Loading bays are a crucial part of the warehouse, but what do customers want from them? Alexandra Leonards explores the importance of safety, maintenance, and bespoke solutions for customers looking to improve their supply chain through efficiency in the warehouse.
As the bottleneck of the warehouse, decisions about the design and installation of loading bays cannot be taken lightly. But what do customers want from this vital part of the warehouse?
“Loading bays are a focal point for activity and need to be as efficient as possible,” says Hörmann UK’s projects director, Tom Langley. “Bringing together a number of elements including machinery, vehicles, and personnel means that safety is pivotal.”
E-commerce has revolutionised the way consumers purchase items, and so, says Langley, retailers are having to constantly look at new ways to manage customer expectations.
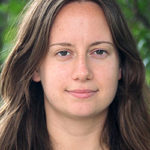
“In order for them to do this, warehouse operators are under increasing pressure to consider how they can deliver goods faster, more efficiently and in the safest possible way,” says Langley.
The growing demand in the warehouse and logistics industry puts pressure on the loading bay market to ensure that safety is maintained throughout this growth.
“It is more important than ever for warehouse operators to manage and meet expectations, while providing individuals on site with robust safety,” said Langley. “With any size project, health and safety is now not only at the forefront of the design of loading bay equipment but is a top priority within the work space.”
Transdek’s managing director, Mark Adams, agrees that safety is a key consideration for customers. He says that safety is one of the core requirements that the loading bay has to meet, and that this hasn’t really changed over the last ten years.
“As one of the most statistically dangerous places in the workplace, it has to provide loaders and drivers the highest possible standards of safety,” says Adams. “It also has to act as a fast and efficient conduit of products from the warehouse to delivery vehicles, it must comply with ever more stringent environmental standards, and it has to be cost effective to operate and maintain.”
He says that due to market forces, there is an increasing focus on maintenance to ensure that loading systems and the loading bay in general run consistently and minimise any potential downtime.
“This is becoming ever more critical as demand for timed delivery slots increases, and consumers’ tolerance for delayed or late orders drops,” added Adams. “Problems are soon aired on social media and brands recognise the importance of meeting their customers’ expectations are ever more important.
“On time in full distribution starts with the loading bay.”
Nowadays, more and more customers are looking to loading bays as a source of management information that can help to enhance overall efficiencies in the distribution network. “By tracking and comparing loading speeds, vehicle fills and downtime frequency, managers are able to increase productivity in both the loading bay and the wider distribution network,” he says.
According to Mark James, Thorworld Industries’ director of administration – quality and safety, historically a standard product would be offered, which the customer’s loading facility would have to fit around.
“Now, customers are dictating what they want from a loading solution, looking for bespoke creations which can be installed around existing equipment or facilities,” he says. “Also, rather than looking at individual components, customers are now considering the entire system, from the flow of traffic in the area to energy saving, when looking at loading solutions.
“This means that the manufacturer has to do the same, creating a whole scheme, visualising where its loading ramp or platform fits into the system, rather than simply offering a standard sized product.”
There are lots of new technologies springing up in the market.
“For the retail and grocery sector the loading bay needs to be able to meet a wider range of distribution demands,” says Adams. “This includes loading a variety of trucks and trailers, from standard rigid trucks and curtainsiders to high volume primary double deck trailers and urban vehicles.”
He says that looking at double deck trailers, these can provide savings of up to 40 per cent to 50 per cent on transport operations, when properly supported in the loading bay. “Unfortunately, many operators lose a lot of these potential gains and end up running at sub-optimal efficiency or even, in the worst cases, scrapping their fleets altogether, simply because there’s no reliable loading mechanism,” he adds.
James says that many warehouses have been created with larger trucks in mind, with high loading bays for ease of use, but smaller delivery vans, and even cars, which are being used more due to the rise in e-commerce, are unable to reach.
“However, there are a number of solutions,” he says. “Wheel risers can be used outside the bay to bring the back of the van in line with the loading dock by raising it upwards. “A dock leveller specifically designed for use with vans can be used.”
Steel solution
A big international sportswear company has improved its loading bay capabilities at one of its UK warehouses by using a cost-effective platform module, which was created by Thorworld Industries.
