The retail revolution has changed the way companies organise warehouses and that is driving demand for reach trucks.
Last year BITA reported strong growth in sales of warehouse trucks – a 15 per cent increase in the first half of 2014 compared to a year earlier. It pointed out that this reflected continuing e-commerce developments in the UK.
Certainly, much of the demand for reach trucks is coming from the retail sector, where they are used with order picking trucks and pallets in distribution sectors.
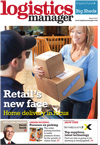
Increasing the height to which trucks can lift has been a key issue – 12 metres is not unusual and even 13 metres is possible. However, visibility, and consequently safety and product damage, becomes an issue at these heights. Some manufacturers now offer tilting cabs to enable operators to see the fork tips without straining. The other option is to use cameras to improve visibility.
Working at these heights also has implications for the mast design. Strength and integrity are clearly vital in a mast extending to 12m-plus. Sway can be an issue at that height so some manufacturers have fitted damping systems to reduce this.
Of course, working at heights over 12m also has implications for efficiency. It takes considerable skill to work at these heights Obviously it makes sense to put the slowest moving items on the top racks.
The growth of e-commerce has also put the focus on speed of operation. Narrow aisle is great for storage density but wider aisles assist with speed and flexibility.
Traditionally reach trucks have been for use within the warehouse – leaving yard operations to counterbalance trucks. However, there has been a move recently to develop trucks that can be used both inside and outside.
Stewart Gosling of RDD, which distributes Mitsubishi forklift trucks, highlights the research that Mitsubishi did in developing its family of reach trucks. Designers talked with managers and operators at companies across Europe, to identify the secret behind optimum operations. “More than any other kind of materials handling equipment, reach trucks are a partnership of driver and machine,” he says. Not only that, “The average reach truck operator mounts and dismounts the truck up to 100 times per day.”
And, he says: “Research shows that, rather than outright speed, productivity is maximised through smooth, precise but above all, predictable operation… so the driver knows exactly how a truck will perform from the moment he or she slips into the seat.”
Linde reckons that around half of all reach trucks are used for work at lifting heights of up to eight metres. And that’s the market it is addressing with its recently launched range of light-medium duty trucks. The R10B to R16B models in the 1.0 to 1.6-tonne load capacity range supplement the existing reach truck series as entry-level model.
“With the new entry-level models, Linde is offering a cost-effective alternative to the performance variant of the reach truck for applications that do not constantly demand a high level of handling performance,” says Alexander Schmidt, international head of product marketing for reach trucks and tow tractors.
The B-range trucks have uncoupled workstations, operating consoles that can be adjusted longitudinally, steering systems which enable the steering resistance and number of steering turns to be set, height-adjustable operator’s seats, load wheel brakes and wide viewing windows through narrow-profile lift masts, which can lift heights of up to 7,700 millimetres.
Jungheinrich’s newest models, launched in September, have been designed with narrow chassis to operate in aisles as narrow as 2,455mm.
The Series 1 models ETV 110 and 112 have lift capacities of 1,200kg and are just 1,120mm wide. They have a newly developed electric steering system, based on the electric steering fitted as standard in other Jungheinrich reach trucks. This means that when travelling straight ahead, the steering wheel spinner knob is always in the optimum ergonomic position for the operator.
To avoid exceeding the lifting capacity of the truck, at the push of a button the driver can check the weight of the load, which is then shown on his display.
The trucks have also been designed to be energy efficient, with field tests showing that the ETV 110 and 112 trucks consume up to ten per cent less energy than their predecessors.
Options include a fork-mounted camera and operator monitor. By viewing the special display, the operator can accurately check payload storage and retrieval even at lift heights of more than seven metres.
Articulated trucks have grown in popularity as an alternative to the traditional reach truck. The Flexi Narrow Aisle truck, for example, can operate in aisles down to 1600mm. Flexi reckons that eliminating the dead aisle space required by counterbalance or reach trucks can increase usable storage space by between 25 and 50 per cent – depending on the building. Flexi launched its new generation AC powered truck last year, which offer improved power and extended service life.
In developing the SENSiA range Mitsubishi incorporated the Sensitive Drive System which tailors the truck’s performance to the driver’s. “SDS keeps drive movements seamless – which is crucial when working with valuable or fragile loads at height.
To control sway, the trucks are equipped with Passive Sway Control as standard. They can also be fitted with Mitsubishi’s Active Sway Control which uses intelligent pressure sensors to counteract the sway that occurs when braking or accelerating when working at heights. “This can improve productivity by six per cent,” says Gosling.
Minimising the total cost of ownership is critical for many. “Particularly in intensive operations, minimising your costs means keeping downtime to an absolute minimum,” says Gosling. “Manufacturer-appointed dealers are well-equipped to deliver the highest levels of service. They hold huge stocks of high-quality components and benefit from manufacturer training… in our case in depots that literally cover the length and breadth of the country so unplanned downtime is absolutely minimised.”