Never before has logistics been more critical. Yet outdated perceptions persist to the detriment of progress. Liza Helps reports
Blot on the landscape. Monstrosity. Horrific. Oppressive. Troubling. Unsightly. Totally inappropriate. Just some of the words used to describe logistics warehousing in the UK. In itself, this is not anything to cause undue anxiety – these are just words mainly directed at the ‘look’ of the buildings, but they are, however, symptomatic of the general attitude towards logistics as a whole. And that is a cause for concern.
Right now, the demand for warehousing space across the UK has never been higher, fuelled by a shift in consumer spending from the High Street to online and turbo-boosted by the pandemic, which saw online retail sales grow from 19% to 26% in just 18 months – a growth of 36%. And it continues to grow, with UK shoppers predicted to spend £120.48 billion online in 2021, up from £76.1 billion in 2019 – an increase of nearly 60%.
Demand for space
It is estimated by Knight Frank that for every £1 billion spent online, there needs to be a further 1.36 million ft2 of warehouse space to support it. On that basis, just to support the increase in online spend from 2019 to 2021, there would have to have been a further 60 million ft2 of warehouse space added in the UK.
No surprise, then, that take-up of warehouse space has reached record levels with Knight Frank predicting it is set to breach the 51.6 million ft2 record set in 2020, following news that some 15.7 million ft2 was leased or bought in Q3 2021.
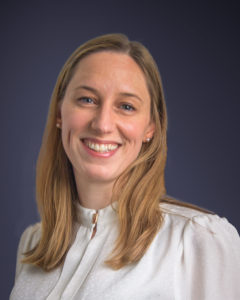
So far, take-up has reached 46.9 million ft2 in 2021 – 27% above the amount leased in the same period in 2020. “The recent supply chain crisis has demonstrated the need for greater supply chain resilience and this is driving new sources of occupier demand,” believes Claire Williams, Industrial Research Lead at Knight Frank. “The shortage of HGV drivers, labour and materials – due to a combination of Covid-19, post-Brexit customs measures, and the Suez Canal blockage earlier this year – have highlighted the need for simplified, shorter supply chains and shorter, more direct routes to consumers.Companies have accelerated efforts to secure warehouse space where they can hold high levels of inventory close to consumers, minimise delays and ensure uninterrupted service.”
It’s not all bad
According to Andrea Kellegher, Associate Director of Strategic Communications at planning consultant Turley, community benefits are rarely mentioned. “A lot of logistics warehouse facilities are purpose built,” she says. “So in terms of design, ancillary development can unlock open space – there can be substantial landscaping with funding for public transport as well as jobs.
“There is the perception jobs associated with logistics are low skilled and low paid but there is skilled work and people do not understand this,” Kellegher continues. “However, if we heard more from communities where logistics has been established for a long time, we would hear about benefits and in many cases these would outweigh issues regarding the design of the facilities.
“It’s about education and effective engagement especially through consultation at the pre-application stage. It is an opportunity to listen to and address the concerns of the local community and then address those concerns arising through and around design, and expanding benefits to the local community – be that apprenticeships or securing a percentage of jobs for locals, instigating work shuttle buses or connecting local footpaths and creating areas for wildlife conservation.”
Another area not lauded is the fact that modern logistics developments are designed to the highest sustainability standards and have been for years. Many schemes are being promoted as net zero not just in operation but also in construction making them some of the greenest of all built environments.
Scarce availability
The big problem is that although take-up has increased, the amount of warehousing available has not. In his latest statistical report, Kevin Mofid, Head of EMEA, Industrial & Logistics Research at Savills notes, “supply has fallen by 10 million ft2 in just six months, meaning the availability of warehouses is at its lowest level ever.”
What that means, continues Williams, “is that many companies are discovering that quality warehouse space that meets size, location and specification requirements is scarce”.
