Restricted space and faster fulfilment equals huge pressure in the warehouse, but reach trucks are up to the challenge. Johanna Parsons looks at the options.
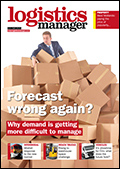
It is no longer enough for a reach truck to simply lift its loads high. E-commerce is changing the way warehouses work with massive pressure on fulfilment. At the same time a shortage of warehouses is forcing operators to squeeze more stock into confined spaces, often meaning picking takes place alongside replenishment work, even at heights of over ten metres.
Reach trucks are expected to work around a busy workforce in tight spaces, lifting higher than ever before and of course keep downtime to as little as possible. Luckily it seems the new breed of reach trucks is rising to the challenge.
The lack of available industrial units has made storage density a prime factor for logisticians. And this in turn means that more attention is paid to the configuration of the warehouse and the capability of the equipment in use.
“A rise in demand for warehouse space, coupled with ever increasing land costs, is having a significant impact on the decisions being made by operators,” says Steve Richmond, systems and projects director of Jungheinrich.
“Additionally, organisations are being forced to become more creative in how they use and optimise the space available to them. Generally the most cost effective way to maximise space is to look at expanding vertically; in this way, the total storage capacity can be increased without affecting the building’s footprint,” says Richmond.
David Bowen warehouse product manager for Linde Material Handling, agrees that going higher is an attractive option, when there may not be many. “Warehouse managers looking to expand are limited in their options. Some choose to extend existing warehouses space, which is not always possible because of the availability and cost of land surrounding them. The warehouse shortage in the UK has resulted in considerably higher rent costs so operators are looking to maximise their existing space by increasing the height of the shelving and racking.”
In fact, Linde has seen a marked increase in demand for reach trucks that will go higher. In 2005 only 38 per cent of trucks sold had extended lift heights of over eight metres, but by 2014 the figure was 52 per cent.
Another way to optimise storage density is with more racks in narrow aisle arrangements. Aisle-Master’s managing director Martin McVicar says similar trends are influencing take-up of narrow aisle trucks. “There have been numerous reports on the shortage of warehouse space, due in part to increasing demand from internet retailers. This means more and more operations are looking to remain in their current premises even during times of growth. A solution is to maximise the space available by narrowing aisles down to a minimum and using every inch of vertical space by raising the height of racking.
“In combination with articulated VNA forklifts such as Aisle-Master this can eliminate the expense and considerable disruption of relocation and also avoids the costs associated with outsourcing storage. If new premises are to be built, the size and therefore costs of the build can be reduced by maximising storage density from the outset,” says McVicar.
Ron Farr, warehouse solutions manager for Yale bears this out. “Going high is a great option with the right type of equipment. Counterbalance trucks begin to lose capacity quite quickly as they begin to lift to tall heights, while reach trucks are lifting higher. It is important to consider that additional lifting heights increase the cycle times of the truck, which can in turn create congestion in busy working environments. That’s when going with VNA machines pays dividends, lifting to heights of 17 metres and able to drive and lift at the same time, the diagonal travel dramatically reducing the cycle times.”
But reach trucks are now able to lift higher than before, and it can be possible to save space for manoeuvrability or potentially even go to narrower aisles with a smaller reach truck without losing capacity. Paul Smith, VNA and warehouse systems specialist for Hyster, says: “Companies usually select a 2 tonne reach truck, not to lift 2 tonnes, but to achieve the right weight at the highest lift height. Some operations may find that they can specify a smaller truck where a larger one may have been required previously.”
Farr agrees that reach trucks are still a great option for height and speed, particularly if a total redesign of the aisles is out of the question. “Imagine an empty square and populating this area for a standard adjustable pallet racking solution. Designing this for a counterbalance style machine will typically mean that only 34 per cent of the floor space is used for storage while the remaining 66 per cent is needed for the truck to turn in the aisle. With a reach truck the cube utilisation improves and now 49 per cent of the area can be used for racking while only 51 per cent is needed for the truck,” says Farr.
