The Co-op has just gone through a major upgrade to its supply chain software and solutions specialist Barry Morgan explained how and why, when he spoke at the Supply Chain Conference on Tuesday.
The retailer had been using a Manhattan WMS from 2004 and the decision was taken to upgrade to the 2015 version of the software.
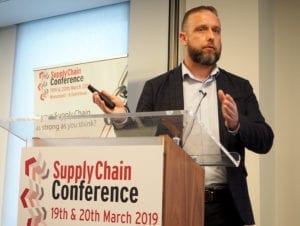
Morgan pointed out that one of the challenges was simply that a lot of people in the business didn’t think it needed to upgrade. As part of the process, the Co-op looked at all the systems in the business and categorised them in terms of risk.
The strategy was to replace the old system on a like-for-like – not same-for-same – basis, with a single design for all 12 warehouses.
To make the upgrade involved aligning processes across all the depots – which took some time to implement. Nevertheless, implementation of the upgrade was completed on time by the second quarter of 2018.
Morgan highlighted some of the benefits of the upgrade. For example, the old system included lots of software modifications many of which were no longer needed. So with the new version it was able to reduce the number of modifications.
Another benefit was that the new WMS has better integration with other systems, and it has also reduced unscheduled down time.
Patrick Rigoni, founding partner of SmartChain International, examined the demand driven adaptive enterprise as a necessary condition to reap the full benefit of digitalisation.
To manage the supply chain you need data – we have lots of data but the reality is that only a small of the information you have is relevant.
If you cannot identify this and include the wrong information in your analysis you will get the wrong conclusions.
Rigoni highlighted key problems such as the bullwhip effect, and he looked at the benefits becoming demand driven.
And he warned that without becoming demand driven, digitalisation could simply mean doing the wrong things more efficiently.
The challenge of supplying global markets came under scrutiny when Procter & Gamble’s Onofrio Caradonna opened the Conference.
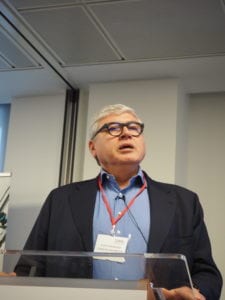
Caradonna, who is P&G’s Europe product supply shared services leader, focused on Global Distributor Markets, more remote markets where the company works through distributors.
He pointed out that the distributors are very good at selling but not always good at forecasting. As a result it was very difficult to manage inventory.
The start was a quick fix solution using spreadsheets but there were significant problems, and it quickly moved on to look at how to accelerate business growth by designing a more customer centric supply chain.
The Global Distributor Markets (GDM) Supply Chain Synchronisation involved enabling business growth by creating a compliant and synchronised global supply chain to serve customers and consumers with a global portfolio, with the right quality, service and cost and cash, for P&G and its distributors.
It requires a big cultural change moving from customer service to customer-centric. Needed to redesign supply chain to focus on those things that customers want and need (and would be willing to pay for) to boost sales and profit.
Caradonna highlighted some of the achievements of this approach. In one example, he said it had been possible to cut 50 per cent in delivery time moving from sea containers to intermodal. This reduced customer inventory and increased their cash flow to invest in new categories launch.
And in another example, it had reduced the minimum quantity order which had enabled the distributor to eliminate expensive.
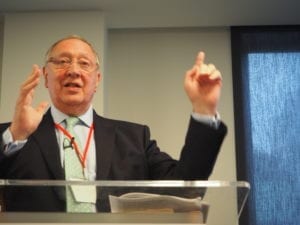
In the second session of the morning, Alex Watson, head of logistics – operations & fulfilment at Superdry, explained Superdry’s supply chain journey.
Superdry took the overall award at the 2018 Supply Chain Awards having progressively transformed its supply chain, driving innovation in the business to deliver competitive advantage.
He then went on to look forward at the challenges facing society as whole. He quoted futurologist Peter Diamandis on the power and implications of exponential change. He highlighted the importance of the move from physical into digital infrastructure that is already happening.
The Supply Chain Conference continues in London on Wednesday 20th March, when John Munnelly, head of operations at John Lewis’s Magna Park campus, will explain how the retailer is reimaging the world of logistics. And Jurgen Kull, HP’s director of supply chain operations EMEA, will discuss “Striving for excellence in Collaboration”.
Click here for more details.