Indeed, CBRE’s latest research has put the amount of available Grade A logistics space over 100,000ft2 at just 7.1 million ft2, representing a record low vacancy rate of 1.53%. This compares to a vacancy rate of 5% in Q3 2020, which saw 21.35 million ft2 of readily available space. This suggests that the supply pipeline is struggling to keep up with demand.
Developers and landowners are trying to provide the desperately sought new warehousing with speculative space under construction reaching a record high of 13.7 million ft2 in Q3 2021.
But it is not enough…
The single biggest brake on provision of warehouse space to ensure that the supply chain in the UK continues to service the demands of country – be that fuel, vital healthcare products to the NHS and retail purchases such as groceries when people are in lockdown – is the supply of land with planning permission.
Anything that prevents the course of an application through the planning process dramatically hampers the provision of that critical space.
A symbiotic relationship
Housing cannot be logistics isolated, according to Andrea Kellegher, Associate Director of strategic communications at planning consultancy Turley. “Not in this day and age.”
In 2019, Turley and the British Property Federation highlighted the inextricable link between housing and the amount of warehousing required to support it in the light of the shift from the High Street to online shopping that was already occurring. At the time, online retailing accounted for 19% of total retail spend.
It estimated that an additional 21 million ft2 of warehouse floorspace would be required each year based on the government’s housing target of 300,000 homes per annum – a ratio of 69ft2 of warehouse space for each new home delivered. That figure was revised upward to 73ft2 as the pandemic turbo-charged online retailing to around 30% of total retail spend in 2021 – a figure that prior to the pandemic forecasters had not expected to be hit until 2025.
“Whether or not we need 300,000 homes a year,” says Gwyn Stubbings, GLP UK’s Planning Director, “is by the by, but whatever the number of those homes, we have to think how we are going to service them going forward.”
Paul Hanley, Partner at investor developer Bridge Industrial agrees. “Of course we need new homes – and lots of them – so it seems only right that the government should have some focus on this in the planning review. However, with more and more people wanting online delivery to their homes, there really should be much more consideration to how we achieve this efficiently and quickly.”
In that light, Savills Economics Director Mark Powney says, “Supply chain should be treated as nationally significant infrastructure like roads and rail because without it we do not function as has been made abundantly clear during the pandemic.”
Andrew Pilsworth, SEGRO’s Business Unit Director, National Logistics, notes, “The requirement for residential has an incredibly high profile but it is all about balance, It is not an either-or – residential and logistics have a symbiotic relationship.”
It’s not just about servicing those homes either. Carmelle Textor, Planning Director with developer Chancerygate, points out that employment for the people in those homes is also critical.
“So actually employment land should be given as much weight as the housing land but that is not the case at the moment.”
Some local authorities have been made painfully aware of the issue. In Stowmarket in Mid Suffolk, there was a boom in housing development but what became obvious to the council was that despite this boom, the town itself had not prospered over the same period.
Putting it simply, there were not enough jobs and the town rapidly descended into that of a dormitory settlement.
No employer seemed willing to invest in the town and no developer could be persuaded to build a commercial development to attract them. So the obvious answer was to kickstart an employment development themselves on a 156-acre site on the edge of the town alongside the A14.
The 2.45 million ft2 scheme, known as Gateway 14, secured planning permission in the Summer and is being promoted by Gateway14 Ltd (wholly owned by Mid Suffolk Council) and developer Jaynic. It could provide up to 3,000 jobs.
As it is part of the government’s Freeport East Project, the scheme has garnered such strong interest from businesses already that directors of Gateway14 believe the site could be occupied in half the time than was originally anticipated.
And that is why words matter. Because it is not just the ‘look’ of a modern warehouse building that is being called into question. It is also the capability of that building to house the number, quality and diversity of jobs promised in a planning application. Frankly, the sector is viewed with such low regard – despite recent events showing that it is part of the critical infrastructure of the nation – that the integrity of the employment is viewed with incredulity by government, MPs, local mayors and county and local councillors alike.
