Online shopping has changed the warehouse needs of the customer. As a crucial part of the warehouse, the loading bay needs to keep up, says Alexandra Leonards.
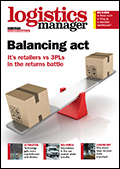
The landscape of the loading bay marketplace has changed dramatically in the last few years. With the demand for next and same day delivery, the need for smaller delivery vans has been a key turning point for the market.
“Traditionally, trucks would pick up goods from warehouses and deliver to smaller depots and shops,” says Mark James, director of administration, quality and safety at Thorworld Industries. “However, the ability of smaller vans to deliver more quickly has meant goods are now going straight from the warehouse to the end customer – but this is proving to cause problems within loading facilities.”
Of course, lots of warehouses are designed with bigger trucks in mind; involving high loading bays for ease of use. But smaller vans can’t reach these. This has pushed the industry to create new solutions to tackle the issue. “ Wheel risers can be used outside of the bay to bring the back of the van in line with the loading dock by raising it upwards,” says James. “A dock leveller specifically designed for use with smaller vans can be use.”
Ramps can then be implemented to enable access from raised warehouses down to outside ground levels.
“Lastly, and the option which is growing in popularity, is the installation of a loading Pod,” adds James. “ These Pods act in the same way as a loading docks but are fitted to the outside of a warehouse, negating the need for extensive work to be done inside the building, for example the lowering of floors.”
Transdek too is responding to the challenge created by the growing popularity of online shopping. “One of the key areas that we are involved in is the development of small, flexible cross docking centres to serve as urban hubs for online delivery platforms,” said Mark Adams, managing director of Transdek UK. “Moving away from the traditional distribution centre model, these modular cross docking centres provide retailers and e-tailers with a cost effective solution that rapidly adapts to fluctuating market demand.”
Transdek is working with a big UK online retailer to develop some of these sites, using surface-mounted, freestanding equipment to minimise impact on existing infrastructure.
“We are focused on developing modular loading equipment and cross docking stations that are quick to install, easy to relocate, and offer an efficient, seamless product flow from high capacity trunking trailers, such as double deckers, down to small rigids and home delivery vehicles,” adds Adams. “Flexibility is vital to servicing all types of vehicles.”
As well as this Transdek is developing new technology to support product security, with driver-operated ID readers on the load house doors, a mobile login capability to check equipment functionality prior to despatch, integrated internal and external CCTV monitoring.
“As retailers are increasingly competing on the quality and timing of their delivery services, it is critical to ensure the continuous and smooth running of the loading bay,” says Adams. “Our latest equipment includes the ability to remotely login to the control panel, enabling maintenance personnel to monitor and troubleshoot most issues in a much shorter time frame, minimising loading bay downtime and cutting maintenance costs.”
A key driver of new developments, says James, is energy saving, which has both environmental and monetary advantages.
“There are many methods companies are using to help them save energy,” says James. “New build warehouses are being subjected to “air tight tests”, which enables any air gaps to be identified and blocked.
“With existing dock levellers, seals are installed around the sides to plug any gaps and a coating can be applied to the deck of the leveller to reduce heat transfer.”
As well as this safety is having a big impact on design.
“Safety of employees, goods and vehicles is of paramount importance within the loading bay,” adds James. “Thorworld believes one of the biggest hazards faced by the industry is the premature departure of a vehicle from the loading dock.
“There is potential for this vehicle to move, either through creep, caused by momentum transfer when a fork lift is driven on to a vehicle, or through user error or miscommunication, such as a driver driving away while the fork lift is still at work.”
Transdek’s Mark Adams says that the logistics focus of retailers, manufacturers, parcel companies and 3PLs has been transformed by the huge rise in buying online, the growth of discount retailers and the return to local convenience store shopping.
“Additional driving forces include increasing demand for same day and next day deliveries, along with massive surges in peak period demand and events such as Black Friday and Cyber Monday,” says Adams. “Although loading bay design has traditionally been reactive, as a result of these market dynamics we are increasingly seeing that the strategic development of loading solutions can open up new opportunities for transport operators to run high-capacity trailers.
