Is packaging keeping up with the rest of the logistics process when it comes to technology? Alexandra Leonards explores the new technologies arriving in the market, and examines some of the biggest challenges being faced by packaging companies.
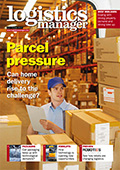
It’s near impossible to name a product or part that doesn’t use some form of packaging during its journey to customer or consumer. And yet, the process is still only quietly understood as an important part of the logistics process.
Developing new technologies for packaging is just as vital as creating new innovations for order picking, transport or sorting. After all, packaging still has to live up to the expectations of consumers, and meet the standards of retailers and manufacturers.
Packaging is crucial, and so its development over time is crucial. But is it keeping up with other areas of the logistics process?
“The market is far from staid and continues to see a raft of innovation designed to meet both the customer’s needs; whether reducing costs, improving efficiencies or enhancing the consumer experience,” says Martin Styler, packaging machinery and systems expert at Antalis Packaging. “We believe technology will play a greater part in packaging in the next five years.”
In particular, augmented reality is predicted to be a big trend for the not so distant future. This is driven by the need for businesses to impress their customers and create a positive experience within the brand.
“To look at the potential of augmented reality in packaging, one need only look at the impact already on retail; from Coca-Cola to L’Oréal, multiple brands embrace the marketing benefits of smartphones with augmented/virtual reality revenue forecast to hit $120 billion worldwide by 2021,” he says. “In this way, we see the future of packaging as interactive and responsive, and giving power to customers by enabling them, for example, to scan an image on food packaging to access full sourcing data and recipes, or to enter an online competition.
“The future could see everything from nutritional information to flat-packed furniture instructions delivered in this way. The possibilities really are endless.”
Martin Tanner, director product management and marketing at Bosch Packaging Technology, identifies virtual reality as a market disrupter.
“We believe we will use more and more virtual reality in the near future, which will take industry 4.0 solutions to the next dimension,” says Tanner. “Augmented and virtual reality offer completely new possibilities to support staff with maintenance, troubleshooting or during training courses by supplementing live images with additional information, or even simulating three-dimensional environments.
“Thanks to virtual reality, operators can see a virtual image of their machine, for instance via a smartphone or special glasses.”
Virtual reality applications help with error location and troubleshooting, and they can also be used for virtual training measures like learning about format changes in near real-life conditions. “Trainers can view the simulation live and give supporting instructions on the spot,” says Tanner. “For operators, this is an efficient and safe way to deliver training since mistakes do not have direct consequences and the production process does not need to be interrupted.”
According to him, the packaging market has started moving towards Industry 4.0 and complete system solutions. “At Bosch, we have devised a number of digitally connected solutions for food and pharma applications – and we are not stopping here,” adds Tanner. “Our objective is to develop reliable and easy-to-use systems that apply cutting-edge technology.
“One of the latest Industry 4.0 solutions is the Maintenance Support System (MSS). This feature simplifies the execution of all kinds of maintenance activities.” This technology analyses machine data in real-time – the data sends operators and engineers an overview of everything they need to know about the machine from their mobiles.
“Last but not least, linear drive technology is becoming more of a standard in the industry,” concludes Tanner.
DS Smith has recently launched two new technical solutions for the e-commerce sector: DISCS and Made2fit.
“In an industry first, DISCS™ (Drop, Impact, Shake, Crush, Shock) replicates the stress that packaging and products can suffer as part of the supply journey,” says DS Smith’s Rob Carle. “The tests are designed to examine the durability, sustainability and integrity of the packaging.
“As for Made2fit, this technology enables the creation of right-size packaging – eliminating void space, and as a result reducing both operational and shipping costs.”
According to Carle, these kind of technologies represent the future of packaging. “They address issues that have dogged the e-commerce industry – such as packaging which doesn’t survive the complexities of the modern supply chain, and packaging which doesn’t fit the products – and provide innovative and welcome solutions,” he says. “Technology, such as DISCS and Made2fit, will change the way the e-commerce industry operates and should mean that packaging is making a positive contribution to the brand experience.
