A control tower can enable companies to optimise inventory and improve load efficiency – and the return on investment can be significant. Perhaps it’s time to look again at the benefits. Malory Davies reports…
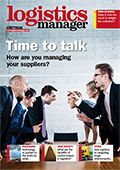
A control tower by definition is a tall building, which should allow a perfect overview. In fact, says Stefan Reidy, chief executive of Arviem, the supply chain visibility solutions specialist: “The control tower should interact with different parties to allow everyone running an efficient process. Applying this definition to the logistics business, the focus should actually be opened up and the discussion should be more about a multi-enterprise and multi-business-unit control tower – and not about a logistics operations control tower. The major benefits will then be achieved in eliminating inefficiencies in the end-to-end process, prevent disruptions and reduce cost.”
Paul Hayes, KeyPL business unit director at XPO Logistics, argues that the tower is crucial to maintaining optimal inventory levels on the inbound supply chain side and improving load efficiency on the outbound transport side.
“It gives the operator a bird’s eye view of the flow of goods at individual sites, including very specific data; for example, how long a vehicle has waited to be loaded and unloaded and what the best inventory combination is for a particular customer,” he says. “Essentially, control towers improve visibility, using aggregated information from multiple sources to drive operational efficiencies.”
And, says Sian Hopwood, senior vice president for B2B at BluJay Solutions: “A control tower programme is fundamental for the 21st century – data streams from across the globe feeding into a single point, producing intelligent insights to improve the management of the system. Companies that get it right can achieve much more efficient internal processes as well as more personalised and effective customer relations.”
Interest in using control towers has been rising, says Mark Wilkinson, supply chain consultancy manager at Indigo Software. This is “a direct result of the greater complexity and length of supply chains, plus the need for much greater cross-functional collaboration within organisations, which traditionally has not been a strength for many companies.
“The real benefits of using control towers are found in distribution networks and having trackable vehicles out on the roads, so they are a lot more common in retail and 3PLs. For example a transport network with its own fleet of trucks is likely to rely on control towers and telematics dashboards with images and information on everything from fuel consumption, vehicle speed, delivery time expectations.”
Bobby Shome, business development director EMEA at Centiro, points out that for retailers, there are unique insights gained by connecting the dots and gathering information normally scattered and siloed in a retailers’ operation, and the benefits a control tower can bring are two-fold.
“Firstly it is another avenue from which you can get closer to the consumer and understand their behaviour, which is always a good thing,” says Shome. “Through the influx of data a control tower supplies, brands are able to optimise the services and goods that they want to offer to individual customers.
“Secondly, control towers allow a retailer to join up all related business functions, giving customer experience, supply chain operations and e-commerce departments the same view of the customer journey. This creates greater horizontal harmony and collaboration within the company.”
While tall buildings might be used as the control tower analogy, logistics control towers do not require tall buildings. What they do require is good IT systems.
XPO’s Paul Hayes says: “The IT interface is an important starting point for both parties. Many companies have legacy systems, and they don’t always talk to each other. For one customer, we had to integrate 36 different legacy IT systems and build a digital “funnel” to help translate all the data into a standardised format we could use.
“It is important to note that implementing a control tower is not a ‘one size fits all’ solution. We have to be very flexible – and at times quite creative – to provide solutions that benefit our customers,” says Hayes.
Dan Mowbray, commercial director at Jigsaw, argues that the starting point is to establish a baseline. “This will include identifying waste and opportunities for improvement and optimisation. This leads to setting targets to track cost and service improvements through comprehensive KPIs and reporting. It is also important to ensure visibility and accountability as key enablers of change.
“In Jigsaw’s experience, successful implementations arise when the customer has a complex and large-scale transport operation with national coverage. Jigsaw can use its core expertise to work with the customer to identify and remove aspects of their transport operation that are inefficient and wasteful,” says Mowbray.