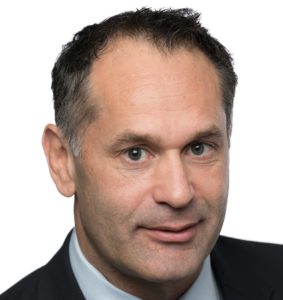
As developer investor GLP UK’s Planning Director, Gwyn Stubbings, says, “People have very little idea what goes on in a warehouse and have no idea how sophisticated they are. There is an issue in perception that the sector is dirty, with low-skilled, low-quality jobs, which could not be further from the truth.”
Indeed, colleague Bruce Topley, GLP UK’s Managing Director notes: “The misconception that it is ‘just’ manual labour is wrong. You’ve got management, telecoms, computer engineers. Yes, there is manual labour but that is just a part of the diversity of jobs being delivered in each warehouse development.”
“The perception of low-paid and fewer jobs is misguided,” adds Ben Oughton, Development Director at Jaynic. “Most logistics businesses pay well above the minimum wage and the belief that automation takes away jobs is far too simplistic – it may reduce the total job numbers but it also creates higher paid technical engineering roles.”
The flaws of perception
Nobody is denying that the industry was low density and relatively low pay in the past. According to Dominic Page, Planning Consultant at Gerald Eve, the average man on the street has a very dated perception of the industry. “There has been a massive shift with the adoption of technology in the supply chain to make it faster, more effective, efficient and sustainable. Nowadays there is a lot of automation
and robotics with warehouses employing a plethora of engineers and IT professionals to keep them running.”
None of this has happened overnight, however, according to Jonathan Dawes, Planning Director at Tritax Symmetry. “The rate of change has been missed by the wider population. In general the industry gets on and solves things without much fanfare. When the pandemic hit, the supply chain industry adjusted – there were no groundbreaking interventions, it just got on and did it.
Too (politically) hot to handle
One policy that will always challenge progress for modern logistics development is the greenbelt, believes Simon Jenkins, Development Director at specialist industrial and logistics developer Panattoni.
For Emma Andrews, the Planning Director at Savills, the pandemic has made it clear that logistics and the supply chain is a vital piece of the national infrastructure. “Planning needs to evolve; it needs to know what a modern supply chain looks like – it is a motorway junction in the greenbelt,” she says.
“From a logistics point of view, the best locations will always be on motorway junctions – and the majority of these are in sensitive locations,” adds Dominic Page, Planning Consultant at Gerald Eve.
Indeed, Mark Powney, Director at Savills Economics, says that looking at all the motorway junctions on the busiest HGV movement corridors nationally – and at sites within 2km of those junctions – he has found 52% are within the greenbelt.
What is probably more pertinent is that if just a single percentage of that land were to be developed it could provide up to 31 million ft2 of space.
“The greenbelt is there to protect, and we understand that,” says Jenkins, “but too often greenbelt boundaries are defined in out-of-date local plans that in some instances have not been subject to review, to establish if they remain fit for purpose for many years.”
There needs to be very special circumstances for greenbelt land to be released for development and due to its political nature especially at a local level Powney suggests that it should not be up to a local authority to decide.
“The government needs a strategic approach to greenbelt release along the main movement corridors – a lot of the locations have a very high level of deprivation. Industrial and logistics development can deliver jobs – it is not just about economics versus the environment, it is social as well.”
Be that as it may, Page says, “It would be a big call for a political party to get behind the release of greenbelt land for logistics.”
“People see logistics from the outside with an absence of knowledge of what is happening on the inside,” continues Dawes. “How it involves increasing levels of automation and robotics pushing up productivity and maximising margins.
“There is a whole business within that one building – from the managing director to sales and marketing, customer relations and software and IT engineers, as well as warehouse floor workers – all under one roof.”
