Safety is so easily overlooked in the workplace – but could it be the key to a speedier and more efficient operation? Alex Leonards reports …
It’s the height of peak season. Workers rush around the warehouse while a fleet of shiny forklifts lift those all-important pallets onto trucks, ready to deliver the goods. You’re on time and on target. But so-and-so has forgotten to make that final check, and the warehouse manager hasn’t planned for the big machinery move. An accident, which was bound to happen, has finally happened. And that means some nail-biting downtime. An easily avoidable mishap has just cost your company thousands. So is the fallout worth the risk to your business?
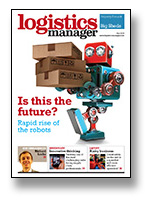
Costs triggered by accidents and damaged equipment can be colossal. And so the right, or wrong health and safety measure can have a huge impact on a business.
“The last thing a facility wants is a period of downtime caused by an accident,” says James Smith, director of A-Safe (UK).
But accidents do not just compromise your finances and the safety of an individual or individuals. They can impact productivity, reputation, morale – and these are things that most businesses just can’t afford to lose.
There is a big misconception about the relationship between safety and speed or efficiency. A common belief is that speed and efficiency are lost when safety is at the forefront of operations. Because, surely, more time spent on checks and planning means less time getting the product from A to B?
This is one way of looking at it. But Smith’s perspective paints an entirely different picture. He says that safety and speed or efficiency are not mutually exclusive.
“In fact, safety is absolutely critical to speed – or rather productivity,” he says.
Stuart Taylor, managing director of Mentor Training, the forklift training provider, agrees: “Study after study demonstrates that a safe workforce is an efficient one. After all, if you’re operating dangerously, you’re at greater risk of an accident. And whenever there’s an accident, there’s a cost and it’s rarely a small one.”
Taylor says that even a minor collision can cause a shed load, and any stock written off incurs a cost. “Seemingly insignificant incidents like these still lead to lost time for clean-up and restocking and re-site and recycling costs,” he says. “Not to mention truck repairs, stalled productivity and the impact on staff morale.”
The fallout from an accident wastes time, and ultimately, money. It’s just not worth cutting corners.
A significant issue associated with health and safety, is the lack of understanding about legislation and regulations in the workplace.
According to Peter Golding, managing director of Fleetcheck, some companies are completely unaware of the penalties faced by companies that fail to implement appropriate safety precautions and systems.
“How can you put measures in place if you don’t know the regulations?” he says.
Golding highlights the significance of the Health and Safety at Work Act (1974), which states: ‘It shall be the duty of every employer to ensure, so far as is reasonably practicable, the health, safety and welfare at work of all his employees’.
He thinks that drivers and employers need to be “fully aware” that a truck is still the workplace – and that the Act incorporates the safety of any other road user ie cyclist, another vehicle or pedestrian.
“As many as 90 per cent [of companies] are not aware of their legal responsibilities and the consequences of an accident that results in prosecution, let alone the huge financial gains to be made by following good practice,” says Mentor’s Taylor.
So, how safe are British warehouse operations?
Tom Langley, projects director at industrial door and loading bay manufacturer Hörmann (UK), says that safety is taken seriously in UK warehouses, and that it is always seen as a top priority.
“Often one of the first things we notice on arriving at a site is the signage reminding staff of correct procedures and warning them of any potential hazards,” he says.
Laura Nelson, managing director of RTITB – the global training standards organisation, agrees: “Compared to the rest of the world, warehouses in the UK are incredibly safe, but there is still much more that can be done. There are still basic things you can see in most warehouses, where an incident could occur quite easily and this needs to change.”
Rob Vesty, sales manager (UK & Ireland) for Pyroban, the explosion protection safety company, thinks that when it comes to potentially explosive atmospheres, most businesses are aware of their duties under the Dangerous Substances and Explosive Atmospheres Regulations (DSEAR).
