From the meticulous handling of goods, to snowballing throughput in the warehouse, home delivery is transforming the culture of order picking. Alex Leonards reports …
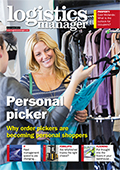
Ten years ago, the idea of whizzing goods around the country, delivering to doorsteps a day after they were ordered would’ve been the exception. Nowadays, it’s becoming the rule.
The culture of retail has completely changed in the last decade, prompting a shift towards improved home delivery services, and a transformation of order picking within the four walls of the warehouse.
“We have implemented a culture shift within our warehouses, where colleagues are being asked to behave like personal shoppers, rather than traditional pickers,” says Jim Hartshorne, vice president operations, home delivery, DHL Supply Chain. “This includes a heightened awareness of people’s shopping preferences and the emotional investment they have in big ticket items.”
In DHL’s warehouses, to guarantee products are loaded in the faultless condition customers demand, pickers are paying closer attention to detail. Employees ensure all the components of an item are included so the order is always correct the first time around.
“The warehouse is no longer the black box that it used to be shipping in bulk to stores,” says Sébastien Sliski, general manager supply chain solutions at Zetes. “It is now a critical fulfilment point in the customers’ brand experience.
“Other than the delivery experience, the frontline warehouse staff can be the final customer service determinant of order accuracy, timing, product condition and associated documentation accuracy.”
As Sliski points out, the impact that warehouse workers can have on both customer perception and total fulfilment cost can be very significant.
“Ensuring therefore that they are equipped with the right tools to keep them productive and efficient and minimising the risks of human error is critical,” says Sliski. “Picking complexity has increased as a result of consumer fulfilment choices, pickers who were used to bulk order picking for stores at a pallet or case level are now dynamically picking consumer orders at an item level.”
And, to push for efficiency gains, pickers are now expected to simultaneously pick multiple orders in one route. “Ensuring appropriate system support tools with robust checks and balances is key to supporting efficient process in this new environment,” adds Sliski. “Gaining visibility of demand and fulfilment within and beyond the warehouse is paramount to ensuring proactivity in a lean operation.”
Of course, increased throughput has put great pressure on warehouse employees.
“Allowing employees to spend more time actually completing orders, in an easier way, has meant productivity levels are on the rise and workers have more ergonomic options,” says Chris Heslop, senior manager, Honeywell. “This is more important now, than ever before, as warehouse operations are becoming critical to brand identity.”
Operations that result in incorrect or late deliveries don’t just reflect badly on the logistics company, they can also damage the brand’s reputation. “So rather than being a back-office function as in the past, the warehouse is very much in the forefront,” says Heslop.
But it’s not just the scale of throughput, nor the demand for perfect packages that is creating an increasingly pressured warehouse environment.
“Amazon entering the home delivery market for groceries has created big challenges for other supermarket chains because they have access to a lot of technology with automated distribution centres and already have a fantastic infrastructure, with delivery vehicles going out into the community anyway to deliver other goods, which gives them a head start,” says Eric Carter, solutions architect at Indigo. “They’ve got the network, vehicles, infrastructure and staff on the ground versus provincial supermarkets, who have to employ people specifically to pick online orders from an inefficient layout within the store environment.”
According to Jason Shorrock, vice president retail strategy EMEA at JDA, the culture of the warehouse has had to adapt significantly to service the growing number of products now being sent straight to the consumer. “It now needs to be more flexible to enable more dynamic and complex picking processes in real time,” he says. “This is increasingly important as retailers are having to offer quicker delivery options to serve demand and keep the customer happy.”
But how do warehouses physically adapt to these big cultural changes?
Edward Hutchison, managing director of BITO Storage Systems, says that nowadays there is normally an ‘e-tailer evolutionary path’. This essentially means that warehouses start by fulfilling home delivery orders manually. “When established they add mechanisation and once firmly established, they will consider automation,” says Hutchison. “‘Stepping stone’ solutions are required throughout this evolutionary path and, whatever stage they are at, there is a need for flexibility to deliver during periods of peak demand such as Christmas and Black Friday.”