Richmond says Jungheinrich has seen a growing trend for operators to go higher but maintaining a conventional reach truck layout. “The trend for 12-13 metre racking is continuing. In retail, for example, an increase in e-commerce has seen retailers want to go as high as possible. The same goes for third party logistics providers; the current trend here is to take traditional wide aisle reach truck applications as high as possible.”
Neil Healey of UniCarriers points out that narrow aisles can prohibit working speeds because trucks cannot pass each other in the aisles, but matching the versatility of VNA working has been a motivation for manufacturers to push reach truck design further. “Reach truck designers got to work and extended both the lift heights and capacity of trucks at height. Reach trucks now exceed lift heights and capacities that only a few years ago were restricted exclusively to narrow aisle machines. This breathed a new lease of life into warehouse design offering the benefits of maximising the use of the available height in a building while maintaining the flexibility for several trucks to work in the same aisle and pass each other.”
And Healey warns that storage density is not a panacea. The speed of working is also crucial, particularly for fast moving stock items that are so typical of e-commerce. “It is easy to think that the cost efficiency of a warehouse is based on maximising the storage capability. This can be shown to be correct when slower moving lines are involved. In faster moving environments, establishing the correct balance between storage capacity and throughput capability is essential. It is in this area that the development of reach trucks has changed some of the calculations to achieve the optimum,” says Healey.
Healey says that allowing space for multiple trucks to operate around each other is particularly important for e-commerce operations with orders often being picked for the customer straight from the rack. “Reach trucks and order pickers combine in operation to maximise throughput when most needed. With the growth of online shopping, the growth in order picking has been exponential. Naturally as order picking increases, so does the need for replenishment, and it is in this area that reach trucks and order pickers can work together in the same aisle to maximise throughput.”
With e-retailers offering ever faster fulfilment many retail warehouses operate round the clock, and factoring in seasonal peaks means downtime is something of a dirty word. How you power your truck has been a priority for manufacturers, with minimal charging times, and ideally the elimination of the battery change process as the goal. Many are looking to lithium-ion technology which offers energy efficiency along with very short charge times, reducing or entirely doing away with the need to change batteries.
“On the one side, online shopping is changing the way warehouse operators organise their storage and order picking processes and on the other side lithium-ion as a power source is leading the way to exciting new developments in the internal organisation of warehouse giving additional flexibility to cope with changing demands from the market place,” says Linde’s Bowen.
“Lithium-ion technology is taking up a position as a major development in the market,” agrees Richmond, “not least because of its cost effectiveness.
“An industry-wide focus on energy efficiency has also made this eco-friendly option attractive to customers. Furthermore, a reduced need for battery changing equipment increases safety and the shorter charging times allow operatives the opportunity to charge during breaks, creating a more flexible working environment.”
Richmond says that in the year ahead Jungheinrich will expand its in-house production of lithium-ion batteries so that nearly all new forklift trucks will have the technology as an option. But he says it’s not as simple as just taking one type of battery out and putting the new one in.
“In comparison to lead acid batteries, the lithium-ion alternative is substantially smaller and lighter in weight. This has caused fresh challenges in the design of reach trucks, as historically the heavier lead acid battery pack doubled up as a counterbalance for the truck. The smaller Li-ion battery packs require research and development teams to consider new ways to best counter the load of the truck,” says Richmond.
And there are other drawbacks. Healey says UniCarriers views alternative battery technology such as lithium-ion as having potential, but he says at the moment it is cost prohibitive and also unsuitable for many sites’ working patterns.
Farr reports that Yale is already looking beyond lithium-ion to fuel cells. “Offering rapid refuelling, from a design perspective, these no longer need to conform to the square shape of a battery but can be integrated into the truck itself.”
