From data analysis and semi-automation, to electric vehicles and high performance batteries, technology in the forklift truck market is evolving. Alexandra Leonards takes a look at some of these new developments.
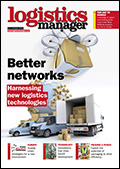
Technology offers the promise of new and exciting developments for the materials handling market. Warehouse operators are looking for equipment that guarantees high performance, efficiency, safety and environmental benefits. Forklift technology in particular is evolving to deliver these important qualities.
In most arms of the logistics industry, data is under the spotlight. If used correctly, it can be tremendously useful for an operation – and although they might not know it yet, warehouse operators need technology that can do just that.
“Many businesses are lacking suitable monitoring for their forklift fleet,” says Thomas Toenders, telemetry solutions specialist for Hyster. “Quite often, they may not realise that they can be much more productive and save money by using data provided by an accurate fleet management system.”
According to Mark Wakeman, national territory sales manager at UniCarriers, one of the biggest developments currently happening in the market is the progression of fleet management systems.
“These systems are being influenced by our customers who are under immense pressure to find ways of reducing out of contract costs caused by operator damage,” says Wakeman. “Modern Fleet Management Systems become more sophisticated, including for example collision damage sensors which record the severity of a collision, the time of the incident and who was driving the truck.”
These systems can respond to dangerous situations automatically. For example, if a major impact occurs in the warehouse, a truck is able to instinctively shut down – and the truck can only be restarted by a designated manager.
“In the long term this can reduce accidents and damage costs,” says Wakeman. “Furthermore, this gives accountability and traceability to customers and helps reduce their out of contract costs.”
Customers are feeling the pressure from health and safety regulators to ensure pre-shift checks are made and subsequently archived.
“Vehicle Operator Management Systems eliminate the need for paper check lists and keeps electronic records which are easily accessible even months down the line,” says Wakeman.
According to Ron Farr, manager of warehouse solutions for Hyster, uptime is of the upmost importance to the materials handling industry.
“Trucks are used in high intensity situations, particularly for the logistics and transport sector, manufacturing industry, wholesalers and retailers so Hyster trucks are tested under extreme conditions,” he says.
This is where warehouse simulation software can come in very handy.
“Warehouse simulation software from Hyster can be used to calculate throughput and configure the most efficient layout for the operation, taking congestion problems into account,” says Farr. “It can help to determine the right number and types of truck required, including forklifts, with simulation for coping with seasonal demand.”
Wakeman says that customers are constantly attempting to maximise output and minimise costs. UniCarriers have identified this as a big influence on its customers taking more interest in its logistics analyser, or simulation software.
“This simulation software can accurately calculate truck numbers required, look at different racking layouts to optimise storage,” says Wakeman. “This enables us to put forward cost effective solutions.”
Another trend that appears to be dominating the logistics industry is a shift towards semi-automation and automation. And this is no different for the materials handling market.
“There is definitely a trend towards semi automation especially within the Very Narrow Aisle sector,” says Wakeman. “These types of trucks can use RFID technology to guide the truck (lift and travel) to the desired picking or stacking location within the warehouse without any intervention from the operator.”
According to Wakeman, these methods ensure the truck will always get to the destination in the quickest and most efficient way.
Increasingly, forklift design is incorporating the impact vehicles have on the environment and energy efficiency. A move towards electrically powered trucks is particularly palpable.
“A number of features are responsible for some businesses making the move to electrics, such as improved efficiency, particularly in terms of battery power, and the associated low cost of ownership,
including maintenance costs,” says Karen Calver, product strategy manager for Hyster. “Electric trucks are also becoming even more economical than previous models and allow environmentally friendly operation with zero emissions”.
But for many, internal combustion vehicles are still the best option.
“They are far cleaner and more fuel efficient than they have ever been – so as with any materials handling equipment, the truck selection ultimately comes down to the specific application requirements,” says Calver.
