How can operators guarantee their warehouse storage is safe? Well, a good start would be a thorough design, an eye for quality and encouraging a safety culture. Alex Leonards reports…
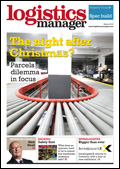
What is the most important factor in its safety? The quality of the racking itself, says Edward Hutchison, managing director of BITO Storage Systems. “Higher quality racking will be better at maintaining its structural integrity – a key consideration in a very price competitive market.”
Naturally, warehouse operators look for the right price, as well as efficiency and safety. But is low-priced racking really a good investment long term? Perhaps not when safety is being compromised by cheap products creeping into the market.
These cut-rate products can generate difficulties for warehouse operators, as you can’t always tell which materials they are built with. This is because they don’t have a traditional audit trail.
“At BITO, we provide a guarantee on our products,” says Hutchison. “If there is a failure, for example some form of white oxide that builds up on a pre-galvanised sheet, we can then trace back all the components that have been made with that batch of pre-galvanised sheet and therefore, go to site to inspect it or, in the worst case scenario, we would carry out a re-installation. “We haven’t had to do that, but this is the difference,” says Hutchison.
Steve Cowen, chairman of the Storage Equipment Manufacturers’ Association (SEMA), also has concerns about low-priced storage.
“Some treat racking and shelving as a commodity and look for little other than the lowest price,” he says. “This is a rather short-sighted approach in that a storage system is a safety-critical piece of equipment.
“In the event of a serious accident a collapse can, in the worst case, put the installation out of commission for several weeks, as well as potentially injuring staff.”
This can have a significant financial impact on a business.
“Not all companies have duplicate facilities, nor the spare capacity that runs alongside to enable them to fill the gap caused by such an eventuality,” says Cowen. “As some wise man said, ‘you think safety is expensive – try having an accident.’”
There are a number of potential dangers associated with racking in the warehouse. Pallets falling out of racking from behind, and then dropping down to the aisle below, is one unwelcome hazard. To prevent this, Hutchison suggests fitting anti-collapse wire-mesh cladding, as well as backstops which prevent pallets from being pushed too far back.
Mike Alibone, SSI Schaefer’s business development and marketing manager, says that plastic “wrap-round” upright protectors are becoming increasingly popular. In fact, they’re often viewed by operators as an absolute solution.
“They can give a false sense of security as they can hide damage and make inspection more difficult,” he says. “Supplying racking and shelving protection devices is arguably the wrong solution, but perhaps a necessary evil.
“In our view, prevention is better than the cure.”
Schaefer identifies thorough planning and design as one of the best ways to protect racking, and therefore ensure safety. Alibone says that a way to guarantee safety is to design the installation so that the correct goods are being stored in the right manner, and to ensure there is sufficient space to carry out the operation safely. He also warned against improvising or “making do”.
Hutchison points out that BITO products have a guarantee on their dynamic systems. He also reckons that live storage systems are one of the best examples of how a design can promote both functional efficiency and safety at the same time in a warehouse. And live storage is becoming more prevalent in the market.
“This increasingly popular order picking solution combines the virtues of dense, FIFO storage – up to 60 per cent higher than conventional racking – with improved pick cycle rates and at a much lower cost than full blown automated storage and retrieval systems,” adds Hutchison.
As well as making the most of space, and being cost efficient, this design has health and safety at its core. Live storage lanes are loaded with pallets from the aisle on the replenishment side (back), while items are picked on the other side (front). This separates loading and the use of lift trucks from the “more pedestrian function of order picking”.
“This is not just safe, it makes live more convenient and obstruction free for both replenishers and pickers,” adds Hutchison. “Furthermore, because goods can be arranged in order-oriented pallet grouping in the live storage lanes for dispatch, this will make loading more efficient – thus reducing lorry waiting times and the potential for accidents in a high risk area.”
Bolted frame construction is another safety conscious design. It allows easier exchange of damaged components, “ensuring structural integrity is maintained”.
“For the beams, a boltless system provides rapid adaptability – solid safety hooks secured by a 90 degree turn will prevent them being accidentally lifted,” says Hutchison. “This system not only provides a high load capacity but also excellent lengthwise rigidity for the racking system.”
SEMA’s Steve Cowen looks beyond warehouse design or products for safety. He thinks that racking collapse, and the prosecution associated with it, are simple to avoid when there is a “safety culture” implemented in the warehouse. He believes that racking is safest when correct protocols for inspection, maintenance and repair exist.
“It’s the duty of an employer to manage risk to life and property, who must always demonstrate a safe system of work,” he says. “As the law stands, investment in terms of money, time and trouble must ‘grossly outweigh’ the risk, not balance it.”
According to Cowen, the legal responsibility given to warehouse operators to design, construct, inspect and properly maintain storage systems has increased significantly. Since last month, new sentencing council guidelines have come into play. This means companies might face bigger fines and more individuals may face custodial sentences.
Creating this all-important “culture of safety” among staff members can also mean maintaining acceptable standards of housekeeping. Of course, it doesn’t take a genius to know slippery floors or blocked aisles will result in more damage. But being more aware about little things like this can make all the difference when it comes to safety.
Regular inspections play an important role in ensuring the continued safety of racking. Companies like The Rack Group offer inspection services as well as repairs. And arguably, the lull after Christmas is the best time for an inspection.