Wilkinson points out that most warehouses and supply chains are fairly silo-ed, even within a single warehouse. Not only that, “very often when an organisation has grown rapidly, they will have acquired different sites each running different processes and most likely, different technology systems. The result is inconsistent data capture and sites cannot easily compare and share information using a control tower. Before implementing a control tower, processes, systems and technology need to be standardised and simplified.
“Then if you expand this beyond the individual organisation to cover an entire supply chain network, the issue becomes even more complicated because systems need to collaborate with a huge variety of network providers. This requires what’s known as semantic integration – where an order or an action is defined and mapped as an identical concept across each organisation within the network, which is a major challenge. For example, an order defined by one system originating from one supplier needs to be mapped in the same way by the customer to ensure like-for-like comparisons.
“It’s important to keep it simple and be sure to know what data is really critical to have. This means ensuring that the alerts set up or the information displayed is the right information and it is data that will make decision making easier and quicker,” says Wilkinson.
Sian Hopwood highlights the importance of knowing how you are going to store and manage the necessary data before you start centralising things like management structures and freight forwarding. “You need to have regular updates on everything from point of origin through customs and transport right to the customer’s doorstep. With the rise of connected devices and mobile technology, this is a lot easier than it used to be, as updates can be gathered automatically and in near real-time. Nevertheless, you’ll need the appropriate technology in place.
“Once you’ve addressed that, it’s key to have a cloud-based management platform in place to enable you to use your new data. By handling data in the cloud, you can make it available to users up and down the supply chain in a standardised format, avoiding the need for ungainly email correspondence and lengthy waits between stages of the chain,” says Hopwood.
Hans-Georg Kaltenbrunner, vice-president industry strategy for manufacturing, EMEA at JDA Software, notes that when businesses start implementing a control tower, they tend to focus on the logistics functionality. “Businesses, however, need to avoid overwhelming the control tower, by filtering the relevant information from the white noise.
“When implementing a control tower, organisations need to factor in that once Electronic Data Interchange (EDI) messages are received, the information containment might already be out of date. Some smaller freight forwarders and handling agents might not have the technical prerequisites to send EDI-messages; this increases the possibility of blind spots across the logistics process. JDA has recently implemented Transvoyant’s technology, to help its customers alleviate this problem. The use of this type of technology employs advanced analytics, based on real-time big data curated from the likes of sensors, radar, smartphones, satellites, GPS and video cameras. This approach produces live and predictive insights, allowing the control tower to be far more accurate and in control of disruptions,” says Kaltenbrunner.
The rise of the Internet of Things is having a significant impact on the development of control towers.
In fact, says Hopwood, the IoT provides the hardware that makes control towers possible. “From in-truck sensors to warehouse-based pallet tracking, the data collected by IoT devices means that the central command team can be updated on everything from shipment temperature and humidity to stock levels and last-mile delivery speeds.
“Before the IoT became widespread, these factors had to be reported on manually, and it wasn’t possible to do that quickly enough to provide an accurate real-time picture of the whole supply chain. With the IoT, the command point effectively has eyes on the ground all the way along the chain,” says Hopwood.
Paul Hayes agrees: “Control towers feed off digitalised supply chains: the more data you put in, the more it allows you to do. Asset-tracking technologies and fleet management solutions have been around for a while, but at XPO we’re finding ways to leverage technology for next-generation safety and efficiency. For example, we can envision a time when fridges will automatically order groceries and we will support customers who move into that space. More immediately, we’re trialling voice recognition and other technologies in logistics settings, and focusing on transparency in the supply chain.”
Arviem’s Stefan Reidy points out that you can’t manage what you don’t know. “Even the best control tower solution can only analyse and interpret data, which is available. IoT enlarges the amount of available data by being able to collect data at the edge of the network and by making such data available even in real-time. IoT provides precise, real-time information from the operational supply chain revealing supply chain operations that have until now been invisible to supply chain managers.
“Bringing in a multi-enterprise focus for a control tower also introduces a dependency on data from other stakeholders on the availability and reliability of data.