Battery technology is having a big impact on the cold store market in particular.
“High performance batteries enable companies, for example, to work 20 per cent longer in a cold store environment compared to standard batteries,” says Wakeman. “When a truck is working in cold conditions 20 per cent of the battery performance is lost due to the low temperature.
“The new battery technologies effectively ‘get back’ the 20 per cent.”
As well as this, many companies are considering installing cold store cabins, which can achieve longer operating times and greater productivity, at the same time giving the operator a more comfortable working environment.
There is a level of conflict for many businesses when it comes to deciding what they want from a technology. Some companies are looking for simplistic methods and technologies, while others are searching for high-tech materials handling.
“The market currently sees a polarisation, since operators need “horses for courses”, says Rory Harvey-Kelly, general manager of Baoli Material Handling Europe. “Customers on the one hand need high-tech trucks, but on the other hand more and more end-users are asking for basic technology.”
According to Harvey-Kelly, one of the key drivers for the design and development of Baoli forklifts is operators that prefer very basic technology.
“Our dealers influence the technological improvements, because they are our exclusive contact point with our end-users,” he says. “Baoli forklifts are designed for easy use and maintenance.
“On-going technology increases reliability and improves serviceability.”
He says that a very important aspect for its dealers and operators is consistency. “Operation and service of a forklift fleet is more cost effective, when trucks are designed on a joint platform sharing key components,” he says.
Customers have a big role to play in the development of new technologies in the market. “Customers do influence forklift technology significantly,” says Wakeman. “One example is the UniCarriers Ergo logic Joystick which enables the driver to control all the hydraulic functions on the forklift safely with one hand. Taking into account the customer’s needs, the Ergo logic Joystick was designed to not only make the truck more efficient but also to improve the operator’s environment.”
More than just cost, efficiency and speed
It isn’t just costs, efficiency and speed that operators have to think about when choosing the right technology. Safety always seems to be one of the key considerations for customers deciding which truck is best for them.
“Operator safety and training is a key consideration within any materials handling operation and with forklift trucks implicated in around one-quarter of all serious workplace transport-related injuries and some ten fatalities a year, it’s easy to understand why,” says John Maguire, commercial director for Narrow Aisle. “Successful warehousing is always a balance of productivity and safety, but safety has to be the foremost consideration.”
Ubisense, the enterprise location intelligence company, says that one of the dominant issues created by forklift truck design is the absence of a clear field of view for drivers. The controls are designed to face the forks, so drivers find themselves peering through the equipment. This leaves most drivers with very limited visibility when looking ahead. Another big problem is pedestrians underestimating the speed of forklifts, as well as drivers moving too quickly. Ubisense says that if a driver brakes or stops quickly, they may topple over, which can injure both the driver and any pedestrians nearby. Quite often there isn’t much separating a pedestrian from a forklift in the warehouse. A standard facility will have a yellow line on the ground marking the separation point. Although this may be an efficient safety precaution most of the time, pedestrians won’t necessarily always been seen by a driver, or stick to the rules.
Ubisense says that although there are countless technologies out there dedicated to reducing the number of accidents caused by forklift trucks, there is still a lot of room for improvement. It says that despite the fact that real-time monitoring and control can improve collision avoidance, ‘one of the main problems has been the latency of infrastructure-based, real-time location systems (RTLS).’
The company says that frequently, by the time the system identifies both the location and time, and sends out an alert, it can be too late. According to Ubisense, these warnings are more like ‘you just hit a pedestrian’ than ‘slow down, pedestrian ahead’. It also says that these systems can be fairly complicated – often sensors are fitted throughout a warehouse, which can be a lengthy and expensive process.
Ubisense has launched its AngleID solution which can ‘precisely detect the position of a pedestrian in line with a forklift’s direction of travel.’ According to the company, it can provide precise location data even in heavily metallic warehouses, with the
power reader offering ‘ten times the range of most systems.’
