The loading bay is a vital area in the operational processes of the warehouse. Constantly in use, the flow of goods from truck to storage and back again, needs to be seamless and safe. Lisa Townshend examines the challenges.
The area of distribution seems to be riding the crest of a wave at the moment but in reality it is more akin to the roller coaster – up and down with a few unexpected twists and turns. This is especially prevalent when you look at the suppliers of loading bay equipment to fulfil the spec for the timely loading and unloading of goods to keep the supply chain moving in any given sector.
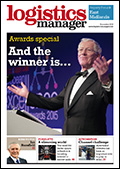
One big trend that seems to be revealing itself is the slowing of the retail side with regards to the need for services such as lifts, levellers, seals and shelters, doors and associated equipment. However that does not mean that the sector itself is slowing, rather that areas such as ports are the latest big thing. The recent additions to the logistics centre at DP World London Gateway and the moving of operations for companies such as Pentalver at the Port of Tilbury shows the interest in ports currently.
The recent investment in the Pentalver facility at the Port of Tilbury has seen the logistics company move into a facility at Berth 43, covering a 6.6-acre site strategically positioned close to the London Container Terminal operations within the port estate.
The depot has automated equipment designed to minimise vehicle turnaround times. An additional new empty container handler has also been added to the Tilbury fleet.
“Our new premises reinforce our commitment to the Port of Tilbury, which continues to play a significant role in Pentalver’s plans for the future,” says Shaun Allen, chief operating officer of Pentalver Group. “The new site, which is closer to the container terminal business and benefits from significant investment, ideally positions us to meet the needs of our Tilbury clients now and in the future.”
But what does this mean in terms of loading bays? Well, suppliers of loading bay equipment have to think a little more creatively in terms of dealing with logistics centres located near deep water and the challenges of dealing with large containers. Projects such as the one at DP World has also had to take into consideration the high volume of reefer goods which need to be carefully temperature controlled.
Product development is a continual process in loading bay technology as Tom Langley, projects director at Hörmann UK explains: “We manufacture our own products – every dock leveller, every door etc – they are all made in our own facilities. Every year we look at all of our product offerings and see how they can be tweaked to improve efficiencies in design, manufacture, adherence to the latest regulations etc… we may not be talking about significant technological advances every year, but small changes that can make a real difference. In addition, we make sure we listen to our clients to get a better idea of what they need and what changes in their sectors are driving development in ours.
“An example would be in parcel delivery and the changing nature of their delivery vehicles and response times so the trend in the market would be for smaller doors and high speed. And we do get a lot of people buying from us to sell to other people, so having products that are easy to install is a benefit for them.”
Security is another issue that needs to be taken into consideration, depending on the nature of the building Langley continues: “It does depends on the type of distribution centre or building it is. So, yes, we are noticing an increase in security concerns but that does tend to be more for fire doors or access doors rather than the loading bay side of it. Our doors are reasonably secure anyway – the majority of sites are going to be secure anyway. It’s more where you’ve got a fire exit door.”
Safety matters
Security seems to go hand in hand with safety. When installing or maintaining loading bay equipment you have to be mindful, as Hörmann’s industrial service manager Phillip Clark explains: “In a 24/7 DC or in parcel logistics that can be quite difficult because of 20-30 bays.
Although you’ve got the beauty of that many bays, they’ve got them because they are that busy. Trying to pinch a single bay at a time to try and service with two guys can be quite difficult because you’ve got the plan to make things safe which you’ve then got to choose between the client’s requirement and the safety requirement of having to service it. Because there is no down time per se for their usage, it then becomes a battle between yourself and a lorry as to who gets priority – a load or a service. You have to have a really good customer relationship and be able to negotiate with the on-site technicians to essentially ‘condemn’ a door – close it down so you can service it – and then move on.”
Safety should not just be a legal burden but viewed by managers as a means to improve efficiency and generate return on investment. That’s the view of John Meale, managing director of Thorworld Industries. “The vehicle loading and unloading area is potentially one of the most hazardous areas in any company, warehouse or distribution centre, yet this need not be the case. Indeed, safety is a cornerstone of the FEM (The European Materials Handling Federation) Vision & Strategy 2020, the Federation’s manifesto for the future of European materials handling.”
