Warehouse operators are under constant pressure to meet the needs of changing markets that might demand a move to VNA operations or more space for an online picking operation. And getting the flooring right is a critical part of any change.
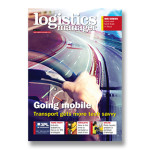
Developments in retailing and manufacturing are having an impact on requirements for warehouse flooring and mezzanines.
Maria Torrent-March, warehouse director at Europa Worldwide, says: “The growth of online retailing is having an effect on demand for mezzanines because it’s putting added pressure on warehouse operations and capacity. Mezzanine levels are ideal for parcel despatch operations where there is a high numbers of SKUs condensed in a small area, so operators are able to streamline processes. By their nature, mezzanines are installed as a means of expansion and a way of increasing the flooring space available within the standing structure of the warehouse. As e-commerce continues to gain momentum this need will only increase, and every customers product is different and so requires different handling and storage solutions.”
Mezzanine International is celebrating its 25th anniversary this year and now has a client list that includes: Amazon, Tesco, John Lewis, Burberry, PC World, Game, Rolls-Royce, JLR, Unilever, GSK, and McDonald’s.
Scott Chambers, managing director of Mezzanine International, recently highlighted the dramatic technological developments in mezzanines. Historically, he said, mezzanine floors were constructed from scaffolding tubes with wooden planks simply bolted on top. The other alternative was concrete blocks spanned with lengths of timber with a plywood decking as a cover. “Dangerous as they were, these two methods had been in use for over 100 years.”
But 40 years ago, things changed and the standard mezzanine product became a combination of structural steel and timber. “The emergence of the mezzanine industry as we know it today came with the use of the roof purlin. By changing the profile of galvanised roof Z-purlins and creating an inward lip C-section beam that could be used with hot-rolled steelwork, we created a cleat that could connect the new purlins directly into an I-section beam,” he said.
“This produced a neat, economical system on top of which various modern decking systems could be placed to create a mezzanine floor.”
The benefits of this new system included cost, long spans, speed on installation and – importantly – greater quality and safety.
Europa’s Torrent-March points out that weight is a major consideration for mezzanine floors. “It has to safely support the weight of the pallets and any automation equipment in place. There is also a finite amount of space to work with on a mezzanine, so operations layout is a major factor, to ensure processes are running at maximum efficiency and will stand up against additional pressures during peak periods. Installing a mezzanine level will also impact the floor space underneath. The supporting columns and beams will create certain restrictions on activity on the ground floor so these need to be factored in – keeping it clear for a despatch and loading zone for example so that forklifts can still load trailers unencumbered.”
And the increase in warehouse automation is having an impact on flooring requirements. Torrent-March says: “I’d say the two go hand-in-hand. The nature of having a mezzanine level means you need to consider automation as an integral part of the process. For example, automation has to play a part in transferring the SKUs to the mezzanine, and once the parcels have been prepared, back to the ground floor ready for distribution. This technology helps to manage the limited space on the mezzanine floors and has to be built according to the operational requirements. Box erectors, box sealers, conveyors and scanning equipment, for example – this technology takes up space, which is limited on mezzanine floors, and has to be built in to the pick and pack line. As growing numbers of people make their purchases online this technology becomes more and more necessary for operators to manage increased volumes.”
Certainly, mezzanines are increasingly seen as an integral part of the warehouse, rather than just an easy way to get some more space.
When international e-commerce and logistics company One World Express opened a distribution hub in Birmingham’s Woodgate Business Park, a mezzanine was core to the development.
The 5,600 sq m site at Woodgate Business Park has undergone a significant refurbishment, and now includes a double mezzanine floor – almost tripling the floor space available. One World Express has also invested in its technology, with one of its sorting machines able to handle over 9,000 parcels per hour.
And Clipper’s new 500,000 sq ft multi-channel logistics hub at Northampton also makes extensive use of mezzanines.
John Lewis is the anchor customer for the site which has been designed as a shared user facility for retail logistics, with a sortation solution to complement the existing Click & Collect capability within the Clipper business.