“ These can carry as much as 100 per cent extra load compared to single deck equivalents.”
He says that ultimately, there needs to be a synergy between the loading bay and delivery vehicles, with an aim to deliver products to customers on time and with the best level of efficiency.
“When it comes to variable vehicle heights and sizes, as operators diversify their fleets to gain maximum productivity, the ability to load quickly, safely and consistently can make all the difference between the vehicles being a success or, making a loss on the investment.”
Strategies for parcels operations
Hörmann has developed its latest loading bay solution to help improve both efficiency and safety for parcel delivery companies. Recognising the pressure from the growing e-commerce market on delivery companies to manage consumer expectations, the company created the cushioned BBS dock shelter.
The shelter is designed especially for small transport and delivery vehicles, like the VW Crafter and Mercedes Sprinter. The company says that with most businesses using commercial vans to meet customer demand, it developed the dock shelter so that it “can be adapted to suit the shape of these vehicles and have hinge doors with an opening angle of 180 degrees as well as 270 degrees.”
The new design incorporates foam-filled cushions which line the edge of the shelter, this is to help protect valuable stock in the warehouse from the elements as well as ensuring there is a complete seal between the vehicle and warehouse.
The dock shelter has a range of optional extras, including: a protective cover for loading bays without canopies, a rubber ramp profile GD1 for mobile dock levellers with threshold, a tailboard slot with low depth at the loading bay for vehicles with rear access and a recess in the top cushion for damage free docking of vehicles with rear cameras.
“With e-commerce continuing to increase and UK warehousing changing, distributors are continuously looking at ways to help fulfil consumers changing requirements,” says David Newcombe, managing director, Hörmann. “We are committed to providing solutions, like the BBS dock shelter, to help meet these expectations and ensure that we provide our customers with a solution to help improve loading bay efficiency and safety.”
Being the differentiator
But how different can one loading bay really be from the next?
“Being able to offer bespoke creations is key to maintaining and attracting customers and as such, having the ability to provide “made to measure” loading solutions will set a manufacturer apart from its competitors,” says Thorworld’s Mark James.
“The ability to see an installation as a “whole”, considering the entire loading/unloading function of a company, rather than a stand-alone component, will also give a manufacturer the edge over its peers.”
Transdek’s Mark Adams says that to differentiate itself, the company supplies more than just loading bay equipment. “We aim to design and engineer total solutions that facilitate the integration of more efficient transport,” he says. “As well as looking at how our loading bay equipment will operate in its own right, we want to make sure that our customers are running the most efficient transport possible. “And we also want to know how the whole thing will fit together, how the loading bay will interface with all goods vehicles that it will be servicing, and what added value it can bring to our customers’ operations.”
Sporting bay
After buying a new warehouse facility, a major international sportswear manufacturer wanted to improve the building’s existing loading bay facility. But it wanted to do this without disrupting the traditional concrete raised or dug out loading bays.
The business chose Thorworld’s platform module, and after looking at both the permanent and non-permanent solutions available, it decided a steel platform module scheme was the most appropriate.
“It’s not unusual for warehouses to lack dedicated loading bays, however if the right access is in place, there are numerous options for transforming an ‘open doorway’ or level loading area into an effective, and safe loading bay area,” says Ian Langan, technical director, Thorworld Industries. “Both these permanent solutions involve significant disruption and cost in terms of planning and civil engineering, factors which are not always feasible, especially if a building is rented or has planning permission restrictions.”
The business chose insulated roller shutter doors, including an internal platform, which were coated with Bimagrip anti-slip, to facilitate access from inside. The platform includes a sizeable working area to accommodate the use of both forklifts and powered pallet trucks, including dock shelters, traffic lights and dock lights and safe operative access via steps with side platforms.
As well as this, three hinged barriers were fitted at the rear of the platform to enable goods to be added and removed from ground level with a forklift truck.