Shifting consumer demands are prompting a warehouse design revolution. Alexandra Leonards explores where narrow aisle trucks fit into the new logistics landscape.
Changing consumer habits and desires, economic changes and unbounded choice, the environment in which the logistics industry finds itself in is ever-changing. Consumers want more choice and quicker deliveries – with next day, and even same day becoming the norm.
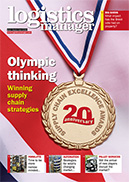
“This requires better warehouse management communication in the day-to-day operation, as well as improved warehouse design as a longer-term solution,” says Ron Farr, manager of warehouse solutions at Hyster. “Hyster uses a warehouse simulator to help customers design the warehouse for optimal flow and product mix, creating a lost cost of operation solution while achieving the peak flow rates needed.”
In the past, warehouses stocked goods for high street stores, where case picking was the norm. “Now, with the rapidly increasing demands of online shopping, suppliers are seeing consumers purchase goods individually resulting in the order picking function needing to accommodate 24 hour demand for individual line items,” says David Bowen, sales support and training manager at Linde.
Operations are shifting, and with that, the design of warehouses are changing. Narrow aisle trucks are here to cater to this new purpose and design. “There are a huge number of existing warehouse buildings across the country constructed and equipped over the last 25-30 years,” says John Maguire, commercial director of Narrow Aisle. “Due to the enormous changes in the retail market and the economy in general, many of these sites are no longer fit for purpose.”
Maguire says that often the original usage of a warehouse changes completely. “Therefore the storage and material handling equipment installed is no longer efficient to say the least. This can present an opportunity to re-design and re-configure, using new intralogistics technology and handling techniques, to create a much more cost effective operation often with a very attractive pay back period.”
He says that there are a high number of warehouse operators who, because of a lack of good quality warehouse facilities, have to reconfigure their sites to reach the additional storage capacity. He identifies this as one of the key reasons global sales of Narrow Aisle articulated trucks reached a record high last year. “The major changes taking place in the retail sector – in particular the move by consumers to online ordering – will create many new opportunities for the 3PL sector but the shortage of newer good quality warehouse sheds, especially in the UK and USA, will lead to more investment in refurbishing and reconfiguring older warehouse stock,” he says.
Linde has experienced some significant growth in its VNA truck sales. “Very narrow aisle trucks are a consistently popular product in recent years, we’ve noticed a growing demand for very narrow man up trucks such as Linde’s K-truck,” says Bowen.
So why choose narrow aisle trucks over a standard counterbalance forklift? Gary Ison, product manager at Toyota Material Handling, says: “The key benefit for a narrow aisle truck is the aisle width it works in – typically narrow aisle machines require half the operating aisle width of counterbalanced trucks, giving an increase in valuable racking space for storage. However, they are also typically 3-4 times greater in cost and require much more highly skilled operators at a premium salary/agency cost.”
“The cube utilisation of the warehouse is important for ensuring that the cost of storage is minimal,” says Hyster’s Ron Farr. “Particularly as property prices continue to climb, the higher the number of pallets stored in a single location the lower the cost per pallet. Consider a typical counterbalance truck working in a racking application: just over 50 per cent of the building floor space is required to allow manoeuvring of the fork lift truck.”
Linde’s David Bowen says that comparing narrow aisle trucks to standard counterbalance trucks can be difficult, because it really depends on how a warehouse operates.
“Linde’s VNA man-up trucks allow for an aisle width of approximately 1.8 metres, whereas a standard counterbalance truck requires aisles of three metres in width,” he says. “This means that VNA truck applications do not allow space for any other trucks or machinery to pass along the aisle.
“In a larger aisle with counterbalance or reach trucks, it’s normal for trucks to pass each other in opposite directions. This may seem like a limitation for some of our clients, but it actually all comes down to an effective warehouse management plan to allow a continuous flow of goods being transported.”
Narrow aisle trucks most benefit environments that store goods at higher levels, and, of course, for spaces that have tighter aisles.