The business, after recently buying a new warehouse, wanted to improve the existing loading bay facility without the disruption or permanence of traditional concrete raised or dug out loading bays.
The company decided, after researching permanent and non-permanent solutions, that a steel platform module scheme would be the perfect solution.
Ian Langan, technical director at Thorworld Industries, says: “It’s not unusual for warehouses to lack dedicated loading bays, however if the right access is in place, there are numerous options for transforming an ‘open doorway’ or level loading area into an effective, and safe loading bay area.”
The recently purchased site had the logistics scope for these kinds of improvements to be made. The sports brand could see that efficiency and safety could be enhanced by installing a modular steel solution.
But the company wanted to avoid the expense and disruption of either ‘building up’ a concrete platform to the height required to access lorry trailers, or alternatively, ‘digging down’ to create foundations for a recessed loading bay.
“Both these permanent solutions involve significant disruption and cost in terms of planning and civil engineering,” says Langan. “Factors which are not always feasible, especially if a building is rented or has planning permission restrictions.”
The international business expressed an interest in Thorworld fitting new insulated roller shutter doors, along with an internal platform, coated with Bimagrip ant slip, to facilitate access from inside.
The new platform would provide a sizeable working area, big enough to accommodate the safe use of fork lifts and powered pallet trucks, and would include dock shelters, traffic lights and dock lights, as well as safe operative access via steps with side platforms. Three hinged barriers were fitted to the rear of the platform to allow goods to be added and removed from ground level with a fork lift truck. Both hinged and telescopic lip dock levellers were provided to maximise the range of vehicles that could use the loading bays.
Thorworld designed a platform that could be positioned level to the building’s two shutter doors, at trailer height, so that trucks could reverse up to the doors and fork lifts or pallet trucks could load or unload containers, supported and enabled by the apparatus.
Langan says that an internet search, a method the majority of Thorworld’s customers now use to source bespoke loading bay solutions, was their first port of call.
“Now more than ever, new clients are contacting us having first seen an example or existing installation of a Thorworld loading solution on our website,” says Langan.
Thorworld’s skilled engineers were able to deliver all the necessary technical expertise to oversee the design, installation and subsequent maintenance of the business’ loading bay module. Combinations of systems comprising ramps, platforms and dock levellers were used to deliver a bespoke, semi-permanent solution, capable of fulfilling all the requirements of a dedicated concrete loading bay.
“These systems, when used in conjunction with insulated doors and shelters, perform exactly as a permanent fixture would, and can also provide significant operational and energy savings by minimising the heat transfer between clients’ warehouses and outdoor environments,” says Langan. “When all these key features combine, it’s simple to see why the equipment is perceived as such a viable alternative to a concrete loading bay. It’s an optimum solution; cost effective, non-permanent, highly effective and most of all, safe.”
Health and safety
Hörmann has installed more than 130 loading bays at two John Lewis Partnership sites in Magna Park Milton Keynes.
The 638,000 sq ft warehouse facilities were designed to future proof the leading retailer’s supply chain and support its growth in online business. To make sure that health and safety measures are adhered to on the site, it was important to develop a safe working environment.
Differing dock specifications, vehicles, visiting drivers and lack of direct communication between driver and warehouse staff are some of the things that can prompt potential problems.
So, with this in mind, having already supplied both existing John Lewis Partnership sites at Magna Park three, Hörmann installed several products to prevent health and safety hazards.
To accommodate the exact requirements of John Lewis Partnership’s diverse fleet of vehicles, 16 mechanical dock levellers were installed for van bays to ensure that there was a flush connection between the loading bay and vehicle. The precise positioning enabled a safe link, and the van bay shelters also helped to deter slip-ups by reducing the amount of water that could enter between gaps during adverse weather conditions.
As well as this, double-skinned steel SPU F42 sectional doors with full width panoramic vision panels were installed on each loading bay and Nytrex buffers were installed onto the outside of the warehouse to prevent expensive collision damage and absorb the dynamic shock from a lorry during docking.
This article first appeared in Logistics Manager, December 2017