Negative opinions
It is frustrating to be viewed so negatively. “Too often, the benefits of logistics development in terms of job creation and their important role in, for example, online retail deliveries, is forgotten,” insists Richard Hickman, Head of Planning at St Modwen. “Instead, the scale of the built development becomes the focus of concern and opposition.
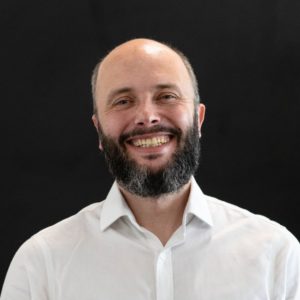
“There are instances where local authority members have positively engaged and understood the value and importance of logistics development,” Hickman notes. “But more often our experience is that opinions are dominated by negative impressions, such as logistics creates less-skilled jobs, and lack connection to the broader strategic direction of the positive impact on the UK’s economic growth.”
Local authorities
Andrew Pilsworth, Business Unit Director, National Logistics at developer investor SEGRO agrees: “There is an element that it is somewhat easier to convince a local authority to embrace manufacturing than logistics and while we have local MPs hugely supportive of our schemes providing the number and quality of jobs, not all MPs and local authorities will view warehouse development favourably – it is up to us to convince them about the quality and diversity of the jobs on offer and to promote developments as fantastic modern work places.”
“The industry needs to educate people as to just what logistics does and what it needs to function effectively. As agents we try to do this but sometimes it is viewed as a case of, ‘we would say that anyway’,” adds Tom Hardwicke, Head of Agency at SHW.
The educational piece has to be done for virtually every application over and over again.
The problem with planning
The problem with the planning system is that it is designed to be reviewed on a rolling five-year basis and will look at historic data for new plans. “Basically looking backwards to go forwards,” says Chris Procter, Director of Caddick Developments.
In a nutshell, if the land allocated for employment in the previous five-year local plan was all used up, then there is need for more sites – if all the sites were not used up, then there is not the need to allocate as much.
But as Mark Powney, Director at Savills Economics, says, “What happens when there is a change in demand? How can you project forward historic average annual leasing demand when there is more household shopping online, when due to Brexit a lot of UK firms are re-shoring, when UK freight volumes leaving and coming into the UK are increasing – these growth drivers are not picked up by looking backwards.”
This is in contrast to the government’s approach to housing where a clear national target has been set and district-level requirements are now enshrined in the standard method, combined with a well-established five-year supply requirement and the relatively new Housing Delivery Test.
According to planning consultant, Turley, there is no comparable way of determining the need for employment land and no equivalent sanction for not meeting that need. Unlike residential, there is no forecasting model to ascertain future employment land requirements.
Richard Hickman, Head of Planning at St Modwen says: “The absence of a clear and consistent methodology for establishing how much land should be identified for logistics through local plan reviews means that local authorities are not allocating sufficient land for logistics development. There is a standard methodology for housing, so why not logistics and other forms of employment development?
“The inflexibility of the plan-led planning system has been exposed to an even greater extent in the past 18 months as it has been unable to respond to the significant rise in market demand for logistics floor space arising from the pandemic and increase in online retailing.”
For Mark Powney, Director at Savills Economics, this is at odds with economic reality. “Logistics delivers more full-time jobs than any other sector,” he says. “Wages are growing faster than any other sector. In terms of business growth, it is the strongest in real terms but needs more land to facilitate growth.
“We are in a post-Brexit world; we want to attract investment and salaries, etc, but the one thing that is going to hold us back is labour productivity,” Powney stresses. “The UK is the least productive of all Western European countries – we need to invest in the most productive part of the economy and logistics is predicted to grow 29% – other sectors are at best 18%.
“The sector is trying get traction but we are coming from a low base – in its recent planning white paper, the government only mentions logistics once.”
