RFID technology has not taken off in the way many expected just a few years ago, but the cost is coming down, and the potential to couple it with other technologies means that new opportunities are opening up. Lisa Townshend reports.
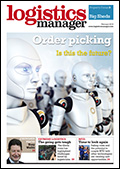
Radio Frequency Identification has had a long and winding journey. Purported to have been developed during WWII following the discovery of radar in 1935, German pilots would roll their planes at a certain point, altering their radar signal and identifying themselves (albeit crudely) as German and not Allied forces – in effect the first passive RFID system*.
It was British forces who developed an active Identify Friend or Foe (IFF) system that used transmitters on the planes that would emit a signal when it received signals from radar stations on the ground.
Since then RFID has been developed for many different uses. Anti theft systems, locking mechanisms, tracking systems, automated tolling tags, dosage tracking in cows (yes, really) and even marketing campaigns such as a recent one for Battersea Dogs and Cats Home in a London shopping centre.
Benefits
There are many benefits to implementing RFID tagging within a supply chain, including:
Efficiency – RFID tags do not require a line of sight to be read. This means they can be embedded and still be read, whether it is within the metal of a roll cage, the plastic tag of a fashion item, the wood frame of a pallet or even the flesh of an animal! It is also readable when moving so there are no bottlenecks– it is possible to set up transfer gateways for the movement of goods. An added benefit to this is the elimination of errors through mis-scanning and fast access to information.
Durability – RFID tags are known for their durability in harsher environments. This makes them ideal for use in extreme temperatures or moisture levels; outdoors or where they face chemical exposure.
ROI – although the implementation costs of an RFID system is higher than systems such as barcodes, the efficiencies of the tags provide a good long-term return on investment.
Validation – with the rise in fake goods, companies are looking at ways to be able to authenticate goods throughout the supply chain. According to an estimate by the Business Alliance to stop Counterfeit and Piracy (BASCAP), the value of counterfeit and pirated products globally in 2015 amounted to $1.77 trillion. This does not take into consideration the impact on human life with substandard and fake goods. RFID tagging could help fight this because of its ability to be hidden in packaging.
As always, when there are benefits there are also challenges. These include:
Cost – the flexibility, traceability and durability of active RFID tags and systems do make them more expensive than, say, barcode scanning. However, as with most technologies, development of faster and more efficient ways of manufacturing and implementing tags has lead to the price of systems coming down and is now making the use of RFID tags more viable for smaller businesses.
Security – again this gets addressed with technological evolution, but security is often a big consideration for companies looking to integrate RFID systems into their processes. The possibility of sensitive tags being able to be scanned externally by a rival or the potential for fraud when using RFID in activities such as payment verification can be a barrier to implementation.
‘Collision’ – one issue with RFID is the problem of tag collision and reader collision. Tag collision is when more than one tag reflects back a signal at the same time, confusing the equipment. Reader collision is when the signal from one reader can interfere with the signal from another where coverage overlaps. The issues with collision can be overcome, but do require further consideration and planning.
Despite these shortcomings, use of RFID within the supply chain is widening. Solutions provider Red Ledge has seen the development of the technology in RFID increase over the last few years. Technical Sales Manager at Red Ledge, Adam Bowes details: “Using innovative software solutions and RFID technologies to create lean and efficient logistics and supply chain processes is gathering pace. We have seen over recent years an increase in RFID solution adoption across our industry.
“RFID tag and reader technology has developed considerably over the last five years. We are now capable of tagging and reading accurately and in-bulk, items of all materials, including metals and liquids.”
With the increased development of the technology another benefit has appeared, as Bowes points out: “Another factor in the continued growth of RFID solutions within the logistics and supply chain industry has been the general availability and decreasing cost of RFID tag technology. In 2010 we were paying about 50p per tag for a standard paper UHF RFID label. Today we can supply a better product for less than 10p per tag.”
Daniel Dombach, director EMEA Industry Solutions and Ralf Schulze, manufacturing lead EMEA at Zebra Technologies, sees the acceptance of RFID coming slowly: “While we haven’t yet seen RFID go mainstream with entire supply chains using the technology, there is a general acceptance and understanding of the value proposition. The most prominent use of RFID is using it to identify physical assets such as tools, pallets etc. The logistics and manufacturing industries in particular need consistent and often urgent tracking of products or tools and this can only be done through swift efficient tools to ID these physical assets. It is only a matter of time before everyone in the industry is harnessing RFID technology to drive efficiency on a mass scale.