“This usually leads to the specification of explosion proof forklifts and other equipment such as scrubber driers, access platforms and even shrink wrap machines which need to be suitably protected if operating in a potentially explosive atmosphere,” he says. But he does see the potential for risks when equipment is not maintained regularly or safely, or when parts are sourced “inappropriately”.
According to Laura Nelson, the level of safety very much depends on who the warehouse staff work for.
“In most medium and large companies, we find that drivers get at least the minimum they should need to ensure safety,” she says. “However, in smaller businesses it is still more hit and miss.
“It is in these smaller companies that attitudes towards the importance of safety need to change, as well as putting proper consideration and investment towards training.”
A-Safe’s Smith thinks that health and safety needs to be dragged swiftly to the foreground.
“Health and safety best practice has proved to be transformative for so many businesses, yet even today in some quarters out-dated attitudes to health and safety prevail,” he says. “There are still vital points that need to be highlighted, none more important than establishing health and safety as an integrated part of the overall improved running of a facility.
“Health and safety should never be seen in isolation – it should be a vital component of any well-run facility.”
But attitudes are slowly changing – safety is becoming more and more important for businesses in the industry.
“A lot of health and safety practice and products are put in place out of fear of the claim culture, but I believe companies are correctly looking at it more and more as a process to improve the whole business, whether that’s improving your product or just looking at the way your overall facility functions. To take one example, from an environmental point of view it is good to recycle or turn your machinery off – but these things all tie in to health and safety as well,” says Smith.
“If you store and organise your waste in the best possible way, then you’re adhering to health and safety but you’re also doing things in the right way.
“That’s a real trend – businesses truly understanding that the better way is always the safer way.”
Strategy: Improving safety
“ Just look at how good products will control and improve the flow of people and traffic around a facility,” says A-Safe’s James Smith. “Consider the amount of time a company has to spend on maintenance in one problem area, or consider how a poor facility layout can cause accidents, or consider how improper segregation of pedestrians and vehicles is a recipe for disaster.”
But how do we begin to tackle these kind of annoying snags? Smith believes that they can be addressed by using low maintenance products in a properly laid out facility, alongside good traffic management procedures.
“It’s implementing the nuts and bolts of health and safety,” he says.
Increased presence of technology and personalised training seems to be a trend that many companies specialising in safety hope to see in future.
“The industry needs to embrace technology more to help improve the training experience for operators and make the process more engaging,” says RTITB’s Nelson. “Instead of all operators going on the same lengthy training course which doesn’t capture their attention, their training experience should be personalised based on their own experience, ability and skills – this will result in better training outcomes.”
Hörmann’s Tom Langley thinks that businesses should have a comprehensive approach to safety – making sure that they consider any potential risks from the start.
“We work with our clients to ensure the correct loading bays, doors and equipment are supplied to suit each operation,” he says. “One solution doesn’t fit all, so it’s important to ensure the products specified are appropriate for use.”
When talking about safety, the subject of regular service and maintenance comes up time and again.
“This is usually a legislative requirement but it’s something that can easy slip,” he says. “Docks and doors that have been damaged or have not passed their inspections should be immediately put out of commission until repaired or replaced, and only experienced, competent people should undertake any service or repair work.”
The importance of good training should not be overlooked – it can be the difference between a safe warehouse that runs like clockwork, and a dangerous environment just waiting for a slip-up.
“All staff need to be provided with the relevant skills and knowledge to keep themselves and their colleagues safe; all too often its assumed that much of this is common sense and the rest can be picked up on the job but this is simply not the case,” says Mentor Training’s Stuart Taylor.
“We always recommend that those booking training look for an accredited course from the Association of Industrial Truck Trainers (AITT) that covers the three elements of training outlined in the L117 Approved Code of Practice: basic, job-specific and familiarisation.”
All training should be followed up with regular refresher training – keeping the workforce informed and up-to-date. But training alone doesn’t guarantee full proof safety.