Caring for the floor
A warehouse floor is critical to logistics operations. It determines the safety and efficiency of the equipment that moves about on it – and it is particularly important when automation is part of the operational mix.
One approach is concrete grinding. CoGri Group was set up in 1989 as a manual floor grinding company using trolley mounted grinding machines. CoGri’s Kevin Dare patented the laser grinder in the early 1990s providing a way of grinding floors to be “superflat”.
When Amazon decided to change the racking area in one of its UK distribution centres from wide aisle to very narrow aisle, it called in CoGri to prepare the floor. Paul Altham, technical services manager for Concrete Grinding, says: “A number of wide aisles were being replaced with six narrow aisles of 70m each to offer increased storage density and reduced pick times.”
First, Face Consultants, CoGri’s testing organisation, surveyed the floor. Another CoGri business, CG Flooring, was brought in to carry out repairs to some of the steel armour joints in the VNA prior to grinding the floor.
Finally, Concrete Grinding came in to finish the job, laser grinding the VNA to the required flatness.
Altham says: “We found the concrete at this particular unit was very hard and as a result wasn’t as easy to grind as it usually is in this part of the country. However, we used two of our patented Laser Grinders to accelerate the programme, which is the best in the world at what it does, so we soon managed to get through some stubborn flooring and complete another fantastic job.”
Resin flooring provides a long-lasting, high performance system for the most exacting situations, but Grimsby Resin Floors (GRF) points out that choosing the correct system to meet specific flooring requirements is an important part of the selection.
GRF offers a nationwide industrial flooring service to the logistics and warehousing market, and is an approved contractor for all the major resin flooring manufacturers in the UK such as Sika, Ucrete, Altro and Resin Surfaces.
Many of the country’s leading supermarkets and other retail chains use GRF in their distribution centres to maintain their floors in a safe and serviceable condition. GRF’s offerings include concrete and expansion joint repairs through to traffic management in the yard.
CSL masters the mezzanine for Wiggle
Last year fast growing cycle retailer Wiggle decided to relocate from multiple small sites in Portsmouth to a 320,000 sq ft fulfilment centre in the West Midlands.
Operations are spread over three floors with a mezzanine providing the two upper floors. This gives Wiggle three independent pick/pack zones and sortation areas designed specifically to avoid issues caused when one combined system is stopped for maintenance/repairs.
Wiggle chose Conveyor Systems (CSL) to provide a full turnkey conveyor project. The brief was to combine packed consignments from the three pick/pack areas over three floors and sort them down 12 lanes into four dispatch zones for separate carriers and services. The system needed to cope with up to 90 boxes per minute of varying sizes and weights, from small parts and clothing up to boxes of bicycle wheels.
Wiggle’s programme manager for the project and head of logistics & operations development, Dan Corrigan says: “As this was a new facility it was difficult to visualise the conveyor system prior to the mezzanine floor installation, but CSL provided a detailed 3D drawing which included both the mezzanine and the conveyors which brought clarity to this. The install process was smooth and the end results have allowed us to increase control, flexibility & volumes”
The conveyor system was designed by CSL at over 900mm wide and was engineered after taking into account observations by both management and operators at Wiggle, plus the vast array of shapes, sizes and weights of products to be handled – and operational issues.
Once an order is picked, packing operatives check and pack into an array of outers ranging from poly bags to large cardboard boxes, prior to applying carrier despatch labels. The consignment is then placed on a section of zero line pressure accumulation roller conveyor to be transported to the ground floor sortation area. This type of conveyor is used widely on the system to provide non-contact queuing to avoid damage to the varied products and prevent possible jams.
Two powered spiral lower-ators bring boxes down from the upper mezzanine floors and using state-of-the-art scanning arrays on each line, barcodes identify the required carrier despatch lane. When the packages reach the correct despatch lane they are diverted off at 90 degrees using high speed switch sorters. Depending on the source pick floor, they either decline down a grip top belt to an ergonomic picking height or transit on a horizontal roller conveyor to the discharge area where a despatch operative removes and places them onto a pallet or into a wheeled cage ready for carrier collection.