“The future is intelligent packaging which delights consumers. We hope that before long, all e-commerce packaging will be easy to source, assemble, ship, open and then either return items in or recycle at home.”
Robotics
Robotics technology is becoming increasingly present in the market. “In most cases they replace the workforce carrying out repetitive and monotonous jobs, as well as making the workforce more productive, speed up packaging times, and cut costs by reducing the need for temporary staff,” says Antalis’ Martin Styler.
Manufacturing is an area that Styler has particularly noticed the technology being used in, but it is becoming more and more present in logistics also.
“In several projects we’ve worked on, there will be a case erector system supported with a robot in position to pick up and put the product into the case and send it onto the delivery station; thereby, quite literally from the manufacturing process to the sealing of the box, there is no human contact,” he says.
Robots are also being readily used for palletisation. “ Inherently, this has always been an arduous task for human workers, having to constantly bend and lift, especially in the case of heavy duty goods,” he says. “As such, putting a robot in place that can simultaneously pack different pallets via a pre-programmed schedule – all without any health and safety risks, can make good business sense.”
In future, he predicts the use of robotics will only grow further. “Of course, there will still be some level of human intervention needed but, whereas previously there might be 100 people in a manufacturing plant and distribution centre, in 10 years’ time we might only see 20 people or so, mostly there to oversee the lines, with robotics performing the majority of tasks,” adds Styler.
Mark Gray from Universal Robots says that collaborative robots are a new technology that are being used as part of an Industry 4.0 initiative. “The ability to use automation which is easy to deploy is the key,” says Gray. “Collaborative robots have been designed to be easy to program using a programming touch screen that operators can interpret and see messages from the robot. Collaborative robots are used in packaging at the moment for picking applications and end of line palletising where the small footprint means it takes very little floor space.”
In the face of rapidly changing market demands, strict safety regulations and rising labour costs, robotic solutions are becoming more and more attractive for packaging companies that require solutions with maximum flexibility, according to Bosch Packaging Technology’s Martin Tanner.
“Robots can be applied to product handling for multiple formats, sizes and packaging styles on the same machine,” says Tanner. “What is more, the machines perform consistently for 24 hours a day, seven days a week, thus increasing production, lowering costs per unit and increasing quality, thus giving manufacturers a competitive advantage.”
He says that robotics is a key technology, which is widely used in the packaging industry. “Be it for product handling, distribution, feeding, cartoning or case packing,” he says. “Backed up by numerous years of experience with pick and place applications, and over 1200 solutions installed worldwide, it is safe to say that Bosch’s Delta robotic packaging equipment is a great choice for low weight products or goods that require gentle handling.”
And to simplify operations even further, lots of robots now have software that supports monitoring and troubleshooting processes.
“For example, new software now allows operators to prepare production processes offline and simulate runs, helping to reduce set-up time for new batches, with errors spotted quickly before actual production starts,” says Tanner. “ Bosch provides manufacturers the option of using its Gemini 3 software, which displays a 3D visualization of robot movements.
“It simultaneously provides operators with the view seen by the vision system, positioning them to better troubleshoot issues with the vision profile.” He predicts that we will see even more collaborative robotic technology that enables safe interactions between humans and robots.
Challenges in the market
Packaging prompts a lot of challenges because it serves a whole range of important functions. “Such as protecting the product inside – all the way from production and transport to consumers’ cupboards at home, conveying the brand’s marketing message and image, as well as differentiating the product from the competition on supermarket shelves,” says Bosch Packaging Technology’s Martin Tanner. “Consumers are bombarded with advertising messages everywhere they go, so the biggest challenge for packaging suppliers is to design something outstanding that meets both product needs and individual production requirements.”