The device works by sensing ultra-wideband pulses from its RFID tags by using an antenna ray to identify the exact angle between the tag and the reader. Then it ‘compares that angle in up to eight different zones and reports entry and exit events at each in real time.’
In practice, an AngleID reader is put on either side of a truck, and an RFID tag is placed on the employees themselves (on either lanyards or badges). By doing this, the truck can identify whether or not there’s a pedestrian in its direct path. Ubisense says that the device can detect pedestrians up to 150 feet in front of the vehicle. At the same time, it is able to ignore people that are safely in the pedestrian lane.
Boosting the efficiency of electric trucks
The efficiency of electric trucks is increasing continuously. These trucks are considered the ‘workhorses’ of the electric truck range,” says Karen Calver, product strategy manager for Hyster. “They are productive, durable, energy-efficient and rugged with a low cost of ownership.”
Hyster’s 4-5T electric models feature an Eco-eLo mode, which the company says reduces energy consumption during intensive use, while at the same time maintaining a high power level. The manufacturer says that this results in an overall reduction in cost of ownership and maintenance. This is also assisted by simplified access to the battery and components with removable side panels and floors.
Hyster trucks that include its new PSI Engine are able to switch between operating modes. Maximum fuel efficiency, with a 24 per cent improvement (measured in loads moved per kilo of fuel) can be achieved with its Eco-eLo mode.
“These modes allow the truck performance to be tailored to the application and give flexibility for the same truck to do more, in peak demands, for example,” says Robbert Wijnandts, counterbalance product manager EMEA, Hyster.
Wireless tracking takes off
Hyster has launched its Hyster Tracker Wireless Access Monitoring System, which is designed to track performance data and monitor and report on the performance of warehouse equipment. This is achieved via a wireless tracking technology.
“Even in the most demanding applications, the Hyster Tracker fleet management system empowers managers to enhance productivity, control costs and optimise their fleet using accurate business intelligence,” says Hyster’s Thomas Toenders.
Lifting the lid on layer picking
Recent advances in layer picking handling technology are having an impact in the grocery retail supply chain. Narrow Aisle’s John Maguire says: “Historically, orders bound for grocery retail outlets have been picked and despatched from the distribution centre as either full pallet loads or mixed loads picked manually onto pallets or in to roll cages,” he says. “Layer picking is seen as a highly cost- and throughput-effective alternative to these two options by retailers and their suppliers alike and as an essential method of leveraging order picking efficiency and eliminating manual handling.
“Selecting customer orders in layer picking quantities slickens the picking process and increases the speed of pallet throughput at a warehouse or DC by employing technology to handle single or multiple layers of products and allowing the user to build up mixed pallets quickly, safely and efficiently with minimal use of manual labour.”
Retailers are attempting to reduce their inventory. And so they want fast moving lines for one or two layers instead of complete pallet loads.
“Thanks to the economies involved in packing layers, a full layered pallet of 50 cases can be picked for up to 5 times less cost than traditional manual case picking strategies,” says Maguire. “Case pick rates of up to 1200 outers per hour per man are typical.”
Narrow Aisle has generated a technology specifically for layer picking-based storage and order fulfilment. Its FlexiPICK truck enables operators to reap the benefits of layer picking, without having to invest in high fixed cost automated handling technology.
“In simple terms, when using the FlexiPiCK full pallet loads of the most popular layer quantity product in the distribution centre are arranged in an aisle format at ground level and with assembly stations positioned at the end of each aisle,” says Maguire. “The FlexiPiCK’s integrated hydraulic arms carefully grip single or multiple layers of product and deliver each individual layer picked to the assembly station where a load is made up of full layers.” Each layer is secured with additional pallets for the separation of goods at the warehouse or a brick-and-mortar store.
“Narrow Aisle’s customer data indicates that with FlexiPiCK layer picking technology over 1000 cases per hour can be picked,” says Maguire.