A tyre blowout is never good. But, imagine your blowout is due to your truck being shot at in enemy territory while vital chilled medicines are slowly warming in the trailer. Welcome to the world of extreme logistics. Lisa Townshend reports.
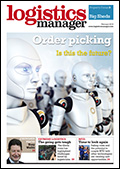
The role of logistics in extreme situations is both vital and challenging. The added layer of complexity to the already complex task of ensuring goods are where they need to be when they need to be makes for a demanding role. At the recent European Supply Chain Excellence Awards held in London in November 2015 saw many of these demanding operations highlighted in the Extreme Logistics category as well as in other categories. In this article we will look at some of these operations and what it takes to manage a logistics operation in places such as Afghanistan and Sierra Leone.
The winner of the International Operations and the Public & Third Sector categories was a joint entry by the Department for International Development (DFID) with Crown Agents and International Procurement Agency (CAIPA) for their role in the emergency supply of up to 1,250 line items to the relief operation in Ebola-ravaged Sierra Leone. The operation was in response to an international public health emergency with unprecedented implications, and the two organisations had to collaborate closely to provide a highly efficient emergency supply chain to help tackle the scourge of Ebola; the urgency of the operation was literally a matter of life and death for thousands of Sierra Leoneans.
John McGhie, DFID’s supply chain demand manager for the Ebola crisis, recalled how the response to the crisis developed: “The collaboration began mid-September 2014 when Crown Agents was contracted as surge capacity by DFID’s standing humanitarian response team. The UK government determined that dedicated Ebola treatment centres (ETCs) and Community Care Centres (CCCs) were needed to isolate and treat the growing numbers of Sierra Leoneans affected by the disease.
“The initial phase of the response saw Crown Agents charged with supplying everything required within the first of the dedicated Ebola Treatment Centres (ETCs). Crown Agents handled the sourcing, processing, shipment and delivery of up to 700 line items – covering every piece of equipment that would be needed to create an efficient and robust emergency response centre. There were the obvious items, the visible ones that people were seeing in the news items every day: the pharmaceuticals, the personal protection equipment, the thermometers, the gloves, the saline bags. Then there were the items that were less obvious as part of a supply chain, but still just as vital to ensuring a functional and rigorously hygienic environment in which to fight Ebola: the washing machines, the mops, administrative necessities like pens and clipboards, gaffer tape, and much more.
“Crown Agents was then contracted to work on the supply of six further treatment centres and the International Procurement Agency (IPA) was added to the collaboration. The partnership on the resupply of six of the seven treatment centres was where the supply chain strategy and the performance became honed, advanced and even more expertly executed. The work on this phase of the operation involved the establishing of the supply chains that would keep those centres stocked and effective. During the resupply phase a catalogue of 1,250 line items was developed and, from that list, around 1.2 million line items were purchased in total.”
There were four strategic pillars underpinning the entire supply chain for this operation, including:
- Pooled procurement – By pooling the procurement needs of all of the DFID-supported centres, labs and end users we were able to improve DFID’s buying power as well as work with suppliers to ensure capacity was sufficient to meet future demand and stop end users ‘competing’ for the same limited resources.
- Moving centralised warehousing closer to the end users – it was decided that there needed to be a centralised warehouse location as close to the end users as possible. Finding suitable warehousing facilities within Sierra Leone was not easy but a disused cement warehouse was converted into a good standard medical warehouse with suitable areas for storage of both ambient and cold chain-controlled pharmaceuticals. Physical storage space was always short, however, so a warehouse in Liverpool supplemented the one in Sierra Leone.
- Moving from a push to a pull supply system – In the early weeks of the response, it was essential to get stock moving and to the ETCs and CCCs as quickly as possible so, to this end, a push system was used. Initially each facility and end user received a standard package\ of items DFID thought necessary to start up and operate the sites. CAIPA made a decision to move from a push to a pull system as quickly as possible so the individual facilities could determine what they really needed. So, a catalogue was established which the end users could order from.