“This is becoming an increasingly popular method of warehouse cost optimisation because a VNA installation can increase storage capacity by approximately 30 to 35 per cent,” says Bowen. “With goods stacked at higher levels, our VNA trucks have been designed to accommodate lift heights of 17 metres, compared to our counterbalance trucks at six metres and reach trucks at 13 metres.”
VNA trucks are popular for grocery applications and also in any environment that requires multiple trucks to operate in a single aisle, says Farr. “They are also well suited to applications where different trucks and processes are taking place in a single aisle, such as order picking and pallet handling.
“In order picker applications the aisle needs to be wide enough to have two trucks pass which normally results in a need for a VNA reach truck to operate within the constraints of the aisle dimensions.”
The numbers speak for themselves – with VNA trucks growing at a rate of 7.4 per cent compared to last year, according to Hyster. “These trucks also have the benefit of providing 100 per cent selectivity and the speed of the machine is very quick,” says Farr. “The only real limitation is that there should be only one truck for each aisle in a warehouse.
“While these types of trucks are used in a wide range of different warehouse operations in different industries, we find that they work particularly well in logistics and manufacturing applications.”
However, Toyota’s Gary Ison points out that: “With the rapidly growing e-commerce sector, movement of bulk is being reduced by the need for smaller quantities, faster. This means wider aisle with expanded pick faces to accommodate more low level picking type trucks working in closer proximity.”
New technologies
Linde’s David Bowen points out that the materials handling industry as a whole is experiencing a big technological shift with the introduction of automated and semi-automated trucks.
“Linde’s VNA man up trucks are no exception to this and Linde has introduced many new features to this range accordingly,” he says. “Looking to the future, our customers are now starting to look for simple, cost-effective semi-automated and fully automated forklift trucks for both pallet transfers and pallet storage.”
He says that automation is growing across all industries. “The future for warehousing looks set to be revolutionised,” he says.
Linde has a number of partners in this area and has set up a ‘Linde Robotics’ automation team. The company has also begun the process of installing its first automated system in the UK with modified VNA trucks rather than for specifically designed automated trucks.
“Linde’s automated man-up range can navigate through warehouse buildings autonomously with the aid of geo-guidance,” says Bowen. “The technology on our narrow trucks is flexible enough to enable phased automation, which makes possible the mixed operation of manual and automated processes.”Narrow Aisle is looking into new products that are capable of lifting increasingly heavier loads at higher levels within narrower storage aisles. John Maguire says that interest in its StorMAX truck, which lifts to heights upwards of 11 metres and has 1000kgs capacity, has been huge.
Gary Ison highlights developments in safety. “Personnel protection systems are developing which offer the possibility for more than one truck to operate in the same aisle, optimising the throughput.”
Case study: Go-Pak goes narrow aisle
When Go-Pak UK, which specialises in disposable products and packaging, found that its 10 metre high UK warehouse was no longer big enough, it moved into a 13 metre high site of 76,000 sq ft – three times the size of its previous space.
When full, the company’s high-bay store has the capacity for almost 10,000 standard 1200 x 1000 mm ISO pallets. The site is designed around a narrow aisle configuration, and uses articulated forklift trucks from Narrow Aisle’s Flexi range.
“It was clear from the company’s previous experience that a narrow aisle high-bay building was required,” says Phil Callan, Narrow Aisle’s technical design manager. “The space that the new unit offered matched the company’s product and pallet load throughput profile.”
The warehouse is served by four electric-powered Flexi AC HiMAX 1400 forklifts. These trucks enable pallet loads to be stacked over 12 metres high – its ‘space frame HIVIs lift mast and specifically developed high quality integrated tilting and side shifting fork carriage eliminates mast deflection at the highest lift heights’.
The trucks include multi-shift availability because of their cassette battery changing and 6.5 hour charging technology.
Bob Rumble, Go-Pak’s warehouse manager, says: “We are delighted with our new facility which, we feel will allow us to sustain the highest supply chain efficiency.” state of the art facility was a daunting prospect but, with Flexi Warehouse Systems’ help, the whole project was implemented smoothly and within the timescales allocated.”