“The price of RFID chips is going down and, in fact, the long term cost is substantial but by no means prohibitive. It is the price of non-compliance, however, that has greatest significance for businesses. As the quality, speed and security of RFID technology increases, this may well be mirrored in cost. However, can businesses really afford not to invest in technology that can increase efficiency and reliability at such an exponential rate?
“We are currently part of what is widely referred to as the fourth industrial revolution and the next stage of RFID technology is hinged upon its coupling with other technologies. Location plus identification is only set to spread and is one of the foundation building blocks for smart cities, linking the Internet of Things into the wider social context, beyond the business need.”
In December 2015, Deutsche Post began offering vendors the chance to track items using RFID tags. Designed to cater to the needs of small-scale business senders the Ländernachweis (advice of country) service allows for cross-border tracking of items to be even more transparent. Deutsche Post’s Alexander Edenhofer explains: “[We] began offering EPC UHF RFID technology to customers in December – to those that ship goods in envelopes and small packages abroad. In the parcel world, each parcel has a barcode to be tracked and the sender knows when the parcel is shipped and when it is received. Goods shipped in mail items without registered services are blind between posting by the sender and arrival at the receiver’s address.
“Our service is designed for selling and shipping low value goods, such as books, CD/DVD, toys, consumer goods from the Beauty, Health and Personal Care sectors. There are four major points we are promoting:
l Increased transparency for vendors and customers
l Willingness of customer services to provide information means fewer inbound calls
l Better reviews from marketplace sales
l Transit time experiences optimise the dispatch advice”
Discussing the options vendors have Edenhofer adds: “The use of RFID tracking label must fit into customers’ warehousing and shipping processes. For this we have created different kinds of label types: Prepaid for small customers, separate labels for medium sized customers and labels for addressing also with pre- or uncoded RFID tags integrated. Sometimes it may useful for our customers to invest in new RFID printing technology. It depends on their output and the cost per item.”
With the increase in stability and effectiveness of the systems and a decrease in cost to deploy, now could be a good time to look at implementing RFID.
Case study: Red Ledge RFID system tracks packaging
BorgWarner manufacture turbochargers for the automotive industry at their Bradford production site. Using a core number of suppliers across Europe for raw materials; these often need specialist packaging – a mixture of wood, metal and cardboard. To reduce packaging costs (in excess of £53k annually), there was a move to re-usable plastic stillages, owned & issued to the supplier by BorgWarner. Each of the stillages costs several hundred pounds with the total investment of £110K for the re-usable stillage pool.
There were three key objectives:
1 Reduction of unacceptable attrition rates on stillages due to being stolen, missing or returned late
2 Increase visibility of stillages both at the suppliers and at BorgWarner’s site
3 Reduction of maintenance and replacement costs for the existing asset pool
- Each stillage had two UHF RFID tags in moulded and encoded
- An RFID gateway/portal was fitted at a natural choke point within the goods in/out area and is directly controlled using Red Ledge’s asset tracking system
- Empty stillages are loaded onto trailers using a forklift truck; between 12-20 at a time. As the truck enters the RFID gateway, sensors pick up the direction of the truck. The portal reads the tags and based on the stillage type identifies the supplier they are going to
- The supplier has a pre-defined length of time before they must return the stillages. If they do not then they are fined
- When stillages are returned they contain raw material. As they pass the portal it is identified and booked into stock. RFID-enabled handheld devices are configured to take weekly stock checks and are also taken to supplier sites when a remote stock check is required
- Any damaged stillages are repaired and the repair logged on the Red Ledge system. If it is ‘supplier caused’ damage the supplier is fined
- Once the system went live stillage losses went to zero
- Year 1 Packaging cost reduction of £31,150 net
- Other labour savings calculated at £10,400
- On-time returns went to 100 per cent and damages reduced significantly
- Since implementation one supplier has received a fine for damage – accountability proven using the Red Ledge data
The system has been operating for three years. This was the first BorgWarner site to use RFID tracking technology and was presented to the Global Development Team of BorgWarner in February 2015. Since then many other sites have come to look at the technology in action, with a view to adoption across the group during 2016.