The Association of Loading and Elevating Equipment Manufacturers’ web site (www.alem.org.uk) reveals the scale of complying with the minimum of standards. No less than 18 different documents of Codes of Practice, Directives and Regulations start off the process of supplying the equipment and ensuring safety and quality throughout the lifecycle of loading bay equipment.
Recycling
Recycling the product at the end of its lifetime has its own challenges. Repair and replacement of equipment needs to also be considered. Clark concludes: “Companies such as ourselves are starting to try and gear up to reducing our carbon footprint. When you break a door panel out you end up releasing carbon dioxide so we’re looking at ways of reducing that. In addition we are looking at how as a business we can recycle panels, which obviously has an environmental factor. It is quite a challenge because at the minute as far as I am aware there isn’t a company out there that recycles PU panels. If one of the big waste management companies were to get involved there certainly a niche market out there! But with that in mind we are looking constantly at our processes.”
Case study: Mitchell solves space dilemma
Business models and practices change, and companies often need to work within legacy buildings that don’t match their current needs. Commercial diesel power and transmission distributor, Mitchell Powersystems, overcame these issues by calling in Smart-Space to provide more loading bay facilities, and liberate warehouse space at its Sutton-in-Ashfield centralised distribution site.
Mitchell’s logistics manager, Gene Laker, explained: “Prompt delivery is a priority for our customers and we decided that we could provide a better service to them with a centralised distribution hub, rather than a network of regional depots. One of our existing buildings met most of our needs, but lacked adequate space for orders to be collated and for sheltered vehicle loading and unloading. Footings were already in place for an extension, but we feared that conventional construction would be costly, time consuming and highly disruptive.”
Smart-Space has provided the company with a 20×25 metre open-ended covered loading bay to the existing warehouse. This allows vehicles to be loaded and unloaded under cover, adds more outdoor storage, and releases space within the main facility for more efficient storage and stock management.
The Smart-Space system uses strong but lightweight roll-formed steel sections in place of conventional hot rolled steel. Ground loading forces are low so such buildings generally have lighter and less costly foundations than conventional construction, saving time and money. In this case, footings for a conventional extension were in place, enabling an exceptionally speedy build at a cost of just under £50,000.
As Laker noted: “The installation went very well, the guys worked really hard to get it completed with little disruption to our operation. On-site time was less than one month. We are very pleased with the result.”
Case study: Transdek double deck lifts for Home Bargains RDC
Transdek UK has supplied 15 double deck lifts and ancillary equipment at a new Southern regional distribution centre for TJ Morris, the Home Bargains retailer.
TJ Morris currently operates more than 400 Home Bargains stores across the UK and employs 13,500 staff. With a turnover of £1.5bn and growth of approximately 15 per cent per annum, the company plans to expand to more than 700 stores within the next five years.
The retailer is opening a £110m, 1,000,000 sq ft RDC has been constructed at Amesbury, Wiltshire. Transdek was appointed to install 12 20-tonne (18 pallet/30 roll cage capacity) and three 6.5-tonne (6 pallet/12 roll cage capacity) double deck lifts at the RDC, along with a vehicle cleansing lift.
Gary Cobb, distribution operations manager for TJ Morris, said: “We have already converted our goods out operation with Transdek’s double deck loading systems at our RDC in Liverpool. Based on its all-round professional service and the reliability of its lifts, Transdek was the chosen partner for our new Southern RDC.”
Each modular double deck lift was supplied as a pre-built pod, designed for rapid installation directly onto the yard slab. All lifts were initially held off site at Transdek’s factory and delivered to Amesbury as required. A two-day window was allowed for the fitment of each unit.
Throughout the design process, Transdek’s project management team liaised closely with the architects and sub-contractors. As a result, 900mm high docks were incorporated at the site’s dedicated double deck bays to provide a direct run-through onto the bottom deck of Home Bargains’ fleet of fixed double deck trailers.
The 900mm docks allow a double deck trailer to be loaded in two lift cycles –reducing vehicle fill times, speeding up turnaround, minimising product handling, improving safety and driving down costs. Transdek also manufactured 15 modular loading ramps to facilitate a descending gradient from the warehouse for the direct run on and run off the lower vehicle deck.
The double deck lifts are fitted with Transdek’s Active Management System (AMS), which integrates the unit’s control panels into the RDC’s main IT system, providing live plant status information and analysis of the performance of each bay.