There are developments in “opportunity charging” even with traditional batteries. The latest “4-post IRONCLAD” battery from EnerSys offers safe opportunity charging without removing the battery. Martin Walsh, senior product manager EMEA of EnerSys Motive Power says: “Our fast opportunity charging system can re-charge 25 per cent of the battery’s power within one hour, which is an industry leading performance.”
And it’s not just about speed. As Bowen points out, some of the efficiencies of avoiding cumbersome battery changing comes right back round to the important issue of warehouse space. “Being able operate through 24 hour periods without needing a spare battery with all the cost and inconvenience of changing that this entails is a major benefit for warehouse operators. Not only that but freeing up the space used as the battery room today helps to increase the amount of goods stored in an existing building.”
The new requirements of current logistics operations have inspired some impressive adaptations to the reach truck. The demand for space, storage density and the pace of e-commerce have all influenced the developments manufacturers have made in recent years. From the technology that keeps them working for longer to the new heights that they can lift to, the new reach trucks are raising the bar, and rising to the challenge.
Boosting uptime with Cat reach trucks
Lemonpath Contract Packing & Logistics, has signed a deal with Impact to take a mixed fleet of 12 Cat trucks.
The order includes six gas-powered GP18NTD counterbalance forklifts and six electric NR16N2 reach trucks, was supplied under a long-term contract hire agreement including all-inclusive service and maintenance provision.
The 12 new arrivals will be in operation 12 hours a day, five days per week at Lemonpath’s two main sites in Leicester, operating across 450,000 sq ft of warehouse space.
The trucks will be used to load varied cargoes including everything from garments to gifts to ‘goody bags’, depending on what it is Lemonpath’s customers require. Orders are loaded onto pallets, and subsequently into the trailers of Lemonpath’s distribution fleet.
Lemonpath Contract Packing & Logistics offers full-service logistics to clients around the UK and Worldwide. As well as its core contract packing business, the company also provides storage across its sites, and can package and process orders in rapid time.
Managing director, Chris Antliff, says: “Impact helped us specify the right mix and models of materials handling equipment for this order.
“We especially appreciate the flexibility the company offers in its contracts, as we encounter seasonal periods of peak demand every year. With the provision of additional equipment when required, as a ‘bolt-on’ to the contract, this means we can meet our own customers’ exacting orders on time, without fail.”
“Impact’s all-inclusive contract hire package helps us hit the high materials handling fleet uptime target that’s a cornerstone of the packing business,” adds Antliff. “Impact’s engineers ensure their visits are out of hours, wherever possible, and knowing any potential issues with our trucks will be spotted and rectified before they become a problem offers considerable peace of mind.”
Catering supplier creates space with Aisle-Master
Little and Cull supplies prepared meals to hotels, restaurants, catering groups and airlines. It recently took delivery of an Aisle-Master articulated truck at its new factory to get better use of space in the cold store, where the truck works in aisle widths of just 1800mm pallet to pallet.
The company sources most of its products from Newton Abbot where it was founded, and has a second factory in the area which was recently revamped.
“Handling and storage were important issues for us when we were in the planning stages of the refurbishing project for the premises,” said co-owner Tom Little. “Space was limited from the outset as we wanted to free up as much room as possible for production, while also having plenty of freezer capacity.”
The firm originally wanted a reach truck for use inside and a counterbalance for outside, but concerned about pallet density he spoke to Greg Vooght of materials handling consultant Westexe. “We have successfully recommended the Aisle-Master narrow aisle range to other customers with similar requirements and when Tom saw a demo of the machine in a cold store in the vicinity he knew it would be the solution,” said Vooght. Westexe also advised on the best racking configuration to achieve a maximum pallet density. Compared to a reach truck, 30 per cent extra storage space has been created by using the 20SE cold store spec Aisle-Master. This was also cheaper than investing in two trucks.
Little says: “This is a reliable and truly multi-purpose truck that we can use everywhere and its versatility is a real plus. The drivers also appreciate the easy operation and smooth controls.”