“While operator training ensures that your team knows how to work safely and, as studies have shown, productively, it’s good supervision that ensures this is sustained for the long term,” says Taylor. “The attitude and behaviour of warehouse staff can make or break a safe operation but a competent supervisor will be willing and able to act should complacency or bad practice creep in.”
It is also really important that those working alongside operators are not forgotten. “They account for 57 per cent of those injured by lift trucks,” says Taylor. “Raising awareness and engaging this at-risk group is key.”
Personal protection: The challenge of the hard hat
The deployment of personal protective equipment (PPE), such as hard hats, goggles, gloves, is not always as easy as it might appear – approaching it in an unorganised way can cause huge problems.
“A central storeroom is often located away from the operational floor, meaning that it is away from the operational floor, meaning that it is away from the day-to-day path of workers,” says Nigel Hewitt, business development manager for vending solutions at ERIKS. “This can often mean the difference between employees replacing a pair of gloves with a hole in them and leaving it for another day, when they have more time or taking precious time out of their jobs to retrieve it.”
Hewitt thinks that with no automated process, there is always room for human error. “One pair of gloves can look very similar to another, yet the purpose can be varied and safety can be called into question if the wrong pair is supplied,” says Hewitt.
He also believes that, in storeroom facilities, it can be problematic monitoring the quantity of equipment an employee has direct access to. It can be equally difficult checking the equipment that is best suited to the job at hand. “PPE is not a one-size-fits-all solution, and ill-fitting equipment can be as much of a health and safety concern as none at all.”
Legislation: Larger fines for safety offences
The Sentencing Council’s new definitive guideline on health and safety offences came into force on 1st February this year. The legislation has introduced new, significantly larger fines for health and safety offences. But how will these new fines impact the level of safety in logistics operations? Well, the jury appears to be out on this one.
Some believe that the desired effect, to have a more safety conscious industry, will be achievable with this new legislation. Others think it will pile on the pressure, leading to mistakes.
“I think it’s likely that the new guidelines will increase awareness of health and safety issues within organisations, especially as individuals are liable as well as companies,” says Hörmann’s Tom Langley. “It’s no longer good enough to have a permit or RAMS (Risk Assessment and Method Statement) to cover yourself. “All members of staff also have to ensure that they and others are working safely.”
When asked what impact the new fines would have on a company’s safety, Laura Nelson’s answer was definitive: “In my personal opinion, none,” she says. “The companies that are aware of the fines or are conscientious about abiding by health and safety guidelines are largely already doing what they need to avoid such fines.
“To those companies that don’t know about these risks or that aren’t interested, an increased fine simply won’t make any difference.”
And Pyroban’s Rob Vesty agrees. “Only a limited impact, as most business leaders who are conscientious enough to care about their staff are already doing something,” he says. “General awareness is the most important thing for improving safety.”
James Smith thinks that larger fines will inevitably push more companies toward focusing on their health and safety. However, he warns that these health and safety procedures need to be integrated correctly. But he also has some doubt in the fines – suggesting that they may potentially be damaging rather than productive.
“Heavy fines could be counterproductive if businesses start to panic and introduce health and safety practices as a box ticking exercise,” says Smith. “Fines on their own can be problematic – health and safety education, as always, is the key.”
Case study: iFlex for Škoda
Škoda Auto wanted a balance between a quality safety solution and maintaining an ‘attractive and modern-looking facility’ at its Octavia manufacturing plant in the Czech Republic. Its steel barriers were in need of repair and maintenance. As there was an open day planned to celebrate 120 years of Škoda motors, time was tight.
A-Safe installed its iFlex Single Traffic Plus Barriers, iFlex High Level Traffic Barriers, and A-Safe Bollards at the plant. The first installation only took around 24 hours, and it was finished two days before the open day. The Bollards protected gates and entrances on the interior and the exterior, the iFlex High Level Traffic Barriers protected walls and infrastructure, and iFlex Single Traffic Plus Barriers guarded equipment in areas of high workplace traffic density.