In the past, says Zetes’ Sébastien Sliski, the focus was on hypermarket and supermarket style stores with a centralised warehouse. “These centralised hubs would usually have one order picking process in place, which allowed the warehouse to push stock to stores in bulk,” he says.
“Today consumers can access a retailer from the comforts of their own homes or on the go via mobile devices, and these larger warehouses are now responsible for fulfilling more complex single orders.
“Essentially the supply chain is demand driven and consumers are pulling stock directly from the warehouse, whether that’s via click and collect or home delivery and in the majority of cases, one single order picking process won’t necessarily be the most effective option.”
Indigo’s Eric Carter says that although home delivery has become so popular because it’s so convenient, this has created a number of efficiency problems for different kinds of warehouses. “Take the supermarkets as an example,” he says. “In highly densely populated areas, retailers will have dedicated e-commerce warehouses laid out to maximise picking walk-though efficiency and they are likely to be using automation or goods to person technology, if not everywhere, in key places.”
Carter says that in highly populated places, like a local food superstore in Durham, online grocery orders have to be picked and fulfilled from the store. “This is inefficient, because the retailer has to employ a large number of store based pickers and also, the stores themselves are not laid out for picking efficiency in the same way as a warehouse is designed, but to maximise sales and impulse buys from browsing shoppers,” he says. “Pickers are therefore walking miles each day around the shop and the cost of fulfilment can be hugely variable.
“Add into this mix the tendency for customers to want to buy heavy items when they shop online, often in bulk for extra convenience, and it makes it more problematic for the store-based picker.”
On the other hand, there are businesses like Ocado and Amazon that use robots or robot pickers to work alongside humans in the warehouse. “So here are two polar opposite scenarios that the same supermarket chain is potentially having to deal with and at the same time, ensure their customers are getting an equivalent overall shopping experience from the brand as a whole,” he adds.
Warehouses are changing in more ways than one. Retailers not only want their goods shipped on time, and in good shape, they want them shipped from 3PLs that choose the entire warehouse operation. “In the past, customers expected to pick a system themselves which we would then implement,” says DHL Supply Chain’s Hartshorne. “Increasingly, they are looking to us to take on the whole process and deploy our systems in their business.”
With this in mind, DHL is moving towards a more standardised model in the warehouse. “We use the best technology available and the cross fertilisation of ideas across sectors and within a sector,” says Hartshorne. “Typically when deploying one of our systems we work with the rule of thumb that, approximately 80 per cent of our solution will be standardised while 20 per cent is bespoke to each customer.”
But it’s not just the operations of a warehouse that are in the process of transformation. According to Heslop, both the size and location of distribution centres are changing, especially in places like the US. “Instead of huge centralised DCs, companies are building smaller ones in more strategically placed locations to be closer to urban centres, and to make the home delivery process even easier for customers,” says Heslop. “Retail stores themselves are already becoming mini-distribution centres due to the need for speedy delivery, as there are more stores than there are large distribution centres, and generally, are closer to the customer.”
Demand for home delivery will continue to rise
Zetes’ Sébastien Sliski thinks that as same day and nominated day delivery becomes more affordable, both for the consumer and the retailer, demands for home delivery will continue to rise. “The complexities come not just from single item orders from multiple sources but, each order will have a different agreed delivery date, thus creating multiple service level agreements,” he says.
A more and more connected supply chain with end-to-end visibility is another trend Sliski predicts for the near feature. “Creating an environment with greater and broader transparency with well-informed employees and consumers,” says Sliski. “Organisations are extending the functionality of their heavy duty ERP/WMS to add agility to meet the needs of the ever demanding consumer.”
There’s a heavy focus put on making sure that staff have the correct equipment to carry out picking for delivery, and there’s more of this ahead. “However, technology itself is very rarely agile,” explains Sliski. “But the processes and systems that are put in place in the warehouse will ensure flexibility and scalability within the supply chain.”