- Collection and analysis of supply chain data – Underpinning the response was the need to collect and analyse supply chain data to aid decision making. Using two analytical systems throughout the response allowed for this and formed the basis of regular reports to DFID on stock availability, spending and consumption. This also allowed DFID to keep track of assets in the country.
Operation Gritrock
Looking closer to the operation in Sierra Leone, the logistical infrastructure had to be put in place to ensure the timely and safe delivery of the medical supplies to the country. Enter Operation Gritrock, the name for the DfID-led aid operation to Sierra Leone aiming to control the Ebola outbreak and led by 84 Medical Supply Squadron; part of 9 Regiment RLC and based in Hullavington near Chippenham.
Major Douglas Ingram, commanding officer of the 84 Medical Supply Squadron, explained the beginnings of the operation: “The Squadron was given notice in late 2014 that it was to take part in Operation Gritrock and within two weeks was able to have both ends of the supply chain in operation, assuring the battle winning commodity for the operation – medical supply. A detachment was deployed to East Midlands Airport (EMA) controlling all medical stores into theatre and a second node in Sierra Leone.”
On the UK side of the Supply Chain a five-man team operated at EMA. This team leader was also the liaison point up and down the Chain of Command and with the outside agencies involved in the operation. The team wrote operating procedures and developed into a bespoke node providing assurance to the medical supply chain, as well as other commodities for both the military and other involved in the operation. The operation with other government departments and working within the civilian environment was a new experience for the team, improving both the military and civilian understanding and working practices.
The team in Sierra Leone were initially responsible for the collection, tracking, accounting and onward movement of the stores and for the assurance of the Cold Chain from flight arrival to point of delivery. As a new operation into an austere and potentially lethal environment, the team needed to be innovative to ensure the medical supply chain. Medical commodities often need specialist temperature and climatic storage, which were a challenge in the hot and humid environment of Sierra Leone.
The team also brought the logistic information system, Management of the Joint Deployed Inventory (MJDI) into theatre, thus increasing their workload with the reconciliation of the medical account. This team was also responsible for the reverse Medical Supply Chain coming back out of Sierra Leone and ultimately for the closure of the account on their return to the UK.
A key commodity for the operation was blood. Blood component logistics is a complicated discipline given the short shelf-life of blood and platelets and the requirement for these components, and frozen plasma, to be delivered within exacting temperature constraints. The austere and climatically challenging conditions of West Africa exerted even greater pressure on the cold chain.
Major Ingram added: “From Oct 2014 to Jul 2015, 2,448 medical line items were supplied to theatre at a total cost of nearly £1m and amounting to 39 tonnes of freight. Three complete medical laboratories were also flown out. On top of this the team dealt with 34 tonnes of general stores and partway into the operation, also became the designated route for all mail into theatre. This was all achieved by a node of five soldiers at EMA and initially, one soldier in Sierra Leone.”
With an operation on a scale such as this, it was easy to see why 84 Medical Supply Squadron were winners of the Extreme Logistics category at the European Supply Chain Excellence Awards.
Operation CATALINA+
Bringing the equipment back home
One of the finalists in the Extreme Logistics category faced a wholly different type of challenge. Based in a classified location and working primarily with contracted civilians unused to the procedures followed by the military, this operation was taking military vehicles and equipment and readying them for redeployment or storage. Based in extreme temperatures and lacking the facilities employed within the original facility in Afghanistan, the team from 62 Supply Squadron, 6 Regiment RLC managed the operational repair and redeployment of roughly 700 vehicles in nine months.
Operation CATALINA+ was a UK MOD Reverse Support Chain node established at a base in the Middle East. It allowed military vehicles and sensitive equipment to be redeployed from Afghanistan to the UK in a cost efficient, yet secure manner. All vehicles and equipment were initially inspected and accounted for, prior to the removal of security sensitive equipment. The vehicles were then subjected to a rigorous bio-security cleaning process in line with Defra standards before being moved to a local port for return to the UK. The aim of the operation was to return the vehicles with ‘Proof Of Good Order’ (POGO) for the National Audit Office. These procedures enabled early, detailed planning of vehicle regeneration in the UK to support (almost) immediate redeployment upon arrival on contingent operations.