TRENDS: The e-tail effect
High street fashion and retail brands are now turning to the logistics and handling sector for guidance in adopting new strategies to support the seismic shift in the retail sector, says Paul Davies, sales and marketing director at Link 51.
It is unsurprising then that in the warehouse storage market, there is a clear shift towards e-tail friendly systems.
“Many orders that BITO has fulfilled of late have been to provide systems to meet the particular needs of online retail fulfilment,” says BITO managing director Edward Hutchison. “The level of anywhere, anyhow fulfilment demanded by omni-channel retailers requires storage and order picking systems that can facilitate rapid and accurate deliveries for store replenishment, click and collect and the direct to home channel.”
Peak periods can be a challenge for warehouses catering to online retail.
“It is clear why companies are seeking flexible picking systems that can be scaled up or down to accommodate large variances in volumes, SKU range and SKU profile – not only for fulfilment of online orders but, in many cases, handling the returns also – which has a counter cyclical peak to fulfilment, says Hutchison. “This will require a mix of systems for different pick rates – for example, adjustable shelving for slower moving items and carton flow racks, which offer a greater density of pick locations within a short distance.
“Boltless versions of these systems are popular because they can be quickly and easily configured or reconfigured to handle the large peaks experienced in the online sector.”
TRENDS: Sprinkler-friendly
Sprinkler friendly shelving is also becoming more prevalent, as warehouse operators are looking to meet the requirements of insurance companies.
“Recent developments revolve around the increasingly common use of racking and shelving as self-supporting multi-tier picking systems (‘pick-towers’) instead of purpose-built mezzanines,” says SSI Schaefer’s Mike Alibone.
TRENDS: Euro pallets
Surprisingly, there is now some small growth in the use of Euro-sized pallets and containers here in the UK.
“Not so long ago a Euro pallet was a rare sight and, while they still constitute a minority within the overall UK pallet population, their numbers are growing and increasingly companies need to plan for the handling of these pallets as well as a traditional pallets,” says Hutchison. “Similarly for small part containers, companies need to cater for the Euro containers, in particular accommodating their footprint.
“For this reason we are seeing a big move from traditional one metre wide shelving towards widths of 1300 mm because that will accommodate two lots of Euro containers 600 mm wide or three lots of 400 mm wide containers.”
In BITO’s German manufacturing facility, it is producing more 1300mm wide shelves than one metre shelves to accommodate these Euro containers. But, this is of course a very new trend for the UK.
TRENDS: Getting higher
The growing height of warehouses as another trend. The growth is pushed by companies wanting to exploit all available space. “Hence the increase in rack height for reach truck and VNA operation,” says Alibone. “Fifteen years ago a speculatively built warehouse over 10m was unusual; nowadays 15m is normal.
“This has brought with it some problems as the load carrying specification of the warehouse floor has – by and large – not changed to reflect this increase in height and hence, storage levels.”
Narrow Aisle is also growing in height, today 11 metres is not abnormal.
TRENDS: Live storage
The use of traditional small parts storage products, like shelving and longspan racking, is becoming less common, says BITO’s Hutchison. There has now been a move towards inclined shelving and carton live storage. “This is due in large part to the inherent virtues of the carton live system, ie faster picking and reduced manpower as well as improved space saving and organisation. In short – just the kind of initiative warehouses and distribution centres are constantly seeking.”
Case study: Multi-tier pick tower
Link 51 has created a multi-tier pick tower that is designed to provide online retailers with a faster, more effective way of fulfilling orders in the ever-growing e-tail sector. In some cases, the tower has amplified warehouse capacity by 300 per cent.
Multi-tiered pick towers are flexible in that they are designed to fit into any size warehouse or space, and can include tailored needs ‘from workbenches to pallet racking on lower levels’.
“It’s important that the Multi-Tiered Pick Tower not only meets the clients current operating requirements, but is flexible in terms of growth and be able to accommodate increased levels of automation in the future,” said Kevin Blanchard, major project manager at Link 51. “As with all quickly developing markets, it’s imperative to keep ahead of the curve and provide solutions which not only meet our client’s expectations, but go that one step further.”
Case study: Cutting the cost of racking relocation
Flexi Warehouse Systems, the warehouse planning and design consultancy services division of Narrow Aisle, is now offering a rack reconfiguration system that reduces the time and cost associated with relocating, remodelling or extended adjustable pallet racking and sprinkler systems.
Traditionally, moving racking runs to enable the width of the aisles within a logistics centre to be narrowed or, indeed, widened, has been a labour-intensive process that, in most cases, involves the dismantling and rebuilding of the existing racking system, often resulting in material damage and project delays.
The technology – which has been deployed across hundreds of sites in the United States – allows racking runs to be quickly and safely transported to the required location within the store where, once the structure has been positioned and secured to the floor, it is immediately ready to be restocked.
Flexi provides a guaranteed fixed price, timescale and detailed project plan for each relocation scheme it undertakes – and reckons it can reduce the net cost by 50 per cent.
“Remodelling racking systems to make more space-efficient use of a building’s storage cube has in the past been an expensive process that often involves on-site disruption and lengthy periods of downtime,” said John Maguire, commercial director of Flexi Warehouse Systems.
“Rethinking the racking footprint and employing more space-efficient materials handling systems is one way of ensuring that a building’s storage capacity is maximised,” he said.