Sliski predicts that if the right investment is made right at the beginning, retailers will be able to keep up with and evolve at the same rate as consumer demand and behaviour.
Of course, you can’t talk about the future without mentioning automation or even autonomous robots. But is it set to be biggest trend for home delivery?
“While robotics isn’t a major factor yet for two-man home delivery, we are seeing examples of automation,” says DHL Supply Chain’s Jim Hartshorne. “This includes using new technology such as artificial intelligence in route scheduling and loading patterns.
“We are adapting our systems to automate more processes, such as order collation where we can collate different orders together to decrease the number of separate deliveries we are making.”
DHL has seen technology increasingly being used to help with the sale of value added services at the point of purchase, in areas like packaging, removal and installation services.
“The future of home delivery is in line with the general pace of change we are seeing across our industry,” adds Hartshorne. “Implementing new technology such as AR and visual recognition into the picking environment will allow us to maintain speed and efficiency as an industry.”
Sliski says that there is a place for automation throughout the entire supply chain, but that it is not all about the technology.
“Before a retailer commits to an automated warehouse there are things that can be looked at to build ‘best of class’ picking operations,” he says. “Automation is good for predictable, consistent demand patterns but don’t offer the flexibility and agility of other more adaptable systems like voice, for those orders with limited travel time, but also, Pick to Light, which is good for slow moving orders, for instance.”
He says that to bring more innovative order picking solutions to the warehouse, many retailers might look at upgrading their WMS. “This can prove time consuming and costly – and in most cases, by the time they’ve implemented and got the ‘new’ technology up and running, they already need to be using something else, whether it’s Voice Picking, Pick-to-light or Artificial Intelligence,” says Sliski. “Creating advanced functionalities within legacy WMS solutions with a pick and mix of three or four process driven order picking solutions, will allow retailers to unlock agility within their supply chain.
“Ultimately, meaning that if a more efficient technology became available tomorrow they would be capable of introducing it without overhauling their entire WMS.”
BITO’s Edward Hutchison thinks that some of the manual aspects will be replaced by automated goods to picker systems. “There will also be a demand for low cost automation,” he says. “This will involve simple technology that is easy to implement and it will enable the redeployment of people who might be carrying mundane containers on a regular basis to more useful functions.”
There’s an underlying fear creeping up about robots stealing jobs. But how likely is that to happen in order picking?
“I think there will always be a mixture of the two, with the proportions varying depending on the location and local environment,” says Indigo’s Eric Carter. “In the short term, we can expect to see increasing levels of automation in the more densely populated areas, especially within the M25.
“Automation is currently still very expensive however and it’s not really economically viable for most companies to fully automate everything and not use any human labour, unless the demand levels are very high because of the population density.”
But ultimately, over the long term, he predicts that the numbers of people employed in the warehouse will drop significantly as automation slowly takes over. “Picking with robots is definitely a big area, for example, using robots for products that would otherwise have to be picked by hand, like fruit and vegetables,” adds Carter. “It’s clear that companies making these investments, for instance Ocado and Amazon, see that in addition to using robotic technology for their own orders, they can potentially offer a third party service to other retailers, either by outsourcing distribution services and diversifying, or licensing the technology itself.”
JDA’s Jason Shorrock says that it seems inevitable that robots will end up carrying out many of these picking tasks in the warehouse, as seen by some of the more advanced facilities that are already operating. “There will be sectors that will take longer to automate – such as fresh produce, but even these areas will eventually succumb to the ever more sophisticated capabilities of robots,” he says. “Investment in automation technology is growing and this will be an inevitable part of the warehouse in the future, as the capability increases and price points reduce.”
Honeywell’s Chris Heslop says that e-commerce and home delivery will continue to grow in popularity for consumers, and meeting their expectations is always a priority. “The key to meeting this challenge is in continuously finding ways to work smarter – and this is where new, advanced technologies like voice automation and complimentary technology such as robotics, comes into play,” says Heslop. “Increasingly, a company’s technology infrastructure can be the difference between falling behind and edging ahead of the competition – but it’s important to ensure employees have the right training in place.”