Major Joseph Brown, the commanding officer for 62 Supply Squadron, highlighted the metrics for success by which the operation was judged: “The success of the CATALINA+ operation was judged on three key metrics. Firstly, the achievement of POGO; proved though the successful receipt, without the raising of discrepancy reports, of vehicles and equipment consigned to the UK. Considering the value of material moving though the node during this period was over £500m, and that no discrepancy reports were raised, the results could not have been better. Indeed, the performance was exemplary and the framework is now seen as the benchmark for future operations.
“Avoiding reputational damage through the prevention of accidents in the workplace (or ‘operational safety’) was another key issue. We placed significant emphasis on providing a safe working environment and our approach was specifically noted during the successful Defence Safety and Environment Authority (DSEA) inspection. In addition, there were no significant injuries during our deployment. Our focus on operational safety required us to ensure that third country national sub-contractors (employed by our civilian logistics partners) were subject to the same codes of practice of our military staff. Given the diversity of languages, we delivered extensive briefings via interpreters, using diagrams and demonstrations where required, to ensure that they were complying with DSEA safety regulations for the loading of vehicles to low loaders.
“Finally, a key metric was the maintenance of goodwill with the Host Nation. This was critical to enable on-going military operations in the Middle East. It is a difficult metric to measure, due to specific cultural differences, but it shaped all of our actions. The behaviour of our personnel had to be beyond reproach, as well as being culturally aware and deferential to our hosts at all times. Despite the requirement for regular, frequent (and at times robust) liaison with local security forces and port authorities, we received no complaints.”
Operation CATALINA+ included some of the following activities:
Receipt: The unloading of large military vehicles from cargo aircraft. When vehicles were damaged and could not be moved in accordance with established methods, sound military judgment (with appropriate oversight) was used to improvise safe and efficient methods of recovery. The ‘receipt’ team comprised of approximately six military personnel.
Accounting: The removal of and accounting for complex and sensitive sub-systems, including weapons, radios and other equipment from each vehicle. Where components of subs-systems were found to be deficient (or surplus) during these accounting procedures, liaison with the units who had consigned the vehicle was used to rectify any discrepancies. Through sheer diligence this activity resulted in more surpluses than deficiencies, including approximately £500,000 of surplus radio equipment. The accounting team comprised of approximately 20 military personnel.
Bio-security: This was due to be delivered by contractors, but the contract failed. The accounting and issue (with an element of the inspection) team re-rolled to complete this task in an improvised facility that we had developed as a contingency plan. This was perhaps the defining moment on Operation CATALINA+ because it had not been originally anticipated that military manpower would complete this task. However it became critical to mission success, and would not have been possible without a huge amount of flexibility an innovation.
Out load: This team was a hybrid of military manpower and contractor partners. This included the loading and shrouding of military vehicles on civilian low loader vehicles, transport, liaison with Host Nation security forces to provide police and military escorts, and the unloading of vehicles at the port. Host nation security restrictions also dictated that such moves be conducted only at night, and were restricted in size and scope. Once at the port, military manpower (required to wear civilian clothing to prevent them from being identified as service personnel) moved the vehicles onto the shipping. One notable change to the out load activity was that host nation security constraints dictated that the final loads were run at a different port, which had not been used before and was less well developed and secure. Extensive reconnaissance, re-planning and co-ordination was required to ensure that this new port could be used safely and efficiently. This planning was completed in collaboration with civilian logistic partners and local authorities against some very challenging timelines.
The three examples of logistics in the face of extreme challenges does show that no matter what you are moving and where, you need collaboration, flexibility, innovation and a good planning strategy to ensure success. Not so very different from retail, automotive, food or any other branch of supply chain. Just minus the peril.