by both user and provider long after implementation, with system support and maintenance no longer hindering the user’s IT department.”
But the ability to integrate warehouse systems is an important step forward, says Anton du Preez.
“Better integration between voice devices, screens and scanner to support “multi-modal” processes is a recent advancement that has brought about an improvement in systems,” says du Preez. “Ruggedised noise-cancelling wireless headsets that improve user comfort and reduce costs have also been a positive step forward.”
Jeffrey Slevin managing director of Lucas Systems, says that the two categories of technology that are having the greatest impact on order picking are mobile computing and automation, noting that in many ways these trends are complimentary.
“Despite increasing use of automation, there is a point where additional automation cannot be justified and manual, hands-on steps are essential,” he says. “And that’s where mobile computing is having its impact: wherever you need people to touch and move product. New mobile computing technologies are making those hands-on processes smarter, easier and better.”
There has been a huge amount of interest in the use of RFID in the warehouse, but there are doubts about the degree to which it will ever be used.
For Rob Hodgson, Access Group’s divisional sales leader – supply chain, there is no doubt.
“RFID will not find a mass market home in the warehouse. In other areas, certainly,” he says. “But in the warehouse there is not the margin to incorporate the cost.”
What does seem to be agreed on is that there is a need for hardware to mimic the speed of development that software systems are experiencing.
“Hardware technology in the consumer space develops at a much more rapid rate than its development in the industrial space,” says Philips. “Industrial hardware could do with speeding up its development.”
Case Study
Picking a ‘mobile workforce’
EU expansion has diversified the workforce of the UK. Warehouses have seen a rising number of workers for whom English is not their first language, and in instances English is a language with which they are not fluent. Rather than hinder operations, it has accelerated technological development, which in turn has had a positive effect on efficiency as a whole – and advanced employee training.
Jon Hall, group operations director at Belgravium Technologies (parent company of TouchStar) says that companies using traditional picking processes rely on English language instructions given on paper or via a hand held terminal. These companies, he says, will need to be very selective about who they hire to ensure the individual’s English language is of a high enough level to understand the instructions or face a high risk of error. However, Hall notes that both light picking and voice picking systems can negate these barriers significantly.
“Voice picking allows the worker to be given clear, audible instructions in the worker’s native language and then asks the worker to give voice responses to confirm what they are doing at every step in the picking processes, again in their native language,” he says. “This not only removes the language barrier, it also helps to eliminate human error resulting in a pick rate accuracy of over 99 per cent.”
He also notes that light picking systems also have the ability to remove language barriers as they tell the mobile worker what to pick based on lights being illuminated in picking bays. However, Hall says that this technology is generally most effective where large numbers of small items are being picked in a small area, rather than for a large warehouse or distribution centres.
In response to an increasing number of languages, Ceva simplified its operating procedures, and improved the user interface with the warehouse management system, according to Stefano Sangalli, publishing divisional director, Ceva Logistics Italy.
Anton du Preez notes that a multi-language warehouse is neither a new phenomenon nor one limited to the UK. While he notes that an influx of non-native speakers creates challenges for paper and screen-based picking systems – because these typically present a lot of text that the picker needs to read and understand before they can carry out their job and translating these are not easy – voice solutions present information in a simple step-by-step manner that alleviates the need for fluency in the national tongue.
“We provide systems that work well regardless of accent or dialect and present information in this simple, step-by-step manner,” says du Preez. “Users can even speak in their native tongue if the business permits. If you think about it, we all learned to speak before we learned to read and write.”
Darrel Williams says that language was often a barrier in any workplace irrespective of the technology or picking solution, however all that has changed.
“It’s not a secret that voice systems have raised the performance bar and the performance expectations of warehouses in every sector, and at board level, leaders are now keenly aware that the logistics operation can make or break a business,” he says.
According to Williams, companies look to provide solutions that really enable and empower their workforce, irrespective of its make-up, to meet the exacting demands of their industry.
It is not uncommon for several languages to be used in a single warehouse, all the while meeting or exceeding the performance levels that the business has come to expect.
“Technology such as Honeywell Vocollect Voice Solutions does exactly this by lifting each and every worker to the same high performance level,” he says.
Case study
Connect finds its voice
Connect Distribution provides spare parts for domestic appliances to both trade and consumer buyers. It has more than 1,000,000 product lines that go through its six-acre national distribution centre in Birmingham, which processes over 180,000 orders per month. The company increased the size of its NDC staff. As such, it needed to improve productivity and accuracy across its order fulfilment.
Previously, the company had used a label-based picking method, which slowed the operation. The method was also prone to human error and required additional checking at the packing stage.
Looking for a new solution, Connect’s director of NDC operations Iain Priestley first commissioned Voiteq to run a trial of its own VoiceMan and Vocollect’s voice technology in September 2009.
Following this trial, Connect decided to implement the voice solution into its conveyor picking zones. The firm replaced the existing label-based picking method in 2010, and in the summer of 2012 extended voice into its put-away operation.
Connect wanted to continue to make use of its existing legacy WMS and its functionality.
Selecting VoiceMan middleware from Voiteq, enabled this. The solution links the WMS at the back-end to the voice user on the DC floor. The VoiceMan solution also provides a tool that allows Connect to view exactly what’s going on with its team at any one time.
Voiteq selected the Vocollect Talkman T5 computers and SR20 headset for a hands and eyes free operation.
In addition, Connect needed label printing to be combined with the voice offering, as each customer order is individually labelled for identification and traceability. Zebra’s QL320 printer was chosen to work in combination with voice and is worn over the shoulder to maintain the freedom that voice offers.
Since deploying voice across its picking zones, Connect has added the VoiceMan Putaway module, allowing the company to use voice beyond picking.
“In year one, we achieved annual productivity gains of between 25 to 40 per cent,” said Priestly. “In year two, we are seeing an 85 per cent improvement in productivity.”
Since installing the system, the company has experienced a 76 per cent gain in accuracy.
Not forgetting that Connect Distribution also needed a better way of managing its labour force, the voice system interacts directly with its custom built incentive software, BGEN, and provides supervisors with real-time information on performance and helps identify whether there are any training needs required.
The improvements enabled the company to obtain a return on investment in just 12 months.