Government stance
The Planning for The Future White Paper in August 2020 set out how the planning system was to be reformed to better serve modern society. Central to its focus was the need to tackle the housing crisis with a delivery target of 300,000 new homes a year. To reach this ambitious target, each local authority was to provide a binding housing target but no such targets were put on employment land. Indeed there was only one brief and passing comment that local authorities should give consideration to the needs of the industrial and logistics sector. [At present the White Paper is in abeyance until after the COP26 conference in November but no one is holding their breath for a change in direction.]
“The big challenge for local authorities is planning for housing delivery,” says Chris Procter, Director of Caddick Developments. “It is a contentious issue compared to employment land. Very few people in general will turn up for an industrial consultation compared to a residential one, which can be more politically thorny, so often it has been a case of letting employment get on and do its own thing. It can usually be met under current planning conditions but in the past few years, there has been a significant quantum shift in demand for employment land allocations.”
“Planning reform focus is only ever on housing because that strikes a chord with voters and the next generation,” adds Procter. “There is a presumption that commercial and business looks after itself, which is clearly not the case in a primarily plan-led system, which has woefully failed to keep pace with seismic shifts in the sector.”
Missed opportunity?
For Paul Hanley, Partner at investor developer Bridge Industrial, “it’s clear the government’s white paper completely misses the importance of the industrial and logistics sector”.
Len Rosso, Head of Logistics & Industrial Space at Colliers agrees. “The government had one chance and
it did not take it.”
This same attitude could be said to have led the government to conclude that HGV drivers and indeed many other logistics professionals were too low skilled to be essential when it came to the classification of workers in post-Brexit immigration policy in February 2020 – a time when 64% of transport and storage businesses were struggling to fill vacancies.
At the time, leading sector bodies such as Logistics UK were appalled and warnings went out that these are, in fact, very challenging roles. “Vocational occupations make a significant contribution to the UK economy – the government must realise it is not just academically trained workers that hold value.
“The logistics sector is the lifeblood of the nation’s economy, ensuring shops, hospitals, restaurants and schools, etc, all receive the goods they need to operate. Although businesses within the logistics sector will do everything possible to keep the UK trading, without adequate levels of staff, operations will become strained and UK PLC will inevitably suffer.”
Those words were strangely omniscient when a mere 18 months later the HGV driver shortage would lead to chaos at the fuel pumps and is threatening goods supply over Christmas.
“If the powers that be cannot appreciate the changes in the industry or value its contribution to the UK economy, then how can the public?,” says Emma Andrews, Planning Director at Savills. “And if neither the powers that be – nor the public – can discern the changes or value its contribution, then how can the planning system?”
Employment land
This has become such an issue that planning specialist Turley published a report called Playing to our Industrial Strengths highlighting the problem.
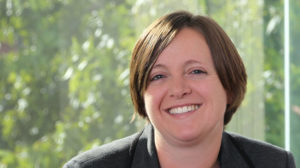
“The frustration about all this is based on the whole lack of airtime given to employment land – and logistics in particular – by government, as evidenced in the planning white paper,” explains Sara Dutfield, Planning Director at Turley.
“Without support for the industry in terms of land allocation, from the top down you will get an uncoordinated approach leading to a fragmented network when it needs to be connected.”
Dutfield’s colleague, Andrea Kellegher, Associate Director of Strategic Communications, says it is more important than ever for local authorities to identify land for logistics. “It is a local political decision and if you have the support from the top down, it makes it easier at a local level for people to support these projects.”
“More support at a national level should cascade down – not putting in that support on a national planning policy level would be a huge missed opportunity,” agrees GLP UK’s Stubbings.
But perhaps that is the whole point. By not actively supporting it at a national level means the responsibility is devolved to a local level. Some may say that is shirking the responsibility. But, as Gerald Eve’s Dominic Page concludes, “Industrial and logistics is land-hungry and more often than not, as it cannot be accommodated in established urban areas, it is looking at greenfield, greenbelt and countryside areas and central government does not want to be crashing into that.”