He says, that from a production standpoint, manufacturers of all sizes have to bear the following three aspects in mind when coming up with an optimal packaging solution: flexibility, automation and connectivity.
“Since they are often required to pack different products on the same line, packaging systems must have the flexibility to adapt to changing demands quickly (i.e. smaller packages for seasonal promotions), while also being able to handle different pack styles and configurations (i.e on-the-go versus multi packages),” he says.
According to Universal Robots’ Mark Gray, the major challenges affecting industry today are costs and efficiency.
“For the UK to be a competitive manufacturing base automation has a key part to play in improving efficiency and keeping costs down,” he says. “Brexit has prompted the discussion on whether the free movement of labour will be available in the future, companies will have to look at strategies using technology to help.”
Introducing automation into the process is something that Tanner also identifies as an important consideration. “The second aspect calls upon manufacturers to understand the required level of automation: from basic (hand-fed loading) and intermediate (automated loading and wrapping with manual case packing or cartoning) to full (all packaging steps are automated),” he says. “Modern packaging technologies allow producers to grow their packaging line at their specific pace of business development – starting with hand-fed machines and step-by-step automation.”
Looking ahead, he sees the next automation level involving integrating production floor management (using tablets or smart phones) controlling cleaning and maintenance procedures, and transferring real-time data from the production floor to operators’ desktops even faster.
“Furthermore, connectivity will play a huge role in simplifying and future-proofing packaging processes since each product transfer from one part of the production line to the other poses a potential failure point,” adds Tanner. “Identifying these points is key to designing an efficient system solution. Connectivity facilitates data transfer even further: by including trackable codes on the packaging itself, producers and consumers alike can identify where the product comes from, to which transfer point it should be shipped, or which transport batch it came in.”
A well-known issue associated with the market is waste. “Packaging waste is high on the agenda, now more than ever,” says Antalis’ Martin Styler. “Amid the recent plethora of media headlines around the overuse of transit packaging, the lack of coffee cup recycling and plastics in the ocean, companies are under increased pressure to become more environmentally aware and to support the elimination of waste plaguing our planet.”
Bosch’s Tanner also identifies sustainable materials in packaging production as an important issue in the market.
“Conscious consumers pay close attention to their purchases: they are keen to know whether the product was made from recyclable materials, sourced from sustainably managed forests or bears the FSC certificate,” says Tanner. “However, some environmentally friendly materials simply cannot be used in packaging as they fail to meet strict production requirements.
“Sustainable packaging options are gradually entering mainstream production, such as the Sealed Paper Packaging solution that was jointly developed by Bosch and Swedish paper producer BillerudKorsnäs.”
Styler says that added to the equation is the current legislation around packaging.
“First of all there is the Packaging Waste Regulation, which states that companies producing over 50 tonnes of waste a year are taxed on the amount that goes through the business,” he says. “Then this April saw landfill taxes rise from £84.40 per tonne to £86.10 per tonne, with further increases planned next April and beyond.
“This is in addition to a gate fee given to cover the capital and maintenance costs of the landfill operator. Thus, logistics firms are under increasing pressure to go greener and the rationale is two-fold; to improve their CSR credentials while also reducing tax costs.”
Of course the end consumer is a factor that is always at the heart of the process.
“On a customer-centric front, the challenge really is creating cut-through,” says Styler. “With e-commerce on the rise, customers are receiving more parcels every day, so it’s all about creating cut through – with the clever choice packaging technologies and innovations core to adding that ‘WOW’ factor.”
As well as this, Antalis are facing additional challenges on the operational side of things.
“In particular, meeting the unexpected and expected peaks in customer demands amid a more unpredictable retail dynamic,” adds Styler. “With this in mind, we recently launched a Smart Audit service where we can help businesses get their packaging operations in ship-shape order so that they can be prepared as much as possible.”
For DS Smith, the biggest challenge when it comes to packaging technology market, is adapting to the complexities of the modern online marketplace and designing fit for purpose e-commerce packaging.