“The Internet of Things can, to certain extent, overcome that dependency. Reliable data can be collected in real-time where the action is, independent of the involved stakeholder,” says Reidy.
Jigsaw’s Dan Mowbray says the ability to collect, manage and analyse this information effectively and make meaningful decisions (often in real-time) is a challenge that presents opportunities to streamline and simplify transport operations while enhancing customer service. Jigsaw has invested heavily in transport planning and management systems that support these objectives.
Hans-Georg Kaltenbrunner of JDA says: “In the past, control tower projects have relied heavily on offline or batch orientated data flows. The use of IoT offers the opportunity for businesses to use real-time data streams from containers use IoT technology.
“Real-time data streams from tracking vessels and air freight equipment significantly enhances and increases the amount of data available, creating an even a bigger challenge to intelligently filter and define alerts, when needed.”
What’s the value?
It’s all too easy to spend money on control tower systems, but the important thing is to get an adequate return on investment.
Jigsaw’s Dan Mowbray points out that client investment in a control tower is low but the potential gains are high. “Jigsaw’s systems enable integration with client ERP and WMS systems to ensure seamless information flows with clients’ other business information systems. Key stakeholders also affect change and make improvements which will contribute to the overall success of the implementation.”
RoI estimates vary for different operations. JDA’s Hans-Georg Kaltenbrunner points out that the ROI simply depends on the way the control tower is used – with potential savings ranging from one to three per cent. “These savings come from reduced freight costs due to a smaller amount of expediting and a decrease in the amount of damage control an organisation will have to undertake,” he says. XPO’s Paul Hayes says RoI varies very much by supply chain, but typically up to ten per cent is achievable.
But Indigo’s Mark Wilkinson sounds a note of caution: “The issue with control towers is not so much the theory of whether they add value, but how well they really work in practice to deliver a clear return on investment. There’s a lot of hype and they have been billed as a panacea when actually, the reality is quite different. The extent to which every aspect of the supply chain can be integrated to deliver real end-to-end visibility and scale this across all trading partners is questionable, which limits the ultimate value of a control tower. They also require a lot of human intervention, which contradicts the current move within logistics towards greater automation and artificial intelligence.
“For a large proportion of SMEs I would question how valuable an investment in a control tower really is and whether they might be able to improve their response times and decision making with really good dashboards and alerting.”
Can you go further?
Getting a control tower up and running opens up the possibility of further efficiencies by linking it to supply chain planning and execution systems.
The technology is already available to do this, points out Hans-Georg Kaltenbrunner of JDA: “This approach allows the entire supply chain to work together seamlessly, making intelligent decisions as and when they need to. The data intelligence used by the control tower can filter down to the planning and execution systems in real time, diverting shipments to an alternative port until the extreme weather dies down or suggesting another route for the shipment to take entirely. By linking these two elements together, organisations can ensure that production continues to run smoothly and customers receive their orders on time.”
BluJay’s Sian Hopwood argues that if the control tower is linked to a cloud-based management system, then planning and execution functions can talk to each other very easily. “Companies need to move away from a siloed model, where planning sits in one building and sends out diktats to the rest of the business by email or fax. Instead, the whole company should be on a unified cloud platform, enabling all departments to read from the same hymn sheet.”
Many retailers are moving away from traditional forecast-led supply chains in favour of consumer-driven demand networks that flow the same real-time information to all supply chain participants, says XPO’s Paul Hayes. “As the technology becomes more nimble, logistics providers need to respond with greater agility, and a control tower helps make this possible.”
But achieving integration can be challenging, says Indigo’s Mark Wilkinson. “It’s very difficult to integrate all these systems across a vast network of supply chain partners and see meaningful information. It is best suited to companies that are vertically integrated because of the practicalities of trying to get multiple systems within different companies talking to each other.”
Ultimately, says Stefan Reidy of Arviem: “A control tower provides a one-stop, full end-to-end view of all visibility information together with business intelligence/analytics in a single platform. The “all visibility information” is only doable by an extended approach.”